Inżynierowie tribolodzy przedłużają żywotność maszyn dzięki integrowaniu wyników analiz laboratoryjnych środków smarnych z danymi generowanymi przez pracujący sprzęt.
Monitorowanie stanu środków smarnych oraz stanu technicznego maszyn, w których są one stosowane, staje się coraz ważniejsze, ponieważ użytkownicy końcowi chcą jak najbardziej wydłużyć okres eksploatacji swojego sprzętu. Użytkownicy końcowi wymagają obecnie, aby środki smarne i maszyny działały na optymalnym poziomie w coraz trudniejszych warunkach. Aby osiągnąć ten cel, stan techniczny maszyn i stan stosowanych w nich środków smarnych musi być monitorowany w celu zapewnienia, że środki te zachowują pierwotne właściwości eksploatacyjne, niezbędne do wykonywania wymaganych zadań.
Monitorowanie stanu, czyli analiza płynów, jest nadal cennym narzędziem wymaganym do okresowej oceny właściwości środków smarnych i stanu technicznego maszyn. Wartość tej techniki wzrasta, ponieważ użytkownicy końcowi mają mniejszą ilość zasobów, które są dla nich dostępne, a jeśli konkretna maszyna nie działa zgodnie z oczekiwaniami, zastosowanie monitorowania stanu ma zasadnicze znaczenie dla znalezienia przyczyny źródłowej problemu i jak najszybszego znalezienia jego rozwiązania w czasie rzeczywistym.
W niniejszym artykule przedstawiono aktualne informacje na temat nowych procedur testowych, które zostały wdrożone w celu oceny stanu środków smarnych i stanu technicznego maszyn. W celu napisania tego artykułu skontaktowano się z kilkoma kluczowymi ekspertami przemysłowymi, aby poznać ich punkt widzenia na nowe osiągnięcia w dziedzinie monitorowania stanu środków smarnych.
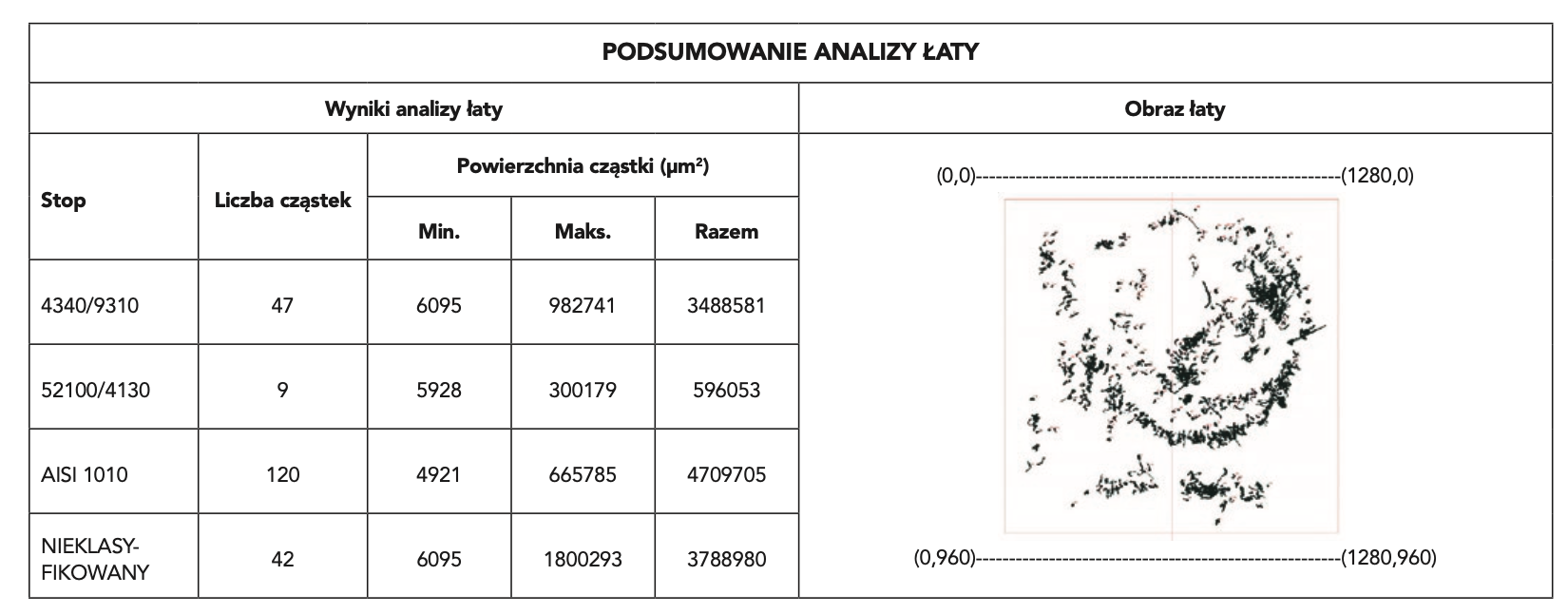
Analiza stopów w zanieczyszczeniach metalicznych środków smarnych
Allison Toms[1], starsza konsultant techniczna w firmie GasTOPS Inc. w Huntsville (stan Alabama, USA) i była wiceprezes ds. technologii i usług inżynierskich, skupiła się na wykorzystaniu technik monitorowania metalicznych zanieczyszczeń środków smarnych, będących skutkiem tarcia współpracujących powierzchni.
Od lat 40. XX wieku do badania zanieczyszczeń olejów smarnych w postaci drobin metali stosowano analizę pierwiastkową. Około 2000 roku szersze zastosowanie w analizie olejów smarnych, szczególnie w lotnictwie, znalazła analiza pojedynczych cząstek z wykorzystaniem skaningowej mikroskopii elektronowej sprzężonej z mikroanalizą rentgenowską (Scanning electron microscopy with energy dispersive X-ray spectroscopy; SEM-EDX), choć pierwotnie była ona wykorzystywana głównie do szczegółowej analizy uszkodzeń już po wystąpieniu awarii. Jednak mikroskopy skaningowe SEM-EDX, choć uproszczone w stosunku do urządzeń klasy laboratoryjnej, były nadal skomplikowane, trudne w obsłudze i ważyły 900 funtów (408 kg), co utrudniało ich zastosowanie na obiektach w przemyśle.
Allison Toms podała, że nowa technika analityczna, wykorzystująca laserowo wzbudzaną spektroskopię emisyjną (laser-induced breakdown spectroscopy; LIBS) do indywidualnej analizy opiłków metali, stanowi fundamentalną zmianę w dziedzinie analizy stanu olejów smarnych.
Możliwość identyfikacji poszczególnych stopów metali w opiłkach w oleju smarnym oznacza, że wyeliminowana została potrzeba interpretacji wyników oznaczeń pierwiastków. Klasyfikacja poszczególnych stopów w zanieczyszczeniach metalicznych olejów poprawia wykrywalność uszkodzeń smarowanych nimi maszyn, które często nie są wykrywane podczas analizy składu pierwiastkowego. Technika ta została początkowo opracowana dla maszyn o dużej wartości, takich jak samoloty.
Krótkie impulsy laserowe powodują ablację (odparowanie) cząstek metali i powstanie gorącej plazmy, emitującej promieniowanie, które jest analizowane za pomocą spektrometru. Cząstki metali mogą pochodzić z urządzeń zbierających i wykrywających wióry metali, filtrów i ferrografów. Mogą to być również luźne cząstki znajdujące się w środku smarnym. Technika ta jest obecnie wykorzystywana na całym świecie przez lotnictwo komercyjne, wojsko, działy utrzymania ruchu w przemyśle oraz producentów wyposażenia oryginalnego (OEM).
Przykładem może być analiza łaty do silnika lotniczego, pokazana na Rys. 1. Jak mówi Allison Toms:
Zakres wykrywania wielkości obejmuje cząstki o rozmiarach od nawet 70 mikronów do tysięcy mikronów. Klasyfikacja stopów jest lepsza niż 95% dla wszystkich 23 badanych stopów, a dla niektórych nawet lepsza niż 97%. Technika, którą stosujemy, pozwala w ciągu kilku minut przeanalizować do 20 cząstek i określić ich skład według stopu oraz rozmiary. Urządzenie jest małe, lekkie, przenośne i łatwe w obsłudze.
Wykorzystywana jest też technika uzupełniająca, znana jako zaawansowana analiza drobnych cząstek metali w oleju (advanced oil fines analysis, AOFA). Identyfikuje ona zanieczyszczenia metaliczne w środkach smarnych według stopów i według wielkości cząstek do 0,5 mikrona oraz zawartość procentową każdego stopu, co daje dodatkowe informacje na temat stopnia uszkodzenia smarowanego urządzenia.
Jak mówi Allison Toms: W technice AOFA wykorzystuje się obecnie lasery SEM-EDX do analizy i identyfikacji stopów w cząstkach metali w środkach smarnych. Technika ta jest obecnie wykorzystywana przez linie lotnicze do badania silników, co pozwala z dużym wyprzedzeniem czasowym uzyskiwać informacje o zbliżających się awariach. Obecnie prowadzone są badania mające na celu włączenie tej technologii do mniejszej, kompaktowej metody LIBS.
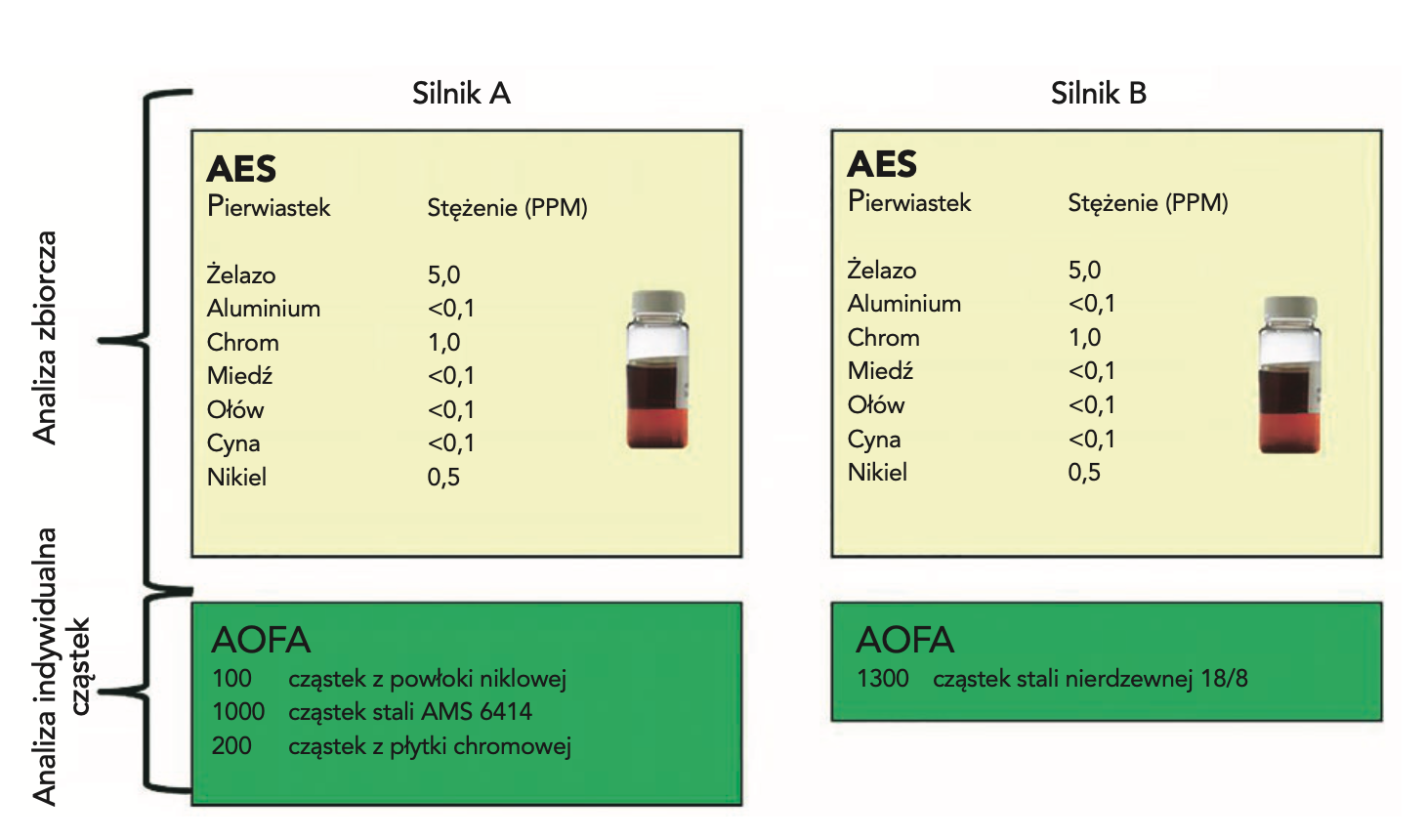
Na Rys. 2 porównano analizę AOFA z atomową spektroskopią emisyjną (atomic emission spectroscopy; AES) w dwóch silnikach lotniczych. Jak mówi Allison Toms:
Wystąpiły dwie różne awarie, ale wyniki spektroskopii AES były identyczne dla obydwu silników. Natomiast analiza AOFA oceniła każdą cząstkę i wygenerowała szczegółowe wyniki badania składu stopowego. Różnica między tymi dwiema technikami polega na tym, że AOFA analizuje cząstki indywidualnie, podczas gdy AES zapewnia zbiorczą analizę chemiczną/pierwiastkową wszystkich cząstek razem.
Kolejną zaletą analizy cząstek metali w oleju LIBS jest wykorzystywany sprzęt – przenośny, łatwy w użyciu i dostarczający wyniki w krótkim czasie. Jak mówi Allison Toms: Szczególnie wojsko chciało mieć mniejsze, bardziej wytrzymałe i łatwiejsze w obsłudze urządzenie.
Allison Toms podała przykład firmy posiadającej samoloty z silnikami turbośmigłowymi, która wykorzystała analizę AOFA do wykrycia problemu niemożliwego do zidentyfikowania za pomocą spektrometrycznej analizy oleju.
Gdy zaświeciła się lampka ostrzegawcza, sygnalizując wykrycie problemu, próbka oleju została przetestowana za pomocą analizy AOFA, co potwierdziło podejrzenia firmy, że przyczyną było uszkodzenie uszczelki karbonowej. Tak więc zaplanowano zapobiegawczo demontaż silnika podczas następnego postoju samolotu i potwierdzono wtedy pogorszenie stanu technicznego tej uszczelki. Firma będąca właścicielem samolotu turbośmigłowego wykryła ten problem ponad 700 godzin przed planowanym demontażem silnika, co pozwoliło zaoszczędzić około 400 000 USD dzięki uniknięciu opóźnień i odwołań lotów oraz szkód wtórnych.
Allison Toms uważa, że zawsze istnieje zapotrzebowanie na lepszą diagnostykę i prognostykę w monitorowaniu pracy i stanu technicznego maszyn: Znajomość konkretnego stopu (stopów) i liczby cząstek każdego stopu zapewnia większą szczegółowość informacji na temat zużywających się elementów. Wiedza ta umożliwia bardziej dogłębną analizę przyczyn awarii i wcześniejsze informowanie o zbliżających się awariach. Dodanie informacji o stężeniu procentowym każdego stopu zwiększa wiedzę na temat powagi uszkodzenia.
Przenośne laboratorium analityczne
Członek Stowarzyszenia STLE Jack Poley z firmy Condition Monitoring International w Miami (Floryda) również uważa, że dostępność przenośnych urządzeń doprowadziła do powstania nowych procedur testowych monitorowania stanu.
Mówiąc przede wszystkim o analizie płynów, testy wykonywane za pomocą urządzeń przenośnych, w tym przyrządów ręcznych, odgrywają obecnie znaczącą rolę w tym, co jest postrzegane jako rosnący ruch w kierunku „maszyny”, a więc pojawienie się kompaktowych laboratoriów do pracy na obiektach. Laboratoria te wykonują najbardziej popularne z obecnie stosowanych testów cząstek metali w środkach smarnych, w tym AES (Atomic Emission Spectrometry; atomowa spektroskopia emisyjna). Jest to odzwierciedleniem dążenia do bardzo szybkiego (w czasie rzeczywistym) uzyskania danych, na których podstawie można dokonać oceny stanu tak szybko, jak to tylko możliwe.
Do monitorowania stanu technicznego maszyn w czasie rzeczywistym wykorzystywane są czujniki. Jak mówi Jack Poley: Czujniki w analizie płynów są stosunkowo nowością (pojawiły się około 2000 roku), ale nadal nie są wystarczająco stabilne, aby przetrwały w gorącym, często zanieczyszczonym środowisku pracy środka smarnego. Jednak czujniki do analizy płynów nie mogą konkurować z czujnikami drgań, ponieważ dane z nich są zbyt niekompletne ze względu na ograniczenia możliwości przyrządów, takie jak możliwość wykrywania tylko zużycia elementów wykonanych ze stali (żelaza), a nie innych niezbędnych w konstrukcji maszyn stopów metali (zawierających miedź, ołów, aluminium itp.). Inny pierwiastek – krzem – nie może być wykrywany przez obecnie dostępne czujniki. W miarę jak czujniki będą zyskiwały coraz większą czułość i zaczną naśladować pełny zakres badań środków smarnych w celu monitorowania stanu technicznego maszyn będzie kontynuowany rozpoczynający się obecnie postęp polegający na tym, że laboratoria stacjonarne będą coraz bardziej ustępowały laboratoriom mobilnym.
Jack Poley podaje przykład w pełni wyposażonego laboratorium przewoźnego, w którym metodą kontroli metali zużywających się jest spektrometr fluorescencji rentgenowskiej (X-ray fluorescence spectrometer; EDXRF): To laboratorium jest w stanie wykryć możliwości wystąpienia awarii w krótkim terminie poprzez ilościowe określenie dużych cząstek metali (większych niż cztery mikrony) w środku smarnym, poza żelazem i innymi metalami.
Według Poleya technikę tę można zaadaptować do oceny środków smarnych w trakcie eksploatacji do oceny skutecznej smarowności: Zmniejszenie wytrzymałości filmu olejowego może prowadzić do nadmiernego smarowania granicznego, które może zmylić analizę dużych cząstek metalu w oleju (LPWM).
Jack Poley zaznaczył, że w przyszłości takie oprzyrządowanie będzie zawierało oprogramowanie wykorzystujące sztuczną inteligencję (AI), ponieważ takie aplikacje już istnieją. Ten w pełni zrealizowany projekt podniesie poziom analizy płynów, wykorzystywanej do monitorowania stanu środków smarnych tak, aby nie tylko zapewniać analizę w czasie rzeczywistym, ale także oferować autodiagnostykę i doradztwo.
Większość postępów w dziedzinie monitorowania stanu technicznego nie dotyczy technologii wykorzystywanych do przeprowadzania testów, ale poprawy łatwości i szybkości ich wykonywania. Jak mówi Jack Poley: W ciągu ostatnich pięciu lat nie opracowano żadnych rzeczywistych nowości z wyjątkiem przenośnego laboratorium analitycznego. Skupiono się na przyspieszeniu wykonywania testów monitorujących stan, bez pogorszenia jakości wykrywania i oznaczania ilościowego.
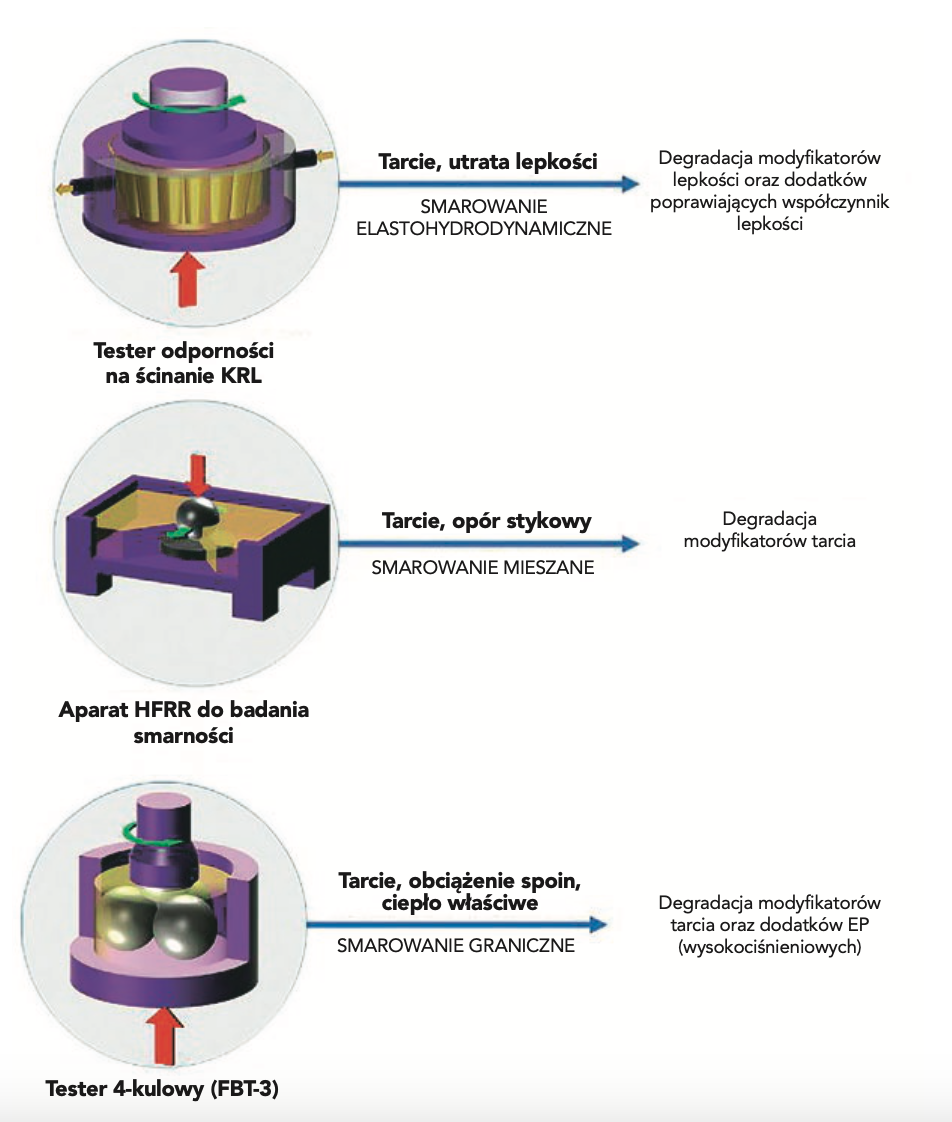
Dlaczego trybometry są wygodnymi narzędziami
Wygoda jest kluczową cechą, jak uważa dr Deepak Veeregowda, dyrektor ds. globalnego marketingu i sprzedaży w firmie Ducom Instruments Europe B.V. z siedzibą w Gronigen, Holandia.
Obecnie jesteśmy proszeni o wykorzystanie trybometrów (zaprojektowanych do pomiaru tarcia i zużycia środków smarnych) w monitorowaniu stanu środków smarnych podczas ich eksploatacji. Trybometry są stosowane w połączeniu z narzędziami konwencjonalnymi, takimi jak spektroskopy, które ustalają korelację pomiędzy ubytkiem dodatków w środku smarnym a czynnikami wpływającymi na wydajność maszyny, takimi jak tarcie – mówi dr Veeregowda.
Deepak Veeregowda podkreśla, że chociaż analiza spektroskopowa może zmierzyć wzrost tarcia, który wskazuje na spadek wydajności środka smarnego, technika ta niekoniecznie potwierdza, że przyczyną jest degradacja dodatków do środka smarnego: Trybometry mogą pomóc w znalezieniu przyczyny źródłowej spadku wydajności środka smarnego i określeniu, czy dodatek, taki jak modyfikator tarcia lub dodatek wysokociśnieniowy, uległ degradacji w trakcie stosowania środka smarnego.
Veeregowda podaje przykłady trybometrów, takich jak tester wytrzymałości na ścinanie KRL, używany do pomiaru wyczerpywania się modyfikatorów lepkości, aparat o ruchu posuwisto-zwrotnym wysokiej częstotliwości do badań smarności (high freguency reciprocating rig; HFRR), używany do monitorowania modyfikatorów tarcia oraz tester czterokulowy, który mierzy wyczerpywanie się zarówno modyfikatorów tarcia, jak i dodatków wysokociśnieniowych.
Na Rys. 3 przedstawiono wszystkie trzy trybometry i wskazano system smarowania, w którym one funkcjonują. Jak mówi Deepak Veeregowda: Trybometry mogą być stosowane do monitorowania stanu, do pomiaru współczynnika tarcia, ciepła właściwego, utraty lepkości i średnicy skazy zużycia. Środki smarne, dla których można wykorzystać trybometry, obejmują: oleje przekładniowe takie jak oleje przekładniowe, oraz płyny hydrauliczne stosowane w przemyśle ciężkim i energii odnawialnej.
Wraz z rosnącym wykorzystywaniem stopów aluminium i innych metali nieżelaznych opracowywanie środków smarnych z dezaktywatorami metali oraz monitorowanie ich wydajności w czasie stało się ważniejsze dla użytkowników końcowych. Doskonałym przykładem jest tu analiza stanu syntetycznego oleju przekładniowego stosowanego w turbinach wiatrowych. Oczekuje się, że ten olej przekładniowy będzie zapewniał optymalną wydajność turbiny podczas jej pracy przez wiele lat.
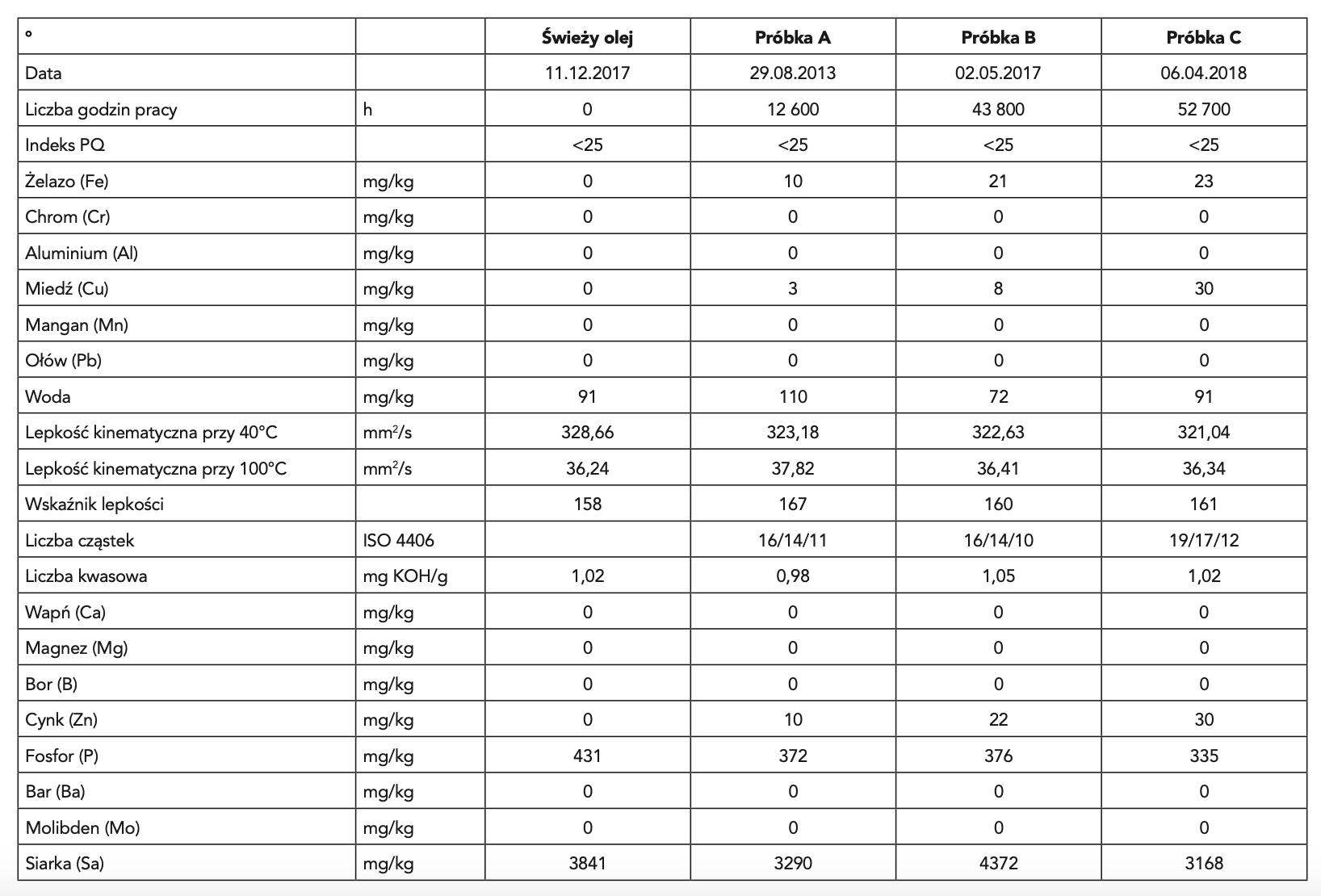
Wysokosprawna chromatografia cieczowa (HPLC)
Jak mówi dr Thomas Fischer, dyrektor naukowy w firmie OELCHECK GmbH z siedzibą w Brannenburgu, (Niemcy): Tradycyjną techniką monitorowania syntetycznych olejów przekładniowych jest spektroskopia w podczerwieni z transformacją Fouriera (Fourier-transform infrared spectroscopy, FTIR). Dostarcza ona informacji opartych na zmianach zachodzących w zużytym oleju poprzez porównanie jego widma z widmem odpowiadającego mu świeżego oleju lub oleju referencyjnego.
Oprócz innych wyników spektroskopia FTIR może wykryć utlenianie oleju poprzez tworzenie wiązań tlenowych, ale, szczególnie w przypadku olejów syntetycznych, metoda ta nie może być stosowana do ilościowego określenia tego zjawiska. Zmiany w widmie FTIR mogą być określone ilościowo tylko wtedy, gdy molekuły obecne w środku smarnym absorbują światło podczerwone w różny sposób przy różnych długościach fal. Oleje PAO (polialfaolefiny) lub estrowe są stosowane jako oleje bazowe w nowoczesnych syntetycznych olejach przekładniowych, ponieważ mają większą stabilność oksydacyjną przez długi czas w porównaniu z konwencjonalnymi olejami mineralnymi grupy I lub II.
W przypadku stosowania środków smarnych na bazie olejów mineralnych metoda IR może być użyta do obliczenia utleniania poprzez rosnący pik przy liczbie falowej 1710 cm-1. Pik ten jest reprezentatywny dla wiązań karbonylowych. Wzrasta on w sposób ciągły w miarę starzenia się środka smarnego z powodu wprowadzenia tlenu do cząsteczek węglowodorów. Jednak tego podejścia nie można zastosować do smarów na bazie estrów, ponieważ jeden z głównych pików estrów występuje przy bardzo bliskiej liczbie falowej 1740 cm-1. Dlatego też piku przy 1710 cm-1 nie można wykorzystać w przypadku olejów syntetycznych do monitorowania degradacji oleju wskutek utleniania, mówi Thomas Fischer.
Ze względu na utlenianie syntetyczne oleje przekładniowe są przeznaczone do eksploatacji w czasie nie dłuższym niż 10 lat. Ich stan nie może być monitorowany metodą FTIR, tak więc opracowano metodę uzyskiwania dodatkowych informacji o tych środkach smarnych. Metoda ta wykorzystuje alternatywną technikę, znaną jako wysokosprawna chromatografia cieczowa (high pressure liquid chromatography, HPLC). W dziedzinie zastosowań przemysłowych chromatografia HPLC jest powszechnie stosowana do pomiaru zubożenia inhibitorów w chłodziwach na bazie wody. Do opracowania nowej metody wykorzystano próbki syntetycznego oleju przekładniowego, pobierane z przekładni turbiny wiatrowej w okresie sześciu lat.
Główna przekładnia planetarna turbiny wiatrowej o mocy 1,5 MW jest wypełniona około 600 litrami syntetycznego oleju przekładniowego. Przez sześć lat okresowo wykonywaliśmy analizy tego oleju. Próbki do badań metodą HPLC zostały pobrane odpowiednio po 12 600, 43 800 i 52 700 godzinach pracy turbiny. Co prawda wszystkie wyniki standardowej analizy używanego oleju, jak pokazano na Rys. 4, wskazywały, że kluczowe parametry oleju przekładniowego są zgodne z oczekiwanymi, jednak olej stawał się coraz ciemniejszy, jak pokazano na Fot.5. Mimo że nie ma tu żadnego standardu, zmiana koloru pozwala inżynierowi trybologowi, który indywidualnie diagnozuje każdą próbkę, na dokonanie szacunkowej oceny, czy skład środka smarnego mógł się zmienić z upływem czasu – mówi Thomas Fischer.
Pierwsza próbka oleju – po 12 600 godzinach pracy – była jasna i klarowna, podobna do świeżego oleju. Kolejne próbki pokazały, że olej zmienił w krótkim czasie kolor na ciemnobrązowy.
To ciemnienie oleju nie dało żadnych wskazówek, czy wydajność środka smarnego się pogorszyła, ale było niepokojące i doprowadziło do dalszych badań właściwości oleju. Przeglądając zwykłe wyniki analiz, stwierdziliśmy, że kluczowe parametry, takie jak lepkość, wskaźnik lepkości i zawartość wody, a także porównanie w podczerwieni, pozostały niezmienione. Jedynie liczba zasadowa (TBN), będąca miarą kwasowości, nieznacznie wzrosła. Zawartość kluczowych pierwiastków w dodatkach do oleju, czyli fosforu i siarki, spadła tylko nieznacznie, ale pozostała w granicach oczekiwań. Nie stwierdzono wzrostu zawartości metali z elementów zużywających się z wyjątkiem miedzi. W diagnozie stwierdzono, że olej może pozostać w eksploatacji, jednak ze względu na zawartość miedzi powinien być analizowany w krótszych przedziałach czasowych, mówi Thomas Fischer.
Zawartość miedzi, która mieściła się w granicach normy po 43 800 godzinach pracy, znacznie wzrosła po 52 700 godzinach. Doprowadziło to do zalecenia, że olej należy natychmiast wymienić. Jednak zawartość miedzi niekoniecznie wyjaśniała odbarwienie środka smarnego.
Odnieśliśmy wrażenie, że wzrost zawartości miedzi może wskazywać na spadek stężenia dezaktywatora metali nieżelaznych w oleju przekładniowym. Uderzyło nas, że zarówno wysoki wzrost poziomu miedzi, jak i ciemne przebarwienie oleju przekładniowego miały miejsce w stosunkowo krótkim czasie, poniżej 10 000 godzin pracy. Niestety, nie mogliśmy zastosować żadnej z szybkich i stosunkowo niedrogich tradycyjnych technik analitycznych, w tym FTIR, aby określić, czy i jak bardzo zmieniło się stężenie dezaktywatora metalu. Dodatki dezaktywujące metale są zwykle oparte na związkach azolowych. Przykładami są tu tolytriazol i benzotriazol, mówi Thomas Fischer.
Te dezaktywatory metali są bardzo skuteczne w ochronie powierzchni zawierających miedź przed zużyciem korozyjnym. Niestety, dezaktywatory metali stale się zużywają. Jeśli nie są obecne w środku smarnym, rozpoczyna się korozja miedzi. W przekładniach elektrowni wiatrowych głównymi elementami, w których ta korozja prowadzi do katastrofalnej awarii, są koszyki dwurzędowych łożysk baryłkowych. Jeśli łożyska te ulegną awarii, wynikiem będzie bardzo kosztowna naprawa.
Ponieważ regularnie stosujemy metodę HPLC do pomiaru stężenia inhibitorów w chłodziwach samochodowych, postanowiliśmy wykorzystać ten instrument również do oceny dezaktywatorów metali w smarach i określenia pozostałego stężenia inhibitorów metali nieżelaznych w syntetycznych olejach przekładniowych, mówi Thomas Fischer.
Metoda HPLC została wykorzystana do pomiaru stężenia toliltriazolu i benzotriazolu w próbkach świeżego i zużytego oleju.
Stwierdziliśmy, że świeży olej wykazywał wysoką zawartość toliltriazolu. Jednak po przepracowaniu 43 800 godzin stwierdziliśmy znaczny spadek stężenia tego rodzaju dezaktywatora metalu. Próbka, która była używana przez ponad 50 000 godzin, wykazała jedynie bardzo małe stężenie dezaktywatora metali nieżelaznych. Ten spadek zawartości dezaktywatora może być wykorzystany jako silna wskazówka, że wysoka zawartość miedzi w próbce oleju jest spowodowana zużyciem korozyjnym koszyka łożyska, ponieważ dodatek ten nie jest już obecny. Z naszego doświadczenia wynika, że stężenie metali nieżelaznych, takich jak miedź, ołów i cyna, może gwałtownie wzrosnąć w bardzo krótkim czasie, gdy układ pracuje z wyczerpanym inhibitorem. Nowa metoda HPLC, obecnie stosowana jako standardowa w analizie oleju przekładniowego, stanowi podejście do monitorowania możliwego źródła szybko postępującego zużycia korozyjnego.
Thomas Fischer uważa, że gdyby do monitorowania stanu oleju w przekładni turbiny wiatrowej użyto metody HPLC, wówczas spadek stężenia dezaktywatora metalu zostałby stwierdzony już po 43 800 godzinach pracy tej turbiny: Znając te wyniki, nasi eksperci z dziedziny trybologii zaleciliby wymianę oleju przekładniowego po upływie kolejnych 2000 godzin pracy, ponieważ w przeciwnym razie zużycie koszyka łożyska będzie szybko rosło.
Metoda HPLC jest w porównaniu z innymi metodami analizy oleju czasochłonną i kosztowną techniką analityczną, ale Thomas Fischer uważa, że wyniki uzyskane w tym studium przypadku uzasadniają jej zastosowanie: Sam proces jest stosunkowo kosztowny ze względu na fakt, że przed analizą HPLC każda próbka musi zostać poddana ekstrakcji metodą ekstrakcji do fazy stałej. Jednak zaawansowany system ostrzegania, możliwy dzięki analizie HPLC, jest uzasadniony, ponieważ pozwala uniknąć uszkodzeń i kosztownych napraw.
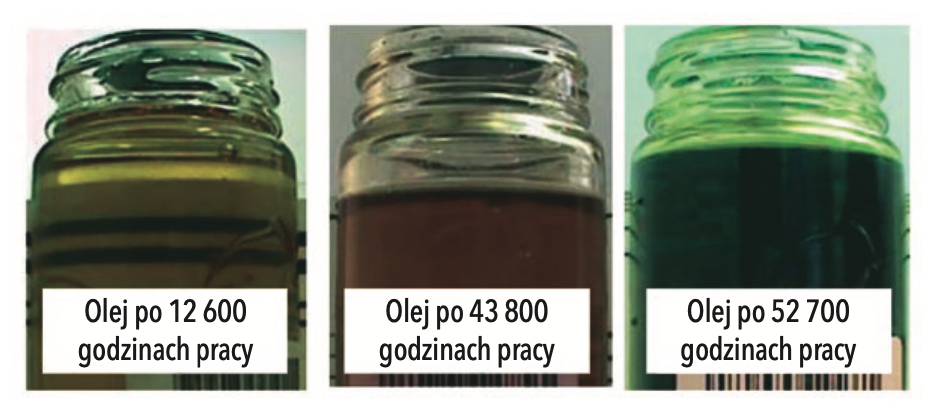
Kolorymetria sączka membranowego (MPC)
Greg Livingstone, członek STLE i główny specjalista ds. innowacji w firmie Fluitec International w Bayonne (stan New Jersey) stwierdził, że kolorymetria sączka membranowego (membrane patch colorimetry test, MPC, przeprowadzana według normy ASTM D7483) wniosła znaczący wkład w monitorowanie stanu płynów stosowanych w turbinach czy sprężarkach oraz płynów hydraulicznych pod względem tendencji do tworzenia osadów. Procedura ta jest w stanie przewidzieć, kiedy płyn może potencjalnie tworzyć osady, umożliwiając użytkownikom podjęcie proaktywnych działań przed tworzeniem się laków.
Procedura kolorymetrii sączka membranowego wygląda następująco. Próbka badanego płynu jest rozcieńczana taką samą objętością eteru naftowego i filtrowana przez membranę nitrocelulozową o wielkości por 0,45 mikrona. I dalej, jak mówi Greg Livingstone: Kolor produktów degradacji oleju wyłapanych przez filtr jest mierzony za pomocą spektrofotometru i porównywany z kolorem kontrolnym. Różnica kolorów (ΔE) jest następnie oceniana w skali CIE, aby oszacować wielkość osadów. Metoda ta umożliwia użytkownikom końcowym podjęcie proaktywnych działań przed utworzeniem się laków, które mogą mieć szkodliwy wpływ na środek smarny. Test wykorzystujący kolorymetrię sączka membranowego jest jedyną metodą zatwierdzoną przez ASTM, zaprojektowaną w celu przewidywania właściwości osadów tworzących się w środkach smarnych w trakcie eksploatacji. Użytkownicy tej metody unikają konieczności reagowania, gdy osadzające się laki spowodują problem z niezawodnością sprzętu.
Greg Livingstone podkreślił, że do stosowania tej procedury badawczej najbardziej nadają się te aplikacje środków smarnych, które są wrażliwe na powstawanie osadów, w tym turbiny, sprężarki i układy hydrauliczne: Procedura ta okazała się skuteczna w ocenie tworzenia się osadów w mineralnych i syntetycznych przemysłowych środkach smarnych niezawierających detergentów. Środki smarne z dodatkami detergentów i dyspergatorów nie zostały jeszcze dokładnie przebadane. Jedną z obaw jest to, że smary zawierające duże ilości zanieczyszczeń będą zatykać membranę, co znacznie utrudni przeprowadzenie badania lub będzie wymagało zastosowania jego rozszerzonej procedury.
Greg Livingstone zaznaczył, że większość producentów OEM maszyn wirujących zaleca obecnie kolorymetrię saczka membranowego jako kluczowy element monitorowania płynów stosowanych w ich produktach i systemach: Obecnie trwają badania nad opracowaniem procedury online, która umożliwiłaby odpowiednie wykonywanie w czasie rzeczywistym testów osadów powstających w środkach smarnych. Nadzieją jest umożliwienie użytkownikom końcowym szybszego określenia stanu ich systemów smarowania, aby można było podjąć niezbędne działania korygujące.
Wpływ pienienia na działanie środka smarnego
Piana, czyli powietrze w środku smarnym, może negatywnie wpływać na działanie tego środka. Wśród problemów, jakie może powodować piana, jest zmniejszenie zdolności środka smarnego do odprowadzania ciepła, zwiększenie możliwości utleniania i powodowanie słabego przepływu płynu w zastosowaniach takich jak układy hydrauliczne.
Jak mówi dr Aaron Mendez, dyrektor ds. badań i zastosowań w firmie Ayalytical Instruments Inc. z Chicago: Skłonność środków smarnych do pienienia jest jedną z ich najważniejszych właściwości, jakie należy wyznaczać.
Dwie z metod stosowanych do określania skłonności do pienienia to według norm: ASTM D892 i ASTM D6082. Obie metody są w pewnym stopniu zależne od operatora, charakteryzują się niską dokładnością i są podatne na błędy ludzkie w przygotowaniu próbki do testu i postępowaniu z nią. Innymi problemami są: duże gabaryty urządzenia testowego, trudności w operowaniu próbkami oleju przeznaczonymi do testu oraz stosunkowo długi czas jego trwania testu, mówi Aaron Mendez.
Opracowano nową aparaturę do badania skłonności do pienienia, która wykorzystuje standaryzowane oświetlenie, kamerę o wysokiej rozdzielczości oraz zgłoszony do opatentowania algorytm do dokładnego i wielokrotnego pomiaru wysokości piany w różnych warunkach przeprowadzania testów za pomocą dwóch wspomnianych metod. Aparatura mierzy powstawanie piany, jej rozpraszanie, wysokość piany i uwalnianie powietrza.
Ta nowa aparatura testowa, będąca obecnie w trakcie opracowywania w celu zatwierdzenia przez ASTM jako nowelizacja norm D892 i D8062, zapewnia poprawę czułości, precyzji i niezależnego od operatora określania skłonności środków smarnych do pienienia. Poprawiona została również przepustowość testowanych próbek, zmniejszona niepewność analizy. Aparatura pozytywnie wpływa na ogólny proces kontroli jakości i charakterystyki produktu, mówi Aaron Mendez.
Aaron Mendez zaznacza też, że nowa aparatura do badania skłonności do pienienia nie jest w żaden sposób niekompatybilna z formułami środków smarnych: Użytkownicy tej techniki testowej będą mogli opracować aplikacje do określania wydajności dodatków (w szczególności zapobiegających pienieniu), badania kinetyki piany i przeprowadzania eksperymentów z uwalnianiem powietrza.
Zautomatyzowana procedura, stosowana w nowej aparaturze do badania skłonności do pienienia, umożliwia szybkie i jednoznaczne określenie wpływu konfiguracji i konstrukcji przyrządu na określenie skłonności środków smarnych do pienienia oraz wysokości powstałej piany. Jak dodaje Aaron Mendez: Nowa procedura badawcza umożliwia ocenę materiału i kształtu dyfuzorów gazu oraz obiektywne określenie możliwych korelacji pomiędzy wielkością porów a wytwarzaniem piany.
Ta nowa aparatura testowa zapewnia użytkownikowi korzystne warunki do badania skłonności do pienienia i dokładnego pomiaru piany. Jak mówi Aaron Mendez: Stwierdziliśmy, że wysokość piany i temperaturę można mierzyć z niepewnością +/- 0,25 mililitra piany i z niepewnością temperatury +/- 0,1° C.
Aaron Mendez oczekuje, że tę nową technikę będzie można zaadaptować do obserwowania w trybie online wydajności baz środków smarnych oraz gotowych preparatów.
Przyszłość
Jak mówi Greg Livingstone: Zmiany w przemyśle środków smarnych są nieuchronne, ponieważ obserwujemy integrację tradycyjnych analiz laboratoryjnych z danymi uzyskanymi z czujników zainstalowanych w maszynach i urządzeniach oraz podłączonych do sieci Przemysłowego Internetu Rzeczy (IIoT). W przyszłości analiza oleju może nie służyć wyłącznie do oceny stanu środka smarnego lub stanu technicznego określonego komponentu maszyny, ale odgrywać integralną rolę w optymalizacji procesów produkcyjnych i zdalnym monitorowaniu zakładów przemysłowych.
Sieć IIoT umożliwia wzajemne połączenie czujników, siłowników i innych urządzeń, co prowadzi do szybszego udostępniania i analizowania danych. Celem tej sieci jest usprawnienie procesów produkcyjnych i przemysłowych.
Dr Deepak zgadza się z tym i idzie dalej, wskazując, że technologię IIoT można połączyć z koncepcją Przemysłu 4.0, która obejmuje wykorzystanie sztucznej inteligencji, aby umożliwić maszynom używanym w zakładzie produkcyjnym współdziałanie za pośrednictwem sieci bezprzewodowej i czujników w celu optymalizacji procesu produkcyjnego.
Przemysł 4.0 zrewolucjonizuje branżę monitorowania stanu środków smarnych. Technologia IIoT wraz ze wspierającymi ją czujnikami, technologia rzeczywistości mieszanej (MR), wykorzystywana do wizualizacji danych oraz technologia uczenia maszynowego (ML), wykorzystywana do analityki Big Data – wszystko to pomoże w tworzeniu cyfrowych bliźniaków środków smarnych stosowanych w maszynach i innych urządzeniach. Te cyfrowe bliźniaki reprezentują warunki smarowania w maszynach, do których można uzyskać zdalny dostęp w celu optymalizacji ich wydajności. Przemysł 4.0 przekształci konwencjonalne modele biznesowe. Na przykład czas bezawaryjnej pracy maszyn stanie się propozycją wartości oferowaną przez firmy związane z monitorowaniem stanu technicznego.
Aaron Mendez jest optymistą co do przyszłości monitorowania stanu środków smarnych. Ponieważ globalny przemysł środków smarnych przeznacza dużo czasu i pieniędzy na konserwację korygującą i repozycjonowanie środków smarnych, przyszłość rysuje się w bardzo jasnych barwach, jeśli chodzi o poprawę w kierunku obiektywności, precyzji i wydajności metod monitorowania ich stanu.
Jak mówi Allison Toms: Ogólnie rzecz biorąc, przemysł chciałby mieć więcej czujników zainstalowanych na sprzęcie do monitorowania stanu środków smarnych i maszyn. Analiza zanieczyszczeń metalicznych w olejach smarnych z wykorzystaniem czujników na sprzęcie (inline) jest dostępna od ponad 25 lat, co oznacza ponad 500 milionów godzin pracy smarowanych urządzeń w lotnictwie, energetyce, turbinach wiatrowych i żegludze.
Klienci korzystający z indukcyjnych czujników opiłków metali w oleju chcieliby posiadać czujniki monitorujące stan środków smarnych w jednym pakiecie, aby wyeliminować konieczność ręcznego pobierania próbek stanu oleju. Jednak trudno jest znaleźć niezawodny, powtarzalny czujnik stanu środka smarnego, który może monitorować wszystkie parametry środka smarnego, istotne dla różnych aplikacji.
Zwykle czujniki stanu/zanieczyszczenia środka smarnego wykrywają jeden parametr (woda, paliwo, degradacja, lepkość, liczba cząstek stałych/czystość itp.), podczas gdy wymagana jest większa liczba parametrów stanu i zanieczyszczenia oleju. Prawdopodobnie konieczne jest zastosowanie wielu czujników stanu środka smarnego. Ponadto czujniki często wymagają czyszczenia i/lub wymiany elementów. Nad tym zagadnieniem pracuje wiele zespołów badawczych.
Greg Poley uważa, że przyszłość analizy płynów oraz monitorowania stanu środków smarnych i maszyn jest bardzo obiecująca.
Oprzyrządowanie badawcze nadal czyni wielkie postępy w zakresie analizy wykonywanej na miejscu, umożliwiając użytkownikom szybszy dostęp do danych w celu poprawy terminowości ostrzeżeń i zachęcenia do zaangażowania personelu utrzymania ruchu w doradztwo co do konstrukcji urządzeń. Innym zmniejszonym problemem jest to, że udoskonalone techniki testowania doprowadziły do zmniejszenia wielkości próbek, co prowadzi do zmniejszenia ilości substancji chemicznych, wykorzystywanych do analiz. Analizy płynów przeprowadzane na miejscu mogą teraz szybko pomóc w weryfikacji alarmu z czujnika w ciągu najwyżej kilku godzin w zależności od logistyki instalacji, w porównaniu z czasami, kiedy testy były przeprowadzane w laboratorium poza zakładem.
Greg Poley przewiduje, że ostatecznie instalacje analityczne, znajdujące się w zakładach przemysłowych, przyspieszą przejście do możliwości monitorowania stanu zasobów (asset condition monitoring ACM) w czasie rzeczywistym tylko za pomocą czujników, co jest obecnie bardzo trudne.
Inteligentni agenci, czyli programy komputerowe oparte na sztucznej inteligenci, są już wykorzystywani. Istnieje nawet kilka wyspecjalizowanych programów, będących głównymi ewaluatorami danych ze względu na ogromną złożoność procesu ewaluacji w XXI wieku. Dane będą coraz bardziej zróżnicowane i coraz liczniejsze, gdy połączy się wiele dziedzin monitorowania stanu (zwłaszcza gdy w grę wchodzą czujniki). Sztuczna inteligencja będzie potrzebna, aby zapewnić zdolność adaptacji wymaganą do niezależnej oceny znaczenia wyników w celu natychmiastowego rozwiązywania złożonych problemów, z którymi borykają się układy smarowania.
Monitorowanie stanu zaczęło odgrywać ważną rolę w zapewnianiu, że środki smarne i maszyny będą mogły być nadal używane przez długi czas. Postęp technologiczny umożliwia użytkownikom rozpoczęcie pracy z technikami testowania online, a nawet przewidywanie przyszłego wykorzystania sztucznej inteligencji.
Te kroki jeszcze bardziej zwiększą dokładność, precyzję i szybkość, z jaką monitorowanie stanu może w przyszłości dostarczać użytkownikom istotnych informacji na temat ich układów smarowania i maszyn.
Neil Canter prowadzi własną firmę konsultingową Chemical Solutions w Willow Grove (stan Pensylwania). Jest redaktorem współpracującym w Stowarzyszeniu STLE, będącym partnerem medialnym CFE Media.
[1] należąca do Stowarzyszenia STLE.