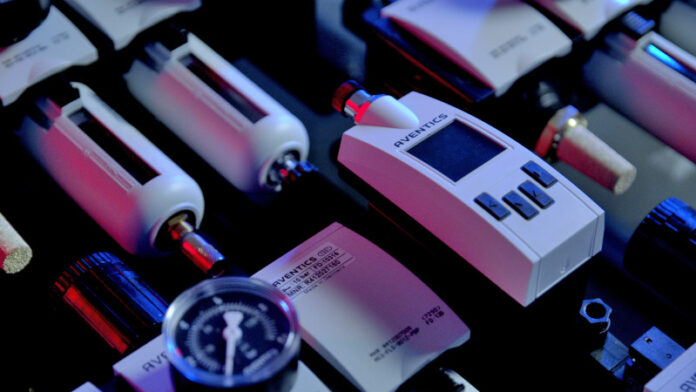
W wielu gałęziach przemysłu zwraca się szczególną uwagę na zużycie energii, zrównoważony rozwój i efektywne wykorzystanie narzędzi transformacji cyfrowej w celu kontrolowania kosztów i eliminowania marnotrawstwa energii. Szacuje się, że niektóre zakłady przemysłowe wydają prawie jedną trzecią budżetu na energię na wytwarzanie sprężonego powietrza do różnego rodzaju zastosowań. Niestety, nieprawidłowo utrzymywane i obsługiwane systemy mogą być przyczyną wycieku znacznej części sprężonego powietrza – marnując energię, zamiast wykorzystywać ją do uruchamiania procesów.
Komponent, który z czasem ulega degradacji lub którego konfiguracja nie jest w pełni zoptymalizowana, może powodować wycieki sprężonego powietrza. Z kolei procesy, które nie pracują na wystarczająco wysokim ciśnieniu sprężonego powietrza, mogą zużywać go więcej, co ma negatywny wpływ na powtarzalność i jakość procesów.
Jednym ze sposobów radzenia sobie z tym wyzwaniem jest konserwacja zapobiegawcza, która identyfikuje komponenty, które mogą wkrótce ulec awarii lub okazać się nieszczelne, zanim to nastąpi. Konserwacja prewencyjna może wcześnie zlokalizować nieszczelności i obliczyć odpowiednie proporcje ciśnienia przy jednoczesnym zachowaniu czasu cyklu. Aby to zrobić, konieczne jest posiadanie odpowiednich danych we właściwym czasie.
Jednak wiele firm nie wie, od czego zacząć, ponieważ mogą nie mieć zasobów lub narzędzi, które umożliwiłyby dostęp do tych informacji w dowolnym momencie, nie mówiąc już o właściwym czasie. Operatorzy, technicy lub zewnętrzni wykonawcy usług konserwacyjnych mogą ręcznie zbierać okresowe pomiary stanu sprzętu, ale informacje te mogą nie być aktualne i wiążą się z ryzykiem błędu ludzkiego. Nawet jeśli ręczne raportowanie jest dokładne, wynikowe arkusze kalkulacyjne lub jednorazowe raporty są często nieaktualne w momencie podjęcia decyzji. W rezultacie rzeczywisty stan aktywów może nigdy nie zostać dokładnie udokumentowany, co skutkuje nierozpoznaniem nieszczelności i niekontrolowanym wzrostem zużycia sprężonego powietrza. Kiedy przeprowadzana jest konserwacja, jest to „konserwacja awaryjna” lub wymiana komponentów, czy też naprawa sprzętu, gdy ten ulegnie awarii lub . Takie podejście praktycznie zawsze wiąże się z wyższymi kosztami i nieplanowanymi przestojami oraz negatywnie wpływa na ogólną efektywność energetyczną zakładu i cele zrównoważonego rozwoju.
Obecnie istnieje technologia, która daje lepsze możłiwości. Dzięki cyfrowej transformacji systemów pneumatycznych zużycie sprężonego powietrza można teraz monitorować w czasie rzeczywistym, aby zapewnić cenne, przydatne dane i wgląd w obiekty, które można wykorzystać do optymalizacji procesów pneumatycznych i kierowania działaniami w zakresie konserwacji predykcyjnej. Wykorzystując inteligentne technologie do podejmowania lepszych decyzji i natychmiastowych działań, można znacznie zmniejszyć zużycie sprężonego powietrza, wdrożyć lepszą konserwację zapobiegawczą i poprawić zrównoważony rozwój.

Transformacja technologii pneumatycznej
Transformacja cyfrowa to dla niektórych wciąż nowe pojęcie, które może wydawać się abstrakcyjne lub niejednoznaczne. W rzeczywistości jest zupełnie odwrotnie.
Transformacja cyfrowa to proces, któremu poddawany jest obiekt, system lub element wyposażenia, który pozwala użytkownikom końcowym widzieć dane w czasie rzeczywistym, podejmować decyzje na ich podstawie i działać w oparciu o te decyzje – tworząc inteligentniejsze maszyny i systemy umożliwiające inteligentne operacje. Mówiąc wprost, transformacja cyfrowa umieszcza właściwe informacje przed właściwym ekspertem we właściwym czasie. Eliminuje to potrzebę zgadywania parametrów procesu lub czekania na awarię sprzętu.
Przemysłowy Internet Rzeczy (IIoT) jest jednym z mechanizmów transformacji cyfrowej, umożliwiającym użytkownikom wykorzystanie istniejących danych poprzez integrację i łączenie inteligentnych czujników i przyrządów, które pozwalają procesom działać inteligentniej i wydajniej niż kiedykolwiek wcześniej.
W przypadku systemów sprężonego powietrza może to być tak proste, jak dodanie czujnika mierzącego zużycie czynnika lub tak skomplikowane, jak podłączenie całej nowej linii. Oba przypadki otwierają wcześniej niedostępne poziomy danych o sprężonym powietrzu i stanie zasobów, zapewniając operatorom lepsze zrozumienie obecnego i możliwego przyszłego stanu ich systemu pneumatycznego. Wiedza ta umożliwia im podejmowanie świadomych decyzji i wykonywanie szybkich działań.
Wykorzystując technologię do automatyzacji i optymalizacji procesów operacyjnych w ten sposób, przedsiębiorstwa uruchamiają ciągły cykl optymalizacji. Cykl ten musi składać się z trzech etapów: Patrz, Zdecyduj i Działaj. W zastosowaniach związanych ze sprężonym powietrzem różne inteligentne rozwiązania automatyzują każdy etap.
Etap patrz:
Ten etap uruchamia cykl, zaczynając od czujnika, który tworzy odpowiednie dane w sposób ciągły, powtarzalny i niezawodny. W systemach pneumatycznych proces ten obejmuje rejestrowanie przyspieszeń i cykli zaworów pneumatycznych oraz siłowników, a także pomiar objętościowego natężenia przepływu, ciśnienia, temperatury, masowego natężenia przepływu i prędkości przepływu sprężonego powietrza. Takie dane w czasie rzeczywistym dostarczają całodobowych informacji o faktycznym stanie zasobów obiektu i zużyciu energii oraz stanowią podstawę do podejmowania świadomych decyzji w odpowiednim czasie.
Etap zdecyduj:
Na tym etapie czujnik dostarcza zebrane dane do sterownika lub urządzenia bramy, które w sposób ciągły agreguje te informacje w czasie rzeczywistym i przedstawia trendy za pomocą łatwego do interpretacji narzędzia wizualizacyjnego. Taka wiedza specjalistyczna umożliwia operatorom podejmowanie szybkich i prawidłowych decyzji.
Etap działaj:
Narzędzia mobilne wykorzystywane na tym etapie wysyłają powiadomienia do konkretnego personelu, które określają jasne, niezbędne działania do podjęcia w oparciu o aktualny stan operacji. Może to obejmować informacje o tym, które siłowniki zbliżają się do końca okresu eksploatacji, mają zwiększone przyspieszenie w czasie lub przekroczyły już docelowy czas cyklu. Dyrektywy te umożliwiają personelowi rozwiązywanie problemów, zanim spowolnią lub zatrzymają daną operacje.
Łącznie etapy te oferują cenną analizę; ich niekończący się cykl generuje pętlę technologiczną, która umożliwia konserwację predykcyjną przy jednoczesnym ciągłym doskonaleniu wiedzy specjalistycznej i efektywności energetycznej.
Zapobiegaj nieplanowanym przestojom
Konserwacja jest nieodłącznym elementem wszystkich obiektów przemysłowych. W systemach pneumatycznych zawory zużywają się z czasem, powstają nieszczelności, które prowadzą do nadmiernego zużycia sprężonego powietrza. Niektóre systemy muszą mieć wiele zaworów, co może utrudniać identyfikację wadliwego zaworu. Rozwiązywanie problemów z nieszczelnościami może być czasochłonne, a przy ciągłym niedoborze siły roboczej i luce w umiejętnościach, personel konserwacyjny może być niewydajny. Może nie być wystarczającej liczby pracowników, aby nadążyć za tym, co należy zrobić, a wiedza dotycząca stanów z przeszłości może nie istnieć. Kiedy produkcja musi zostać zatrzymana na czas naprawy, może to być bardzo kosztowne. W przypadku średniej wielkości obiektów gastronomicznych nieplanowane przestoje kosztują około 100 000 zł za godzinę przestoju.
W najlepszym interesie zakładu jest zapobieganie problemom, zanim się pojawią. W tym miejscu z pomocą przychodzi konserwacja predykcyjna. Konserwacja predykcyjna może znacznie obniżyć koszty eksploatacji i konserwacji oraz wyeliminować nieplanowane przestoje.
Teraz, gdy wiemy już, jak działa cykl „patrz – decyduj – działaj”, łatwo jest sobie wyobrazić, w jaki sposób cyfrowa transformacja systemu pneumatycznego umożliwia konserwację predykcyjną. Rozważmy konserwację pneumatyki w przetwórstwie żywności i napojów, gdzie sprężone powietrze jest intensywnie wykorzystywane do uruchamiania zaworów pomocniczych i higienicznych za pomocą dyskretnych zaworów pilotowych lub systemów zaworów.
Zawory pomocnicze i higieniczne mogą być używane do podgrzewania, chłodzenia, dozowania lub napełniania dodatków i składników do zaworów sanitarnych, które transportują towary konsumpcyjne lub napoje. Połączone inteligentne czujniki, sterowniki i bramki brzegowe rejestrują pełniejszy obraz stanu zaworów, umożliwiając systemowi wykrywanie, kiedy zawory są zużyte lub zbliżają się do końca okresu eksploatacji. Jeśli taki zawór zostanie wykryty, system natychmiast wysyła alert do personelu konserwacyjnego, który planuje planowaną konserwację.
Zdolność do przewidywania potencjalnych problemów przed ich wystąpieniem pomaga ograniczyć nieplanowane przestoje, podczas gdy analiza przyczyn źródłowych w czasie rzeczywistym jasno określa odpowiednie działania, które należy podjąć. Zautomatyzowane usuwanie usterek i analiza jeszcze bardziej skracają czas konserwacji, zwiększają dostępność sprzętu, poprawiają produktywność, a w przypadku wycieków oszczędzają energię.

Cele zrównoważonego rozwoju, optymalizacja zużycia energii
Dzisiaj inteligentne urządzenia pneumatyczne zapewniają wydajność systemu pneumatycznego. Pozwala to zakładom zrozumieć, jak skutecznie kontrolować zużycie energii poprzez lokalizowanie i diagnozowanie wycieków oraz optymalizację ciśnienia w układzie sprężarki.
Sprężarki zużywają dużo energii, a ilość ta jest często większa niż ilość niezbędna do normalnych warunków pracy. Szacuje się, że od 20% do 30% zużycia energii w typowym zakładzie to produkcja sprężonego powietrza. Podczas gdy średniej wielkości obiekty często wydają 8 mln złotych rocznie na energię, każde zmniejszenie zużycia sprężonego powietrza może oznaczać znaczne oszczędności. Im bardziej możemy śledzić nieszczelności i zrównoważyć zasilanie zaworu, tym większą kontrolę mamy nad zużyciem energii. Optymalizacja sprężonego powietrza zużywanego przez zawór przy jednoczesnym osiągnięciu wymaganego czasu cyklu ogranicza ilość pracy, jaką musi wykonać sprężarka i pozwala jej zużywać tylko tyle energii, ile naprawdę potrzebuje do jej wykonania.
Dzięki cyfrowej transformacji systemów pneumatycznych w celu diagnozowania wycieków i obliczania właściwych stosunków ciśnień, zakłady mogą zauważyć zmniejszenie zużycia sprężonego powietrza i kosztów energii.
Idąc naprzód
Transformacja cyfrowa powinna być procesem ciągłym. Bez względu na to, jak wiele inteligentnych technologii zakład musiał wprowadzić do swoich systemów produkcyjnych, modernizacja systemów do najnowszej generacji pneumatyki z obsługą cyfrową stanowi podstawę do lepszego wglądu i kontroli zużycia sprężonego powietrza. Jednym ze sposobów na transformację pneumatyki jest współpraca z dostawcą kompleksowych rozwiązań pneumatycznych, który oferuje sprawdzoną wiedzę, czujniki i sprzęt. Doświadczeni dostawcy rozwiązań mogą współpracować z zakładem, aby zidentyfikować problemy i ustalić priorytety rozwiązań do wdrożenia. Każdy system produkcyjny i zakład jest inny; transformacja cyfrowa działa najlepiej, gdy jest opracowywana indywidualnie dla każdego przypadku, ściśle współpracując ze sprawdzonym dostawcą.
Niektóre przedsiębiorstwa mogą opierać się lub odkładać w czasie transformację cyfrową ze względu na obawy dotyczące kosztów i zakłóceń. Odpowiedzią na te obawy jest: „zacznij od małego, skaluj szybko”. Uproszczone podejście do transformacji cyfrowej to skupienie się na jednej kluczowej domenie lub wyzwaniu – nawet jednej maszynie – a następnie wykorzystanie wyciągniętych wniosków do zwiększenia zakresu stosowania takich rozwiązań. Istnieją dostawcy, którzy oferują kompletne, zintegrowane rozwiązania, które łączą komponenty, czujniki i sterowniki, a także pakiety analityczne zaprojektowane tak, aby umożliwić firmom czerpanie korzyści z cyfrowej transformacji na poziomie, który najlepiej odpowiada ich unikalnym wymaganiom. W przypadku obiektów, które są na dalszym etapie rozwoju, dostawcy oferują rozwiązania, które łączą istniejącą infrastrukturę czujników i sterowników z analityką brzegową.
Transformacja cyfrowa może szybko zapewnić znaczny zwrot z inwestycji dzięki lepszym informacjom i podejmowaniu decyzji. Zastosowanie pragmatycznego podejścia „patrz – decyduj – działaj” pomaga obiektom rozpocząć przygodę z transformacją cyfrową. Rezultat: informacje w czasie rzeczywistym są gromadzone i przekształcane w przydatne analizy i spostrzeżenia, aby kierować i ulepszać praktyki konserwacji predykcyjnej oraz optymalizować zużycie energii.
3 SZYBKIE FAKTY
Według Wikipedii pneumatyka to dziedzina inżynierii wykorzystująca gaz lub powietrze pod ciśnieniem.
Systemy pneumatyczne stosowane w przemyśle są powszechnie zasilane
przez sprężone powietrze lub sprężone gazy obojętne.
Centralnie umieszczona i zasilana elektrycznie sprężarka zasila siłowniki, silniki pneumatyczne, siłowniki pneumatyczne i inne urządzenia pneumatyczne.
________
Amit Patel jest starszym menedżerem ds. marketingu transformacji cyfrowej w dziale Fluid Control & Pneumatics w firmie Emerson. Koncentruje się na kierowaniu kierunkiem marketingowym i strategiczną wizją dla segmentu biznesowego Fluid Control & Pneumatics. Amit uzyskał tytuł licencjata w dziedzinie inżynierii elektrycznej w New Jersey Institute of Technology i posiada Six Sigma Black Belt w zakresie doskonalenia procesów z wykorzystaniem metodologii statystycznych.