Inżynierowie procesu, uzbrojeni w narzędzia do zaawansowanej analizy danych, mogą mieć lepszą kontrolę nad realizowanymi operacjami produkcji.
Szybkość, z jaką szczepionki przeciw COVID-19 stają się dostępne, jest niespotykana – od fazy opracowania do testów klinicznych i masowej produkcji mija wyjątkowo jak na farmaceutyki krótki czas. Świat się nigdy nie zetknął z taką sytuacją. W pewnym sensie mieliśmy szczęście, że pandemia wydarzyła się w czasach znacznych postępów w nauce oraz technologii cyfrowych. Wyprodukowanie szczepionki przeciw globalnej pandemii w okresie krótszym od jednego roku jest czymś, co nie byłoby nigdy możliwe bez technologii cyfrowych.
Wiele firm farmaceutycznych musiało borykać się ze złożonymi wyzwaniami technologicznymi podczas masowej produkcji skutecznej i bezpiecznej szczepionki w rekordowym tempie. Tak więc teraz, gdy czas odgrywa największą rolę, producenci szczepionek nie mogą pozwolić sobie na żadne drobne incydenty na linii produkcyjnej, wytwarzanie partii złej jakości produktów czy nieplanowane przestoje, spowodowane awariami sprzętu. Na szczęście bardzo szybka adaptacja rozwiązań dostępnych poprzez technologię Internetu Rzeczy (IoT), takich jak automatyzacja operacji w fabrykach, symulacje procesów oraz zaawansowana analiza danych, pomogły organizacjom stać się bezpieczniejszymi, wydajniejszymi i efektywnymi kosztowo. Jeśli chodzi o wytwarzanie czegoś tak nadzwyczaj ważnego, jak szczepionka przeciw COVID-19, to szczególnie zaawansowana analiza samoobsługowa (ang. self-service analytics) jest przełomem w produkcji i kontroli jakości.
Komponenty jakości szczepionki
Po wybuchu pandemii analiza samoobsługowa znalazła się w centrum uwagi firm farmaceutycznych, gdyż miała pomóc w zapewnieniu im utrzymania wysokich standardów produkowanych szczepionek przeciw COVID-19. Dla firmy farmaceutycznej jakość produktu odnosi się do atrybutów jakości i wydajności surowców wykorzystywanych w procesie produkcji oraz wydajności linii produkcyjnej. Podstawowymi składnikami używanymi do produkcji szczepionek przeciw COVID-19 są: woda, adiuwanty immunologiczne, środki konserwujące i stabilizujące oraz składnik aktywny (antygeny), który zawiera substancje nieaktywne, występujące w ilościach śladowych i niezbędne dla właściwego procesu produkcji. Stan techniczny sprzętu fabrycznego, warunki magazynowania i transportu, pakowanie i obchodzenie się z produktem to inne kluczowe czynniki, mające wpływ na jego jakość.
W firmie farmaceutycznej dobrą praktyką produkcji jest wykorzystywanie systemu sterowania procesem (process control system – PCS) w celu zapewnienia niezmiennych poziomów jakości, kosztów i wydajności, jednocześnie zaś bezpieczeństwa pracowników. Innym ważnym komponentem zapewnienia jakości produktu jest samoobsługowa analiza danych, która może wykorzystywać dane szeregów czasowych dotyczące procesu produkcji. Dane szeregów czasowych są przechwytywane z wielu czujników zainstalowanych na całej linii produkcyjnej i analizowane w celu dostarczenia specjalistom wartościowych informacji, które są wykorzystywane do zwiększenia wydajności operacyjnej oraz kontrolowania jakości produktów. Analiza samoobsługowa umożliwia też zintegrowanie kluczowych informacji dotyczących partii produkcyjnych, które następnie mogą być ocenione i śledzone dla celów kontroli jakości.
Zapewnienie jakości (quality assurances – QA) daje pewność, że standardy jakości są stale przestrzegane. Mogą być wykonywane pewne działania, mające na celu zapobieganie problemom z jakością, poprzez wykorzystywanie systematycznych porównań wyników pomiarów parametrów ze znanymi standardami, monitorowanie procesów i zmiennych produkcyjnych, a także ustanowienie związanej z tym pętli sprzężenia zwrotnego. W przypadku szczepionek kluczowymi zmiennymi parametrami produkcyjnymi są: pH, temperatura oraz czas cyklu produkcyjnego. Powinny być one monitorowane, ponieważ mogą wpływać na jakość produktu. Generowane przez czujniki dane szeregów czasowych tych zmiennych także powinny być monitorowane.
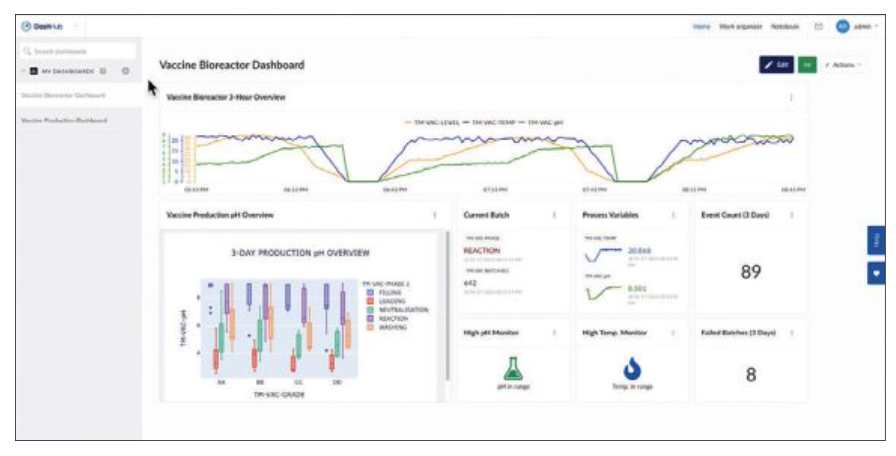
Wykorzystanie potęgi zaawansowanej analizy danych
Badacze danych (data scientists) od dawna wykorzystywali generowane przez czujniki dane szeregów czasowych, które mogły zawierać też dane z innych źródeł, do stworzenia monitoringu procesów oraz modeli predykcyjnych, wykorzystywanych do rozwiązywania skomplikowanych problemów związanych z procesami technologicznymi i produkcji. To podejście do rozwiązywania problemów jest czasochłonne i wymagające pod względem analizy danych. Wymaga też zaangażowania ekspertów z tej dziedziny, tak więc może być wykonalne tylko dla najbardziej kluczowych problemów związanych z procesami.
Jednak specjaliści od procesów oraz eksperci dziedzinowi (subject matter experts – SME) przeprowadzają już codziennie pewne analizy danych, wykonując badania i optymalizowanie swoich procesów oraz rozwiązując problemy. Importowanie danych z czujników oraz integrowanie z nimi informacji kontekstowych z innych źródeł często obejmuje odfiltrowanie okresów nieodnoszących się do tematu oraz wykonywanie manipulacji matematycznych, a także obliczanie korelacji. Wszystko to jest procesem iteracyjnym. Podobnie jak w przypadku podejść stosowanych przez badaczy danych, tradycyjne podejścia do analiz procesów bywają czasochłonne. Staranna eksploracja danych, która wymagałaby wielu dni pracy, a czasem nawet tygodni, jest często wykonywana tylko w przypadku najpoważniejszych problemów.
Bardziej praktycznym, efektywnym podejściem jest pozwolenie ekspertom SME, aby sami wykonywali bardziej zaawansowane analizy. Będą oni mogli wtedy wykorzystać swoją wiedzę techniczną na temat procesów oraz dane szeregów czasowych do monitorowania, analizowania i przewidywania procesów przemysłowych. Przykładem tego podejścia jest wykorzystywanie przez ekspertów dziedzinowych samoobsługowej zaawansowanej analizy danych do optymalizacji produkcji szczepionki przeciw COVID-19.
Eksperci SME potrafili interpretować dane szeregów czasowych do odkrywania posiadających duże znaczenie informacji dotyczących procesów produkcyjnych w dowolnej chwili. Dane te były łatwo wizualizowane, zaś wzorce łatwo rozpoznawane. Ponadto możliwości uczenia maszynowego (machine learning – ML) narzędzia do analizy samoobsługowej wspierały użytkowników, pozwalając im na szybsze rozwiązywanie problemów i optymalizowanie operacji.
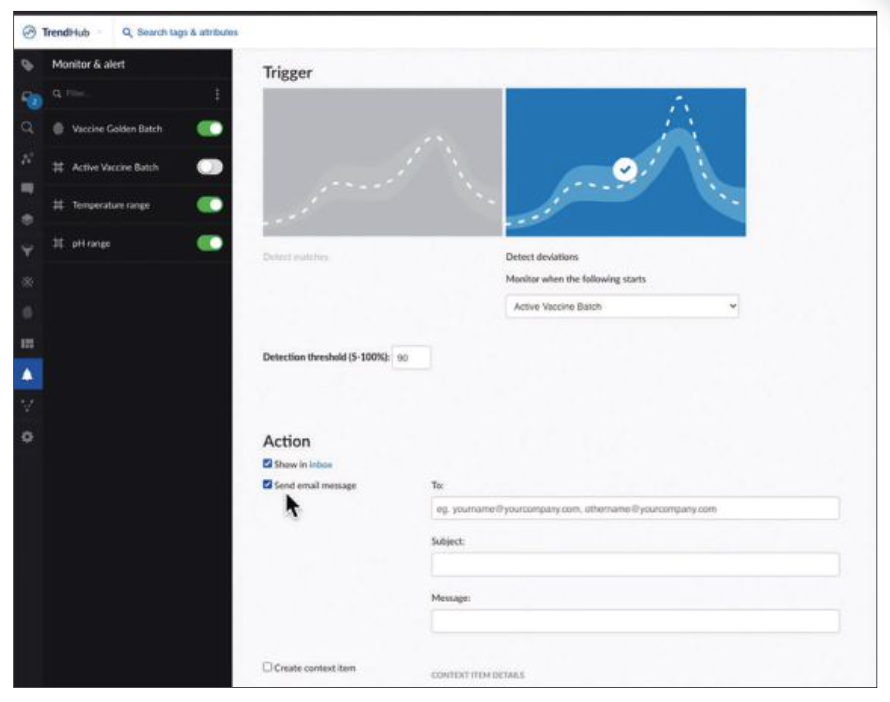
Wyeliminowanie silosów danych jest kolejnym wkładem do kontroli jakości produktu
Zaawansowana analiza danych ma też wpływ na kontrolę jakości produktu umożliwiając ekspertom dziedzinowym kontekstualizację ich danych. Podczas procesu produkcji na jakość wyrobu oraz wydajność operacyjną mogą mieć wpływ różne zdarzenia, takie jak zatrzymania maszyn w celach konserwacyjnych, anomalie procesów, pogorszenie się stanu technicznego zasobów, a także zdarzenia zewnętrzne i straty na produkcji. Zwykle takie informacje są przechowywane w różnych silosach danych przez różne działy firmy przemysłowej, co uniemożliwia transparentność danych. Za pomocą samoobsługowej analizy danych można zbierać informacje o wspomnianych zdarzeniach i zapisywać je na wspólnej platformie, aby były dostępne dla wszystkich pracowników i działów zakładu, którzy mogą wtedy uzyskać dodatkowe praktyczne informacje na temat kontroli jakości i wydajności operacyjnej. W wyniku tego następuje wyeliminowanie silosów danych.
Pełne wykorzystanie danych kontekstowych może mieć zasadnicze znaczenie. Jak widać na przykładzie produkcji szczepionki przeciw COVID-19, każda partia wyrobów ma swoje własne metadane, takie jak numer partii, czas cyklu produkcyjnego, dane dotyczące zgodności parametrów z wymaganymi etc. Wszystkie te dane mogą być rozszerzone o wyniki testów laboratoryjnych. Takie informacje umożliwiają bardziej miarodajną i szybsza ocenę najlepszych partii produkcyjnych, Eksperci od procesów mogą wtedy stworzyć „odcisk palca złotej partii” („golden batch fingerprint” – rys. 3) lub wskaźnik referencyjny „dobrej partii”, który może być wykorzystany do oceniania przyszłych partii produkcyjnych. Dane dotyczące partii niespełniających wymaganych parametrów mogą być wtedy łatwiej wyznaczone i mogą posłużyć jako niezawodny punkt startowy do przeprowadzenia analizy dochodzeniowej, którą opiszemy w szczegółach na przypadku praktycznym.
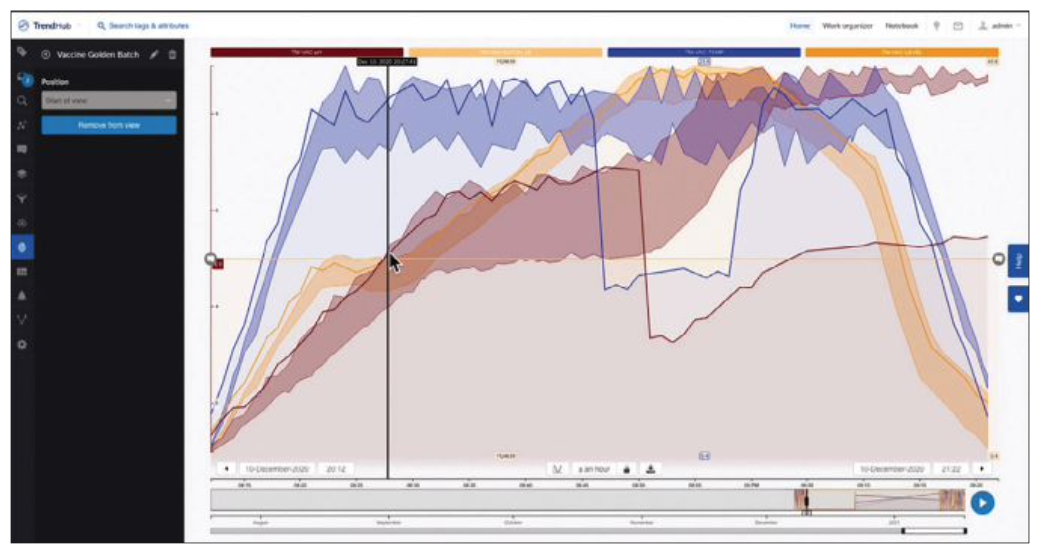
Zarządzanie kontrolą jakości
Gdy produkcja szczepionki przeciw COVID-19 była już w toku, zespół ekspertów od procesów z pewnej firmy farmaceutycznej rozpoznał problem z jakością szczepionki. Było ewidentne, że musieli oni „przekopać się” przez dane z czujników, aby szybko zidentyfikować ten problem. Wykorzystali pewne samoobsługowe narzędzie analityczne, aby obejrzeć wszystkie szczegóły trendów danych z produkcji szczepionki oraz innych kontekstowych informacji dotyczących procesu. To narzędzie analityczne poprowadziło ekspertów przez kluczowe etapy badania problemu i umożliwiło im pełne zrozumienie, jakie czynniki wpływają na jakość partii produkcyjnych szczepionki. Na podstawie tych informacji można było określić działania, jakie należało podjąć, aby rozwiązać problem z jakością produkowanej szczepionki.
Fazy dochodzenia przeprowadzonego przez ekspertów były następujące:
Faza 1. Ocena problemu
Zespół ekspertów w pierwszej kolejności uruchomił kwerendę, aby określić trendy danych dotyczących wadliwej partii szczepionki. Wykorzystywane przez nich samoobsługowe narzędzie analityczne może generować raporty graficzne typu dashboard, które zawierają kafelki będące graficzną reprezentacją ważnych punktów danych procesowych. Analizując kafelki narysowane na wykresie, zespół stwierdził, że czas cyklu niedawnej partii produkcyjnej był znacznie dłuższy od normalnego. Eksperci byli też w stanie określić, że niektóre z faz procesu produkcji miały większe odchylenie od innych.
Następnie eksperci sprawdzili na wykresie kafelki „wartości bieżącej” i stwierdzili, że proces ogólnie zachowywał się w oczekiwanych granicach parametrów sterowania. Na koniec, poszukując rozbieżności w jakości materiału, eksperci przekopali się do danych kafelków, które zawierały kontekstowe informacje dotyczące procesu, aby przyjrzeć się konkretnym zdarzeniom i wyszukać rozbieżności w parametrach partii produkcyjnej. Chociaż w ciągu procesu występowały różne zdarzenia, to eksperci interesowali się tylko zdarzeniami związanymi z „wadliwą partią”, które prezentowały niezgodność z wymaganymi parametrami jakości.
Faza 2. Analiza głównej przyczyny problemu
Ta faza obejmowała analizę głównej przyczyny problemu z jakością szczepionki. Eksperci od procesu badali w niej zdarzenia podczas produkcji „wadliwej partii”, aby określić przyczynę niższej jakości produktu. Ponieważ wartość pH jest kluczowym czynnikiem w określaniu końcowych parametrów jakości produktu, zespół rozpoczął działania właśnie od analizy pH. Zespół wykorzystał „silnik zaleceń” narzędzia analitycznego („recommendation engine”), który wykorzystuje technologię uczenia maszynowego do wygenerowania zarówno zalecanych rozwiązań problemu, jak i odpowiedzi na pytania związane z procesem. Eksperci dowiedzieli się więc, że spadek temperatury spowodował spadek wartości pH. A zatem byli oni przekonani, że prawdopodobnie to spadek temperatury był przyczyną niższej jakości produktu.
Porównując wadliwą partię produktu z zestawem uprzednio zatwierdzonych pod względem jakości partii (zapisanych jako „złote odciski palca”) eksperci byli w stanie precyzyjne określić, w którym miejscu nastąpiło odchylenie parametrów procesu produkcji od wymaganych. Odkryli, że temperatura spadła poniżej wartości progowej, co spowodowało spadek wartości pH poniżej wartości progowej. Wszystkie te odkrycia poparły ich hipotezę o przyczynie wyprodukowania wadliwej partii szczepionki.
Faza 3. Działania proaktywne
Aby zapobiec odchyłkom parametrów szczepionki w przyszłości oraz utrzymywać parametry partii produkcyjnych w granicach idealnych wartości progowych, zespół ekspertów skonfigurował monitor programowy, który mógł pracować w połączeniu z „odciskiem palca złotej partii”. W ten sposób, gdy wykrywana jest dowolna odchyłka parametrów procesu, samoobsługowe narzędzie analityczne automatycznie wysyła e-mail alarmowy do personelu fabryki, zawiadamiając o wystąpieniu potencjalnego problemu. Alarm ten daje pracownikom wystarczającą ilość czasu, aby mogli zająć się tym problemem i zapobiec wyprodukowaniu wadliwej partii.
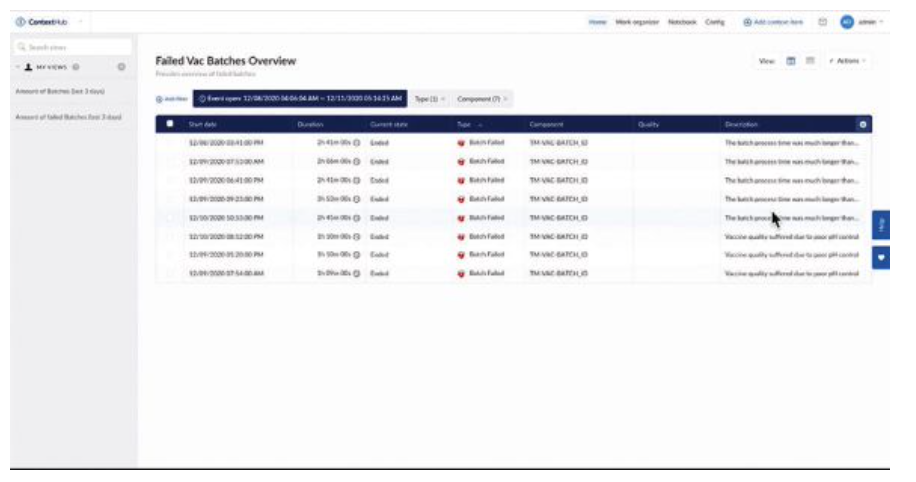
Wnioski końcowe
Technologia umożliwiona przez Internet Rzeczy może dostarczać działom operacyjnym zakładów przemysłowych lepszych informacji praktycznych. Nie było to możliwe nigdy przedtem. Dzięki samoobsługowemu narzędziu do zaawansowanej analizy danych kluczowe procesy realizowane w przemyśle farmaceutycznym, takie jak produkcja szczepionek przeciw COVID-19 oraz innych leków ratujących życie, może obecnie czerpać korzyści z kontroli jakości opartej na danych i zoptymalizowanej technologii produkcji. Oznacza to także, że firmy farmaceutyczne mogą zmniejszyć straty produkcyjne oraz ilość kosztownych przypadków niepowodzeń, spowodowanych anomaliami podczas produkcji.
Jest to tylko jeden z przykładów, jak samoobsługowa analiza danych naprawdę spełnia swoją rolę i napędza optymalizację procesów przemysłowych. Szczepionki przeciw COVID-19 pomagają ratować ludzkie życie i w powrocie świata do normalności. Bez takiego samoobsługowego narzędzia analitycznego produkcja szczepionek mogłaby nigdy nie spełnić swoich celów, wymaganych do ochrony i ratowania życia ludzi oraz powrocie społeczeństwa do normalnego funkcjonowania.
Michael Chang jest analitykiem danych w firmie TrendMiner.