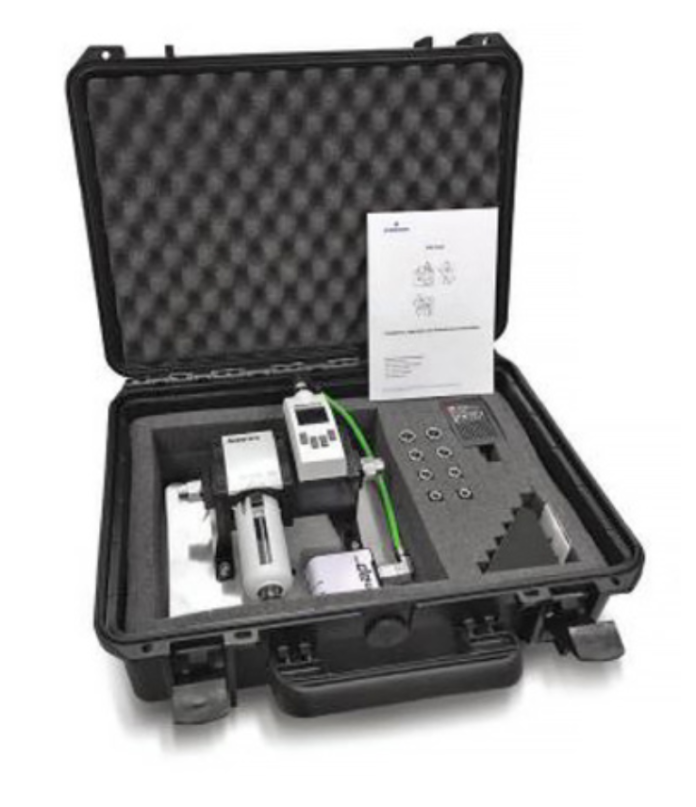
Uwzględnienie danych o przepływie, ciśnieniu i temperaturze
Niezależnie od tego, czy jest to podyktowane celami zrównoważonego rozwoju czy normami środowiskowymi, producenci chcą zmniejszyć zużycie energii i emisję gazów cieplarnianych. Inteligentne układy pneumatyczne sprawiają, że modernizacja układów sprężonego powietrza jest doskonałą okazją do zaoszczędzenia znacznej ilości energii i zmniejszenia ogólnej emisji. W przeszłości producenci nie mieli jasnego i prostego sposobu analizowania zużycia powietrza przez maszyny. Obecnie coraz więcej producentów widzi korzyści płynące z zastosowania inteligentnych układów pneumatycznych do zbierania danych o przepływie, ciśnieniu i temperaturze oraz służących do lepszego zrozumienia zużycia energii przez urządzenia. Ta cyfrowa transformacja maszyn może być skalowana dla operacji pneumatycznych praktycznie każdej wielkości. Operatorzy przechwytują i przetwarzają dane z układów pneumatycznych i innych elementów maszyn, aby uzyskać użyteczne dane na temat zużycia energii. Przekształcanie surowych danych z inteligentnego systemu pneumatycznego w coś, co można wykorzystać, jest kluczem do obniżenia kosztów energii, ponadto ogranicza przestoje, umożliwia skrócenie czasu cyklu i zwiększa ogólną wydajność.
Ilość energii zmarnowanej w układach pneumatycznych może być oszałamiająca. Zakłady produkcyjne tracą zwykle 30% sprężonego powietrza tylko z powodu nieszczelności. Zmarnowana energia prowadzi do przestojów maszyn i oczywiście do wzrostu kosztów energii. Sprężone powietrze jest wykorzystywane w zakładach przemysłowych do obsługi maszyn i procesów, dlatego ma ono zasadnicze znaczenie dla obniżenia kosztów energii w skali roku. Poprawa przepływu sprężonego powietrza przez maszyny w zakładzie, nawet tylko o kilka punktów procentowych, może oznaczać dziesiątki tysięcy złotych zaoszczędzonych na kosztach energii każdego miesiąca, w zależności od wielkości i charakteru sprzętu. Może to przekładać się na setki tysięcy złotych zaoszczędzonych na emisji dwutlenku węgla (CO2). Stosując inteligentne rozwiązania pneumatyczne, takie jak oprogramowanie monitorujące i powiadamiające do wykrywania nieszczelności, producenci mogą często zmniejszyć wydatki na energię sprężonego powietrza o 10–20% i zredukować emisję CO2 o 10%.
Dla wielu producentów taka transformacja pozostaje jednak raczej celem niż rzeczywistością. Choć dostrzegają korzyści, ponad 70% producentów nie ma planu wdrożenia analityki danych i jasnego planu osiągnięcia sukcesu. Przemysłowy Internet Rzeczy (IIoT) i inne technologie wspomagające są uważane za zbyt skomplikowane, kosztowne i czasochłonne do wdrożenia, choć wcale nie musi tak być. Producenci mogą zainwestować w inteligentne rozwiązania pneumatyczne typu plug-and-play, które ograniczają czas i koszty instalacji do minimum. Producenci mogą zrobić pierwszy krok w kierunku transformacji cyfrowej i zobaczyć, jak inteligentne układy pneumatyczne oszczędzają energię w obszarach, w których występują przecieki i straty. Zakłady mogą zwiększyć oszczędność energii sprężonego powietrza dzięki transformacji cyfrowej na dwa sposoby.
Wykrywaj wycieki sprężonego powietrza
Najbardziej oczywistym sposobem utraty energii w systemach pneumatycznych są wycieki. Nieszczelności powodują, że przeciętny zakład produkcyjny traci rocznie około 35% sprężonego powietrza. Gdy elementy układu pneumatycznego ulegają zużyciu, może dojść do nieszczelności, które z czasem będą się powiększać. Im większa nieszczelność, tym większe straty energii. Skutkuje to marnowaniem energii, większym śladem węglowym i wyższymi kosztami operacyjnymi. Niektórzy operatorzy mogą stracić ponad 50 000 dolarów rocznie na jednej maszynie! Oprócz strat energii, nieszczelność sprężonego powietrza może powodować wahania ciśnienia w układzie maszyn, co wpływa na wydajność urządzeń, a nawet na produkcję. W rezultacie maszyna może być zmuszona do dłuższej pracy, aby to skompensować. Te niepotrzebne cykle i wydłużony czas pracy mogą podnieść koszty energii, skrócić żywotność sprzętu i zwiększyć nakłady na konserwację.
Aby wykryć i zlokalizować nieszczelności sprężonego powietrza, firmy sprowadzają techników wyposażonych w urządzenia ultradźwiękowe. Nieszczelności mogą się jednak często pojawiać, utrzymywać i postępować w czasie pomiędzy tymi okresowymi wizytami. Natomiast inteligentne układy pneumatyczne stale monitorują przepływ powietrza. Niektóre czujniki mogą zbierać i dostarczać w czasie rzeczywistym informacje o przepływie, a także rejestrować dane o ciśnieniu i temperaturze w linii zasilającej, umożliwiając zaawansowaną diagnostykę parametrów pracy. Rozwiązania te można łatwo zamontować w istniejących maszynach za pomocą bramek brzegowych. Całodobowy monitoring oprogramowania może wykrywać wycieki w czasie zbliżonym do rzeczywistego. Oprogramowanie identyfikuje daną maszynę i wysyła powiadomienia bezpośrednio do pracowników obsługi technicznej, aby mogli oni przeprowadzić dalsze dochodzenie. Dzięki wykrywaniu nieszczelności w czasie zbliżonym do rzeczywistego, inteligentna pneumatyka może obniżyć zużycie energii sprężonego powietrza o 10–20% i zmniejszyć emisję CO2 w zakładzie o 10%. Wcześniejsze reagowanie na wycieki sprężonego powietrza skraca również planowany (czas poświęcony na testowanie wycieków powietrza w każdej maszynie) i nieplanowany czas przestoju oraz poprawia ogólną efektywność sprzętu (OEE).

Optymalizuj zużycie
Niektórzy producenci mogą nie widzieć zależności między ciśnieniem powietrza a przepływem powietrza. Oznacza to, że mogą nie znać optymalnego punktu poboru sprężonego powietrza dla swojego procesu produkcyjnego. Ciśnienie powietrza w maszynach przemysłowych może być wyższe niż jest to konieczne. Gdy urządzenia zużywają więcej sprężonego powietrza niż to konieczne, zużywają więcej energii, co podnosi koszty energii i zwiększa emisję CO2. Inteligentne czujniki oraz brzegowe urządzenie obliczeniowe mogą zbierać dane o ciśnieniu i przepływie powietrza. Analizując dane analityczne systemu pneumatycznego, zakłady mogą uzyskać dokładne zależności pomiędzy ciśnieniem i przepływem powietrza. Obniżając ogólne ciśnienie w układzie pneumatycznym, można zmniejszyć przepływ powietrza do pewnego punktu przy zachowaniu tego samego czasu cyklu. Znalezienie optymalnego stosunku pomiędzy ciśnieniem a przepływem może prowadzić do zmniejszenia zużycia sprężonego powietrza i kosztów energii o 10–20%, a także do zmniejszenia emisji CO2 o 10%, bez wpływu na produkcję. Dzięki temu producenci mogą utrzymać dotychczasowe czasy cyklu produkcyjnego, ale przy niższym zużyciu energii, kosztach i emisji CO2.

Dane w czasie rzeczywistym, oszczędności
Wykorzystując inteligentną pneumatykę do wykrywania nieszczelności i monitorowania zużycia powietrza, producenci przemysłowi mogą zaoszczędzić znaczną ilość energii. Współpracę z partnerem w zakresie automatyzacji, producent może rozpocząć od obszaru/obszarów, które mają największy sens dla ich sytuacji, budżetu i celów.
Na przykład, globalny producent obsługujący przemysł motoryzacyjny podjął niedawno inicjatywę wdrożenia transformacji cyfrowej, koncentrując się na stratach energii spowodowanych wyciekami sprężonego powietrza i zużyciem powietrza. Firma chciała zmniejszyć zużycie energii poprzez zastosowanie narzędzia do zarządzania energią z obsługą IIoT na istniejącej linii produkcyjnej. Nawiązano współpracę z firmą Emerson, wiodącym dostawcą rozwiązań automatyki, w celu monitorowania i pomiaru ilości energii zużywanej przez linię. Podobnie jak w przypadku większości zastosowań tego typu, linia produkcyjna zawierała różne starsze urządzenia, które pochodziły od różnych dostawców. Każda skrzynka licznika składała się z zasilacza, łącznika magistrali Ethernet, miernika mocy (jeden na obwód) oraz IO-Link, który zawierał osiem dostępnych portów dla czujników. Przekładniki prądowe były umieszczone wewnątrz lub na zewnątrz skrzynki licznika, a wszystkie te moduły musiały być zainstalowane w pozycji pionowej, aby umożliwić cyrkulację powietrza. Złożoność tej konfiguracji zwiększała ograniczona liczba punktów dostępu do sieci Ethernet, z którymi można było pracować, a jej rozbudowa wymagałaby znacznych inwestycji.
Aby sprostać potrzebom tej złożonej konfiguracji, firma Emerson poleciła czujnik AVENTICSTM serii AF2 – łatwy w użyciu czujnik przepływu powietrza, który mierzy przepływ, ciśnienie i temperaturę oraz monitoruje zużycie powietrza w systemach pneumatycznych. Czujnik AF2 idealnie nadaje się do kolekcji starszych maszyn z kilku powodów. Po pierwsze, ten kompaktowy czujnik jest łatwy w montażu i może być zainstalowany na istniejących maszynach i systemach pneumatycznych. Po drugie, AF2 ma opcje komunikacji IO-Link i Ethernet. Czujnik jest łatwy do zintegrowania z jednostkami przygotowania powietrza i daje producentom możliwość działania jako wersja samodzielna. Dzięki kolorowemu, obrotowemu wyświetlaczowi LED, który zapewnia wyraźną informację zwrotną, AF2 wysyła powiadomienia do użytkowników, gdy wykryje nieszczelność, dzięki czemu mogą oni podjąć działania. To proste urządzenie z obsługą technologii IIoT pozwoliło firmie na oszczędność energii przy jednoczesnym ograniczeniu czasu i kosztów instalacji do minimum.
Po wybraniu czujnika firma Emerson pomogła przedsiębiorstwu monitorować i mierzyć ilość energii zużywanej przez linię, podłączając tymczasowo inteligentny analizator pneumatyczny AVENTICS (SPA) do jednej z maszyn. Urządzenie SPA, które zapewnia błyskawiczną analizę systemu pneumatycznego, rejestrowało, analizowało i wizualizowało zużycie powietrza przez linię podczas procesu produkcyjnego. Zespół był w stanie odczytać zużycie powietrza w czasie rzeczywistym, które SPA wyświetla w litrach na minutę (l/min), wraz z wartościami średnimi i maksymalnymi, aby szybko zidentyfikować trendy i anomalie. Dane zebrane ze SPA pomogły firmie podjąć decyzję, czy warto zainwestować w urządzenie PACSystems RXi2-BP Edge Computing Device firmy Emerson, które interpretuje i wyświetla wszystkie przychodzące dane z czujników AF2. Wykorzystując algorytmy matematyczne, przekłada dane na proste, przyjazne dla użytkownika informacje. Informacje te są rejestrowane i wyświetlane na bieżąco na tablicy rozdzielczej opartej na sieci Web i dają użytkownikom lepszy wgląd w zużytą energię bez dodatkowego oprogramowania.
Dane SPA wykazały, że urządzenie PACSystems RXi2-BP Edge Computing Device rzeczywiście pomoże firmie oszczędzać energię i związane z nią koszty, dlatego zdecydowano się na inwestycję. Łącznie firma Emerson dostarczyła około 180 czujników przepływu AF2, aby zaspokoić potrzeby linii produkcyjnej, a także urządzenie PACSystems RXi2-BP Edge Computing Device. To energooszczędne rozwiązanie monitoruje zużycie powietrza pneumatycznego oraz generuje i interpretuje dane maszynowe, dając producentowi z branży motoryzacyjnej cenne spostrzeżenia i pełniejszy obraz tego, co dzieje się w zakładzie. W rezultacie firma zlokalizowała obszary wymagające poprawy, w tym zmniejszenie szczytowego zużycia energii, optymalizację kosztów konserwacji i unikanie przestojów; planuje także dalszą optymalizację swoich maszyn w celu zmniejszenia zużycia energii.

W kierunku transformacji
We wszystkich gałęziach przemysłu zarządzanie energią jest priorytetem dla zakładów przemysłowych. W związku z rosnącymi obawami dotyczącymi zużycia energii i emisji dwutlenku węgla, monitorowanie sprężonego powietrza w układach pneumatycznych umożliwia redukcję emisji i obniżenie kosztów energii. Gdy maszyny nie są monitorowane, nie jest też monitorowane ich zużycie energii. Nieszczelności i straty mogą swobodnie rosnąć, problemy, które mogłyby być rozwiązane na wczesnym etapie, przekształcają się w problemy jakościowe na późnym etapie, a znaczne ilości energii są marnowane.
Droga do transformacji cyfrowej, która uwalnia oszczędności energii sprężonego powietrza, dla każdego zakładu wygląda jednak inaczej. Jak każda transformacja, transformacja cyfrowa jest procesem, który rozwija się w swoim tempie i zależy od warunków panujących w danym zakładzie. Aby z powodzeniem rozpocząć oszczędzanie energii dzięki transformacji cyfrowej, ważna jest współpraca z ekspertem w dziedzinie automatyki, który zna inteligentną pneumatykę i unikalne cechy aplikacji wykorzystujących energię płynów. Mając dostęp do odpowiedniego eksperta, wiedzy i narzędzi, można zrealizować swoje cele w zakresie oszczędności energii sprężonego powietrza i transformacji cyfrowej.
Dieter Michalkowski jest menedżerem ds. klientów globalnych w dziale kontroli płynów i pneumatyki w firmie Emerson. Chris Noble jest konsultantem ds. rozwoju biznesu, żywności i napojów, opakowań oraz IIoT w firmie Emerson.