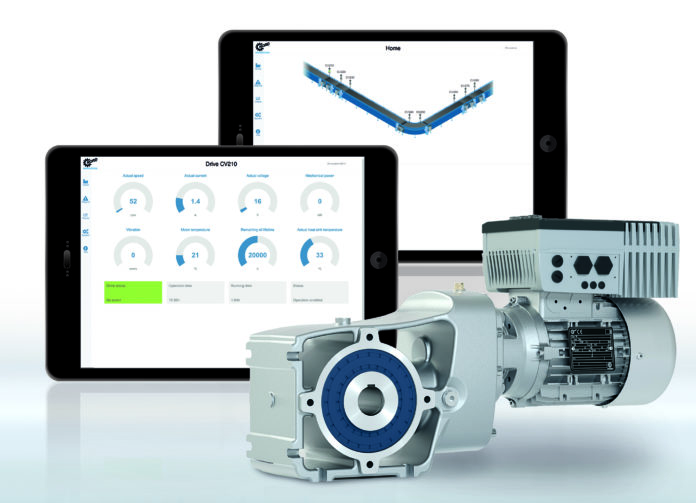
Konserwacja predykcyjna to ciągła analiza stanu w celu proaktywnej konserwacji maszyn i urządzeń oraz wykrywania zmian, skrócenia przestojów i zwiększenia wydajności całego zakładu. Konserwacja zorientowana na status zastępuje tradycyjną konserwację opartą na czasie.
W przypadku systemów napędowych w wymagających środowiskach produkcyjnych, gdzie przekładnie przemysłowe pracują we wrażliwych zastosowaniach, a ich awaria może spowodować poważne uszkodzenia, szczególnie w intralogistyce, przemyśle spożywczym lub sektorze ciężkim, monitorowanie stanu uzupełnia tradycyjne trio napędowe (przekładnia, silnik elektryczny i przetwornica częstotliwości) zapewniając podwyższony poziom bezpieczeństwa i niezawodności. Monitorowanie stanu dla konserwacji predykcyjnej okazuje tutaj swoją wartość: W oparciu o inteligentne algorytmy i oprogramowanie w środowisku IIoT, połączone w sieć jednostki napędowe mogą gromadzić swoje dane o stanie we własnym sterowniku PLC falownika i wstępnie przetwarzać je wraz z danymi podłączonych czujników i siłowników. Wynik wstępnego przetwarzania lub kompletne dane można opcjonalnie przesłać do urządzenia brzegowego. Tam dane wszystkich podsystemów są zarządzane i oceniane. Są one następnie dostępne jako wstępnie wybrane i edytowane inteligentne dane do dalszego wykorzystania i przejrzystej wizualizacji.
Analiza danych zamiast samego odczytu danych
Konkretnym przykładem zastosowania jest bezczujnikowe określanie optymalnego czasu wymiany oleju na podstawie temperatury oleju. Wynika to z faktu, że temperatura oleju ma kluczowe znaczenie dla starzenia się oleju w przekładniach. Informacje te w połączeniu z dostępnymi parametrami przekładni oraz określonymi parametrami eksploatacyjnymi pozwalają precyzyjnie wyliczyć czas wymiany oleju. Fizyczny czujnik temperatury nie jest wymagany. Wstępne przetwarzanie danych napędowych odbywa się w zintegrowanym sterowniku PLC przemiennika częstotliwości NORD, który służy jako jednostka analizująca. Klient ma dostęp do obliczonych danych za pośrednictwem wszystkich popularnych interfejsów.
Właściwa architektura oprogramowania PLC dla każdego rozwiązania
Wyposażenie napędowe można opcjonalnie rozbudować i dostosować do danego zadania automatyzacji. Klienci mogą wybrać zadania (monitorowanie napędu, sterowanie napędem, sterowanie procesem), które chcą bezpośrednio przenieść do napędu. W mniejszych obszarach produkcyjnych ta skalowalność daje możliwość zdobycia pierwszych doświadczeń przed reorganizacją zakładu. Dostępne są trzy poziomy konfiguracji. Na pierwszym poziomie sterownik PLC jednostki napędowej wykonuje jedynie monitorowanie napędu. Parametry napędu są wstępnie przetwarzane w sterowniku PLC i przekazywane do systemu sterowania wyższego poziomu, który jest odpowiedzialny za sterowanie napędem i procesem. Na poziomie średnim PLC integruje sterowanie napędem, a także obsługuje funkcje związane z napędem. Na wyższym poziomie konfiguracji sterownik PLC falownika całkowicie zastępuje system sterowania wyższego poziomu. Oprócz komunikacji z jednostką sterującą, lokalne zarządzanie danymi bez połączenia z Internetem może opcjonalnie zastosować dane.