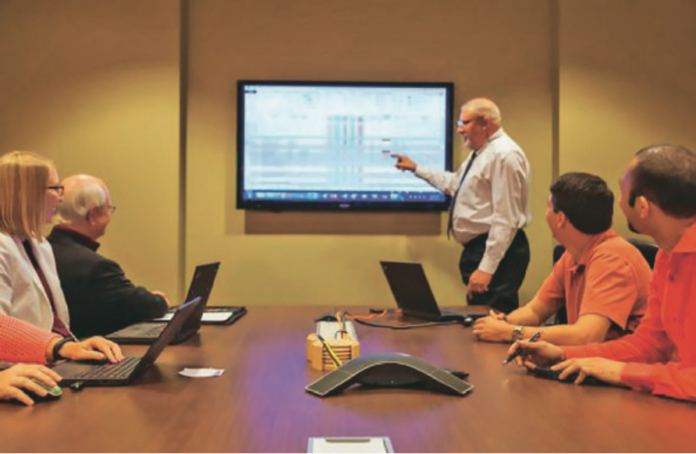
Efektywnie wdrożone praktyki planowania, zgodne z zasadami Lean Management, mogą pomóc firmom przemysłowym w uruchomieniu produkcji w nowo wybudowanych zakładach w nieprzekraczalnym terminie określonym w harmonogramie oraz nadrobieniu opóźnień spowodowanych pandemią.
W wyniku pandemii COVID-19 wiele firm produkcyjnych zawiesiło swoją działalność w zakresie projektów i budowy nowych zakładów. Wiele z tych projektów miało kluczowe znaczenie dla realizacji celów związanych z produkcją oraz znajdowało się już w zaawansowanym stadium prac budowlanych zanim wybuchła pandemia, co gwałtownie wpłynęło na całą gospodarkę światową. Obecnie, gdy przemysł produkcyjny zaczyna dźwigać się po zapaści spowodowanej koronawirusem, właściciele firm poszukują kreatywnych rozwiązań wykonywania projektów technicznych i prac budowlanych, aby nadrobić stracony czas.
Skuteczne wdrażanie praktyk Lean Management w fazie planowania początkowego może pomóc w identyfikacji strategii projektowania technicznego, dostaw materiałów i realizacji budowy, aby nowe zakłady przemysłowe szybciej startowały z produkcją. Poniżej podano kilka kluczowych rozważań oraz informacji praktycznych na ten temat.
Opracowanie efektywnego planu działań związanych z projektem
Z historycznego punktu widzenia liderzy przemysłu produkcyjnego preferowali tradycyjny model D-B-B (design/bid/build; projekt/przetarg/budowa), który stosuje podejście liniowe krok po kroku do realizacji projektu oraz wykorzystuje metodę CPM (critical path method; metoda ścieżki krytycznej) do opracowania harmonogramu prac nad projektem. Co prawda model ten zwykle daje firmie najlepszą kontrolę oraz najmniejsze ryzyko, jednak liniowa natura czyni go najdłuższym pod względem czasu realizacji projektu, określonym w harmonogramie.
Zgodnie z koncepcjami Lean należy stosować strategię planowania typu pull (pull – ssanie, przyciąganie). Polega to na identyfikacji działań, które mogą być wykonane z góry lub zrealizowanie jednocześnie i których celem jest uzyskanie pożądanego stanu końcowego. Strategia pull planning jest procesem pracy zespołowej, który wymaga uczestnictwa wszystkich osób zaangażowanych w projekt. W wyniku tworzone jest zaufanie i consensus na temat elementów, które są kluczowe dla skutecznej realizacji projektu. Prawidłowo opracowany plan typu pull będzie czynnikiem napędowym opracowywania efektywnej i wykonalnej metody realizacji projektu.
Skracanie harmonogramu a zaopatrzenie w materiały do realizacji projektu
Sesja pull planning może zidentyfikować okazje do uzyskania znacznych korzyści w postaci skrócenia harmonogramu. Jednak pełne wykorzystanie tych możliwości może wymagać od właścicieli projektu nieco mniej tradycyjnego podejścia do procesu zaopatrzenia w materiały potrzebne do realizacji projektu.
Przeanalizujmy kontrakt typu open-book (otwarta księga). Generalny wykonawca kontraktu jest transparentny w stosunku do zespołu strony zamawiającej w zakresie otrzymanych ofert od kluczowych branż lub na kluczowe komponenty projektu. Pozwala to zamawiającemu utrzymywać konkurencyjne oferty przetargowe oraz jednocześnie być otwartym na potencjalne alternatywy skracania harmonogramu. Ponieważ model realizacji zamówień typu open-book jest stosunkowo nową koncepcją, rozważmy udostępnienie przykładów poprzednich projektów lub przypadków praktycznych (case study) personelowi działu zaopatrzenia, aby uzyskał informacje na temat tego, jak może on pozostać zaangażowany i utrzymać kontrolę nad procesami realizacji zamówień na materiały.
Ponowne przeanalizowanie strategii korporacyjnych
Wielu właścicieli projektów, reprezentujących firmy produkcyjne oraz instytucje, stworzyło swoje sieci dostawców oraz podpisało długoletnie kontrakty na zakup surowców i innych materiałów, które są potrzebne do działania ich obiektów oraz konserwacji sprzętu. Jest to przyczyną tego, że np. oprawy oświetleniowe oraz membrany dachowe są takie same we wszystkich zakładach danej firmy, znajdujących się w różnych lokalizacjach. Można usprawnić zarządzanie zapasami części zamiennych i materiałów eksploatacyjnych dla działów utrzymania ruchu, nabywać sprzęt i części do niego w dużych ilościach, redukować koszty jednostkowe oraz upraszczać ogólne programy utrzymania ruchu.
Jednak tego typu ograniczenia mogą stwarzać problemy w zakresie przyśpieszania harmonogramów realizacji projektów. Jeśli szybkość wprowadzenia nowego produktu na rynek będzie kluczowym biznesowym czynnikiem napędowym, to właściciele projektów będą zachęceni do bycia otwartymi na wyjście poza standardy oraz rozważanie alternatywnych produktów i sprzętu, które będą nadal spełniać ich wymagania, ale będą za to dostępne w krótszym czasie.
Na przykład wskutek pandemii dostarczenie standardowej rozdzielnicy elektrycznej dla zakładu produkcyjnego może zabrać aż 26 tygodni lub więcej, podczas gdy rozdzielnica innej firmy, ale o podobnych parametrach, może być dostarczona w czasie nawet dwa razy krótszym. Ponadto zakład produkcyjny może wymagać ponad 400 opraw oświetleniowych. Złożenie zamówienia tej wielkości może sprawić, że producent opraw będzie potrzebował całych tygodni na wyprodukowanie towaru i dostarczenie go do klienta.
Natomiast rozdzielając takie zamówienia na kilku dostawców lub rozważając możliwości zainstalowania alternatywnych typów opraw oświetleniowych spełniających wymagania specyfikacji technicznej, będących tylko innym modelem, może przynieść korzyści w postaci otrzymania i zainstalowania opraw, zanim to większe zamówienie zostanie wysłane. Może to mieć zastosowanie także w przypadku systemów ogrzewania, wentylacji i klimatyzacji (HVAC) oraz innych komponentów instalacji budynkowych. Ważne jest, aby zauważyć, że do przeanalizowania rozwiązań alternatywnych wymagane jest uzyskanie dokładnych recenzji produktów: od firmy instalacyjnej, inżynierów – specjalistów z danej branży oraz właściciela projektu. Systemy elektryczne i mechaniczne wymagają stałej konserwacji, tak więc wszystkie strony kontraktu muszą ocenić zarówno ryzyka, jak i korzyści dla cyklu życia zakładu, wynikające z rozwiązań alternatywnych.
Inny przykład. Budowana jest od podstaw nowa fabryka samochodów. Prace budowlane wymagają użycia dużych dźwigów, które potrzebują licznych dużych kolumn wsporczych. Tradycyjne kolumny są wykonane ze stali. Jednak w czasach pandemii z powodu braków stali na rynku producenci kolumn nie byli w stanie sprostać wymaganiom szybkiej realizacji zamówień.
Podczas narady w sprawie planowania budowy fabryki zespół projektowy zaproponował użycie prefabrykowanych kolumn betonowych zamiast stalowych. Chociaż była to niezgodność ze standardem klienta, propozycja została zaakceptowana. Betonowe kolumny prefabrykowane zostały zainstalowane na budowie fabryki 8 tygodni wcześniej niż dostarczono by kolumny stalowe.
Rozpoczęcie procesu budowy
Efektywna sesja planowania typu pull może także znaleźć okazje do podziału projektów na mniejsze zakresy prac. Te pakiety „pull ahead” („prowadzące” w projekcie) mogą umożliwić stronie zamawiającej rozpoczęcie prac budowlanych przed ukończeniem wszystkich projektów technicznych, co pozwoli na znaczne skrócenie ogólnego harmonogramu realizacji projektu.
Weźmy wspomnianą wyżej nową fabrykę samochodów. Dzięki wczesnemu zakończeniu planu organizacji i zagospodarowania placu budowy przewidziane w projekcie prace budowlane mogą się rozpocząć, zanim zostaną zaprojektowane inne elementy budynku. Fundamenty oraz konstrukcje stalowe mogą być wykonane osobno, co pozwoli hutom na realizację zamówień przed zakończeniem projektów technicznych instalacji elektrycznych i mechanicznych.
Dostawa dużych elementów instalacji mechanicznych i elektrycznych dla budynku może wymagać czasu – nawet 6 miesięcy. Tak więc opracowanie specyfikacji technicznych i zamówienie podstacji energetycznych, rozdzielnic elektrycznych, chillerów, central wentylacyjnych (AHU) itd. umieszcza te elementy na czele kolejki materiałów do zamówienia u producentów. Na koniec dopasowanie do siebie systemów – architektonicznego, mechanicznego i elektrycznego, może być zaprojektowane już po rozpoczęciu prac budowlanych, co da zamawiającemu dodatkowy czas na sprecyzowanie swojego własnego projektu wyposażenia fabryki w sprzęt oraz wynikającego z tego zapotrzebowania na media, które należy zgłosić do ich dostawców, np. zakładu energetycznego. Dodatkowy czas zostanie też uzyskany na opracowanie szczegółów technicznych dla linii produkcyjnych przyszłej fabryki, co nie wpłynie na ogólny harmonogram budowy.
Tak więc rozdzielenie projektu na mniejsze części, zamiast pozostawienie w postaci obszernej i kompleksowej całości, pozwala właścicielowi projektu na znaczne skrócenie harmonogramów realizacji.
Znaczenie zaangażowania właściciela w projekt
Każdy projekt w miarę realizacji będzie stwarzał problemy. Jednak sposób podejścia przez zespół projektowy do tych problemów może mieć wielki wpływ na harmonogram projektu. Przywództwo właściciela projektu nadaje ton od samego początku i powinno ułatwić współpracę oraz stworzyć środowisko zaufania i respektowania każdego z uczestników. Zapewni to, że napotykane problemy nie staną się ćwiczeniami we wskazywaniu palcem czy pogrążaniem się we wzajemne obwinianie.
Będąc otwartym na innowacyjne idee oraz zachęcając wszystkich członków zespołu do brania udziału w dyskusjach nad rozwiązywaniem problemów, właściciel projektu ustanawia efektywną kulturę projektu. Poza otwartością na ludzi, dobry właściciel projektu (lub jego przedstawiciel) powinien posiadać zdolność do aktywnego słuchania, efektywnego komunikowania oraz, co najważniejsze, być upoważnionym do podejmowania decyzji i czuć się w tym swobodnie.
Przyśpieszenie realizacji projektów po zakończeniu pandemii COVID-19
Wiele organizacji w przemyśle produkcyjnym stosuje ciągle tę samą metodę realizacji projektu, ponieważ „zawsze się tak robiło”. W wyniku tego sprawą zasadniczą dla konsultantów oraz wykonawców z branż usług specjalistycznych jest to, aby wyjaśniali personelowi kierowniczemu firm produkcyjnych, że takie tradycyjne podejście – „projekt techniczny/przetarg/budowa” – zwykle wydłuża czas realizacji całego projektu oraz że metoda dostarczania materiałów alternatywnych może być konieczna, aby zmieścić się w ostatecznym terminie (deadline) uruchomienia produkcji w nowej fabryce.
W wielu przypadkach opóźnienia projektów wynikające z pandemii stały się katalizatorem dla producentów, którzy zaczęli badać możliwości stosowania rozwiązań alternatywnych. Jeśli są wdrażane efektywnie, praktyki Lean Management mogą pomóc firmom przemysłowym w uruchamianiu produkcji w nowych czy modernizowanych zakładach zgodnie z zaplanowanym terminem ostatecznym oraz nadrabianiu opóźnień spowodowanych pandemią.
Brandon Darroch, certyfikowany specjalista od zarządzania projektami (PMP), jest menedżerem działu południowo-wschodniego oraz starszym konsultantem w firmie SSOE Group. Firma ta realizuje na całym świecie projekty z zakresu architektury, inżynierii oraz zarządzania budową (construction management). Posiada 15 lat doświadczenia w zarządzaniu projektami, zarówno dla wykonawców generalnych, jak i biur projektowych.
Inż. Brian Arend, posiadacz certyfikatu LEED AP (budownictwo ekologiczne), jest menedżerem działu elektroenergetyki oraz starszym konsultantem w SSOE Group. Posiada 17 lat doświadczenia w przemyśle. Pracował w wielu branżach przemysłu produkcyjnego oraz motoryzacyjnego.