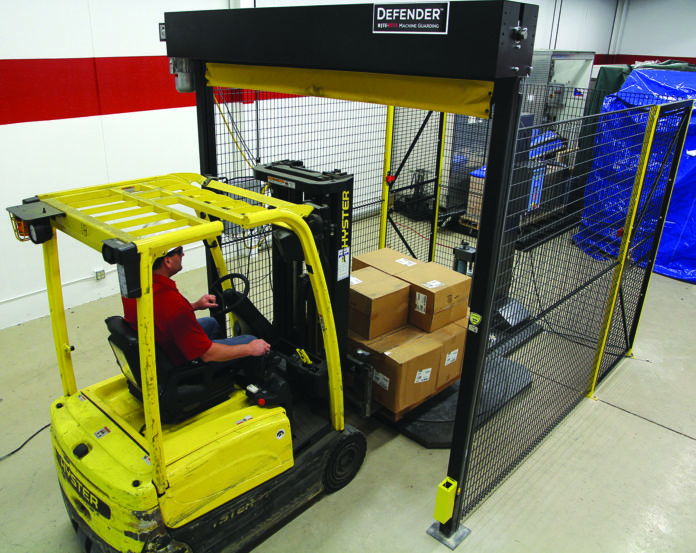
Bariery fizyczne, stanowiące istotny element zabezpieczenia pracowników w wielu aplikacjach przemysłowych, są często najlepszym wyborem po dokonaniu oceny ryzyka w miejscach, gdzie ludzie stykają się i współpracują bezpośrednio z maszynami.
Zawsze gdy praca ręczna może być automatyzowana, warto to robić ze względu na możliwy wzrost wydajności operacyjnej zakładu przemysłowego. Jednak należy pamiętać, że brak zastosowania odpowiednich zabezpieczeń dla pracowników może spowodować zagrożenia prowadzące do naruszenia przepisów i zasad BHP. Ponieważ we współczesnych warunkach rynkowych realizacja zamówień wymaga coraz krótszego czasu, co jest związane m.in. ze spełnianiem rosnących wymagań klientów dokonujących zakupów w sklepach internetowych, dyrektorzy zakładów przemysłowych poszukują każdego dostępnego rozwiązania, które pomoże im rozwiązać ten problem.
Maszyny mogą wykonywać żmudne i monotonne zadania, jak np. pakowanie w folię termokurczliwą, znacznie szybciej i zwykle z większą precyzją niż ludzie. Biorąc pod uwagę, że na całym świecie w przemyśle pracuje ponad 1,5 mln robotów przemysłowych, trudno wyobrazić sobie sprawne funkcjonowanie produkcji bez tych rozwiązań.
Niestety, istnieje zwiększone ryzyko zagrożeń w przypadkach, gdy maszyny i pracownicy koegzystują ze sobą, w szczególności na tych samych stanowiskach roboczych. Personel kierowniczy fabryk, który nadzoruje instalowanie nowego sprzętu, musi być świadomy tych zagrożeń i pomyśleć o zabezpieczeniach dla swoich pracowników. Nie jest to tylko najlepsza praktyka, ale konieczność wynikająca z przepisów prawnych.
Zrozumienie regulacji i przepisów
Punkt interakcji (point-of-interaction – POI) pomiędzy robotami a pracownikami, podobnie jak w przypadku obsługiwania działających maszyn, występuje tam, gdzie często istnieje jednocześnie największe ryzyko oraz brak jednoznaczności przepisów normujących zasady pracy i jej bezpieczeństwa.
Najlepiej więc rozpocząć działania od zapoznania się z regulacjami w tym zakresie. W przypadku rynku amerykańskiego są to przepisy opracowywane przez OSHA (amerykańska Agencja Bezpieczeństwa i Zdrowia w Pracy). Według dyrektywy OSHA 29 CFR 1910.212(a)(3)(ii), „Wymagania ogólne dla wszystkich maszyn” (General Requirements of All Machines) procesy realizowane w kluczowych punktach interakcji muszą być zabezpieczane za pomocą osłon lub innych środków w celu zabezpieczania pracowników przed zranieniem. W Europie kwestie te reguluje norma EN ISO 14120, w Polsce wprowadzona norma PN-EN ISO 14120 „Bezpieczeństwo – Osłony – Ogólne wymagania dotyczące projektowania i budowy osłon stałych i ruchomych”.
Przepisy dyrektywy OSHA stwierdzają: „Punkt obsługi maszyn, w którym pracownik jest narażony na zranienie, powinien być zabezpieczony. Urządzenie zabezpieczające powinno być zatem zgodne ze wszystkimi mającymi zastosowanie normami lub, w przypadku braku mających zastosowanie szczegółowych norm i standardów, powinno być tak zaprojektowane i skonstruowane, aby chroniło operatora przed dostaniem się jakiejkolwiek części jego ciała do strefy niebezpiecznej podczas cyklu operacyjnego”.
W klauzuli OSHA: Obowiązki Ogólne, sekcja 5 podano:
a) Każdy pracodawca
1. Musi zapewnić każdemu pracownikowi takie miejsce i warunki pracy, które są wolne od rozpoznanych zagrożeń, które powodują lub mogą spowodować śmierć albo poważne uszkodzenie ciała.
2. Musi przestrzegać standardów BHP, podanych w niniejszym akcie.
Te regulacje OSHA wskazują wyraźnie, że bezpieczeństwa w pracy nie można ignorować. Jednak, ponieważ procesy realizowane w zakładach ciągle są modernizowane i ulepszane, a opracowane niemal 50 lat temu przez OSHA przepisy nie nadążają za postępami technologicznymi, obecnie są opracowywane nowe wytyczne bazujące na najlepszych praktykach.
Stowarzyszenie Przemysłu Robotycznego (Robotics Industries Association – RIA) opracowało dla rynku amerykańskiego normę ANSI/R15.06 Bezpieczeństwo Robotów Przemysłowych (Industrial Robot Safety). Odnosi się ona do norm obowiązujących również w Polsce: PN-EN ISO 10218-1 „Roboty i urządzenia dla robotyki – Wymagania bezpieczeństwa dla robotów przemysłowych – Część 1: Roboty” oraz ISO 10218-2: „Część 2: System robotowy i integracja”. Normy te odnoszą się do robotów, systemów robotowych (robotycznych) oraz integracji. Norma amerykańska RIA 15.06 została napisana w celu zharmonizowania norm już obowiązujących w Europie. W swojej istocie norma ta wymaga lepszej identyfikacji zagrożeń, uwzględniania ruchu robotów oraz specyficznych zadań, które one wykonują. Zgodnie z jej zapisami można zaprogramować bezpieczny ruch robota przy użyciu oprogramowania, które kontroluje obszar operacyjny robota i prędkość, z jaką może się on poruszać.
W pierwszej kolejności należy wykonać ocenę ryzyka
Norma RIA R15.06 wymaga wykonania oceny ryzyka. Wymienione wcześniej zabezpieczenia stanowisk obsługi maszyn są być może najtrudniejszym aspektem tej regulacji. Dotyczy to bowiem zarówno oddzielenia człowieka od maszyny, jak i zwiększenia bezpieczeństwa oraz efektywności prac.
Podczas dokonywania analizy należy wziąć pod uwagę wiele szczegółów. Niektóre z nich to układ albo projekt procesu, ograniczenia systemu oraz prawidłowe zidentyfikowanie wszystkich związanych z tym zagrożeń, opracowanie metod eliminacji zagrożeń i zmniejszenia ryzyka.
W wytycznych OSHA podano następujący wzór na obliczenie najlepszej odległości zabezpieczenia od maszyny:
DS = K · T + DPF
gdzie DS oznacza bezpieczną odległość (safety distance), K – maksymalną prędkość, z jaką człowiek może się zbliżyć do źródła zagrożenia, T (time) – całkowity czas do zatrzymania niebezpiecznego ruchu, DPF (depth penetration factor) – współczynnik penetracji głębi urządzenia zabezpieczającego (określa odległość, jaką pokona pracownik, zanim zostanie wykryty przez to urządzenie, np. kurtynę świetlną).
Na podstawie tego wzoru zabezpieczenie ma zaleconą lokalizację, wyznaczoną w oparciu o pewną liczbę czynników, w tym zagrożenia wtórne, które mogą wyrządzić szkodę operatorowi maszyny. Wzór ma duże znaczenie dla określania, które z zabezpieczeń powinno zostać zastosowane i gdzie w danej fabryce.

Bezpieczeństwo w punkcie interakcji
Najbardziej podstawowymi urządzeniami stosowanymi do zabezpieczania pracowników realizujących operacje związane z produkcją przemysłową są: kurtyny świetlne, skanery laserowe oraz inne urządzenia wykrywające obecność. Po przerwaniu wiązki światła podczerwonego tych urządzeń następuje zatrzymanie zautomatyzowanego procesu.
W wielu przypadkach urządzenia te zapewniają akceptowalny poziom bezpieczeństwa. Jednak nie zawsze są one najlepszym wyborem do wszystkich aplikacji, szczególnie po wykonaniu oceny ryzyka. Jednym z największych problemów jest to, że pracownicy muszą przestrzegać reguły trzymania się od maszyn w pewnej odległości, wyznaczonej ze wzoru podanego przez OSHA, aby zmniejszyć ryzyko zranienia. Może to doprowadzić do konieczności budowania większych gniazd produkcyjnych, co z kolei pociąga za sobą dodatkowy czas, który potrzebny będzie pracownikom na pokonanie dystansu pomiędzy maszyną a obszarem bezpiecznym, gdy maszyna pracuje. W praktyce często pracownicy omijają ten system za pomocą skrótów, narażając się na niebezpieczeństwo. Ponadto pracownik, który wchodzi do gniazda produkcyjnego, może nadal być narażony na niebezpieczeństwo zranienia, gdy części maszyny po jej wyłączeniu jeszcze obracają się na skutek bezwładności.
Zautomatyzowane drzwi-bariery ochronne
Szybko działające drzwi-bariery ochronne lub zwijane kurtyny są często najlepszym wyborem, ponieważ każde z tych zabezpieczeń może wyeliminować zarówno narażenie na niebezpieczne ruchome części maszyn, jak i zagrożenia wtórne, których źródłem jest proces technologiczny/produkcji, potencjalnie eliminując ryzyko oraz stopień narażenia na niebezpieczeństwo.
W połączeniu z blokadami bezpieczeństwa (do poziomu zapewnienia bezpieczeństwa PLe, Kategorii 4 wg PN-EN ISO 13849-1 „Bezpieczeństwo maszyn – Elementy systemów sterowania związane z bezpieczeństwem – Część 1: Ogólne zasady projektowania” zautomatyzowane drzwi-bariery i kurtyny rozwijane oferują zwiększony poziom ochrony dla zabezpieczania punktu obsługi.
Ograniczają one dostęp do procesu i zabezpieczają przed zagrożeniami wtórnymi, takimi jak dym, iskry, opary lub odpryski, związanymi ze zautomatyzowanymi operacjami spawalniczymi, przez umieszczenie bariery pomiędzy operatorami maszyn a poruszającymi się częściami maszyn. Te typy zabezpieczeń w wielu sytuacjach są idealną alternatywą dla kurtyn świetlnych oraz innych urządzeń wykrywających obecność.
Bezpieczniejsza i bardziej efektywna automatyka
Wzór OSHA na bezpieczną odległość nie ma zastosowania dla zautomatyzowanych drzwi-barier z blokadą, ponieważ nie ma tam konieczności uwzględniania współczynnika penetracji głębi, co pozwala na umieszczenie zabezpieczenia znacznie bliżej obszaru niebezpiecznego. To koreluje z mniejszą przestrzenią przeznaczoną na „strefę bezpieczeństwa” i daje w wyniku końcowym zmniejszenie objętości gniazda produkcyjnego.
Eliminowanie przypadkowych wejść do gniazda produkcyjnego jest dodatkową korzyścią wynikającą ze stosowania zautomatyzowanych drzwi-barier z blokadą. W odróżnieniu od niewidzialnych wiązek podczerwieni w urządzeniach wykrywających obecność, bariery i osłony stanowią zabezpieczenie, które można zobaczyć. Fizyczna separacja, jaką realizują, jest wyraźnym wskaźnikiem optycznym, że operator maszyny wykonuje jakieś zadanie.
Prawidłowe zabezpieczanie operacji realizowanych przez maszyny
Personel kierowniczy musi zawsze poszukiwać nowej technologii, która może przyśpieszyć operacje realizowane w zakładzie przemysłowym. Jednak musi on także mieć przede wszystkim na uwadze przepisy BHP i uwzględniać je przed podjęciem każdej decyzji w tej sprawie. Ocena ryzyka w celu określenia najlepszego zabezpieczenia dla pracowników obsługujących maszynę jest tu pierwszym krokiem. Po sprecyzowaniu wyborów na podstawie wymagań przepisów BHP należy przeanalizować taką opcję zabezpieczeń, która najmniej wpływa na wydajność produkcji – zabezpieczenie fizyczne w postaci zautomatyzowanych drzwi-barier.
John Ritter jest menedżerem produktu w firmie Rite-Hite Doors.