O trendach w ochronie przed zagrożeniami i bezpieczeństwie rozmawiamy z Jeanie Downs, kierowniczką ds. środowiska, zdrowia i bezpieczeństwa, Hitachi Global Air Power US, LLC, Michigan City, Indiana oraz Zackiem Mitchellem, zastępcą kierownika ds. bezpieczeństwa korporacyjnego, Stellar, Jacksonville, Floryda.
Jakie są obecnie trendy w zakresie ochrony przed zagrożeniami w zakładach przemysłowych i produkcyjnych?
Zack Mitchell: Szkolenia, środki ochrony indywidualnej (ŚOI), sprzęt bezpieczeństwa (myjki do oczu, myjki do rąk itp.), sprzątanie i wentylacja to niektóre z trendów, które obserwujemy.
Jakich przyszłych trendów w zakresie ochrony przed zagrożeniami powinni oczekiwać inżynierowie, kierownicy zakładów i projektanci?
Zack Mitchell: Systemy ochrony przeciwpożarowej będą nadal ewoluować dzięki zaawansowanym technologiom i ulepszonym systemom wykrywania. Systemy wentylacyjne będą się rozwijać, aby poprawić jakość powietrza i skuteczniej usuwać niebezpieczne substancje. Wdrożenie stałych urządzeń zapewniających stały przepływ wody, takich jak stacje do przemywania oczu i rąk, stanie się bardziej powszechne, aby zapewnić natychmiastowy dostęp do odkażania w nagłych wypadkach. Ponadto prawdopodobnie wzrośnie wykorzystanie jednorazowych środków ochrony indywidualnej, zapewniając wygodę i minimalizując ryzyko zakażenia krzyżowego.
Jakie rodzaje aplikacji komputerowych są wykorzystywane do wspierania Państwa funkcji ochrony przed zagrożeniami?
Jeanie Downs: Korzystamy z systemu, który dzieli nasze kategorie ryzyka według modułów (środowiskowe itp.). Pomaga on w śledzeniu naszych incydentów i zdarzeń potencjalnie wypadkowych, a także naszych działań naprawczych, wymagając ukończenia działań naprawczych przed zamknięciem incydentu. Pomaga nam również śledzić, czy nasi kontrahenci – i ich pracownicy – są na bieżąco z wymogami bezpieczeństwa. Oparte na chmurze oprogramowanie jest również wyposażone w kalendarz zgodności, który śledzi nasze wymogi regulacyjne i terminy ich spełnienia. Wszystko, czego potrzebuję, jest w jednym miejscu.
Zack Mitchell: Korzystamy z różnych aplikacji komputerowych w ramach naszych systemów ochrony przed zagrożeniami. Obejmują one oprogramowanie do audytu bezpieczeństwa do regularnych inspekcji, system zarządzania dokumentami do dokumentacji administracyjnej, dzienniki aktywności do śledzenia roboczogodzin oraz bazę danych poświadczeń szkoleniowych do zarządzania certyfikatami pracowników.
Jakie są niektóre z kluczowych wyzwań związanych z poprawą ochrony przed zagrożeniami elektrycznymi w Państwa zakładzie i jakie strategie/najlepsze praktyki wdrożyli Państwo, aby zapewnić sukces?
Zack Mitchell: Niektóre z kluczowych wyzwań związanych z poprawą ochrony przed zagrożeniami elektrycznymi w naszym zakładzie obejmują prawidłowe wdrożenie procedur lockout/tagout (LOTO) oraz zapewnienie skutecznej komunikacji i świadomości wśród personelu. Aby sprostać tym wyzwaniom, wdrożyliśmy strategie i najlepsze praktyki. Nasza polityka surowo zabrania stosowania wyłącznie systemu tag-out, wymagając zablokowania wszystkich źródeł zasilania za pomocą fizycznej blokady/bariery przed rozpoczęciem pracy.
Ponadto organizujemy spotkania przygotowawcze z całym odpowiednim personelem, aby zapewnić właściwą komunikację i świadomość potencjalnych zagrożeń. Prowadzona jest również dokumentacja administracyjna uwzględniająca narażenie na zagrożenia, zaangażowany personel i niezbędne kroki, które należy podjąć.
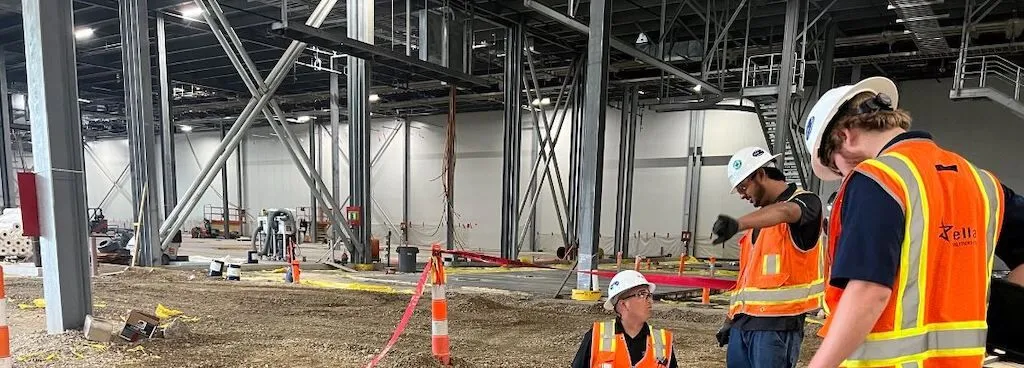
Czy COVID-19 przyspieszył wdrożenie planu ochrony przed zagrożeniami, a jeśli tak, to w jaki sposób?
Jeanie Downs: Pandemia COVID-19 tak naprawdę nie przyspieszyła naszego planu ochrony przed zagrożeniami, ponieważ mieliśmy już solidną strategię. Dodaliśmy kilka protokołów, ale poza tym byliśmy przygotowani.
Zack Mitchell: Tak, pandemia COVID-19 przyspieszyła wdrożenie planu ochrony przed zagrożeniami w naszej placówce. W odpowiedzi na kryzys podjęliśmy proaktywne działania, wdrażając plan ochrony przed COVID.
Jakich wskazówek udzieliliby Państwo osobie, której niedawno powierzono obowiązki związane z ochroną przed zagrożeniami?
Jeanie Downs: Proszę zwrócić się do ekspertów, którzy wykonują daną pracę. Pracownicy, którzy pracują w danym strumieniu pracy, znają ryzyko związane z wykonywaną pracą i mogą pomóc nowemu kierownikowi ds. bezpieczeństwa w kwestiach, których nowy kierownik może nie zauważyć lub o których może nie pomyśleć. Obecni pracownicy mogą również odegrać kluczową rolę w modelowaniu zachowań dla nowych pracowników.
Zack Mitchell: Muszą Państwo wiedzieć, z czym pracują i jakie są związane z tym zagrożenia, zapoznać się z SDS i zapewnić odpowiednie kwalifikacje szkoleniowe.
Czy mogą Państwo przedstawić przegląd potencjalnych zagrożeń występujących w zakładach produkcyjnych i przemysłowych oraz sposób ich priorytetyzacji pod względem zarządzania ryzykiem?
Zack Mitchell: Nieoczekiwane narażenie na niebezpieczne chemikalia, jasna komunikacja z zakresem oczekiwań dotyczących pracy i sposobami łagodzenia zagrożeń, znajomość programów i procedur bezpieczeństwa.
W jaki sposób są Państwo na bieżąco z najnowszymi przepisami bezpieczeństwa i najlepszymi praktykami branżowymi związanymi z ochroną przed zagrożeniami w środowisku produkcyjnym i przemysłowym?
Jeanie Downs: Uważam, że webinaria, seminaria i konferencje na temat bezpieczeństwa są świetnym sposobem na bycie na bieżąco z najnowszymi przepisami, środkami ochrony indywidualnej i najnowszymi produktami bezpieczeństwa. Część wystawiennicza konferencji poświęconej bezpieczeństwu pozwala znaleźć sprzedawcę, który pomoże wdrożyć produkty lub narzędzia, o których właśnie się Państwo dowiedzieli, a które odpowiadają Państwa celom i założeniom w zakresie bezpieczeństwa.
Zack Mitchell: Ustanowiliśmy proces, w ramach którego nasze programy bezpieczeństwa są weryfikowane i aktualizowane co najmniej raz w roku. To proaktywne podejście zapewnia, że nasze programy pozostają zgodne z przepisami firmowymi, jak i państwowymi. Poprzez regularne monitorowanie i uwzględnianie wszelkich zmian lub postępów w przepisach bezpieczeństwa i najlepszych praktykach, utrzymujemy wysoki standard ochrony przed zagrożeniami w naszym zakładzie, jednocześnie dostosowując się do zmieniającego się krajobrazu wymagań bezpieczeństwa w naszej branży.
Jakie środki podejmują Państwo w celu zapewnienia, że wszyscy pracownicy są odpowiednio przeszkoleni i świadomi zagrożeń, z którymi mogą się zetknąć na swoich stanowiskach w obiekcie i jak często ma to miejsce?
Jeanie Downs: Pracownicy nowszego pokolenia uczą się inaczej. Zaczęliśmy ponownie przygotowywać nasze szkolenia, aby lepiej wyposażyć pracowników, gdy dotrą do hali produkcyjnej. Początkowo nasze szkolenia odbywały się wyłącznie w klasie. Od tego czasu dodaliśmy element praktyczny, aby przemówić do naszych młodszych rekrutów. Przypominamy również pracownikom, nie tylko warsztatowym, o znaczeniu bezpieczeństwa. Wszyscy otrzymują cotygodniowe szkolenia z zakresu bezpieczeństwa dostarczane online. Pomaga to wszystkim być świadomym zachowań związanych z bezpieczeństwem, niezależnie od tego, czy są w fabryce w pełnym wymiarze godzin, czy tylko przechodzą przez parking.
Zack Mitchell: Wszyscy nowo zatrudnieni pracownicy przechodzą szkolenia, które są specjalnie dostosowane do zakresu ich pracy. Szkolenia te obejmują zagrożenia, które mogą napotkać, oraz niezbędne protokoły bezpieczeństwa w celu skutecznego złagodzenia tych zagrożeń. Ponadto priorytetowo traktujemy ciągłe szkolenia i podnoszenie świadomości poprzez coroczne doszkalanie pracowników. Zapewnia to, że pracownicy są na bieżąco z wszelkimi zmianami w procedurach, sprzęcie lub potencjalnych zagrożeniach, wspierając kulturę ciągłego uczenia się i utrzymując wysoki poziom świadomości w całym zakładzie.

W jaki sposób monitorują Państwo i oceniają skuteczność środków ochrony przed zagrożeniami w swoim zakładzie i jakie kroki podejmują Państwo w celu ciągłej poprawy bezpieczeństwa?
Jeanie Downs: Przeprowadzamy coroczny przegląd programu bezpieczeństwa, aby upewnić się, że nasze metody ochrony są skuteczne. Oceniamy również wiedzę naszych pracowników na temat bezpieczeństwa. Losowo zadajemy pracownikom w każdym obszarze produkcji serię pytań, aby ustalić, czy musimy przeprowadzić odświeżenie wiedzy na temat bezpieczeństwa dla tego zespołu.
Zack Mitchell: Stosujemy różne metody monitorowania i oceny skuteczności środków ochrony przed zagrożeniami, jednocześnie nieustannie dążąc do poprawy bezpieczeństwa. Po pierwsze, zapewniamy zgodność z przepisami dotyczącymi środków bezpieczeństwa i ochrony przed zagrożeniami. Ponadto kładziemy nacisk na stosowanie odpowiedniego sprzętu ochrony osobistej (PPE) jako kluczowego elementu ograniczania zagrożeń. Co więcej, prowadzimy cotygodniowe spotkania, podczas których omawiane są zagrożenia, zwiększając świadomość pracowników. Spotkania te są okazją do zebrania informacji zwrotnych, omówienia obaw i zidentyfikowania obszarów wymagających poprawy.
W jaki sposób podchodzą Państwo do wyboru i stosowania ŚOI w swoim zakładzie? Jakie kroki podjął Pan/Pani lub Pana/Pani firma, aby zapewnić pracownikom dostęp do niezbędnych środków ochrony indywidualnej i ich prawidłowe stosowanie?
Jeanie Downs: Przeprowadzamy ocenę środków ochrony indywidualnej za każdym razem, gdy aktualizujemy proces. W ramach wniosku o modyfikację obiektu dokonujemy przeglądu i wyboru ŚOI zgodnie z zagrożeniami w procesie. Na hali produkcyjnej mamy automaty ze środkami ochrony indywidualnej. Jeśli pracownik potrzebuje rękawic, może udać się do automatu bez czekania, aż ktoś przyniesie mu rękawice, co również pomaga w zwiększeniu wydajności. Ponadto automat śledzi skuteczność naszego sprzętu. Jeśli na przykład pracownicy stale potrzebują rękawic, być może powinniśmy zmienić rękawice na cięższe itp.
Zack Mitchell: Podchodzimy do wyboru i użytkowania poprzez nakazanie „100% ŚOI” dla wszystkich pracowników, co obejmuje kaski ochronne, okulary ochronne, rękawice odporne na przecięcia, ochronę słuchu w razie potrzeby, ochronę przed upadkiem z wysokości i stosowanie respiratorów. Przeprowadzamy oceny zagrożeń, aby zidentyfikować niezbędne środki ochrony indywidualnej, zapewniamy kompleksowe szkolenia w zakresie ich doboru i użytkowania oraz dostarczamy wszystkim pracownikom wymagany sprzęt przed rozpoczęciem pracy. Gwarantuje to, że nasi pracownicy mają dostęp do niezbędnych środków ochrony indywidualnej i prawidłowo ich używają, nadając priorytet ich bezpieczeństwu i tworząc bezpieczne środowisko pracy.
Z Państwa doświadczenia wynika, jakie są największe wyzwania lub przeszkody w tworzeniu i wdrażaniu środowisk ochronnych w zakładach produkcyjnych i przemysłowych oraz jak je Państwo pokonujecie?
Jeanie Downs: Bezpieczeństwo jest częścią naszej kultury i naszym priorytetem numer jeden – i upewniamy się, że wszyscy traktują je jako priorytet na każdym poziomie. Rotacja pracowników jest największym wyzwaniem dla naszych wysiłków w zakresie bezpieczeństwa. Kiedyś pracownicy produkcyjni pozostawali w pracy przez 40 lat. Pracownicy nie pozostają już tak długo w jednej firmie, co sprawia, że pula nowych pracowników jest stała. Aby utrzymać bezpieczeństwo na pierwszym miejscu, prowadzimy cotygodniowe szkolenia odświeżające wiedzę, a także szczegółowe szkolenia wdrożeniowe i regularne audyty bezpieczeństwa.