Testowanie smarów pomaga w wyznaczeniu ich właściwości smarnych oraz odporności na warunki pracy. W artykule opisano różne typy testów według norm ASTM wykonywanych w zależności od aplikacji danego smaru.
Celem przeprowadzania testów środków smarnych jest wyznaczenie właściwości fizycznych i chemicznych oraz smarnych tych produktów. Niektóre z opisanych w normach testów smarów są wykorzystywane przez ich producentów do kontroli jakości wyrobów. Mogą one obejmować testy penetracji stożkiem według normy ASTM D217 (Penetration) oraz zasadowości według ASTM D128 (Free Alkalinity). Testy właściwości smarnych są wykorzystywane do symulacji lub wskazania, jak dany preparat będzie sprawdzał się w praktyce.
Większość aplikacji ma swoje unikalne wymagania dotyczące właściwości smarnych, tak więc istnieją testy opracowane pod kątem sprawdzenia tych właściwości w różnych aspektach danej aplikacji.
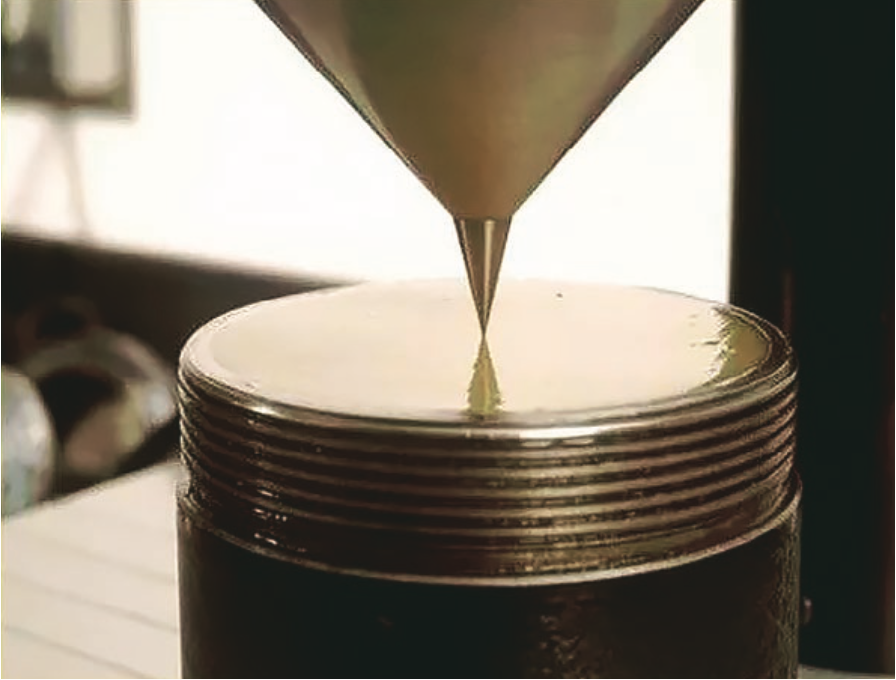
Typy oraz zakresy testów smarów
Dla aplikacji związanych z wymaganą odpornością smaru na ścinanie wykonuje się testy penetracji stożkiem według normy ASTM D217 przy 10 000 lub 100 000 cykli ugniatania oraz testy stabilności metodą wałkowania ASTM D1831 (Roll Stability). Wyniki tych testów pokazują stabilność mechaniczną smaru narażonego na ścinanie.
W przypadkach, w których odporność na wodę odgrywa dużą rolę w zachowaniu właściwości smarnych, przeprowadza się testy odporności smaru na wypłukiwanie wodą z łożyska według ASTM D1264 (Water Washout) oraz przylegania smaru do metalu przy kontakcie z rozpyloną wodą według ASTM D4049 (Water Spray-off). Natomiast wyniki testów stabilności metodą wałkowania w obecności wody według ASTM D8022 (Roll Stability in the Presence of Water) pokazują, jak dany smar funkcjonuje zarówno w kontakcie z wodą, jak i pod wpływem ścinania.
Dla tych aplikacji, w których ważna jest odporność na korozję, wykonuje się testy odporności smarowanych elementów wykonanych z miedzi na korozję według ASTM D4048 (Copper Corrosion), właściwości antykorozyjnych smarów według ASTM D1743 (Corrosion Prevention) oraz właściwości antykorozyjnych smarów w łożyskach kulkowych w dynamicznych warunkach mokrych ASTM D6138 (Dynamic Corrosion Resistance, tzw. test EMCOR), których wyniki dają wgląd we właściwości smaru w praktyce. Dla ekstremalnych warunków pracy przeprowadza się testy właściwości antykorozyjnych smarów w łożyskach stożkowych mających kontakt z syntetyczną wodą morską według ASTM D5969 (Synthetic Sea Water Corrosion Prevention) oraz w łożyskach kulkowych według ASTM D6138, do których można wykorzystać stuprocentową syntetyczną wodę morską lub 0,5 N roztwór chlorku sodu (NaCl).
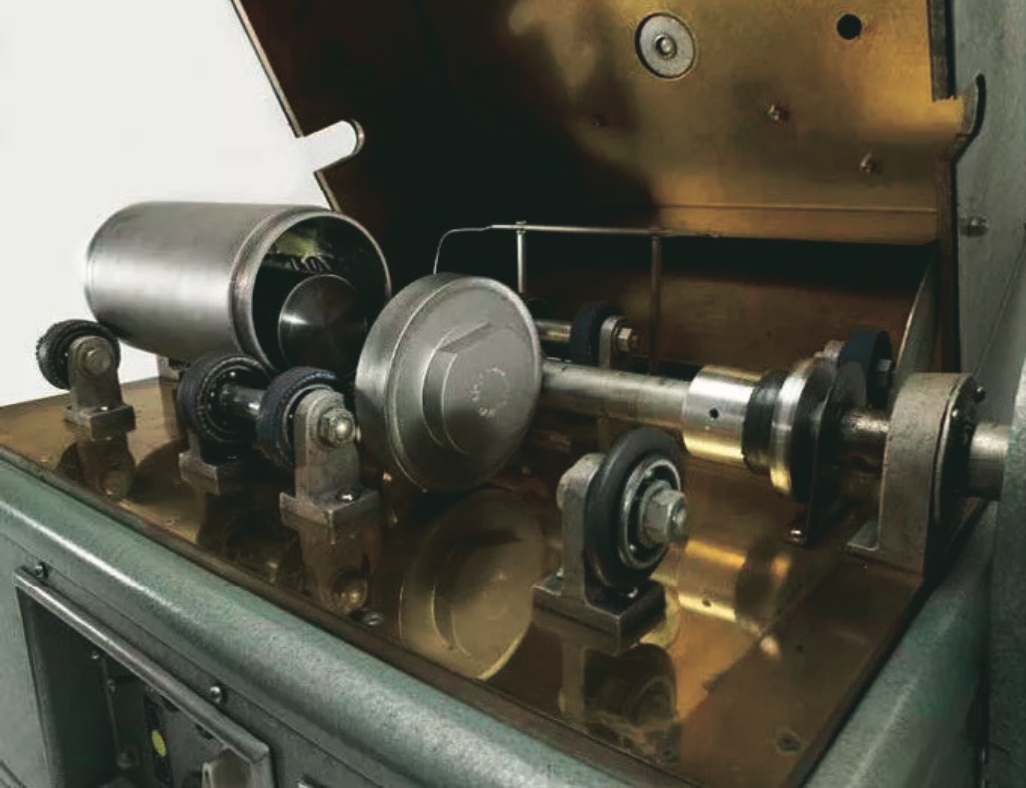
Jeśli smar musi chronić przed zużyciem mechanizmy pracujące przy dużych obciążeniach, to przeprowadza się testy właściwości przeciwzużyciowych według norm ASTM D2266 (Wear Prevention (test 4-kulowy) i właściwości smarów pod wysokim ciśnieniem D2596 Extreme Pressure Properties (test 4-kulowy). Pokazują one właściwości smaru w ciężkich warunkach pracy. Natomiast jeśli mogą wystąpić ekstremalne lub specyficzne warunki pracy, można wykonać testy dodatkowe właściwości smarów poddanych skrajnie wysokim ciśnieniom w układzie wykonującym ruch liniowo-oscylacyjny o wysokiej częstotliwości, do czego wykorzystuje się maszynę testową SRV, według normy ASTM D5706 (Extreme Pressure Properties Using the SRV Test Machine) oraz test odporności na zużycie frettingowe według jednej z następujących norm: ASTM D4170 (Fretting Wear Protection) lub ASTM D7594 (Fretting Wear Resistance Using an SRV Machine).
Jeżeli smar będzie narażony na działanie niskich temperatur, przeprowadza się test momentu obrotowego łożyska kulkowego pracującego w takich warunkach według normy ASTM D1478 (Low-Temperature Ball Bearing Torque Test). Temperatura testowa może być obniżona, aby sprawdzić właściwości smaru w ekstremalnych warunkach. Można dodatkowo wykonać też testy ciśnienia przepływu według normy DIN 51805, które pokażą charakterystykę pompowalności smaru w niskich temperaturach.
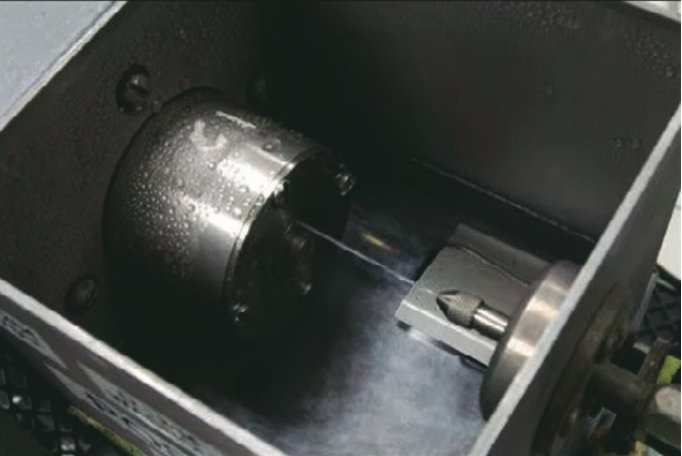
Smary plastyczne – specyfikacje jakościowe według norm i standardów
Podane w normach i standardach specyfikacje jakościowe smarów plastycznych zwykle wymieniają wiele z testów omówionych wyżej. Specyfikacja jakościowa powinna obejmować te testy, które dają producentowi smaru wytyczne do opracowania takiego produktu, który dobrze się sprawdzi w aplikacji. Niepotrzebne testy lub takie, które nie mają wkładu w wymagane właściwości smarne produktu, nie powinny być zawarte w specyfikacji. Specjaliści opracowujący skład chemiczny smaru powinni wykorzystać każdy test podany w specyfikacji jakościowej do stworzenia produktu o wymaganych właściwościach.
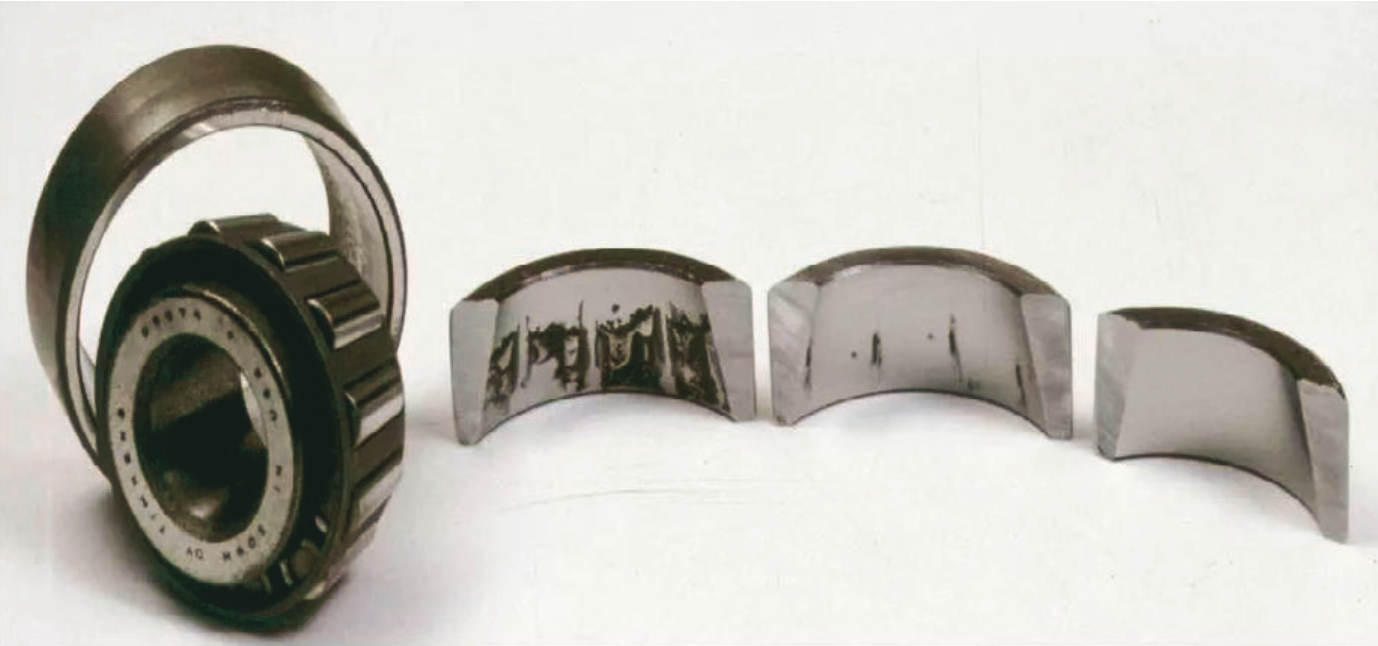
Specyfikacja NLGI smarów uniwersalnych o wysokich parametrach (HPM)
W okresie 18 miesięcy zespół ekspertów od środków smarnych opracował specyfikację smaru uniwersalnego o wysokich parametrach (ang. high-performance multiuse, HPM) amerykańskiego Krajowego Instytutu Środków Smarnych.
Specyfikacja ta wykorzystuje wszystkie testy opisane wyżej do zdefiniowania właściwości smarnych preparatu, który może mieć wiele zastosowań. Celem opracowania tego dokumentu było stworzenie pewnego odniesienia dla użytkowników smarów.
Podstawowa specyfikacja smaru HPM opisuje produkt o dobrych właściwościach smarnych dla wielu aplikacji. Gdy smar narażony jest na ekstremalne warunki pracy, to może być wymagany produkt o wyższych parametrach. Specyfikacja HPM posiada „znaczniki” (tagi), które reprezentują ulepszone właściwości smarne w pewnych obszarach. Smary posiadające jeden z opisanych niżej znaczników muszą spełniać nie tylko podstawowe wymagania specyfikacji HMI, ale także wymagania dodatkowe.
Znacznik WR wskazuje na zwiększoną odporność na wodę (ang. water resistance, w porównaniu do podstawowej specyfikacji HPM). Smary z tagiem WR mają lepsze właściwości smarne według normy ASTM D1264 oraz spełniają wymagania odporności na rozpyloną wodę wg ASTM D4049 i stabilności mechanicznej wg ASTM D8022.
Znacznik CR wskazuje na zwiększoną odporność na korozję. Smary ze znacznikiem CR zachowują dostateczne właściwości smarne i antykorozyjne w obecności rozcieńczonej syntetycznej wody morskiej według ASTM D5969 (Corrosion Prevention in the Presence of Dilute Synthetic Sea Water) oraz dobre właściwości smarne w teście dynamicznego zapobiegania korozji według ASTM D6138 (Dynamic Corrosion Prevention), wykorzystującym syntetyczną wodę morską 100% oraz 0,5 N roztwór chlorku sodu (NaCl).
Smary zakwalifikowane do posiadania znacznika HL wykazują doskonałe przenoszenie obciążenia i zapobieganie wnikaniu wody. Tag HL wymaga lepszych właściwości smarnych w teście zapobiegania zużyciu wg ASTM D2266 (Wear Prevention, test 4-kulowy) oraz odporności na wysokie ciśnienie wg ASTM D2596 (Extreme Pressure Properties, test 4-kulowy). Wymaga także zachowania właściwości smarnych w teście odporności na wysokie ciśnienie, wykonanym za pomocą maszyny testowej SRV według ASTM D5706 (Extreme Pressure Properties Using an SRV Machine) oraz ochrony przed zużyciem frettingowym wg ASTM D4170 (Fretting Wear Protection) i odporności na zużycie frettingowe wykonanym za pomocą maszyny testowej SRV wg ASTM D7594 (Fretting Wear Resistance Using an SRV Test Machine).
Smary ze znacznikiem LT są odporne na niskie temperatury (ang. low temperature) i muszą zachować właściwości smarne w teście momentu obrotowego łożyska kulkowego w niskiej temperaturze według ASTM D1478 (Low Temperature Ball Bearing Torque) oraz „testu mobilności smaru” i testu ciśnienia przepływu według normy DIN 51805 (Flow Pressure Test).
Specyfikacja smarów HPM według NLGI oraz jej różne „znaczniki” pozwalają specjalistom na dobór takiego produktu, który będzie miał właściwości smarne wymagane w bardzo specyficznych aplikacjach. Ponadto pozwalają firmom produkującym środki smarne na wytwarzanie preparatów dokładnie dobranych do potrzeb klientów, którzy potrzebują środków spełniających takie specyficzne wymagania.
1 American Society for Testing and Materials, Amerykańskie Stowarzyszenie Badań i Materiałów; obecnie organizacja międzynarodowa ASTM International.
2 Flow Pressure Test oraz „test mobilności smaru” według amerykańskiej firmy U.S. Steel Grease Mobility Test.
3 National Lubricating Grease Institute, NLGI.
4 według amerykańskiej firmy U.S. Steel Grease Mobility Test.
Chuck Coe zajmuje się środkami smarnymi od strony technicznej i marketingowej od ponad 40 lat. Jest członkiem Zarządu Instytutu NLGI.