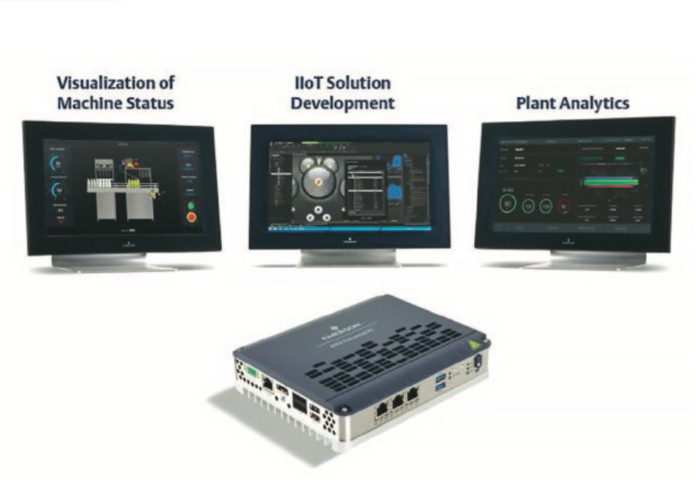
Przemysłowe firmy produkcyjne wykorzystują obecnie sterowniki brzegowe oraz przemysłowe komputery PC (IPC) do wykonywania analizy danych najpierw na krawędzi sieci w fabryce, a potem w biurze przedsiębiorstwa, zamiast w odwrotnej kolejności.
Niezależnie od tego, czy firma produkcyjna posiada kilka zautomatyzowanych maszyn w jednym zakładzie, czy też całą flotę sprzętu w wielu swoich zakładach w różnych lokalizacjach, zawsze istnieje dla niej potrzeba lepszej widoczności sprzętu, uzyskiwania odpowiednich danych oraz ich analizowania. Bez dostępu do danych źródłowych oraz metody ich analizowania takie firmy działają głównie w oparciu o doświadczenie.
Producenci z wielu powodów mogą być niechętnie nastawieni do rozpoczęcia wdrażania nawet podstawowej analizy danych. Ich podstawowe systemy już funkcjonują od dawna, natomiast potencjalny zwrot z inwestycji w nowe technologie może nie być oczywisty dla kierownictwa tych firm. Ponadto wielki problem może stanowić zakup odpowiedniego sprzętu i oprogramowania oraz wykonanie integracji systemów, co jest niezbędne dla uzyskania dowolnego typu przynoszącej korzyści analizy danych.
Jednak firmy te mogłyby się zdziwić odkrywając, że mogą zbudować analizę danych, rozpoczynając od małych kroków na krawędzi sieci zakładowych, zamiast podejmowania od razu wielkich inwestycji na poziomie całego przedsiębiorstwa. Uzyskując na krawędzi sieci wiele źródeł danych Przemysłowego Internetu Rzeczy (IIoT), a następnie przetwarzając je w razie konieczności na Big Data, użytkownicy mogą tworzyć wartościowe i dające się wykorzystać w praktyce informacje. Sprzęt i oprogramowanie do przetwarzania danych na krawędzi (edge computing) czynią to możliwym.
Analiza danych: od dołu do góry zamiast z góry na dół
Wielu producentów może rozumieć inicjatywy wprowadzania analizy danych jako przedsięwzięcia na poziomie całego przedsiębiorstwa, w obszarze rozbudowanych systemów realizacji produkcji (MES). Kierownictwo tych firm może się niepokoić zasobami, czasem realizacji oraz kosztami, wymaganymi do wdrożenia wielkiego projektu informatycznego (IT) tego typu, szczególnie w sytuacji, gdy ich umiejętności i doświadczenie oraz zainteresowanie mogą być bardziej zorientowane na technologię operacyjną (OT) na poziomie fabryk.
Jednak istnieje też inna opcja, możliwa do realizacji dzięki nowoczesnym sterownikom brzegowym, przemysłowym komputerom PC (IPC) oraz skoncentrowanym na technologii operacyjnej pakietom oprogramowania. Użytkownicy końcowi, integratorzy systemów oraz producenci wyposażenia oryginalnego (OEM) wszystkich typów mogą razem zbudować praktyczne systemy analizy danych typu bottom-up („z dołu do góry”) od granic maszyn, zamiast top-down („z góry na dół” – z przedsiębiorstwa/biura). Analiza danych na krawędzi sieci może zaoferować natychmiastowy zwrot z inwestycji w postaci dostarczania wskaźników OEE (całkowita efektywność wyposażenia). Może też być głębsza – skalowalna do poziomu całego przedsiębiorstwa.
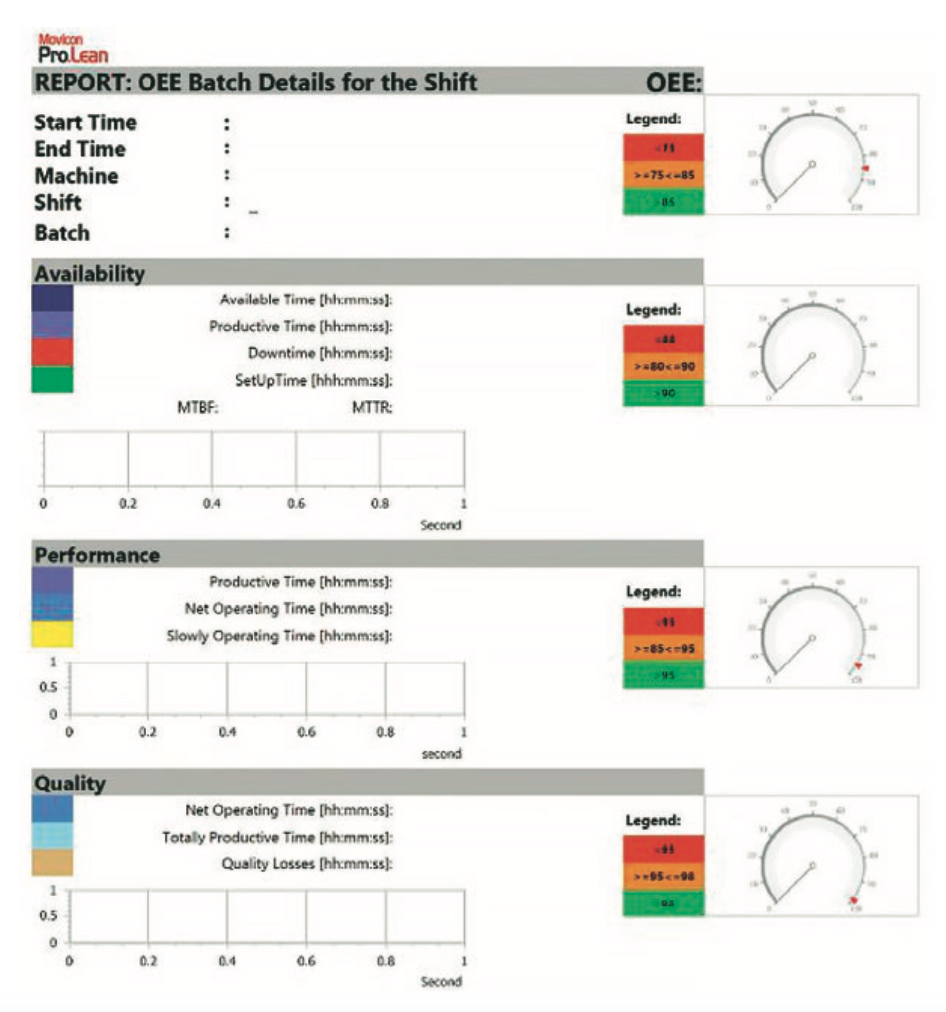
Należy uzyskiwać dane na temat maszyn w zakładzie
Przesunięcie mocy obliczeniowej z biura przedsiębiorstwa na krawędź sieci w zakładzie przemysłowym jest sensownym posunięciem z wielu powodów. Większość z najważniejszych danych dotyczących maszyn jest dostępna w ich układach elektronicznych, chociaż można też zainstalować na maszynach inteligentne czujniki oraz inne systemy zewnętrzne. Podczas gdy jest możliwe przesyłanie i zapisywanie setek tysięcy punktów danych o wysokiej wierności (high fidelity data) w celu ich ostatecznej analizy na poziomie przedsiębiorstwa, to rozwiązanie takie może być jednak kosztowne i często niepraktyczne.
Dzieje się tak, gdy w tej roli występują tradycyjne systemy automatyki przemysłowej, to każdy nowy czujnik musi zostać skonfigurowany ręcznie przez specjalistów oraz mapowany poprzez wiele łączy i systemów komunikacyjnych, aby dane z niego osiągnęły poziom biura przedsiębiorstwa. Podczas tej drogi ważne sygnały mogą stracić swoją aktualność, zaś sygnały niemające znaczenia niepotrzebnie obciążają sieć i zajmują miejsce w nośnikach danych.
Aby uzyskać najbardziej responsywne wyniki, wskaźniki takie jak wymienione poniżej najlepiej jest obliczać na krawędzi sieci, dokąd przybywają dane źródłowe (rys.1):
- OEE (dostępność, wydajność i jakość),
- godziny pracy maszyn,
- przepustowość oraz ilość odpadów,
- zużycie energii,
- status maszyn.
Użytkownicy mogą uzyskać bezpośredni dostęp do danych źródłowych („surowych”) oraz przetworzonych, a następnie wysłać ujednolicone wyniki do chmury obliczeniowej w celu ostatecznej analizy na wyższym poziomie. Przetwarzanie danych na krawędzi sieci w ten sposób jest idealnym rozwiązaniem do uzyskania informacji dotyczących każdej maszyny, co jest posiadającym wysoką wartość krokiem początkowym. W następnej kolejności rozszerza się tę analizę danych na linię produkcyjną lub park maszynowy.
Ponieważ użytkownicy końcowi często mają wiele maszyn, nierzadko rozproszonych po wielu zakładach, każde rozwiązanie technologii IIoT na poziomie pojedynczych maszyn musi być skalowalne do poziomu całej fabryki, a następnie do poziomu całego przedsiębiorstwa.
Skalowalność oprogramowania – od poziomu maszyny do poziomu całej fabryki i całego przedsiębiorstwa
Tradycyjne programowalne sterowniki logiczne (PLC) oraz interfejsy operatorskie (HMI) z pewnością mogą wykonywać niektóre obliczenia na krawędzi sieci oraz realizować przesyłanie danych na wyższy poziom, jednak w znacznie większym stopniu są skoncentrowane na realizowaniu funkcji sterowania w czasie rzeczywistym. A zatem użytkownicy końcowi często potrzebują opcjonalnych urządzeń do przetwarzania danych na krawędzi sieci, posiadających większą moc obliczeniową i obsługujących więcej protokołów komunikacyjnych OT/IT oraz oprogramowania napisanego specjalnie pod kątem realizacji zadań związanych z analizą danych.
Sterowniki brzegowe oraz komputery IPC są dwiema platformami, które nadają się dla użytkowników pragnących wbudować technologię IIoT oraz analizę danych na krawędzi sieci w nowe maszyny lub dodać je do istniejącego sprzętu. Sterowniki brzegowe zawierają funkcjonalność PLC, jednak mają też drugi, niezależny, ale zintegrowany na płycie system operacyjny, który potrafi realizować zaawansowaną wizualizację, analizę i przesyłanie danych.
Komputery IPC są w pełni samodzielnymi jednostkami, które także potrafią wykonywać powyższe zadania. Oba typy platform przetwarzania danych na krawędzi sieci są specyficznie zaprojektowane do pracy w warunkach przemysłowych – odporne na wysokie temperatury i wibracje, mogą więc być instalowane na maszynach lub w szafach sterowniczych na krawędzi sieci fabrycznej.
Cechą odróżniającą sterowniki brzegowe i komputery IPC od standardowych sterowników PLC oraz interfejsów HMI jest możliwość uruchamiania na nich specjalnych aplikacji i pakietów oprogramowania, spełniających jedną lub więcej z następujących ról (rys. 2):
- przesyłanie danych IIoT do sterowników, inteligentnych czujników oraz sprzętu monitorującego stan techniczny maszyn i urządzeń,
- brama sieciowa do komunikacji z innymi systemami, tego samego lub wyższego poziomu,
- wizualizacja statusu maszyn, analizy danych oraz generowanie raportów graficznych typu dashboard,
- obliczenia analityczne wskaźników OEE oraz zrównoważenia energetycznego.
Niezależnie od tego, czy użytkownik końcowy jest producentem wyposażenia oryginalnego (OEM) budującym maszynę, czy działem technicznym fabryki wdrażającej technologię IIoT, właściwa wizualizacja oraz oprogramowanie analityczne przyśpieszy ich prace. Użytkownicy ci w celu redukcji kosztów i czasu wdrożenia powinni poszukać takich pakietów oprogramowania, które oferują kreatory konfiguracji najczęściej wykonywanych zadań, takich jak tworzenie wskaźników OEE. Oprogramowanie powinno mieć możliwość uruchomienia na małą skalę lub lokalnie na jednej maszynie, jednak musi też realizować bardziej zaawansowaną analizę danych i być skalowalne od tego małego poziomu do poziomu całej fabryki, a następnie do poziomu całego przedsiębiorstwa.
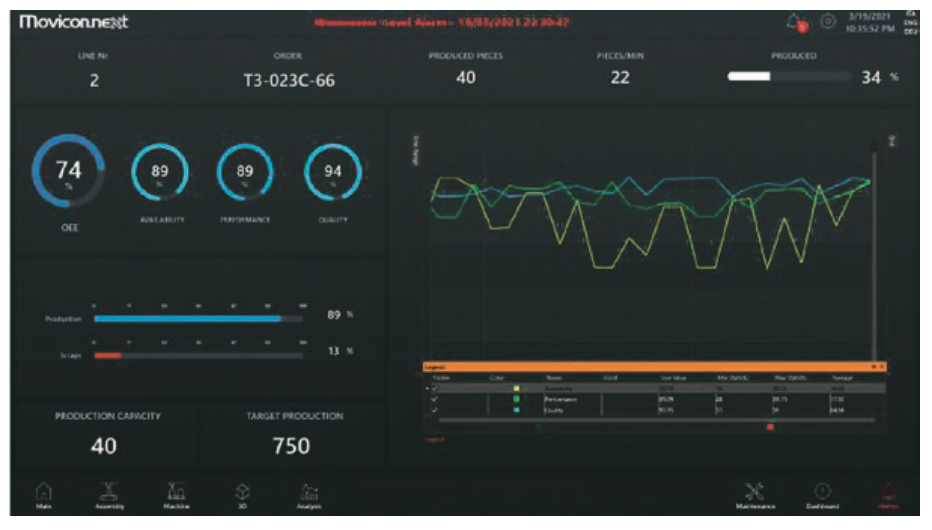
Maszyny obsługujące technologię IIoT
Większość pakietów oprogramowania HMI łączy się z jednym lub większą liczbą typów sterowników PLC. Jednak bardziej zaawansowane mogą się łączyć z innymi czujnikami zlokalizowanymi na krawędzi sieci, przy wykorzystaniu takich protokołów, jak EtherNet/IP, Modbus TCP i OPC UA. Oprogramowanie HMI, które wspiera technologię IIoT, powinno także obsługiwać protokół MQTT (message queuing telemetry transport) w celu komunikacji z chmurą. Te platformy oprogramowania często mają dodatkowe funkcjonalności, takie jak połączenia sieciowe zdalne i mobilne.
Co prawda oprogramowanie HMI może zawierać kilka podstawowych funkcji analitycznych, jednak często konieczne jest wykorzystanie uzupełniających pakietów oprogramowania z rozszerzonymi funkcjami, aby zrealizować analizę danych na poziomie całej fabryki i ocenę efektywności energetycznej zakładu. Dlatego też zintegrowana platforma obsługująca technologię IIoT, lokalne i rozproszone interfejsy HMI, komputerowy system sterowania procesami technologicznymi i produkcji (SCADA) oraz analizę danych jest najlepszym rozwiązaniem umożliwiającym skalowalność (fot. 1).
Programy obsługujące połączenia sieciowe, przesył, wizualizację oraz analizę danych są dostępne indywidualnie lub w postaci pakietu produktów. Czasami są wstępnie wgrane dla wygody do sterowników brzegowych lub komputerów IPC. Posiadając właściwy sprzęt, oprogramowanie HMI oraz analityczne, można przystosować każdą maszynę do pracy w sieci IIoT.
Wykorzystanie w praktyce przetwarzania danych na krawędzi sieci
Niektóre firmy przemysłowe zajmujące sie opakowaniami i pojemnikami, a także produkujące zróżnicowane wyroby specjalistyczne, uzyskały już korzyści z wdrożenia OEE w swoich zakładach. Rozwiązania przetwarzania danych na krawędzi pozwoliły im na zoptymalizowanie ogólnej wydajności produkcji poprzez monitoring przepływów produkcyjnych w czasie rzeczywistym i obliczanie wskaźników OEE bez przerywania produkcji.
Użytkownicy ci wykorzystali kreatory konfiguracji, pozwalające na stworzenie w czasie rzędu minut projektów obliczania kluczowych wskaźników efektywności KPI, wskaźników efektywności wyposażenia OEE oraz wskaźników przestojów. Kreatory to narzędzia w postaci procedur typu krok po kroku, prowadzące użytkowników na drodze do importowania specyficznych informacji i parametrów, wymaganych do stworzenia całej aplikacji OEE. Operatorzy wykorzystują raporty dashboard do wizualizacji produkcji, receptur, informacji o maszynach, liczby wyprodukowanych jednostek, całkowitego czasu produkcji i przestojów oraz porównania czasu cyklu produkcji – oczekiwanego z rzeczywistym. Te informacje są przechowywane w bazie danych i na ich podstawie można tworzyć szczegółowe raporty. Uzyskane wyniki przyniosły wielkie korzyści dla operatorów linii produkcyjnych oraz kierowników działów produkcji, którzy mogli się skoncentrować na uzyskaniu ustalonych celów poprawy wydajności.
Niektóre firmy decydują się na wykonywanie analityki danych lokalnie, tak więc kierownictwo może podejmować decyzje na szczeblu fabryki. Inne zaś wymagają, aby informacje były dostępne za pomocą chmury, tak aby mogły być połączone z innymi zbiorami danych lub analizowane na poziomie całej floty wyposażenia. Otwarta, modułowa, skalowalna i elastyczna platforma jest idealna do wdrożenia technologii IIoT oraz wykorzystania różnych scenariuszy takiego wdrożenia.
IIoT łączy maszyny z krawędzią sieci oraz przedsiębiorstwem
Analiza przemysłowa może się wydawać tajemnicza i wiele firm uważa, że wdrożenie jakiejkolwiek przynoszącej korzyści inicjatywy IIoT jest na razie poza ich zasięgiem. Koszty i złożoność rozpoczęcia projektu informatycznego typu top-down mogą być odstraszające.
Jednak nowa generacja sprzętu, sieci, protokołów i oprogramowania do analizy danych na krawędzi zmieniła ten tok myślenia. Producenci posiadający duże doświadczenie w technologii operacyjnej fabryk wprowadzili sterowniki brzegowe oraz komputery IPC, które są wystarczająco odporne na ciężkie warunki panujące zarówno na halach produkcyjnych, jak i na maszynach. Ethernet przewodowy i bezprzewodowy, w połączeniu z takimi protokołami komunikacyjnymi, jak OPC UA i MQTT, pozwala użytkownikom podłączyć się do każdego źródła danych zlokalizowanego na krawędzi sieci i wysyłać uzyskane informacje do systemów wyższego poziomu.
Te podstawowe funkcjonalności pozwalają użytkownikom na przechwytywanie wielu zbiorów danych z maszyny czy linii produkcyjnej, na poziomie hali produkcyjnej i całego zakładu. Gdy dostępne jest źródło właściwych danych, użytkownicy mogą wykorzystać interfejsy HMI wyspecjalizowane dla technologii operacyjnej oraz oprogramowanie analityczne, specjalnie opracowane tak, aby było skalowalne od poziomu pojedynczej maszyny do poziomu całego przedsiębiorstwa. Takie podejście jest realistycznym sposobem dla użytkowników końcowych, którzy, budując system inteligencji informacyjnej (information intelligence) dla całego przedsiębiorstwa, powinni rozpocząć działania od wdrożenia technologii IIoT w swoich maszynach.
Silvia Gonzalez jest liderem opracowywania rozwiązań działu automatyki maszyn firmy Emerson.