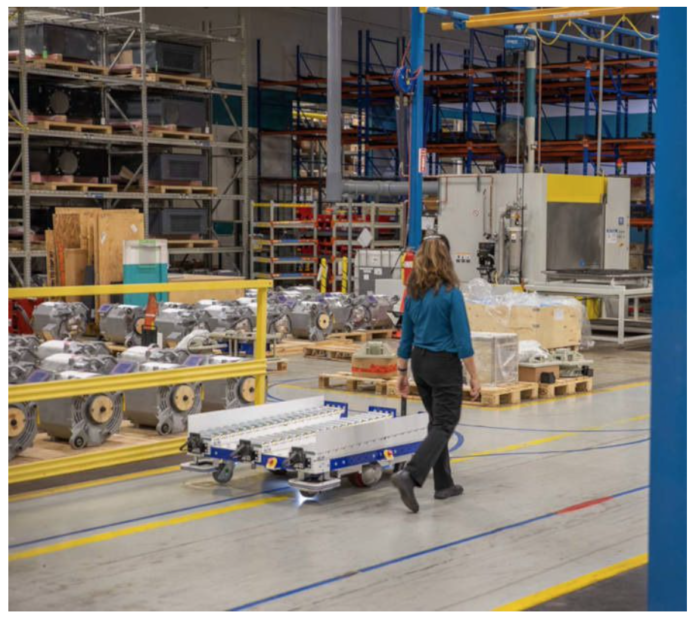
Nowe technologie oraz ulepszenia w oprogramowaniu umożliwiają postęp w zarządzaniu zapasami i przestrzenią magazynową.
Zadania związane z transportem bliskim albo obsługą materiałów, takie jak podnoszenie, przenoszenie, ciągnięcie i pchanie, stanowią źródło problemów związanych z bezpieczeństwem pracowników. W wielu miejscach pracy, w szczególności w przemyśle, zdarzają się wypadki, wskutek których dochodzi do zranienia ludzi.
Według organizacji NSC[1] co roku ma miejsce ponad 4,5 mln wypadków przy pracy, związanych ze zranieniem ludzi. W 2019 roku liczba wypadków śmiertelnych, którym można było zapobiec, wzrosła o 2% i ze względu na to, że technologia ewoluuje, liczba ta może wzrosnąć jeszcze bardziej znacząco.
Bezpieczeństwo i higiena pracy pozostają główną troską pracodawców, a jednym z kluczowych punktów na drodze do redukcji wypadków przy pracy jest zidentyfikowanie ryzyk ergonomicznych, związanych z ręcznym wykonywaniem zadań związanych z transportem bliskim materiałów. Poprzez identyfikację i zmniejszanie tych czynników ryzyka firmy mogą uniknąć ponoszenia ogromnych kosztów, będących konsekwencją wypadków przy pracy. Dobry system obsługi materiałów zwiększy bezpieczeństwo ludzi oraz ich wydajność pracy.
Pojawiające się innowacyjne technologie oraz ulepszenia oprogramowania umożliwiły dokonanie znacznych postępów w sposobie funkcjonowania przedsiębiorstw i zarządzania przez nie swoimi zapasami i przestrzenią. W tym artykule omawiamy siedem nowych technologii, których wykorzystanie zapewni bezpieczeństwo w transporcie bliskim. Warto dokładnie zapoznać się z tymi technologiami i je zastosować.
- Zautomatyzowane systemy magazynowania i pobierania
Zautomatyzowane systemy magazynowania i pobierania[2] umożliwiają bezpieczne zarządzanie różnymi operacjami, związanymi z obsługą materiałów. Pracownicy mogą szybko odbierać towary, układać je na wyznaczonych półkach oraz wyszukiwać je i pobierać. Przedsiębiorstwo uzyskuje dzięki temu korzyści w postaci większej produktywności, lepszej optymalizacji i większej dokładności realizowanych operacji w porównaniu do magazynów tradycyjnych, w których pracownicy wykonują swoje zadania ręcznie.
Technologia AS/RS jest powszechnie wykorzystywana w zakładach produkcyjnych oraz centrach dystrybucyjnych do usprawnienia funkcjonalności magazynów. To zautomatyzowane rozwiązanie zmniejsza potrzebę dokonywania przez pracowników powtarzających się podróży przez niekończące się korytarze w magazynie oraz minimalizuje ruch pomiędzy półkami, oszczędzając powierzchnię półek i podłogi magazynu. Ponadto AS/RS jest łatwiejsza do monitorowania i zarządzania stanami magazynowymi za pomocą systemów sterowanych komputerowo.
- Systemy GTP
Obecnie istnieje coraz większy nacisk na firmy zajmujące się handlem elektronicznym (e-commerce), aby szybciej dostarczały towary do klientów. Efektywnym rozwiązaniem dostarczania towarów do ustalonego punktu odbioru jest tu system GTP[3]. Pomaga on realizować zamówienia, eliminując nieprzynoszący zysku czas pomiędzy odbiorami. Dzięki temu liczba zrealizowanych zadań w przeliczeniu na osobę wzrasta.
W odróżnieniu od systemów PTG[4], w których to pracownicy odbierają produkty, dany towar jest dostarczany bezpośrednio do pracownika, co zwiększa dokładność i efektywność procesu odbierania zamówień. Dlatego też w systemie GTP towar jest zawsze obsługiwany bezpiecznie, dokładnie śledzony i rozliczany. Jeszcze większe znaczenie ma fakt, że system ten zmniejsza liczbę wypadków przy pracy, w tym skutkujących zranieniem ludzi, poprzez umożliwienie pracownikom wygodnego przygotowania zamówień na ergonomicznym stanowisku pracy.
- Autonomiczne roboty mobilne
Kolejną innowacją, oferującą wysoką elastyczność w transporcie bliskim, są autonomiczne roboty mobilne[5]. Roboty tego typu są wykorzystywane do realizacji takich zadań jak lokalizowanie, podnoszenie i przenoszenie towarów w zakładach przemysłowych lub w środowisku niebezpiecznym, w którym wykonywanie tych zadań przez ludzi byłoby dla nich szkodliwe lub wręcz niemożliwe.
Roboty AMR, wykonując różne zadania, potrafią rozpoznawać swoje otoczenie i odpowiednio na nie reagować. Dlatego nie wymagają bezpośredniego nadzorowania przy użyciu zaawansowanych technologii jednoczesnej lokalizacji i mapowania. Dzięki tej elastyczności roboty AMR są użyteczne w bardzo wielu gałęziach przemysłu oraz aplikacjach. Zwiększają efektywność operacyjną, zapewniają precyzję wykonywanych prac oraz zwiększają bezpieczeństwo ludzi.
- Wózki samojezdne AGV
Jak wskazuje ich nazwa, wózki AGV[6] mogą funkcjonować bez operatora znajdującego się na ich pokładzie, a ich prędkość jest monitorowana. Poza zautomatyzowaniem transportu ciężkich towarów wózki te zwiększają produktywność i efektywność w zakładzie.
Wózki AGV zwiększają bezpieczeństwo w miejscu pracy na różne sposoby. Jednak najważniejsze jest to, że eliminują element ludzki, który jest przyczyną źródłową wielu wypadków przy pracy, z których część powoduje zranienie pracowników.
Wózki te mogą ponadto wykonywać zadania niebezpieczne dla pracowników. Przykładami są tu transport materiałów toksycznych, praca w temperaturach ekstremalnych lub przewożenie ciężkich obiektów.
- Rozwiązania ulepszające proces realizacji zamówień w magazynach
Firmy realizujące łańcuch dostaw oraz obsługę materiałów mogą obecnie uzyskiwać korzyści ze stosowania ramion robotycznych, szczególnie do wykonywania zadań związanych z realizacją zamówień, takich jak sortowanie oraz podnoszenie i umieszczanie towarów w odpowiednim pojemniku[7]. Dzięki najnowszym postępom w dziedzinie chwytaków robotów[8] przedsiębiorstwa mogą zwiększyć swoją produktywność, szczególnie w sytuacjach, gdy realizowane są w nich operacje polegające na wykonywaniu powtarzalnych czynności, które muszą być precyzyjne.
Bezpieczeństwo pracowników w magazynach jest jednym z największych zmartwień dla pracodawców, a rozwiązania piece-picking spełniają coraz większe wymagania dotyczące bezpieczeństwa pracowników. Niektóre systemy potrafią obsługiwać cała gamę różnych towarów o różnych gabarytach i kształtach lub pobierać towary z konkretnej strefy. Technologia ta ponadto redukuje koszty pracy i zwiększa produktywność, tworząc bezpieczniejsze i wydajniejsze środowisko pracy.
- Internet Rzeczy
Innowacje w technologii Internetu Rzeczy (IoT) mają na celu usprawnienie zbierania danych pod kątem BHP, przewidywania zagrożeń oraz zapobiegania zranieniom ludzi w miejscu pracy. Aplikacje IoT chronią niebezpieczne miejsca pracy poprzez wykrywanie potencjalnie zagrażających sytuacji i chroniąc pracowników przed niebezpiecznymi sytuacjami.
Wraz z zaawansowanymi systemami technologicznymi, zintegrowanymi z miejscami pracy, czujniki w postaci urządzeń ubieralnych[9] czy mobilne urządzenia inteligentne mogą być wykorzystywane przez pracowników do zapisu informacji na temat warunków panujących w ich miejscu pracy. Jednocześnie do odpowiedniego personelu w zakładzie mogą być wysyłane dane i alarmy, co pomoże tym specjalistom w identyfikacji wszelkich potencjalnych zagrożeń dla pracowników i zapobieżeniu wypadkom przy pracy w przyszłości.
- Urządzeniami ubieralne, noszone przez pracowników
Pojawienie się technologii urządzeń ubieralnych dało firmom możliwości zwiększania swojej konkurencyjności dzięki zwiększeniu produktywności oraz efektywności. Ponadto technologia ta wpłynęła pozytywnie na utrzymywanie odpowiedniego poziomu BHP. Wraz z pojawianiem się różnych nowych technologii popularność zyskuje kolejny trend – inteligentne urządzenia ubieralne. W przypadku pracowników mogą to być środki ochrony osobistej, takie jak kaski i kombinezony lub gadżety osobiste, w tym smartwatche, które pomagają mierzyć kluczowe parametry zdrowotne pracowników, co sprzyja zwiększaniu bezpieczeństwa i zdrowia zatrudnionych.
Przedsiębiorstwa mogą monitorować warunki BHP w swoich zakładach poprzez analizowanie i optymalizowanie operacji przemysłowych za pomocą inteligentnych urządzeń ubieralnych. Urządzenia te pomagają zbierać wartościowe informacje w czasie rzeczywistym. To ponadto pomaga przedsiębiorstwom w podejmowaniu skutecznych decyzji oraz utrzymywaniu właściwego poziomu BHP.
Podsumowanie
Zapewnienie bezpieczeństwa pracownikom powinno być jednym z najważniejszych priorytetów pracodawców na całym świecie. Przedsiębiorstwa w celu zapewnienia ludziom najwyższego poziomu BHP muszą wdrażać różne systemy obsługi materiałów, które wymagają minimum udziału człowieka. Dzięki systemom transportu bliskiego opartym na technologii pracownicy nie będą musieli podnosić lub przenosić ciężkich towarów. To redukuje możliwość wystąpienia wypadków przy pracy, zranienia ludzi lub innych problemów zdrowotnych pracowników, takich jak ból krzyża i przemęczenie.
- W 2020 r. podczas kryzysu spowodowanego pandemią COVID-19 wartość światowego rynku sprzętu do obsługi materiałów była szacowana na 118,7 mld USD. Według raportu firmy ReportLinker przewiduje się, że do roku 2026 liczba ta osiągnie 156 mld USD, przy czym skumulowany roczny wskaźnik wzrostu (CAGR) w analizowanym okresie będzie wynosić 4,7%.
- Według portalu Inside Indiana Business producent wózków widłowych Toyota Material Handling z siedzibą w Columbus (stan Indiana) twierdzi, że obecnie dokonuje największego wzbogacenia oferty produktowej w całej historii firmy. Pojawiły się 22 nowe modele, co sygnalizuje także, że producent w coraz większym stopniu adaptuje napęd elektryczny. Firma Toyota twierdzi, że reaguje w ten sposób na rosnący popyt na maszyny energooszczędne. Wg niej około 70% wszystkich produktów do obsługi materiałów posiadało napęd elektryczny. Toyota oczekuje, że ta zmiana będzie kontynuowana w przypadku wózków widłowych, wózków podnośnikowych oraz podnośników do palet. Od dziesięcioleci produkty firmy Toyota posiadały silniki spalinowe, zasilane gazem ziemnym lub LPG.
- Według portalu Material Handling and Logistics „połączenie rekordowo wysokich generalnych podwyżek stawek, zapowiedziane przez firmy zajmujące się transportem paczek oraz transportem częściowym (drobnicowym; LTL) jesienią 2021 wraz z trwającym wysokim poziomem cen przewoźników zajmujących się transportem całopojazdowym (FTL) spowoduje, że koszty transportu poszybują na rekordowo wysoki poziom w 2022 roku”. Wynika to z badań rynku, opublikowanych 13 stycznia 2022 przez firmy Cowen Research i AFS Logistics.
Luke Goldwin jest doświadczonym menedżerem marketingu treści z udokumentowaną historią pracy w branży łańcucha dostaw oraz logistyki. Obecnie pracuje w firmie FlexCube, gdzie tworzy wartościowe treści, związane z intralogistyką oraz transportem bliskim materiałów.
[1] National Safety Council; organizacja użyteczności publicznej typu non-profit, promująca zdrowie i bezpieczeństwo w USA
[2] układnice magazynowe; ang. automated storage and retrieval systems; AS/RS
[3] „towar do człowieka”, ang. goods-to-perso
[4] „człowiek do towaru”, ang. person-to-goods
[5] ang. autonomous mobile robot; AMR
[6] ang. automated guided vehicles; dosł. pojazdy ze zautomatyzowanym prowadzeniem
[7] ang. piece-picking
[8] ang. end-of-arm tooling; EOAT
[9] galanterii elektronicznej; ang. wearables