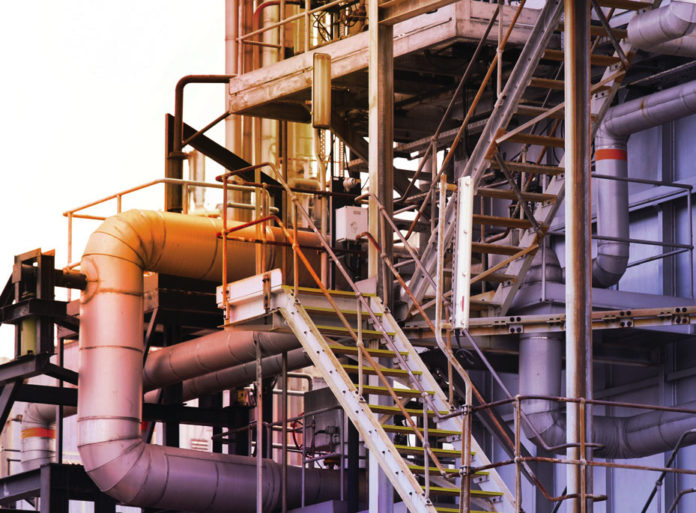
Metody zabezpieczania i naprawy wyposażenia zakładu
Bardzo gładkie i błyszczące, odporne na zużycie powłoki ceramiczne na bazie żywic epoksydowych zwiększają efektywność sprzętu oraz jego trwałość. Powłoki te mogą stanowić szybkie i niedrogie rozwiązanie problemu zużytych części, ponieważ chronione podzespoły są przywracane do użytku przy niewielkiej inwazyjności i w krótkim czasie.
Niezawodność i przewidywalność to główne czynniki, które decydują o sukcesie programu konserwacji sprzętu przemysłowego. W przypadku trudnych zastosowań przemysłowych planowa, prewencyjna obsługa techniczna sprzętu wydłuża trwałość i zmniejsza zużycie materiału dużych i małych elementów metalowych, takich jak mieszadła, pompy, obudowy, zbiorniki, rynny, rurociągi i wirówki. Te urządzenia przemysłowe są często narażone na działanie szlamu, osadów piasku, cząstek stałych i dużych kamieni, które mogą uszkodzić lub zetrzeć nawet najtwardsze, wzmacniane stalowe podłoże.
Niszczenie materiału warstwa po warstwie
Uszkodzenia komponentów mogą wystąpić na skutek czynników mechanicznych, chemicznych, korozji lub ich kombinacji. Czynnik mechaniczny oznacza działanie suchych cząstek lub szlamu przenoszonego przez rynny, rury, pompy i inne. Z biegiem czasu nawet płynne materiały mogą zetrzeć i zużyć twarde stopy metali, takie jak stal AR400. Z powodu osłabienia warstwy wierzchniej cienkie warstwy materiału są kolejno degradowane i usuwane, co powoduje zmniejszenie grubości podłoża oraz osłabienie materiału.
Czynniki chemiczne oraz korozja fizycznie zmieniają obiekt poprzez procesy chemiczne. Na przykład w procesie korozji – utleniania żelaza – powstaje bardzo słaba i luźna warstwa tlenków na materiale metalowym. Korozja może być skoncentrowana w jednym miejscu, formując wgłębienie lub szparę, albo też rozciągać się na znacznej powierzchni, jednorodnie ją utleniając. Jeżeli pozwoli się na rozwój aktywnej korozji znajdującej się pod powłoką zabezpieczającą, może ona spowodować osłabienie podłoża, w najgorszym wypadku skutkując krytycznym uszkodzeniem konstrukcji.
W przypadku czynników chemicznych agresywne związki chemiczne mogą być transportowane przez urządzenia metalowe i reagować z materiałem, niszcząc go warstwa po warstwie. Ponieważ uszkodzone warstwy są nieustannie usuwane z rodzimego podłoża, grubość i spójność materiałowa elementu metalowego stopniowo się zmniejszają.
W każdym zakładzie przemysłowym łatwo znaleźć przykłady takiego zużycia. Obudowy pomp i wirniki zużywają się na skutek przepływu ściernego szlamu i zanieczyszczeń, kawitacji i czynników chemicznych. Następnie zużywają się kolejne sekcje urządzenia. Kilka z popularnych obszarów podlegających zużyciu to miejsca mające kontakt ze strugą płynu o dużej prędkości, gniazda pierścieni, łopatki wirników i wnętrze obudowy pompy. W przypadku rur i przewodów większość oznak zużycia występuje w kolanach, gdzie struga płynu zmienia kierunek ruchu. Niektóre zakłady przemysłowe są zmuszone do wymiany kolan w przewodach nawet co trzy miesiące. Wpływa to na wzrost wydatków na materiał i koszty pracy. W kopalniach i kamieniołomach ruda żelaza może często ścierać łyżki wydobywcze przez ciągłe tarcie spowodowane kopaniem i wydobyciem.
W wielu zakładach przeprowadza się czynności konserwacyjne dużych elementów wyposażenia, gdy ich zużycie stanie się już bardzo widoczne lub gdy wystąpi poważna awaria, np. dziura w zsypie lub odpadające części komponentu. Gdy nastąpi usterka o znaczeniu krytycznym, sprzęt musi zostać wyłączony z uwagi na nieplanowaną, zwykle kosztowną i czasochłonną naprawę. Procedury konserwacji reaktywnej zmuszają fabrykę do wykonywania szybkich napraw, podczas których części są wzmacniane, łatane, odbudowywane lub wymieniane na nowe w celu szybkiego powrotu do pracy. Jeżeli części wrócą do działania bez jakiegokolwiek zabezpieczenia przed ponownym zużyciem, trwałość tego sprzętu będzie mniej przewidywalna, a szansa na pojawienie się nowej usterki krytycznej wzrośnie.
By zapewnić długotrwałą ochronę przed zużyciem, wytarciem, czynnikami chemicznymi i korozją oraz zminimalizować występowanie planowanych i nieplanowanych przestojów, należy na wrażliwą warstwę metalu zastosować powłoki zabezpieczające na bazie żywic epoksydowych, zawierające wypełniacze ceramiczne. Odnawialne powłoki dobrze odwzorowują powierzchnie, zachowując spójność materiału rodzimego, i zabezpieczają przed czynnikami mechanicznymi, chemicznymi, korozją na skutek działania cząstek ścierających materiał, szlamem i substancjami chemicznymi. Opracowane powłoki mogą być stosowane na zużyte części w celu ich odnowienia lub nanoszone na nowe części przed wdrożeniem ich do pracy.

Jak działa powłoka ochronna?
Powłoki te to dwuczęściowe środki epoksydowe, składające się z ceramicznych ziarenek lub pyłu i węglika krzemu. Polimer na bazie żywicy epoksydowej, który wiąże materiał ceramiczny z podłożem, jest tak zaprojektowany, by miał wysoką wytrzymałość, a przy tym doskonale zachowywał się pod wpływem ściskania i obciążeń udarowych. Powłoki te zastygają w temperaturze 13°C do 32°C, a czas wiązania zależy od masy i temperatury – im większa objętość, tym szybciej wiąże. Jest to spowodowane większą ilością ciepła wytwarzanego w reakcji egzotermicznej zastygającej żywicy. Wyższe temperatury podłoża i otoczenia również korzystnie wpłyną na czas wiązania.
Ponieważ materiał ceramiczny jest obojętny chemicznie, nie reaguje z większością materiałów mających kontakt z częściami metalowymi. Powłoka ceramiczna jest odporna na działanie agresywnych substancji i wytrzymuje temperatury do 230°C. Rozmiar materiału ceramicznego – pyłu lub ziarenek – użytego w powłoce ochronnej bezpośrednio odzwierciedla rozmiar cząstek, które w przyszłości będą oddziaływać na metalowe podzespoły. W przypadku dużych cząstek i kamieni specjaliści utrzymania ruchu powinni stosować jako wypełnienie największe dostępne ziarna ceramiczne. W przypadku płynnych ścieków i zawiesin drobne cząstki ceramiczne są wystarczające, by zapobiec zużyciu.
Zaprojektowane do różnych środowisk pracy powłoki ochronne można podzielić na siedem głównych kategorii:
→ masy wypełniające z ziarnami,
→ powłoki wysokotemperaturowe,
→ powłoki ultrawysokotemperaturowe,
→ szybkowiążące,
→ do nanoszenia pędzlem,
→ do nanoszenia metodą natryskową,
→ powłoki odporne na uderzenia.
Masy wypełniające to gęste pasty przeznaczone do nakładania kielnią lub ręką w rękawiczce na powierzchnie znajdujące się w zasięgu ręki człowieka. Powłoka ta jest odporna na zużycie na skutek działania drobnych i większych cząstek w takich miejscach, jak kolana, cyklony i inne obszary, gdzie transportowany płyn zmienia kierunek przepływu i powoduje powstanie turbulencji. Różne rozmiary ziaren wypełniających wraz z różnymi rodzajami mas wypełniających zapewniają odpowiednią wytrzymałość i twardość, co pozwala na zabezpieczenie powierzchni przed zużyciem spowodowanym transportowanymi płynami lub ciałami stałymi.
Powłoki wysokotemperaturowe są odporne na działanie temperatury do 175°C. Powłoki ultrawysokotemperaturowe mają odporność na temperatury do 230°C. Często stosowane są w piecach, systemach transportujących gorącą wodę lub ścieki. Te powłoki ochronne stosowane są często do zabezpieczania podłoża przed czynnikami chemicznymi o podwyższonej temperaturze.
Powłoki szybkowiążące są stosowane wówczas, gdy naprawiane urządzenie musi szybko wrócić do pracy na linii produkcyjnej. Powłoki te osiągają pełną wytrzymałość mechaniczną już po 3 godzinach od aplikacji.
Powłoki przeznaczone do nanoszenia pędzlem to substancje samopoziomujące. Mają niską lepkość i łatwo się rozprowadzają, dzięki czemu mogą być nanoszone wałkiem lub pędzlem albo po prostu wylane na podłoże, pokrywając wyznaczony obszar. Powłoki te mają od 3 do 6 mm grubości i najlepiej się sprawdzają przy podłożach do transportu szlamu zawierającego bardzo drobne cząstki, takie jak piach, opiłki metalu, skrawki czy nasiona. Powłoka ta może być łatwo naniesiona na obszar w zasięgu ręki człowieka, taki jak wnętrze rury, zmniejszy też tarcie spowodowane przepływającym czynnikiem, np. w pompie cieczy.
Powłoki do nanoszenia metodą natryskową to substancje o niskiej lepkości, podobne do tych przeznaczonych do nanoszenia pędzlem. Cechują się jednak mniejszą grubością – 0,5 mm. Jeśli powłoka zostanie napylona za pomocą pistoletu z dostawką atomizującą, to bardzo cienkie pokrycie może zostać zastosowane do dużych i trudno dostępnych powierzchni, skomplikowanych kształtów oraz elementów o małej średnicy, jak zakrzywione elementy lub kolana. Z powodu cienkiej warstwy powłoki te nie powinny być narażone na działanie dużych turbulencji lub uderzeń udarowych.
Powłoki odporne na uderzenia to specjalne materiały opracowane po to, by pochłaniać energię uderzenia i wykazywać odporność na uszkodzenia spowodowane kamieniami, węglem i innymi substancjami spadającymi lub w inny sposób oddziałującymi na podłoże. Materiały te są często stosowane do zabezpieczania zsypów na końcu transporterów w przemyśle wydobywczym i na budowach.

Przygotowanie powierzchni i sposób zastosowania
Powierzchnia metalu musi zostać wysuszona i oczyszczona przed nałożeniem powłoki. Specjaliści utrzymania ruchu powinni usunąć korozję, chemikalia, zabrudzenia, rdzę, lakier i pozostałości starej powierzchni za pomocą środków ściernych, szlifierek, piaskowania lub innych technik czyszczenia. Powierzchnię należy w końcowym etapie czyszczenia odtłuścić za pomocą alkoholu, zanim zostanie położona nowa powłoka.
By związać powłokę ochronną z bardzo zniszczoną powierzchnią lub w celu wypełnienia sporych przestrzeni, podłoże można pokryć metalową siatką działającą niczym zbrojenie wzmacniające wytrzymałość powłoki. Następnie na siatkę nakłada się powłokę. By uniknąć adhezji przy nakładaniu powłoki na dużą powierzchnię, miejsca, w których powłoka nie jest potrzebna, należy maskować środkami smarnymi lub smarem do form. W tych punktach powłoka będzie łatwo usuwalna, ponieważ nie zwiąże się z materiałem podłoża.
Po oczyszczeniu powierzchni należy zwiększyć jej porowatość ze względu na lepszą adhezję powłoki. Piaskowanie za pomocą granulek tlenku aluminium lub węglika krzemu zapewni powierzchni odpowiednią chropowatość. Podobny efekt można uzyskać za pomocą wysokociśnieniowego natrysku wodą ze ścierniwem. Powierzchnia może również zostać potraktowana pneumatycznym młotkiem igłowym lub zgrubnym papierem ściernym o gradacji 60 lub mniejszej. Użycie papieru ściernego akceptowalne jest tylko w przypadku, gdy pierwsze dwie metody nie mogą zostać zastosowane. Po poprawie przyczepności podłoża jest ono ponownie czyszczone za pomocą środków czyszczących i odtłuszczających, a naprawa powierzchni powinna nastąpić szybko, by nie rozpoczął się proces korozji.
Powłoki są dostępne w różnych kolorach, co daje możliwość wizualnej oceny ich zużycia i określenia momentu ich ponownej aplikacji. Jeśli pierwsza powłoka zaczyna się zużywać, odsłoni się kolor niższej warstwy, wskazując, że należy rozważyć nałożenie kolejnej warstwy.
Zbiorniki cylindryczne w wirówkach dekantacyjnych
Wirówki dekantacyjne mają zbiorniki cylindryczne wyposażone w otwory na wejściu i wyjściu do zbiornika. Zbiornik po stronie zewnętrznej jest często narażony na działanie agresywnych środków chemicznych. Zastosowanie powłoki odpornej na zużycie zabezpieczy go i pozwoli ograniczyć częstotliwość jego wymiany.
By zastosować powłokę, zbiornik musi być najpierw wypiaskowany w celu usunięcia rdzy i zanieczyszczeń oraz stworzenia nierównego profilu powierzchni. Tak przygotowany profil powierzchni pozytywnie wpływa na adhezję, zwiększając pole powierzchni na styku komponentów, a także zwiększa siłę wiązania powłoki z podłożem.
Profil powierzchni może się różnić w zależności od typu cząstek oddziałujących na podłoże, rodzaju części i wykorzystywanej techniki. Bardzo ważne jest uzyskanie profilu o głębokości odpowiedniej do danej powłoki. Nieodpowiednia kontrola jakości i brak wytycznych dotyczących stosowania materiałów o dużych cząstkach w przypadku cienkich powłok może prowadzić do powstawania pęknięć powierzchni.
Po obróbce powierzchni zbiornika i jego oczyszczeniu za pomocą środków przemysłowych, takich jak silny alkohol izopropylowy, zewnętrzna część zbiornika pokrywana jest za pomocą pędzla odporną chemicznie powłoką ceramiczną. W miejscach, w których zbiornik narażony jest zarówno na czynniki chemiczne, jak i ścieranie mechaniczne, użycie powłoki ceramicznej na bazie żywicy epoksydowej zwiększy trwałość zbiornika i wydajność jego pracy.
W przypadku dużych gabarytów zbiornika lub trudno dostępnych kształtów, gdzie ręczne nakładanie masy epoksydowej jest niemożliwe, stosuje się powłoki nakładane natryskowo. Nie zawierają one rozpuszczalników i mają niewielkie ilości lotnych związków organicznych (VOC). Zapewniają gładką i równą powierzchnię. W przypadku wirówki powłoka ceramiczna nakładana metodą natryskową znajdzie zastosowanie jako pokrycie innej powłoki ochronnej na bazie żywicy epoksydowej, co zapewni uzyskanie powierzchni o niskim współczynniku tarcia.

Obudowy pomp i wirniki
Pompy przemysłowe znajdują się praktycznie w każdym zakładzie. Usuwają wodę, ścieki i inne płyny, transportując je w inne miejsce.
Płyny w zbiornikach znajdujących się w hutach żelaza zawierają pewną ilość osadu. Gdy płyn jest wypompowywany ze zbiornika, część osadów transportowanych przez pompę przywiera do jej komponentów, takich jak obudowa, gniazda, łopatki i część robocza. Warstwa osadu z czasem się zwiększa, a przerwa między obudową pompy a wirnikiem staje się coraz mniejsza. Przerwa ta jest ważna z punktu widzenia efektywności działania pompy. Efektywność spada wraz z rozmiarem przerwy. Tarcie spowodowane szlamem zawierającym osad z czasem zużywa wnętrze pompy i powoduje zniszczenie obudowy i wirnika. Bez stosowania technik serwisowych polegających na usuwaniu osadu i kontroli zużycia pompa ulegnie awarii.
Zastosowanie powłoki ceramicznej nakładanej za pomocą pędzla na wewnętrzne komponenty pompy zapewni ochronę części przed zniszczeniem poprzez:
→ zmniejszenie współczynnika tarcia i ułatwienie osadom przemieszczania się po obudowie i wirniku bez przywierania,
→ zapewnienie powłoki chroniącej przed zużyciem i ścieraniem spowodowanym tarciem i przepływem,
→ ochronę części odlewanych przed agresywnymi środkami chemicznymi, które mogą reagować z podłożem. Baza epoksydowa i wypełnienie ceramiczne są obojętne chemicznie i bardzo wytrzymałe na działanie czynników chemicznych.
Powłoki ceramiczne sprawiają, że zużycie staje się przewidywalne, dzięki czemu znacznie wydłużają trwałość pomp i zmniejszają ryzyko wystąpienia nieplanowanych czynności serwisowych. Powłoki te pozwalają na pracę pomp o dużych gabarytach z zaplanowaną trwałością i umożliwiają wykonywanie przeglądów technicznych zgodnie z harmonogramem. Poważne w skutkach awarie sprzętu bez pokrycia ochronnego często wymagają zaangażowania całego zespołu utrzymania ruchu, by pozyskać części zamienne, które mogą być kosztowne i trudno dostępne, co wydłuża przestój i zwiększa jego koszt.
Podsumowanie
Odporne na ścieranie powłoki ceramiczne na bazie żywic epoksydowych mogą być stosowane do ochrony delikatnych powierzchni metalowych, co w efekcie minimalizuje ryzyko zarówno planowanych, jak i nieplanowanych przestojów.
Dzięki bardziej przewidywalnemu zużyciu powłoki ceramiczne wpływają na zwiększenie trwałości pomp, zmniejszają ryzyko wystąpienia awarii i związanych z nią czynności serwisowych.
Powłoki ceramiczne zwiększają sprawność i trwałość sprzętu. Mogą stanowić szybkie i niedrogie rozwiązanie chroniące przed zużyciem, ponieważ metoda ta jest mało inwazyjna, a chronione części są szybko przywracane do użytku.
Rachel Nashett i J. Adam Lyman są inżynierami ds. wdrożeń w firmie Henkel.