Wykorzystanie systemów IT w nowoczesnych procesach produkcyjnych jest dziś konieczne, jeśli chcemy skutecznie konkurować na rynku. Konferencja „Digital Manufacturing” w całości poświęcono roli IT w procesie produkcyjnym. Konferencja zgromadziła informatyków z małych i dużych organizacji produkcyjnych, którzy chcieli dowiedzieć się, jak cyfryzacja procesów może zmienić funkcjonowanie ich przedsiębiorstw. Konferencja odbyła się w hotelu Ibis Styles mieszczącym się w samym centrum Wrocławia, stolicy przemysłowego dolnego śląska. W konferencji uczestniczyli dyrektorzy IT, kierownicy projektów, programiści, a także kierownicy produkcji, inżynierowie i menadżerzy.
Do tematyki konferencji wprowadził uczestników Michael Majchrzak, założyciel wydawnictwa Trade Media International, które od 2003 roku publikuje na polskim, czeskim, słowackim i rosyjskim rynku znane magazyny specjalistyczne przeznaczone dla kadry inżynierskiej takie jak: Control Engineering, Inżynieria & Utrzymanie Ruchu, Design News oraz Manufacturing Systems Information (MSI) na licencji ich amerykańskich wydawców.
W trakcie pierwszej z prelekcji dr inż. Jerzy Greblicki dyrektor Branży Radical Automation w firmie AIUT przedstawił automatyzację procesów produkcyjnych z wykorzystaniem platform AGV (autonomicznych pojazdów) jako elementu Radical Automation. Jak stwierdził, w ostatnim czasie zakres automatyzacji procesów produkcyjnych obejmuje zarówno linie produkcyjne, jak i ich otoczenie. Użycie autonomicznych platform AGV zarówno w procesach logistycznych, jak i bezpośrednio na produkcji jest naturalnym elementem tego procesu. Natomiast wyzwaniem staje się nadzór i śledzenie procesu z wykorzystaniem rozwiązań z zakresu przemysłowego internetu rzeczy (Industrial IoT) i analizy danych. Na pewno ważna jest gotowość do zmian w zakresie organizacji procesów produkcyjnych w tym automatyzacja, robotyzacja, integracja platform AGV z liniami produkcyjnymi oraz stosowanie ich jako platform montażowych. Dziś trzeba też coraz częściej stosować elastyczne linie montażowe.

W kolejnym wystąpieniu o zapobieganiu awariom, monitorowaniu oraz o diagnostyce sieci PROFINET mówił Marek Grdeń właściciel firmy Stercontrol. Przedstawił najczęstsze przyczyny występowania problemów w sieciach PROFINET. Sposoby ich monitorowania oraz rekomendacje, w jaki sposób im zapobiegać już na etapie wdrożenia sieci w zakładzie. Firma Stercontrol jest między innymi autoryzowanym dystrybutorem firm Siemens oraz Harting, oraz partnerem firmy Indu-Sol na terenie Polski. Zwrócił uwagę słuchaczy na problem obciążenia sieci (network load) i że chwilowe szczytowe obciążenie sieci może wpływać na czas odświeżania.
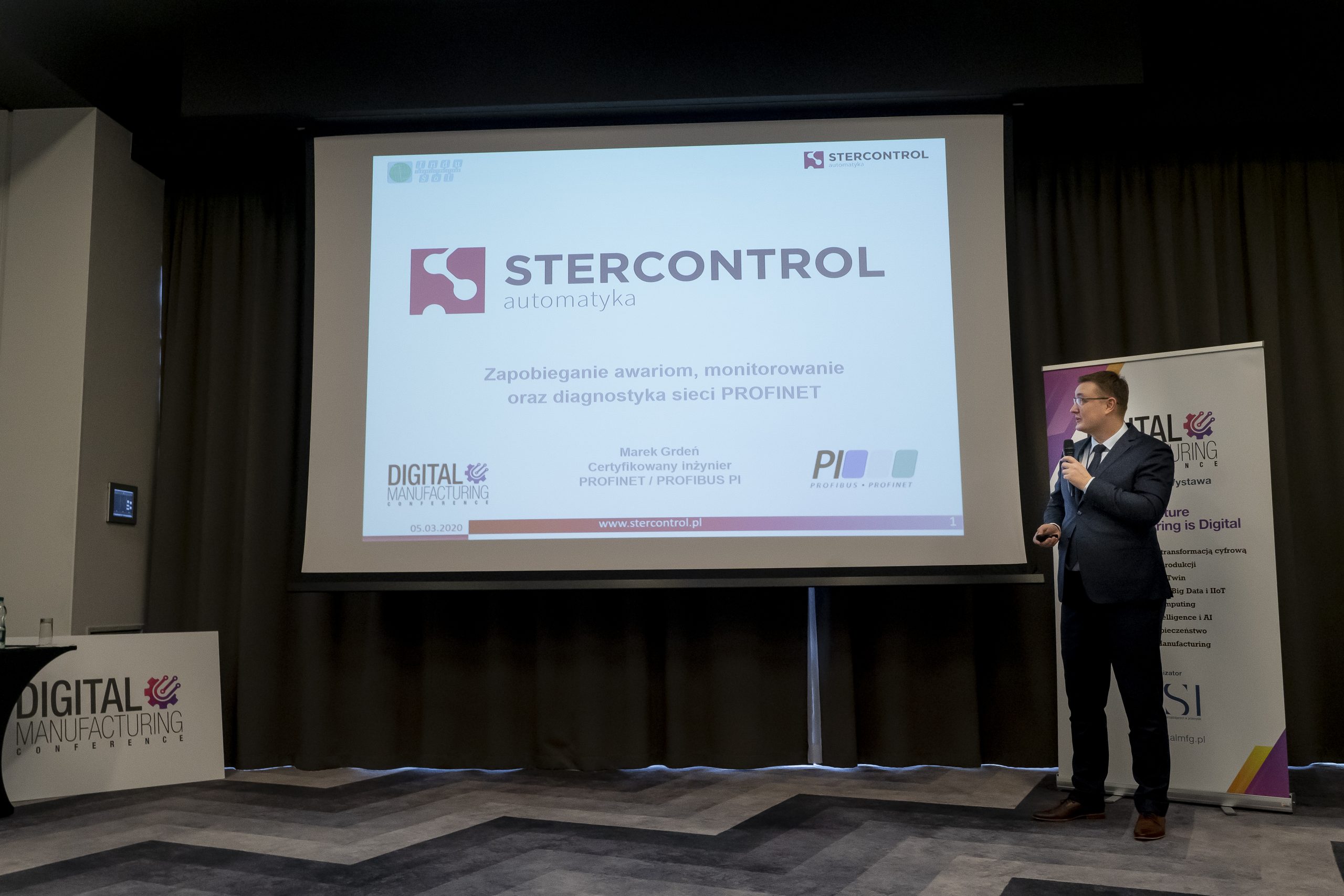
Przemysł 4.0, Fabryka 4.0, Wyzwania IT 4.0 – tak zatytułował swoją prezentacją Marcin Strzelczyk starszy konsultant Systemów IT w firmie Exence. Przedstawił wybrane możliwości oferowanych przez firmę rozwiązań i pokazał, w jaki sposób współczesna organizacja może być zarządzaną/wspierana przez inteligentny system informatyczny. Możliwość sterowania procesami produkcyjnymi na halach, powiązania i przepływ informacji na przykładach działu UR, Produkcji wiąże się z potrzebą reorganizacji systemów informatycznych, których niezbędnym elementem jest również zmiana technologii informatycznych. Dzięki współpracy firmy z największymi dostawcami i producentami technologii IT może ona oferować najnowsze technologie oraz gwarantuje techniczne i merytoryczne wsparcie na każdym etapie współpracy. Mówił między innymi o Systemie eProdukcja – oprogramowaniu klasy SFC (Shop Floor Control), które jest narzędziem wspomagającym planowanie i monitorowanie produkcji z poziomu hali produkcyjnej. Przedstawił też eAudit — System Wspomagający Inspekcję oraz praktyczne wykorzystanie technologii NFC.

Tymoteusz Wojniak z firmy SterControl przedstawił wykorzystanie technologii chmury IIoT do zdalnych rozwiązań związanych ze sterownikami PLC i rozwiązania firmy HMS Network. Omówił aspekty gromadzenia danych i związanego z tym bezpieczeństwa cybernetycznego. Chmura Talk2M działa od ponad 10 lat i łączy ponad 250 tys. maszyn w fabrykach na całym świecie i służy inżynierom zajmującym się serwisem, którzy chcą rozwiązać problemy ze swoim sprzętem. Zapewniając technologię bezpiecznego zdalnego dostępu do PLC za pośrednictwem chmury VPN, rozwiązanie eWON pomaga zbierać dane z systemu sterowania w hali produkcyjnej i bezpiecznie przekazywać je do interfejsu użytkownika w celu przetwarzania. W trakcie prezentacji przeanalizowano możliwości integracji w zakresie gromadzenia danych ze sterowników PLC dla projektów IIoT oraz aspekty bezpieczeństwa cybernetycznego.

Paweł Kużdowicz członek zarządu w firmie abas Business Solutions Poland przedstawił uczestnikom konferencji sposoby na uniknięcie turbulencji w procesie transformacji cyfrowej w przemyśle. Jak stwierdził, cyfryzacja w przemyśle to więcej niż tylko wdrożenie innowacyjnych technologii. Omówił, czym jest, a czym nie jest digitalizacja i jaka jest rola redefinicji modelu biznesowego w procesie adaptacji do zmieniającego się otoczenia. Przedstawił zagadnienia związane z chmurą danych. Także o locie organizacji ku dojrzałości cyfrowej i sztuce miękkiego lądowania, czyli o sposobie na osiągnięcia biznesowego sukcesu w erze cyfryzacji.

Jak wiadomo, coraz większe znaczenie w nowoczesnej produkcji ma wykorzystanie technologii druku 3D. O faktach i mitach związanych z drukiem 3D w produkcji mówił w trakcie swojej prelekcji Michał Kowalczyk Senior Sales Manager w firmie Omni 3D. Czy druk 3D z powodzeniem może zastąpić części metalowe? Jak drukarki 3D radzą sobie z produkcją niskoseryjną? Jakie są najlepsze metody do tworzenia skomplikowanych elementów i czy druk 3D jest rewolucją w utrzymaniu ruchu? To potania, na które szukał odpowiedzi. Nie zgodził się z tezą, że druk 3D nie może zastąpić metalu – wykonanie identycznej turbiny pompy próżniowej z mosiądzu bądź stali nierdzewnej byłoby znacznie droższe, a czas oczekiwania o wiele dłuższy. Druk 3D może o 90% obniżyć koszty wytworzenie funkcjonalnego prototypu, co pozwala na precyzyjne przetestowanie modelu. Nie jest też prawdą, że wydruki nie mają gładkiej powierzchni, bo można zastosować postprocessing.

Jak uwolnić supermoce ukryte w produkcji? To pytanie, które zadał Dariusz Karwasiński Board Member w firmie ilabo. Jak stwierdził w trakcie swojej prezentacji, postępująca automatyzacja produkcji niesie ze sobą coraz więcej korzyści, ale również stawia przed nami niemałą liczbę różnorodnych wyzwań. Mamy do czynienia z coraz większą liczbą danych, opisujących coraz bardziej rozbudowane procesy produkcyjne. Jak z tych danych złożyć w całość garść informacji? Jak z takich informacji zbudować wiedzę? Jakie „super moce” są potrzebne, aby użyć tej wiedzy w sposób, który pozwoli nam produkować więcej, taniej i lepiej? To pytania, na które odpowiedzi mogli usłyszeć uczestnicy tej sesji.
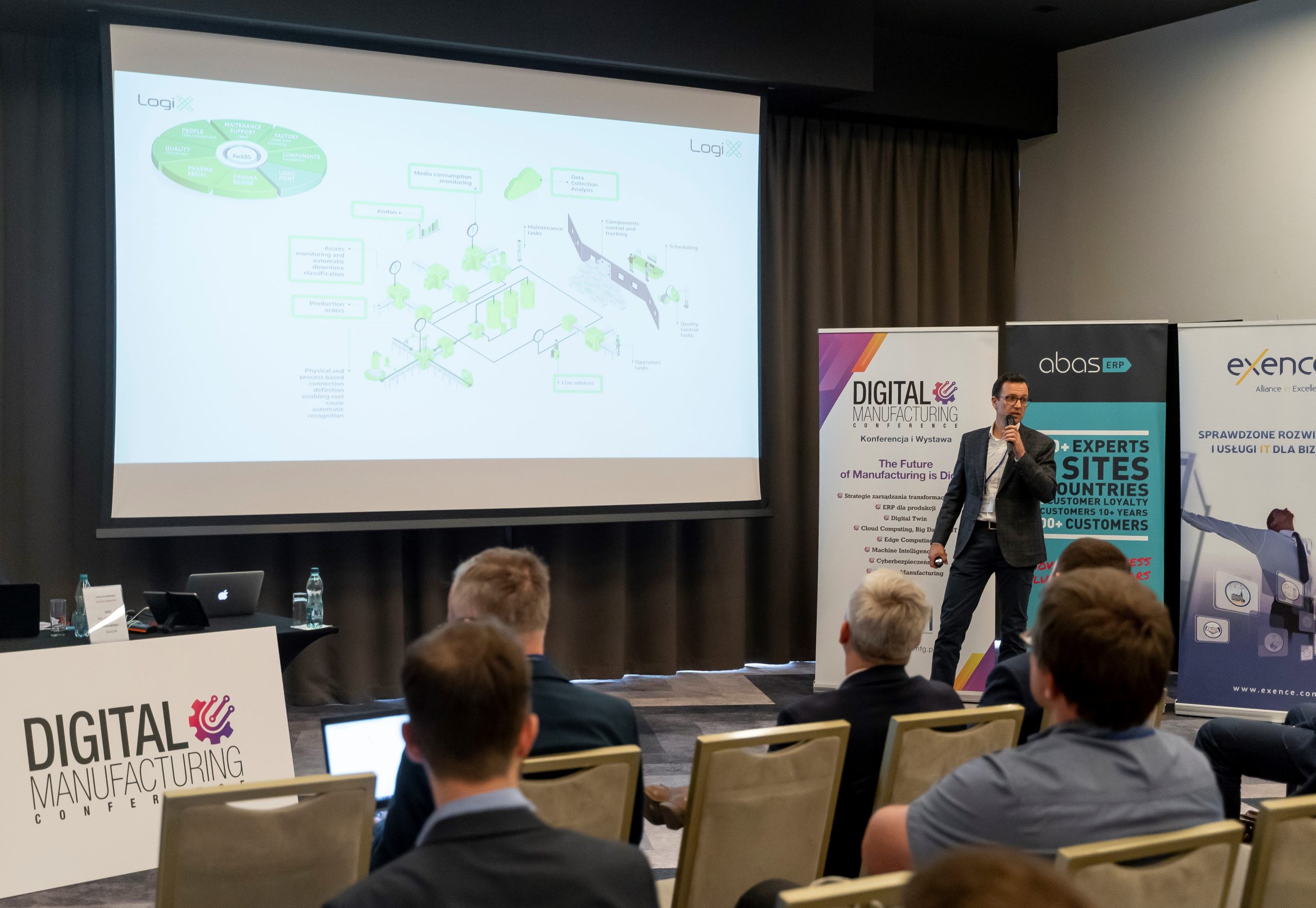
W kolejnym wystąpieniu Filip Polit menadżer sprzedaży krajowej w firmie FlexSim InterMarium przedstawił FlexSim case study dotyczące optymalizacja procesów produkcyjnych i logistycznych. Jak mówił, dynamicznie rozwijające się przedsiębiorstwa stoją przed koniecznością szybkiej i skutecznej adaptacji do potrzeb klientów. Niejednokrotnie prowadzi to do potrzeby wdrażania zmian w procesie produkcyjnym i/lub logistycznym, przebudowy linii czy nawet rozbudowy zakładu. Wiąże się to z ryzykiem inwestycyjnym, zatrzymaniem produkcji, jak również niepewnością czy planowane zmiany będą prowadzić do oczekiwanych rezultatów. Omówił projekty symulacyjne będące wirtualnym odzwierciedleniem rzeczywistych systemów produkcyjnych i logistycznych realizowanych przed wdrożeniem inwestycji w życie.

W panelu dyskusyjnym o produkcji w erze cyfrowej i związanych z tym wyzwaniach oraz szansach dla polskich producentów rozmawiali: Jerzy Greblicki dyrektor Branży Radical Automation w firmie AIUT, Tomasz Haiduk prezes Instytutu Industry 4.0, Jarosław Smulski Senior Program Manager w IDC Polska, Witold Aleksander Cempel prezes zarządu FlexSim InterMarium, Paweł Siembab Global Client Executive w Dassault Systemes oraz Bernard Hajduk Sales Executive w firmie abas Business Solutions Poland. Jak wiadomo, Polska gospodarka odniosła jeden z największych sukcesów wśród krajów rozwijających się od czasu transformacji na początku lat 90. Jedną z głównych sił napędowych był sektor przemysłowy, na który przypada ponad 40% polskiego PKB. Koszty pracy stają się dla Polski mniej istotne jako przewaga konkurencyjna, dlatego polskie firmy będą musiały zwiększać swoje możliwości produkcyjne poprzez inwestycje w nowe technologie. W trakcie dyskusji paneliści poruszyli kwestię obecnego stanu technologii w polskich firmach produkcyjnych oraz w jaki sposób polscy producenci mogą usprawnić swoją działalność dzięki inwestycjom w nowe technologie.

W kolejnej prelekcji, o pełnej digitalizacja, czyli o czwartej rewolucji przemysłowej mówił Tomasz Haiduk prezes Instytutu Industry 4.0. Poruszył problematykę wykorzystania technologii cyfrowego bliźniaka w praktyce produkcyjnej. Jak stwierdził, Przemysł 4.0 przyniósł zmiany paradygmatu biznesowego, a dzięki wykorzystaniu „cyfrowego bliźniaka” możliwa stała się integracji wszystkich obszarów technicznych w jednym modelu danych. Czas niezbędny na przetestowanie pomysłu, zaprojektowanie produktu, wdrożenie produkcji oraz jej optymalizację skraca się dramatycznie. IoT i sieci społecznościowe stają się źródłem wiedzy o potrzebach rynku i Klientów. Nowoczesna produkcja wymaga jednak nie tylko technologii cyfrowych, ale także perfekcyjnej organizacji i zmian w mentalności pracowników. Cyfrowy bliźniak to pole do eksperymentów w tym możliwość nieograniczonych eksperymentów, impuls do kreatywności / nowego myślenia, szybkie dojście do optymalnego rozwiązania, polityka „zero waste” oraz narzędzie do ciągłej optymalizacji.

Marek Orłowski dyrektor handlowy w firmie Datacomp przedstawił w swojej prezentacji zagadnienia przepływu informacji napędzanego nowoczesnymi technologiami. Jak stwierdził Marek Orłowski, w dobie informatyzacji dostęp do aktualnych informacji ma kluczowe znaczenie przy podejmowaniu trafnych decyzji biznesowych. Coraz większa liczba gromadzonych danych może prowadzić do chaosu informacyjnego. Dlatego ich odpowiednia analiza i szybki dostęp do dostosowanych wyników, niezależnie od miejsca i używanego systemu informatycznego, ma tak istotne znaczenie. Taki system, aby sprawnie funkcjonować, musi być zasilony danymi, które muszą zostać wprowadzone, a to często pochłania dużo czasu. Dlatego coraz większą rolę w tym procesie odgrywa sztuczna inteligencja, która po analizie dokumentu podpowie, jaki jest jego typ, do kogo ma być przypisany i jakie treści zawiera. Od tych danych zależy dalsza droga informacji, zanim trafi ona w odpowiednie miejsce. Jak się okazuje, często mamy problem choćby z tym, by znaleźć aktualną wersję pliku. Natomiast 86% pracowników ma problemy ze znalezieniem odpowiedniej informacji. Dlatego potrzebujemy sztucznej inteligencji, zasilania danymi w tym analiz obrazu itp. Wsparcia podczas prelekcji udzielił Panu Markowi Artur Korzeniak – specjalista ds. wdrożeń w firmie Datacomp.


Cyfryzacja przemysłu – moda czy rewolucyjna zmiana? Dlaczego mówimy o czwartej rewolucji przemysłowej? To pytania, które zadał uczestnikom spotkania Jarosław Smulski Senior Program Manager w firmie analitycznej IDC Polska. Podał przykład firmy Volkswagen, która zdecydowała się podłączyć 122 montownie rozsiane po całym świecie do przemysłowej chmury, stawiając przetwarzane tam dane w centrum uwagi. Czy uległ tylko cyfrowej modzie, czy też wyznacza nowe standardy w produkcji? Do czego potrzebujemy Przemysłowego 5G, Przetwarzania na Brzegu (Edge Computing) czy cyfrowych ekosystemów? Co kryje się pod marketingowymi hasłami światowych liderów przemysłu? Co to oznacza dla mojego biznesu? To pytania, na które starał się znaleźć odpowiedź. Transformacja cyfrowa (DX) jest tu i teraz, a 90% dużych organizacji już przeprowadziło projekty IT wspierające DX. Z kolei 41% wszystkich wydatków technologicznych to te na DX a inicjatywy z tym związane przynoszą trzykrotny wzrost przychodów. Zwrócił też między innymi uwagę, że IoT jest układem nerwowym „wszystkiego”. W 2021 roku 40% producentów platform IoT będzie integrować platformy symulacyjne, systemy, aby dostarczyć rozwiązania „cyfrowego bliźniaka”; 70% producentów będzie ich używać do symulacji i oceny scenariuszy, redukując liczbę błędów infrastruktury o 30%.
To wystąpienie okazało się bardzo dobrym podsumowaniem Konferencji, przekonując uczestników, że warto inwestować w rozwiązania związane z cyfrową produkcją.
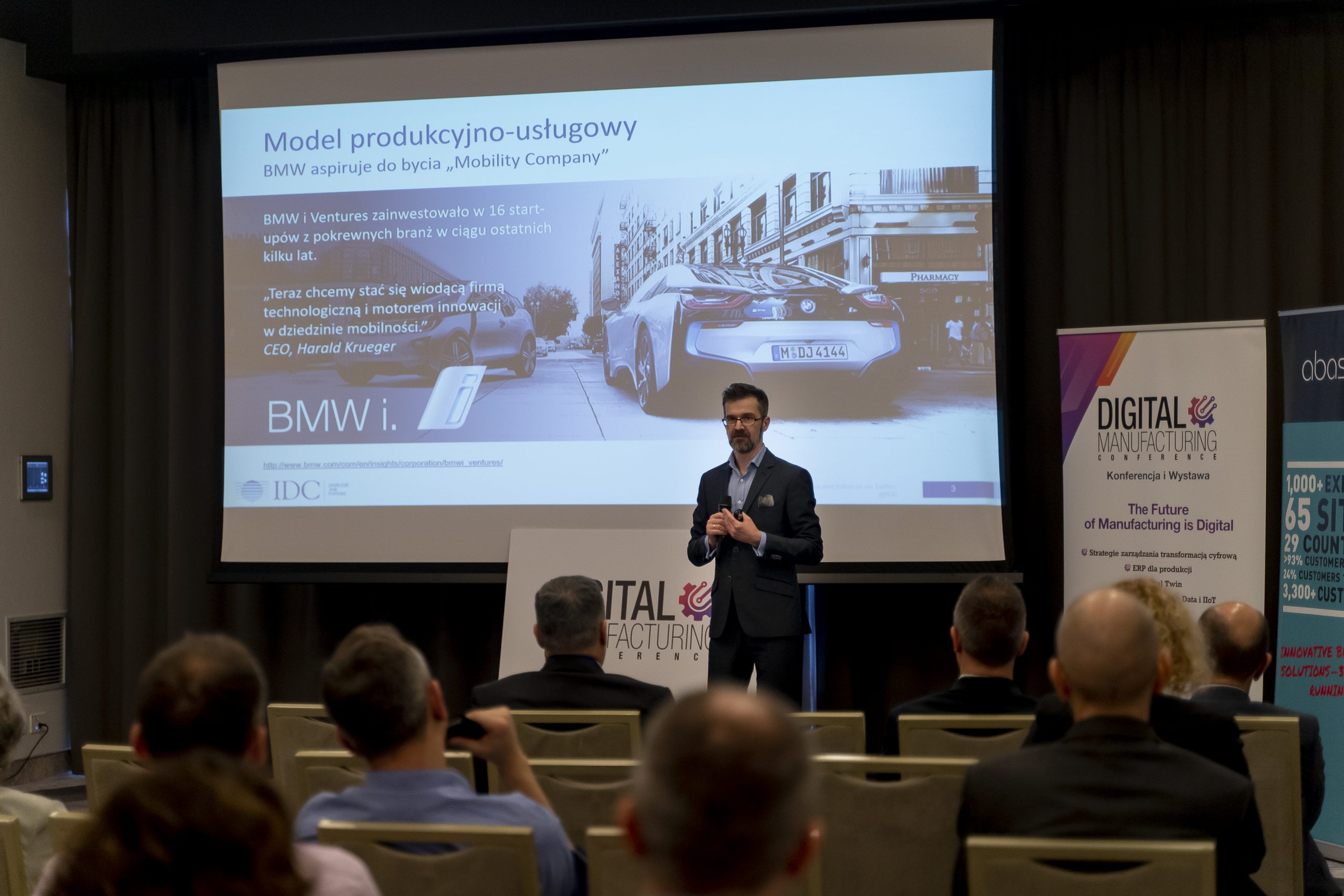
Jak zawsze konferencja była też okazją do nawiązania bezpośrednich kontaktów z wystawcami towarzyszącymi imprezie oraz pomiędzy uczestnikami i prelegentami. Wszyscy podkreślali znaczenie, jakie ma pozyskiwanie wiedzy i kontaktów właśnie w taki sposób. Duże zainteresowanie tym wydarzeniem to efekt bardzo aktualnej dziś tematyki i doboru merytorycznych prelegentów.
Bohdan Szafrański