Rozwiązania cyfrowe, pomagające w zarządzaniu fabryką pracującą w systemie 24/7, pozwalają zwiększyć niezawodność procesów oraz korzyści finansowe dla firm przemysłowych.
W przemyśle powszechnie występują zakłócenia realizowanych procesów technologicznych i produkcji. Muszą one być przewidywane i kontrolowane, gdyż ich skutki mogą być bardzo poważne. Niestety, pomimo wykorzystywania zaawansowanej technologii, przeznaczonej do bezproblemowego i stabilnego realizowania operacji, zakłócenia procesów w zakładach przemysłu chemicznego są nadal powszechne.
Zakłócenie jest wynikiem jednego lub większej liczby problemów związanych z realizowanym procesem. Powoduje ono zaburzenia prawidłowego przebiegu reakcji chemicznych. Zakłócenie może być mniejszego rzędu, takie jak stopniowy wzrost temperatury w czasie, który powoduje wyprodukowanie substancji o parametrach niezgodnych ze specyfikacją, jednak zakłócenie może być też bardzo poważne. Przykładem jest tu niekontrolowana reakcja chemiczna, która – jeżeli nie zostanie szybko zidentyfikowana i opanowana – może zagrozić środowisku oraz bezpieczeństwu pracowników w całej fabryce.
Niezależnie od tego, czy skutki zakłóceń procesów są bardzo poważne, czy też nie, zarządzanie nimi jest czasochłonne i tworzy zamieszanie dla kierownictwa fabryki oraz pracowników produkcji. Może to znacznie opóźnić termin realizacji produkcji. Zakłócenia procesów są szczególnie znaczące w przemyśle chemicznym, ponieważ wymagają wiele czasu do ich korygowania. Identyfikacja przyczyny zakłócenia oraz jej usunięcie może trwać całe godziny, a nawet dłużej niż cała zmiana robocza.
Pracownicy działów produkcji często nie dysponują narzędziami cyfrowymi, potrzebnymi do uzyskania szybkiego dostępu do informacji poprzez przechwyt wiedzy i autonomiczną komunikację podczas przekazywania zmiany roboczej. To powoduje istotne marnowanie czasu na poszukiwanie informacji, generowanie aktualizacji statusów, uzyskanie wyników poszukiwania przyczyn zakłócenia oraz raportowanie, co wynika z istnienia silosów informacyjnych, utrzymywanych przez różne działy fabryki i zmiany robocze.
Jeżeli pracownicy następnej zmiany nie mogą uzyskać dostępu do wszystkich ustaleń dotyczących zakłócenia procesu, to mogą być zmuszeni do ponownego wykonania poszukiwań i operacji. Zamiast prostego rozwiązania problemu zakłócenia, kierownictwo fabryki może być zmuszone do zawrócenia i powtórzenia poprzednich wysiłków.
Brak kluczowych informacji nie jest opcją. Każda godzina pozwolenia na utrzymywanie się zakłócenia procesu może negatywnie wpłynąć na zyski firmy, a nawet stworzyć katastrofalne zagrożenia dla bezpieczeństwa. W rzeczywistości reakcja jednostki operacyjnej na zakłócenie może być kluczowa dla niezawodności procesowej tej jednostki. Sukces i niezawodność jednostki są mierzone jakością reakcji organizacji na zakłócenie procesu.
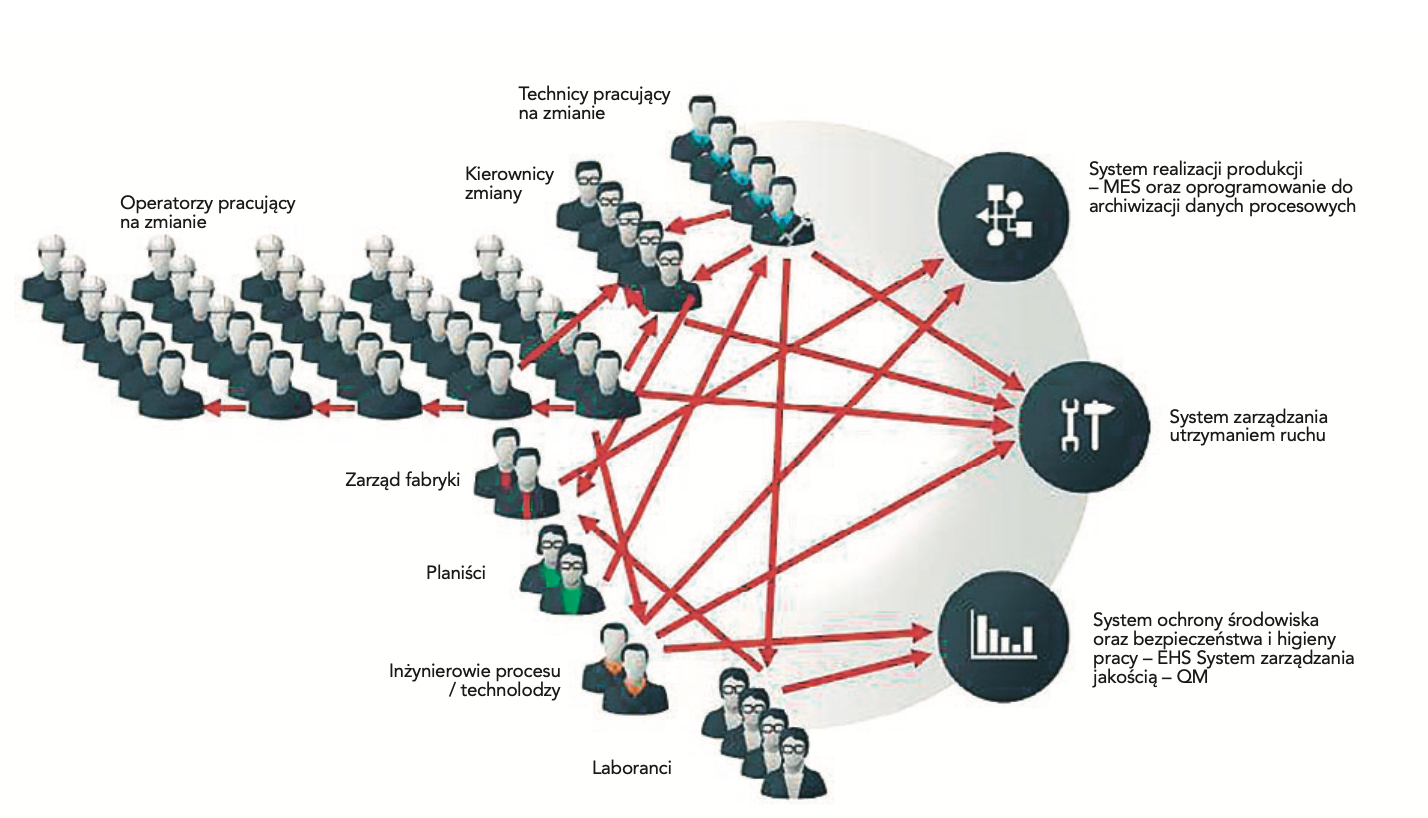
Problemy komunikacyjne
W zakładzie przemysłowym może pracować kilka zespołów na różnych zmianach. Wielu pracowników może wykonywać wiele różnych zadań, zależnie od wielkości zakładu. Fabryka może pracować nieprzerwanie (w trybie 24 × 7), tak więc problemy związane z procesami nie mogą być tolerowane. Fabryka realizująca pojedynczy proces technologiczny może zatrudniać ponad 60 pracowników wykonujących różne funkcje. Sprawą nadrzędną jest, aby wszystkie grupy pracowników miały możliwość komunikowania się ze sobą w celu uzyskania wspólnego zrozumienia tego, co jest wiadome i tego, co jest niewiadome na temat problemu, aby ludzie ci mogli efektywnie współpracować przy jego rozwiązywaniu (patrz Rys. 1).
Gdy personel fabryki w czasie występowania zakłócenia procesu musi jednocześnie wysyłać wiele e-maili oraz obsługiwać wiele arkuszy kalkulacyjnych i dokumentów, to te różne funkcje zwiększą trudności w uzyskaniu ogólnego obrazu zasadniczych problemów. Funkcjonowanie fabryki może więc być utrudnione z powodu istnienia wielu źródeł informacji. Ponadto bardzo prawdopodobne jest, że pracownicy wpadną w pułapkę przyjmowania błędnych założeń dla faktów. Dla każdego zakłócenia realne fakty muszą być rozpoznane i potwierdzone, aby zapewnić prawidłową reakcję. Przekazywanie zmian roboczych, gdy nowi pracownicy przychodzą do fabryki, czyni sytuację jeszcze bardziej problematyczną.
Należy pamiętać, że symptom nie jest problemem, tylko raczej nań wskazuje. Zbiór w pełni zbadanych symptomów może zidentyfikować powodujący je problem, bardzo podobnie jak w przypadku lekarza stawiającego diagnozę pacjentowi.
Tworzenie niezawodności
Zakłócenia procesów w fabrykach są z natury ciągłe i nie zawsze dają się rozwiązać do końca zmiany roboczej. Zarządzanie zakłóceniami w ciągu różnych zmian, gdy fabryka pracuje 24 godziny na dobę, wymaga zatem jakiegoś rozwiązania cyfrowego. Dział produkcji musi mieć system, dzięki któremu pracownicy następnej zmiany mają dostęp do informacji na temat postępów oraz kluczowych działań, wprowadzonych przez kolegów z poprzedniej zmiany.
Technologie cyfrowe, takie jak zarządzanie procesami realizowanymi w fabryce[1], dostarczają pojedynczą platformę, przedstawiającą „jedyną prawdę” dla wszystkich osób zaangażowanych oraz umożliwiającą pracownikom działów produkcji bardziej efektywne rozwiązywanie problemów związanych z zakłóceniami procesów (patrz Rys. 2). To sprawia, że wykonywane w fabryce operacje są niezawodne, pewne i bezpieczne. Uzyskanie ciągłej stabilności w obliczu konsekwentnych wyzwań związanych z procesami jest miarą tej niezawodności.
Dostarczenie pojedynczej platformy komunikacyjnej wszystkim pracownikom wykonującym funkcje związane z produkcją znacznie przyśpiesza rozwiązywanie problemów związanych z zakłóceniami procesów. Zapewnia to, że przekazywanie zmian roboczych nie ma wpływu na działania związane z usunięciem zakłóceń. Komunikacja na poziomie hali fabrycznej oraz całego zakładu musi być bezproblemowa, aby uniknąć czasochłonnego powtarzania poszukiwań przyczyny zakłócenia oraz prób rozwiązania tego problemu, gdyż czasu zwyczajnie brakuje.
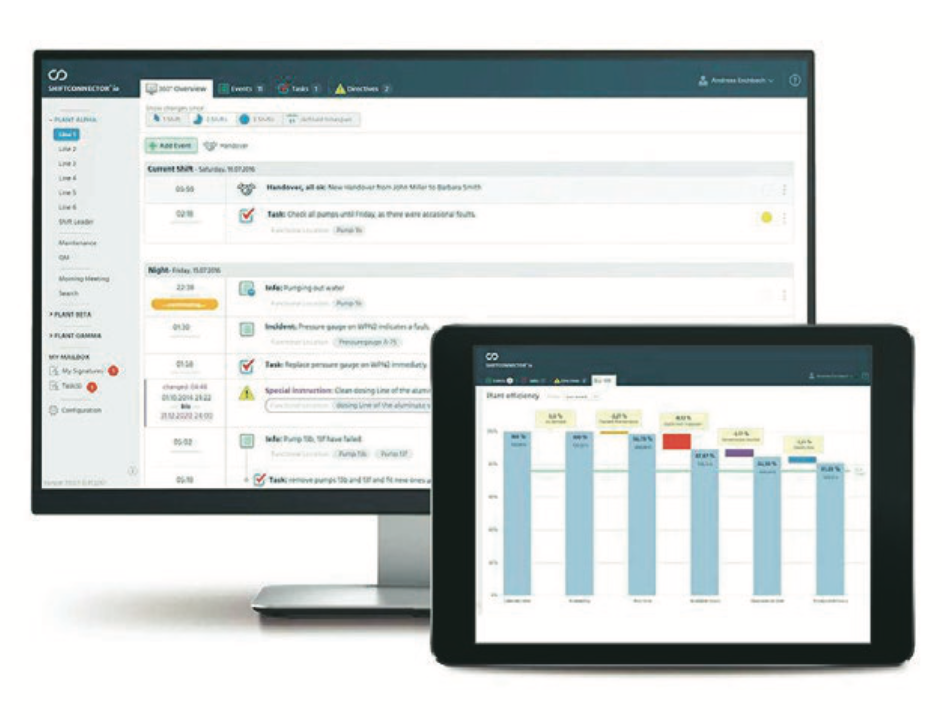
Przemysł chemiczny cierpli na brak digitalizacji
Badanie przeprowadzone przez firmę 451 Research pokazało, że zakłady przemysłu chemicznego są słabo wyposażone w sprzęt i oprogramowanie do cyfrowego transferu informacji. Jeśli chodzi o rozwiązania PPM, badanie pokazuje, że fabryki chemiczne są w większości nieprzygotowane do zapewnienia bezproblemowej komunikacji wewnętrznej i zewnętrznej. Jedynie 10% z 300 respondentów będących przedstawicielami kadry zarządzającej najwyższego szczebla odpowiedziało w ankiecie, że ich firmy są obecnie w stadium wdrażania technologii cyfrowej. Natomiast większość firm z branży przemysłu chemicznego nadal zbiera dane za pomocą ręcznego wpisywania (albo w ogóle nie zbiera).
Pomimo tych ustaleń nadal istnieje duże zainteresowanie cyfryzacją. Optymalizacja bezpieczeństwa oraz procesów są celami korporacji. Wnioski z badania są następujące:
- Komunikacja pomiędzy pracownikami różnych zmian oraz pełniącymi różne funkcje zwykle jest werbalna.
- Personel firmy poza działem produkcji niestety często nie jest informowany bezpośrednio. Ludzie ci są zwykle na bieżąco z tym, co dzieje się na produkcji, dzięki nieoficjalnym kanałom informacyjnym.
- Prace związane z utrzymaniem ruchu oraz inżynierskie są zapisywane na standardowych formularzach, które są następnie archiwizowane i niełatwo dostępne.
- Tworzy się raporty na papierze, które prawdopodobnie też są archiwizowane i w końcu zapomniane.
Niezawodność może być znacznie zwiększona poprzez ustanowienie „cyklu ulepszeń”. Podane niżej cztery etapy wspierają trwałą niezawodność:
- Identyfikacja problemu (według jego symptomów);
- Komunikacja między pracownikami (platforma programowa PPM, zapewniająca współpracę pomiędzy ludźmi z różnych zmian roboczych);
- Działanie korygujące (należy dokumentować kroki podjęte w celu rozwiązania problemu z zakłóceniem procesu);
- Dokumentacja wsteczna (na piśmie, nie werbalna; komunikaty są archiwizowane w bazie wiedzy).
Etap nr 4 jest często pomijany. Dokumentacja retrospektywna powinna opisywać i zatwierdzać wszystkie podjęte działania. Ludzie często mają skłonność do pomijania tego etapu, ponieważ „problem został rozwiązany i firma działa jak zwykle”. Dzięki wykonaniu tego etapu walidacyjnego oraz dodaniu go do platformy PPM zostanie jednak zbudowana baza wiedzy, która będzie mogła zostać wykorzystana do rozwiązania podobnego problemu w przyszłości lub służyć jako repozytorium dostępne dla wszystkich pracowników.
Tworzenie bazy wiedzy
Pandemia COVID-19 wywróciła do góry nogami normalny tryb procesów zarządzania. Przy wprowadzeniu pracy zdalnej starszy personel kierowniczy musi być w stanie zarządzać firmą z odległych lokalizacji. To znacznie zwiększa potrzebę posiadania systemu cyfrowego. Personel firmy nie może już dłużej polegać tylko na fizycznym dostępie do dokumentów oraz do współpracowników. Dokumentacja papierowa, taka jak wydruki arkuszy kalkulacyjnych, może rodzić problemy z dostępem, ponieważ obecnie bardzo wielu pracowników przebywa poza zakładem i pracuje zdalnie.
Dostęp cyfrowy ułatwia inżynierom przekazywanie zadań pracownikom zmian roboczych. Nie ma już znaczenia, gdzie dana osoba przebywa – w fabryce, w domu czy w jeszcze innym miejscu. Firmy muszą inwestować w platformy programowe, które przechwytują informacje wprowadzane przez pracowników jednej zmiany, aby były one dostępne dla pracowników następnej. Dziś takie platformy są projektowane w celu zapewnienia transparentności, niezawodności oraz widoczności dla wszystkich pracowników fabryki pełniących różne funkcje i role. Pomaga to różnym działom w uzyskaniu dobrej integracji.
Obecnie staje się możliwe integrowanie platform PPM z innymi systemami, niezbędnymi dla pracy fabryk. Systemy te to między innymi: skomputeryzowane systemy zarządzania utrzymaniem ruchu (CMMS), takie jak SAP PM lub IBM Maximo, oraz oprogramowanie do archiwizowania danych procesowych, takie jak OSIsoft PI lub LIMS.
Ta unifikacja umożliwia digitalizację procesów oraz ewolucję organizacji w kierunku niezawodnej, opartej o wiedzę, która potrafi szybko i skutecznie przezwyciężać zakłócenia procesów. Wynikiem unifikacji jest także znaczna korzyść finansowa dla firmy. Weźmy podstawowy przykład: fabryka produkująca fenol metodą kumenową. Ulepszenie reagowania na zakłócenia procesów może łatwo przynieść znaczne oszczędności. Trwający jeden dzień przestój zakładu albo wyprodukowanie wyrobu nienadającego się do sprzedaży może doprowadzić do strat wielkości 112 000 USD lub 56 000 USD na zmianę roboczą. Jest to znaczny koszt dla firmy, a i to przy założeniu, że nie wystąpi przy tym jeszcze uszkodzenie sprzętu.
Wdrożenie najnowocześniejszej technologii cyfrowej może przynieść firmie przemysłowej znaczne korzyści zarówno w postaci zwiększenia bezpieczeństwa, jak i ograniczenia strat finansowych.
Dr Joel Shertok, konsultant ds. inżynierii chemicznej i materiałów; Andreas Eschbach, dyrektor generalny (CEO) firmy eschbach GmbH.
[1] plant process management, PPM