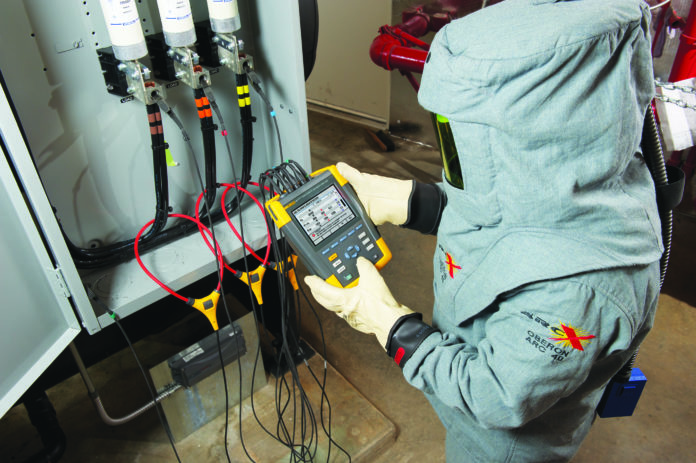
Wybór pomiędzy zainstalowaniem czujników na sprzęcie a wykorzystaniem obsługiwanych przez techników przenośnych narzędzi pomiarowych i testowych zależy od dojrzałości stosowanej w zakładzie strategii utrzymania ruchu.
W każdej gałęzi przemysłu nieplanowany przestój może oznaczać straty rzędu setek tysięcy, a nawet milionów dolarów. Nieoczekiwane zatrzymanie produkcji może być także powodem marnotrawstwa produktów, uszkodzeń sprzętu oraz znacznego zagrożenia bezpieczeństwa. Personel kierowniczy zakładów przemysłowych wie, że utrzymywanie stabilności i ciągłości realizowanych operacji zależy od regularnego wykonywania konserwacji sprzętu oraz szybkiego wykrywania potencjalnych problemów. Na szczęście w ciągu ostatniej dekady na rynku pojawiły się nowe rodzaje narzędzi pomiarowych, monitorujących i testujących, które pomagają służbom utrzymania ruchu w osiąganiu tych celów.
Bardzo szybki obecnie postęp w rozwoju technologii bezprzewodowego monitorowania stanu technicznego maszyn i urządzeń (wireless condition monitoring – CdM) sprawia, że personel zakładów przemysłu procesowego dysponuje nowymi narzędziami praktycznego i bardziej opłacalnego sposobu ciągłego monitoringu takich parametrów, jak napięcie zasilania, temperatura, moc oraz drgania, również w sprzęcie mniej kluczowym dla zakładu. Większość nowoczesnych czujników bezprzewodowych może być zainstalowana szybko i tak samo szybko zdemontowana. Powstaje zatem pytanie: kiedy należy wykorzystywać CdM, a kiedy polegać na tradycyjnej konserwacji zapobiegawczej (preventive maintenance – PM), prowadzonej z użyciem narzędzi przenośnych, takich jak multimetry cyfrowe, sondy temperaturowe, kamery termowizyjne czy mierniki drgań?
Jak można oczekiwać, na to pytanie istnieje więcej niż tylko jedna dobra odpowiedź. To, które rozwiązanie będzie najlepsze dla zakładu, zależy od tego, na jakim etapie znajduje się on pod względem niezawodności i dojrzałości strategii UR oraz ile korzyści dla aplikacji mogą wnieść nowe technologie czujników.
Identyfikacja strategii
Określenie etapu, w jakim znajduje się zakład na drodze do niezawodności, obejmuje wyznaczenie, jaki procent zasobów wykorzystywany jest na zasadzie „praca aż do wystąpienia awarii” (run-to-fail), jaki procent objęty jest strategiami konserwacji zapobiegawczej, a jaki konserwacją prognozowaną (predictive maintenance – PdM). Strategie niezawodności mogą być zdefiniowane w formule systematycznego podejścia do opracowywania nowych wymagań dla UR tam, gdzie nie istnieją dotąd żadne reguły, co ma na celu optymalizację istniejącego programu.
Połączenie działań z zakresu UR z trybem awaryjnym ma kluczowe znaczenie dla skutecznego zastosowania każdej strategii niezawodności. Taki stan możliwy jest do osiągnięcia za pomocą sprawdzonych koncepcji, metod i technik: konserwacji ukierunkowanej na niezawodność (reliability-centered maintenance), optymalizacji konserwacji PM oraz analizy trybu awaryjnego i jego skutków. Są one skupione na opracowaniu zadań serwisowych i konserwacyjnych ukierunkowanych na: czas, stan techniczny lub wyszukiwanie awarii. Koncepcja realizacji tych zadań tworzy program utrzymania ruchu, który jest opracowany pod kątem minimalizacji degradacji systemu i komponentów. Program ten zapewnia, że sprzęt cały czas pracuje optymalnie.
Czasami mylone są pojęcia dotyczące konserwacji zapobiegawczej i prognozowanej. Konserwacja zapobiegawcza jest strategią wykonywania prac serwisowych w ustalonych przedziałach czasowych, niezależnie od stanu technicznego zasobu w czasie wykonywania tych prac. Istnieją dwa typy konserwacji PM: remont generalny według harmonogramu oraz wymiana komponentów według harmonogramu. Obydwa działania są wykonywane w ramach zalecanych działań, mających na celu zapobieganie awariom. Innymi słowy, celem strategii konserwacji zapobiegawczej jest przeciwdziałanie tym przyczynom awarii, które są bardziej związane ze starzeniem się podzespołów i materiałów eksploatacyjnych w miarę upływu czasu. Opracowywanie strategii konserwacji PM w celu minimalizowania możliwości wystąpienia awarii nowych maszyn (w początkowym okresie ich eksploatacji), a także tych wynikających z ich normalnego zużycia oraz awarii losowych (określanych również mianem awarii niezwiązanych z wiekiem sprzętu), jest trudne.
Konserwacja prognozowana (PdM) wykorzystuje ocenę stanu technicznego i działania sprzętu podczas jego normalnego funkcjonowania, w celu zidentyfikowania prawdopodobieństwa awarii. CdM jest podzbiorem PdM, w której rzeczywisty stan techniczny sprzętu jest monitorowany i oceniany w czasie rzeczywistym na podstawie parametrów pracy, tak więc uzyskiwane w ten sposób praktyczne dane mogą być czynnikiem napędowym tych samych działań związanych z konserwacją proaktywną, jak w przypadku PM: remontów głównych według harmonogramów i/lub wymiany podzespołów według harmonogramów. Celem obydwu strategii i działalności jest przywrócenie pełnej wydajności sprzętu.
Strategia CdM, wykorzystująca zainstalowane na sprzęcie czujniki bezprzewodowe, może przynosić korzyści, szczególnie wtedy, gdy wysyłają one dane do zautomatyzowanego systemu wspierającego utrzymanie ruchu CMMS (computerized maintenance management system). System CMMS przechowuje te dane i może alarmować personel kierowniczy oraz planistów, gdy parametry operacyjne sprzętu przekraczają wartości dopuszczalne. Może też automatycznie generować polecenia wykonania prac na podstawie tych alarmów.

Nadanie priorytetów zasobom w zakładzie
Wdrożenie CdM może nie być najlepszym wyborem w odniesieniu do wszystkich zasobów. Problemem jest określenie, które urządzenia powinny być monitorowane za pomocą czujników, aby minimalizować przestoje i marnotrawstwo oraz uzyskać największy zwrot z inwestycji (ROI).
Pierwszym krokiem jest uszeregowanie zasobów na podstawie ich krytyczności. Należy wziąć pod uwagę takie czynniki, jak wpływ utraty każdego z zasobów na ogólny proces. Czy cała fabryka musiałaby wstrzymać pracę, czy tylko jej część? Czy zakład może kontynuować pracę w czasie naprawy, czy wymiany tego urządzenia na nowe? Jaki jest koszt jego naprawy lub wymiany? Jak zasób wpływa na bezpieczeństwo, komfort pracowników oraz środowisko? Jaki jest koszt jego utraty pod kątem zarówno przestoju, jak i potencjalnie zmarnowanego produktu i utraconej produkcji?
Po ustanowieniu krytyczności względnej każdego z zasobów można je odpowiednio uszeregować. Niektóre tanie lub łatwe w wymianie zasoby, takie jak żarówki, są prawdopodobnie najlepiej dopasowane do realizacji podejścia „eksploatacja aż do momentu zużycia”. Podobnie nie trzeba wykonywać ciągłego monitoringu każdego z zasobów. W rzeczywistości nie potrzeba ciągłego pozyskiwania danych z większości zasobów, które funkcjonują poprawnie. Potrzeba natomiast danych ze sprzętu, który przestaje funkcjonować normalnie, co może wskazywać, że realizowane operacje zostaną najprawdopodobniej zakłócone lub przerwane. Po podjęciu decyzji, które dane są nam potrzebne, pomocna może się okazać rozmowa z dostawcą technologii w celu zadecydowania, jak najlepiej mierzyć te dane i jakie są optymalne przedziały czasowe pomiarów.
Wybór zależny od rodzaju zasobu
Często najbardziej krytyczne (i najdroższe) zasoby mają własny wbudowany system monitoringu. Jednak obecnie również nieco tańszy, ale nadal kluczowy sprzęt (Tier 2 and 3 assets – zasoby poziomu 2 i 3) może czerpać korzyści z ciągłego monitoringu za pomocą czujników. Dla tych zasobów strategia polegająca na obchodach i kontroli przeprowadzanej przez techników wyposażonych w narzędzia przenośne może się okazać niewystarczająca. Może się tak zdarzyć, gdy kontrole te nie są wystarczająco częste, aby na czas wychwycić problem i spowodować podjęcie odpowiednich działań w celu zapobieżenia eskalacji tego problemu lub awarii sprzętu.
Jeśli zakład ma sieć bezprzewodową, to monitoring napięcia zasilania w sieciach AC/DC, prądu, mocy, temperatury i drgań za pomocą czujników bezprzewodowych może pomóc we wczesnym zidentyfikowaniu złych warunków pracy sprzętu, które mogą doprowadzić do jego kosztownej awarii. Czujniki bezprzewodowe są ponadto bezpieczniejsze dla personelu zakładu i realizowanych procesów, ponieważ często przy montażu nie wymagają wyłączenia sprzętu, zaś dane z nich mogą być oglądane na urządzeniu mobilnym czy komputerze PC w dowolnym miejscu.
Do grupy najbardziej rozpowszechnionych zasobów, w których można wykorzystać czujniki bezprzewodowe, zalicza się:
→ silniki i napędy silnikowe,
→ pompy odśrodkowe i kompresory,
→ wymienniki ciepła płaszczowo-rurowe oraz reaktory,
→ przenośniki,
→ oprzyrządowanie procesowe,
→ małe transformatory.
Czujniki mogą być też wykorzystane do działań związanych z odbiorem wstępnym.
Dopasowanie technologii i sprzętu
Wybór między wykorzystaniem przenośnych narzędzi pomiarowych i testowych a czujników bezprzewodowych jest procesem nieszablonowym i specyficznym dla każdej fabryki. Należy tu przeanalizować takie czynniki, jak:
→ wiek sprzętu oraz obecną fazę jego cyklu życia – monitorowanie starszego sprzętu za pomocą czujników bezprzewodowych pozwala na jego stałą obserwację i natychmiastowe alarmowanie w przypadkach, gdy parametry tego sprzętu zaczynają przekraczać określone wartości graniczne;
→ zasoby stwarzające problemy – zainstalowanie czujników na zasobach, które chronicznie przestają działać prawidłowo, może zaoszczędzić pracownikom działu utrzymania ruchu konieczności wielokrotnego powtarzania prac konserwacyjnych, jednocześnie zaś umożliwia ciągłe śledzenie w czasie rzeczywistym pracy tych zasobów;
→ dostępność pracowników – jeżeli, podobnie jak w większości fabryk, w dziale utrzymania ruchu jest zbyt mało pracowników do wykonywania niezbędnych prac, zaś wielu z najbardziej doświadczonych techników odchodzi na emeryturę, można zwiększyć możliwości pozostałych pracowników poprzez wyposażenie części zasobów w czujniki bezprzewodowe, co odciąży tych ludzi.
Narzędzia przenośne zawsze będą jednymi z narzędzi stosowanych przez służby utrzymania ruchu. Na przykład sprzęt, który wymaga testowania wibracji jedynie raz w miesiącu, ponieważ nie pracuje w agresywnym środowisku powodującym szybsze zużycie, może być efektywnie utrzymywany w dobrym stanie technicznym dzięki jedynie okresowemu monitorowaniu przez techników wyposażonych w przenośny miernik drgań, chyba że wystąpią problemy. Podobnie w przypadku wielu zasobów można rutynowo odczytywać wielkości elektryczne, temperaturę oraz dokonywać pomiarów termowizyjnych. Z drugiej strony, jeśli wymagany jest monitoring zasobów, do których dostęp jest trudny, znajdujących się w ekstremalnie niebezpiecznym środowisku lub wykazujących sporadycznie trudne do zdiagnozowania symptomy, to czujniki bezprzewodowe mogą zaoszczędzić czas oraz zmniejszyć zagrożenie dla personelu.

Znaczenie monitoringu silników elektrycznych i pomp
Silniki elektryczne są kluczowymi urządzeniami realizującymi wiele funkcji w niemal wszystkich zakładach przemysłu procesowego. Luźne lub niewspółosiowe wały silników mogą przyśpieszyć zużywanie się łożysk oraz spowodować przedwczesne awarie. Wzrost temperatury tych urządzeń z kolei może wskazywać na to, że łożyska wymagają smarowania albo że izolacja elektryczna jest uszkodzona. Problemy tego typu mogą być wykryte wcześniej, za pomocą testowania drgań oraz monitoringu temperatury.
Można zainstalować na odległym sprzęcie bezprzewodowy czujnik drgań w celu identyfikowania niewspółosiowości lub zużywania się łożysk, a następnie użyć przenośnej kamery termowizyjnej do precyzyjnego określenia lokalizacji problemu. Jeśli dany silnik jest zasłonięty przez inny sprzęt, można zamontować przy nim bezprzewodowy czujnik termowizyjny, który w regularnych przedziałach czasowych przechwytuje obrazy z dokładnie tej samej odległości i pod tym samym kątem, jak zrobiłby to technik wyposażony w kamerę. Wyniki tych pomiarów mogą być oglądane na urządzeniu mobilnym, co pozwala na identyfikację problemów, gdy one powstaną.
Pompy są równie kluczowym sprzętem dla wielu procesów. Jeśli takie urządzenie ulega awarii, to może nastąpić zatrzymanie wielu istotnych operacji, co będzie miało negatywne skutki finansowe oraz zagrożenie dla bezpieczeństwa. W takich przypadkach monitoring drgań za pomocą czujnika bezprzewodowego może pomóc we wczesnym powiadamianiu personelu o potencjalnych problemach. Można wykorzystać albo przenośny miernik drgań, albo czujnik drgań do wykrycia zbyt dużych luzów lub niewyważenia wałów pomp, które mogą spowodować przedwczesne zużywanie się łożysk. Ponadto ciągłe monitorowanie prądu i napięcia pompy za pomocą czujników bezprzewodowych może pozwolić wykryć takie problemy, jak zbyt duży prąd rozruchowy silnika pompy oraz sporadyczne skoki lub spadki napięcia, które mogą powodować zadziałanie zabezpieczeń i nieoczekiwane wyłączenia pomp.
Analizowanie jakości energii elektrycznej
Czasami problem nie jest związany ze sprzętem, lecz wynika z jakości energii elektrycznej dostarczanej do zakładu. Tu także istnieje możliwość wyboru pomiędzy wykorzystaniem przenośnych analizatorów jakości energii i bezprzewodowych monitorów energii do zbierania kluczowych danych z instalacji trójfazowych. Oba typy pozwalają na oglądanie trendów i fluktuacji, takich jak niezrównoważenie faz oraz spadki i skoki napięcia.
Analizatory jakości energii mogą także pokazywać zawartość wyższych harmonicznych, wartość współczynnika mocy oraz innych wielkości elektrycznych, które mogą przyczyniać się do wzrostu opłat za energię oraz uszkodzenia sprzętu. Trójfazowe monitory energii mogą przesyłać dane do systemu CMMS, tak więc pracownicy mogą otrzymywać alarmy, gdy parametry pracy sprzętu zaczynają przekraczać ustawione wartości. Główna różnica polega na tym, że analizatory jakości energii dostarczają informacje zarówno na temat pełnego zakresu parametrów energii, jak i oszczędności energii, natomiast monitory energii są narzędziami, które pozwalają na ocenę i potwierdzenie działania sprzętu zgodnie z wartościami podanymi na jego tabliczce znamionowej, aby zapewnić, że sprzęt ten jest zasilany energią o takich parametrach, do jakich został zaprojektowany.
Technika, która wspomaga pracowników
Czujniki bezprzewodowe są w szczególności efektywne w znajdowaniu sporadycznie występujących problemów, które są najtrudniejsze do zdiagnozowania, co zabiera przy tym bardzo dużo czasu. Po zainstalowaniu takich czujników technik może przejść do wykonywania innych zadań, zaś czujniki zbierają dane przez cały dzień, tydzień czy miesiąc, jeśli to konieczne. Jeśli te czujniki są połączone z systemem CMMS, to przesyłane dane mogą być łatwo gromadzone, przetwarzane i oglądane na urządzeniu mobilnym lub komputerze PC. Można tak skonfigurować system CMMS, aby w przypadku przekroczenia określonych wartości parametrów przez określony sprzęt system wysyłał alarm, co umożliwi natychmiastowe podjęcie odpowiednich działań. Kluczem do wykonania tych prac jest posiadanie dobrych odczytów wielkości podstawowych z zasobów.
Podsumowanie
Dane zarówno z czujników bezprzewodowych, jak i narzędzi przenośnych wyposażonych w łączność bezprzewodową mogą być wysłane do tej samej bazy danych w celu dostarczenia kompleksowej historii danego zasobu do analizy i wykonania dokumentacji potwierdzającej spełnianie wymagań wewnątrzzakładowych oraz określonych przepisami. Dzięki bezprzewodowej synchronizacji pomiarów prowadzonych za pomocą narzędzi przenośnych i porównaniu ich z danymi pochodzącymi z czujników bezprzewodowych organizacje uzyskują bardziej kompleksowy obraz stanu technicznego swoich zasobów.
Frederic Baudart jest głównym specjalistą ds. produktów w firmie Fluke. Jest certyfikowanym specjalistą utrzymania ruchu i niezawodności (CMRP). Gregory Perry jest starszym konsultantem ds. niezawodności utrzymania ruchu w firmie Fluke Accelix.