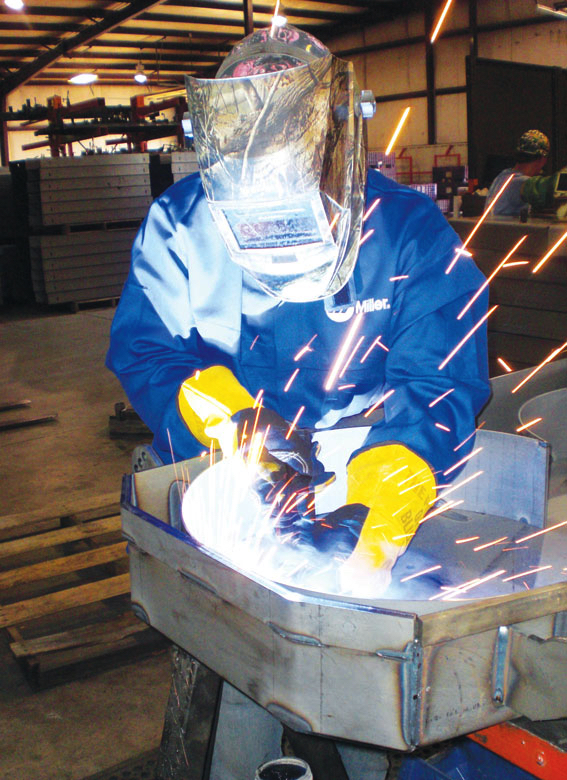
Zastosowanie spoiwa w procesie spawania, czyli wprowadzenie do złącza dodatkowego materiału, minimalizuje ryzyko pęknięć czy innych wad połączeń spawanych, których usuwanie może być czasochłonne i kosztowne. Dlatego niezwykle ważne jest użycie takiego spoiwa, które ma odpowiednie właściwości mechaniczne i chemiczne, a dzięki temu zapewni wymaganą wytrzymałość spoiny w warunkach jej pracy.
Istnieje kilka czynników, które należy przeanalizować przy doborze spoiwa spawalniczego. Są to: rodzaj spawanego materiału, pozycja spawania, wymagania określone przepisami, wymagania określone normami, wymagania projektowe, rodzaj gazu osłonowego, obróbka cieplna po spawaniu oraz sprzęt spawalniczy.
Spawany materiał bazowy
Jeżeli obydwa materiały – spoiwo i metal bazowy – pasują do siebie pod względem chemicznym, to ich właściwości mechaniczne (takie jak wytrzymałość na rozciąganie i granica plastyczności) także będą odpowiednio dobrane. Spawacze mogą być pewni, że ich stopiwo będzie miało taką samą wytrzymałość i właściwości jak materiał bazowy.
Jeżeli łączone materiały nie mają takiej samej wytrzymałości, należy rozważyć inne czynniki. Spawacze powinni przyjąć zasadę doboru wytrzymałości metalu spoiwa do tego z dwóch materiałów bazowych, który ma mniejszą wytrzymałość. Podczas procesu spawania część mocniejszego materiału bazowego rozpływa się w jeziorku spawalniczym i jest to wystarczające do wzmocnienia stopiwa.
Większość materiałów bazowych można łatwo zidentyfikować na podstawie ich wyglądu i reakcji na magnesy, łamanie, zarysowanie, a także płomień lub iskry. Spawacze zwykle mają wiedzę na temat materiałów bazowych, z którymi pracują. W niektórych przypadkach, zwykle podczas napraw lub poprawek spawania, może się okazać konieczne pobranie próbki materiału w celu wykonania analizy laboratoryjnej.
Pozycja spawania
Zawsze, gdy jest to możliwe, spawacz powinien obracać obrabiany element tak, aby mógł go spawać w pozycji podolnej (stopiony metal utrzymywany jest w jeziorku spawalniczym siłą grawitacji). Spawanie w pozycji podolnej jest zawsze najbardziej ekonomiczną metodą. W następnej kolejności należy wymienić pozycje przymusowe: naścienną, pionową i pułapową (okapową).
Jeżeli jednak spawacz musi pracować z dużą konstrukcją spawaną, której nie może obracać, musi wykonywać spawanie w różnych pozycjach. Spawanie w pozycjach przymusowych może być szczególnym wyzwaniem, jeżeli dostępny jest tylko drut spawalniczy o jednej średnicy. Na przykład spawanie w pozycji pionowej przy użyciu drutu o średnicy 3/32″ (2,4 mm) może być ekstremalnie trudne lub nawet niemożliwe. Lepszym wyborem będzie użycie drutu o średnicy 0,0451/16″ (0,111,59 mm), ale wymaga to dodatkowego podajnika drutu oraz dodatkowego źródła zasilania. Ponadto niezbędna jest zmiana magazynków podajnika oraz potencjalnie uchwytu spawalniczego.
Zakłady powinny zdawać sobie sprawę, że zmiany pozycji spawalniczych mogą spowolnić proces spawania i być zagrożeniem dla wydajności pracy. Dlatego należy dobierać najbardziej uniwersalny materiał i średnicę drutu spawalniczego.
Wymagania określone przepisami
Specyfikacja techniczna wykonania prac często narzuca klasę drutu spawalniczego, który ma być użyty. Jeżeli tak nie jest, spawacze powinni dokładnie rozważyć wymagane parametry techniczne spoin i spodziewane warunki pracy spawanych elementów.
Na przykład, jeśli spawacz używa drutu ze stali miękkiej do spawania elementów pracujących w trudnych warunkach, prawdopodobne jest, że wykonane spoiny będą rdzewieć, korodować i tracić wytrzymałość szybciej niż materiał bazowy. Takie spawanie może prowadzić do pękania spoin, szczególnie gdy produkt końcowy ma kluczowe znaczenie, np. jest nim zbiornik ciśnieniowy pracujący w wysokich temperaturach lub most narażony na trudne warunki atmosferyczne.
Każde spoiwo używane przez spawaczy musi spełniać wymagania techniczne dla warunków pracy produktu końcowego, tak aby stopiwo miało taką samą trwałość jak materiał bazowy.
Wymagania projektowe
Poza stosowaniem się do przepisów (tam, gdzie jest to wymagane) ważne jest, aby wybrać takie spoiwo, które spełnia lub przewyższa wymagania dla spoiny określone przez inżyniera projektanta. Na przykład przy spawaniu cienkiego materiału ważne jest, aby parametry łuku elektrycznego były odpowiednie – użycie drutu spawalniczego, który pozwala na głęboką penetrację materiału, może spowodować przepalenie tego materiału przez spawacza. Z drugiej jednak strony, jeśli spawana część jest gruba i ma być wykonana spoina typu V, to użycie metalu spoiwa mającego lepszą charakterystykę penetracji pozwoli na lepsze związanie metalu u podstawy i po bokach spoiny.
Rodzaj gazu osłonowego
Ważne jest, aby spoiwo i gaz osłonowy były wzajemnie dopasowane do danego rodzaju spawania.
Różne gazy osłonowe mają różny wpływ na metal spoiwa. Na przykład dodanie argonu do dwutlenku węgla (CO2) pozwala spawaczowi na przeniesienie własności chemicznych tego metalu do stopiwa w większym stopniu. Ta mieszanina daje stałą dobrą jakość spoiny, pozwala na dobrą kontrolę nad jeziorkiem spawalniczym oraz generuje mniej odprysków.
Odwrotnie – użycie CO2 (gazu utleniającego) powoduje przepalenie niektórych elementów spoiwa metalicznego. Zaletą spawania w atmosferze samego CO2 jest głęboka penetracja spoiny, co jest pożądane przy spawaniu grubszych materiałów. Ma ono jednak tendencję do przenoszenia większych kropli stopionego metalu do spoiny i może tworzyć więcej odprysków niż w przypadku zastosowania mieszaniny gazów osłonowych w postaci kombinacji argonu i dwutlenku węgla.
Istnieją druty spawalnicze, które mogą być użyte do spawania zarówno w osłonie samego CO2, jak i mieszaniny argonu i dwutlenku węgla. Firmy powinny przy doborze spoiwa rozważyć dostępne źródła gazów osłonowych oraz wymagane charakterystyki spawania, a także upewnić się, że wybrane spoiwo jest dopasowane do wybranego gazu osłonowego.
Obróbka cieplna po spawaniu
Istnieją pewne gatunki stali oraz wartości grubości materiałów, przy których musi być zastosowane wstępne podgrzewanie materiału przed spawaniem do określonej temperatury. Czynność ta powoduje, że spawana część stygnie wolniej, co pozwala na uniknięcie problemów z kurczeniem się i pękaniem spoiny. Podobnie obróbka cieplna po spawaniu (Post-Weld Heat Treatment – PWHT) stosowana jest do zmniejszania naprężeń mechanicznych i powolnego oddawania ciepła wprowadzonego w procesie spawania, co pozwala na to, aby spoina i materiały bazowe odzyskały swoje pożądane właściwości.
Przy spawaniu materiałów wymagających obróbki PWHT ważne jest, aby wybrać takie spoiwo, które daje spoiny odpowiednio reagujące na podgrzewanie.
Sprzęt spawalniczy
Typ i wielkość sprzętu używanego do spawania mają wpływ na to, jakie spoiwo będzie najlepsze do wykonania danego zadania. Szczególnie ważna jest maksymalna wartość natężenia prądu spawarki (tzw. amperaż) – musi być wystarczająca dla średnicy drutu spawalniczego użytego do realizacji tego zadania. Jeśli wartość natężenia prądu spawarki jest zbyt niska, trzeba albo zmienić średnicę drutu, co wydłuży proces spawania, albo użyć spawarki o większej mocy.
Ważne jest także, aby spawarka miała możliwość regulacji/ustawienia odpowiedniej wartości natężenia prądu dla danego spoiwa. Spawanie przy niewłaściwej wartości prądu może prowadzić do powstawania odprysków i spoin o złej jakości.
Wyznaczenie pożądanej charakterystyki spawania jest równie ważne. Metale spoiw, które wymagają odwrotnej polaryzacji zasilania (biegunowości) elektrody spawalniczej (Electrode Positive – EP – elektroda połączona z biegunem dodatnim), dają bardzo dużą penetrację spoiny, podczas gdy przy typowej polaryzacji (Electrode Negative – EN – elektroda połączona z biegunem ujemnym) występuje znacznie mniejsza penetracja.
Chociaż wpływ różnych elementów na dobór spoiwa może być dość złożony, a elementy te mogą wzajemnie wpływać na siebie, to zapoznanie się z ich właściwościami ogólnymi może także pomóc spawaczom w określeniu, które spoiwo będzie idealne do danego zadania.
Na przykład dodatek węgla do stali zwiększa jej twardość, wytrzymałość na rozciąganie i odporność na zużycie, ale jednocześnie zmniejsza plastyczność, udarność i obrabialność. Natomiast dodatek niklu zwiększa twardość, wytrzymałość na rozciąganie, udarność i plastyczność, ale zmniejsza podatność na obróbkę maszynową. Podobnie istnieją różne inne elementy stopów, które mają różne własności: odtlenianie, rozdrobnienie ziaren austenitu lub poprawę plastyczności. Dla spawaczy ważne jest, aby przy doborze metalu spoiw brali pod uwagę wymagane właściwości spoin, które mają wykonać.
Autor: Bruce Morrett jest menedżerem produktu w firmie Hobart Brothers.