W artykule opisujemy etapy działań, które należy podjąć, aby wdrożyć w zakładzie inteligentny system rozdziału obciążeń sprężarek pracujących w instalacji sprężonego powietrza, co przyniesie zwiększenie efektywności i zmniejszenie strat energii.
Dla dyrektora zakładu przemysłowego, któremu zlecono zadanie zmniejszenia kosztów zużywanej energii oraz zminimalizowania śladu węglowego swojego zakładu, najlepszym rozwiązaniem będzie prawdopodobnie zajęcie się instalacją pneumatyczną. W pierwszej kolejności należy ustalić, czy ta instalacja wykorzystuje częściowo, czy całkowicie sprężarki odśrodkowe.
Wdrożenie w instalacji sprężonego powietrza systemu sterowania rozdziałem obciążeń poszczególnych kompresorów może zasadniczo zmniejszyć zużycie energii przez te urządzenia oraz zredukować tym ślad węglowy zakładu. Dla zmaksymalizowania potencjalnego zwrotu z inwestycji (ROI) w system sterowania rozdziałem obciążeń kluczowe jest zajęcie się zarówno stroną zasilania, jak i odbioru instalacji sprężonego powietrza. Tak więc należy rozpocząć działania od przeglądu instalacji w zakładzie. Wyznaczony kierownik projektu powinien sporządzić listę celów i oczekiwań tego audytu oraz udostępnić ją audytorowi z firmy zewnętrznej, specjalizującej się w systemach sprężonego powietrza.
Istnieje wiele firm przeprowadzających audyty energetyczne dla całego zakładu. Podczas gdy firmy te mogą wykonać akceptowalny audyt strony zasilania systemu (ang. supply side – sprężarki, elementy przygotowania sprężonego powietrza i zbiorniki), to specjalista od audytów instalacji pneumatycznych zwykle przeprowadza dokładną analizę strony odbiorczej (ang. demand side – rury, zbiorniki wtórne oraz urządzenia zasilane sprężonym powietrzem). Najprawdopodobniej zna on najnowsze rozwiązania w dziedzinie sterowania wytwarzaniem sprężonego powietrza. Te dodatkowe informacje mają znaczenie, ponieważ układy sterujące są kluczową częścią planu modernizacji systemu pneumatycznego w kategoriach zwiększenia wydajności oraz oszczędności energii.
Niniejszy artykuł opisuje i wyjaśnia kolejne etapy działań, które należy wykonać, aby wdrożyć inteligentny system sterowania rozdziałem obciążeń w instalacji sprężonego powietrza, nadający się dla zakładów posiadających wiele sprężarek odśrodkowych.
Wytyczne i zalecenia
- Ustalenie celów oraz oczekiwań dla audytu instalacji sprężonego powietrza.
- Zebranie danych i wpisanie do arkusza programu Excel wraz z raportem końcowym dla celów recenzji wewnętrznych. Dane powinny być odczytywane nie rzadziej niż co 15 sekund i uśrednione dla przedziałów czasowych jednominutowych.
- W przypadku większych systemów, szczególnie z wieloma sprężarkami odśrodkowymi, zaleca się użycie przepływomierzy sprężonego powietrza do pomiarów na orurowaniu oraz mierników energii do pomiarów na kompresorach.
- Uzyskanie histogramów pokazujących procentowy czas pracy sprężarek przy różnych wydajnościach i mocach na podstawie danych z okresu co najmniej jednego tygodnia.
- Dokładne oczyszczenie sprzętu, aby uniknąć spadków ciśnienia na osuszaczach i filtrach. Jeśli stosowane są osuszacze adsorpcyjne, należy sprawdzić, czy wartość ciśnienia oczyszczania jest nastawiona według zaleceń producenta i ewentualnie ją skorygować. Sprawdzenie, czy został osiągnięty punkt rosy dla wymaganego ciśnienia roboczego za pomocą panelu sterowania osuszacza lub przenośnego monitora punktu rosy, zainstalowanego tuż za osuszaczem.
- Kolejny punkt sprawdzenia strony zasilania instalacji to sprzęt pneumatyczny, który tworzy dynamiczny spadek ciśnienia w systemie, taki jak szybkie zawory elektromagnetyczne. Należy zastosować czujniki ciśnienia, które potrafią zapisywać dane pokazujące wpływ tych komponentów wytwarzania sprężonego powietrza na cały system.
- Identyfikacja okazji do zwiększenia wydajności systemu za pomocą zainstalowania zbiorników magazynujących sprężone powietrze. Mogą one znajdować się w kompresorowni lub w zakładzie – po stronie odbiorników.
- Przeprowadzenie testów nieszczelności instalacji sprężonego powietrza w całym zakładzie. Testy te powinny pokazać zarówno miejsca, jak i wielkość wycieków. Oszacowanie zwrotu z inwestycji na podstawie porównania kosztów napraw z potencjalnymi oszczędnościami.
- Identyfikacja aplikacji, w których sprężone powietrze nie jest wykorzystywane prawidłowo. Przykładem jest tu przedmuchiwanie powietrzem przy maksymalnym ciśnieniu. Bardziej efektywnymi rozwiązaniami są tu dysze niskiego ciśnienia ze wzmacniaczami oraz dmuchawy niskiego ciśnienia.
- Zaznajomienie się z różnymi typami sterowników kompresorów sprężonego powietrza.
- Rozpoczęcie prac od kompresorów, które obecnie pracują w fabryce.
- W wielu przypadkach rekomendacje podane w raporcie z audytu mogą obejmować zainstalowanie nowego kompresora lub grupy kompresorów, tak więc należy poświęcić czas na zaznajomienie się z metodami sterowania, które różnią się od tych, z jakimi mamy doświadczenie.
- Zebranie danych na temat poboru mocy przez sprężarki śrubowe bez obciążenia oraz punktów upuszczania ciśnienia w sprężarkach odśrodkowych. Charakterystyki sterowania dla różnych koncepcji pokazują najlepiej zależność mocy sprężarki od jej obciążenia.
- Zaznajomienie się ze zjawiskiem tzw. dziur regulacyjnych (opis w dalszej części artykułu). Wymaga to znajomości istniejących lub przyszłych układów sterowania kompresorami oraz ich wpływu na możliwości zmniejszenia zużycia czy marnowania energii na podstawie profilu przepływu (histogram czas – wydajność).
- Ocena projektów technicznych sterowania rozdziałem obciążeń dla instalacji albo systemów z wieloma sprężarkami odśrodkowymi lub zawierających sprężarki odśrodkowe i śrubowe.
- Strategie ograniczania ciśnienia (ang. pressure bumping) – punkty nastaw poszczególnych sprężarek odśrodkowych są wymuszane w celu utrzymywania pracy w pożądanym zakresie wydajności. Przedziały ograniczania ciśnienia zwykle wynoszą poniżej 1 psig (0,069 bar), typowo od 0,25 do 0,50 psig (0,017–0,034 bar). Takie sterowanie utrzymuje wszystkie kompresory w stanie pracy w pożądanym zakresie wydajności, zanim w którymkolwiek z nich zacznie działać zawór upustowy.
- Sterowanie kierownicą wlotową (inlet guide vane, IGV) oraz zaworem upustowym (blowoff valve, BOV). Sterownik lokalnej sprężarki wymusza takie położenia zaworów, że maszyna pracuje w pożądanym zakresie, wyłączając wszystkie jednostki, zanim którakolwiek zacznie upuszczać nadmiar ciśnienia powietrza. Niektóre firmy oferujące ten typ sterowania wymagają, aby ich sterownik sprężarki był instalowany na maszynie. Inne mogą dostarczać osobny interfejs do montażu na ścianie, który integruje sterowanie pracą wszystkich sprężarek.
- Kształtowanie obciążenia. Zbiorniki o dużych objętościach oraz w wielu przypadkach zwiększające ciśnienie dostarczają powietrze o znacznie wyższym ciśnieniu niż ciśnienie robocze w fabryce. W takim układzie znajdują się wzmacniacze ciśnienia o małej mocy oraz zawory sterujące przepływem, które redukują ciśnienie powietrza wypływającego ze zbiorników wysokociśnieniowych. Zwykle znajduje się tam kompresor (lub kompresory) dopasowujący wydajność instalacji do aktualnego zapotrzebowania (ang. trim compressor). Działanie logiki sterującej polega na takim uderzeniu ciśnień roboczych kompresorów, aby utrzymywać je w pożądanym zakresie pracy, gdy jest to konieczne.
- Prawidłowe dobranie przekrojów rur instalacji sprężonego powietrza w celu zminimalizowania spadków ciśnienia.
- Rozważenie zainstalowania sprzętu do ciągłego monitorowania wydajności oraz mocy sprężarek po zakończeniu audytu.
- Opracowanie planu na przyszłość. Czy oczekiwane zapotrzebowanie systemu na sprężone powietrze w przewidywalnej przyszłości wzrośnie, czy zmaleje?
Technologie sterowania sprężarkami odśrodkowymi
Sprężarki odśrodkowe wykorzystują sprężanie dynamiczne, zamieniając energię kinetyczną na energię ciśnienia. Zarówno warunki otoczenia, jak i temperatura wody chłodzącej mają wpływ na wydajność oraz sprawność tych urządzeń. Jeżeli końcowy raport z audytu zawiera zalecenia dotyczące charakterystyk pracy, należy zawsze wymagać, aby krzywe odzwierciedlały wydajność w standardowych stopach sześciennych na minutę (scfm; 0,028 m3/min) przy ciśnieniu 14,7 psia (1 bar), w temperaturze 60°F (15,6°C) oraz suchym powietrzu (wilgotność względna 0%). Jest to ważne przy poszukiwaniu dziur regulacyjnych.
Eliminacja upustów ciśnienia powietrza jest sprawą kluczową dla maksymalizacji wydajności systemu ze sprężarkami odśrodkowymi. Często jest to jedyna możliwość zmniejszenia zużycia energii.
Rys. 1 przedstawia standardową charakterystykę pracy sprężarki odśrodkowej wraz z linią ciśnienia, linią pracy niestatecznej (linią graniczną pompażu; ang. compressor surge line), przepływem wymaganym, przepływem maksymalnym, położeniami kierownicy wlotowej IGV oraz zakresem regulacji wydajności (ang. turndown). Linia ciśnienia oznacza ciśnienie robocze, wydajność wymagana oznacza przewidywaną wymaganą wydajność, wydajność maksymalna to szczytowa wydajność uzyskiwana przez sprężarkę przy ciśnieniu roboczym, natomiast linia pracy niestatecznej (pompażu) oznacza naturalny skok urządzenia przy ciśnieniu roboczym. Pompaż występuje w punkcie charakterystyki, w którym krzywa pracy niestatecznej przecina się z linią ciśnienia. Należy go unikać, ponieważ w tym punkcie sprężone powietrze odwraca kierunek przepływu, co może uszkodzić kompresor. Kolorowe krzywe pokazują położenie kierownicy wlotowej w zależności od kąta – przy 90° jest całkowicie zamknięta, przy 45° otwarta w połowie, natomiast przy 0° całkowicie otwarta. Wydajność minimalna to punkt, w którym linia pompażu przecina linię ciśnienia. W pokazanym przypadku występuje to przy wydajności 2500 scfm (70,792 m3/min) oraz ciśnieniu 120 psig (8,27 bar).

Podczas uruchamiania konfiguruje się linię sterowania w celu zabezpieczenia kompresora przed pompażem. Kierownica wlotowa zamyka dopływ powietrza, gdy ciśnienie wzrasta (wydajność sprężarki się zmniejsza). Gdy sprężarka osiągnie maksymalną wydajność, zawór upustowy zacznie się otwierać w celu zabezpieczenia kompresora przed pompażem.
Na Rys. 2 pokazano nowy punkt otwarcia zaworu upływowego, uzyskany podczas uruchamiania sprężarki w zakładzie. Jest to punkt przecięcia się czerwonej linii przerywanej (linii sterowania tuż poniżej linii granicy pompażu) z linią ciśnienia. Zwykle ustawia się linię sterowania 5–8% poniżej linii granicy pompażu. Natomiast uzyskany w zakładzie procentowy zakres regulacji wydajności oraz wydajność, przy której otwiera się zawór upustowy, będą mniejsze od pokazanych na standardowej krzywej wydajności. Ustawiony w zakładzie punkt otwarcia zaworu upustowego ma teraz współrzędne: 2650 scfm (75,040 m3/min) i 120 psig (8,27 bar).

Sterowanie sprężarkami śrubowymi
Sprężarki śrubowe olejowe mają możliwość stosowania czterech typów sterowania: modulację wlotową, zmianę geometrii (nazywaną też wyporem zmiennym), dociążanie/odciążanie oraz napęd elektryczny o zmiennej częstotliwości (VFD lub napęd o zmiennej prędkości VSD). W sprężarkach śrubowych bezolejowych możliwe są tylko dwa rodzaje regulacji: dociążanie/odciążanie oraz napęd VFD (VSD). Zauważmy, że charakterystyka sprężarki zmiennoobrotowej VSD jest oparta na wykorzystaniu silnika elektrycznego z napędem o zmiennej częstotliwości VFD (silnika indukcyjnego z napędem VFD – falownikiem/inwerterem).
Rys. 3 pokazuje różne metody sterowania w warunkach idealnych na wykresie zależności mocy względnej w procentach (oś pionowa) od obciążenia względnego w procentach (oś pozioma).
Każdy system pneumatyczny ma swoją unikalną charakterystykę pracy, tak więc wykresy pokazane na Rys. 3 mogą nie odzwierciedlać rzeczywistych, spotykanych w praktyce. Na wydajność sprężarki mają wpływ cechy konstrukcyjne systemu pneumatycznego. Takie czynniki jak objętość zbiornika sprężonego powietrza, objętość rur instalacyjnych, zakres ciśnień roboczych, liczba sprężarek oraz zdarzenia związane z przepływem sprężonego powietrza, które powodują nagłe spadki ciśnienia w systemie – wszystko to może mieć wpływ na wydajność systemu pneumatycznego. Krzywa VSD pokazuje liniową zależność pomiędzy obciążeniem procentowym a mocą procentową. Wynika to z tego, że sprężarka jest wyłączana i pozostaje w trybie oczekiwania przy obciążeniach poniżej swojej znamionowej wydajności minimalnej.
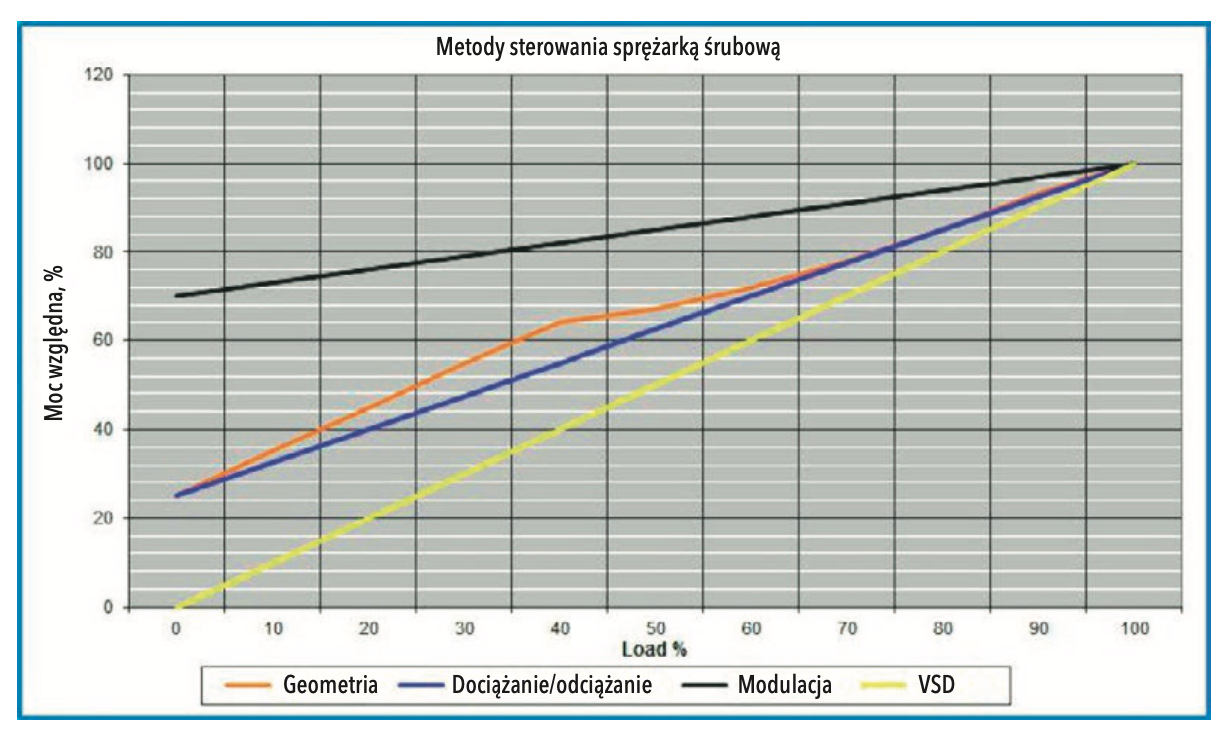
Zjawisko dziur regulacyjnych
Zjawisko dziur regulacyjnych (ang. control gaps) istnieje w niemal każdej instalacji sprężonego powietrza. Dziura regulacyjna to taki obszar, w którym zapotrzebowanie na sprężone powietrze jest zbyt małe dla kompresora dopasowującego (trim compressor), aby pracował on bez upuszczania nadmiaru ciśnienia, a jednocześnie zbyt duże, aby kompresor ten rozładował nadmiar ciśnienia i się wyłączył. Dziury regulacyjne występują podczas pracy układu sprężarek na granicy wydajności sprężarki stałoobrotowej i zmiennoobrotowej. Eliminacja dziur regulacyjnych w instalacji sprężonego powietrza w zakładzie może być trudna. Ważne jest, aby zrozumieć, gdzie to zjawisko występuje i dlaczego. Zrozumienie jego natury umożliwi personelowi fabryki dobranie sprzętu na wymianę oraz dokonanie ulepszeń w instalacji, które mogą wyeliminować dziury regulacyjne.
W przypadku sprężarek odśrodkowych dziury regulacyjne są czasem trudniejsze do wyeliminowania niż w przypadku sprężarek śrubowych, szczególnie gdy wszystkie sprężarki w systemie posiadają podobne wydajności znamionowe. Wykorzystanie sprężarek o różnej wydajności oraz ciśnieniach roboczych może zredukować lub nawet wyeliminować dziury regulacyjne.
Pełne zrozumienie profilu wydajności oraz ciśnienia instalacji sprężonego powietrza w danej fabryce jest kluczem do rozwiązania tego problemu. Na Rys. 4 pokazano dziury regulacyjne w systemie, w którym pracują trzy sprężarki odśrodkowe. Jedno z tych urządzeń jest nowe i posiada zawór wlotowy z kierownicą IGV. Natomiast dwa pozostałe są starsze i wykorzystują zawory dolotowe motylkowe. Zakres regulacji wydajności sprężarki odśrodkowej wykorzystującej kierownicę IGV na dolocie jest znacznie szerszy niż sprężarek z dolotem motylkowym. Obszary A i B na wykresie pokazują dziury regulacyjne, gdy turbosprężarka #3 pracuje z upustem nadmiaru ciśnienia. Podano tam też wartości pojemności zbiornika, wymaganych do zmagazynowania powietrza przepływającego przy danej wydajności sprężarki i ciśnieniu powietrza w czasie 1 minuty. Pasmo ciśnienia w turbosprężarkach jest zwykle małe, a zatem objętość zbiornika, wymagana do pokrycia zapotrzebowania na sprężone powietrze w obszarze dziury regulacji wydajności w czasie zaledwie 1 minuty, jest na ogół duża, jak to zilustrowano na rysunku.

Rys. 5 przedstawia histogram ilustrujący profil zapotrzebowania systemu na sprężone powietrze w procentach czasu w różnych okienkach wydajności sprężarki. Histogramy takie są użyteczne przy identyfikacji dziur regulacyjnych, gdy sprężarki w instalacji oraz lokalne sterowniki nie są w stanie efektywnie realizować zapotrzebowania systemu na sprężone powietrze. Może to powodować niepotrzebne marnowanie wielkich ilości energii. Dokładna analiza profilu wydajności pozwala na poprawne dobranie parametrów nowych lub wymienianych sprężarek. Rys. 5 pokazuje wydajność od minimalnej do maksymalnej w okienkach o szerokości 300 cfm (8,495 m3/min).
Rys. 5 ilustruje częstotliwość upuszczania nadmiaru ciśnienia sprężonego powietrza (czerwone słupki) dla sprzętu wymienionego na Rys. 4. W obszarze dziury regulacyjnej A turbosprężarka #2 otwiera zawór upustowy przez 12,8% czasu. W obszarze dziury regulacyjnej B turbosprężarka #3 otwiera zawór upustowy przez 30,3% czasu. Ten system przy bieżącej konfiguracji wykonuje upuszczanie nadmiaru ciśnienia i zarazem marnuje energię przez 43,1% czasu pracy.
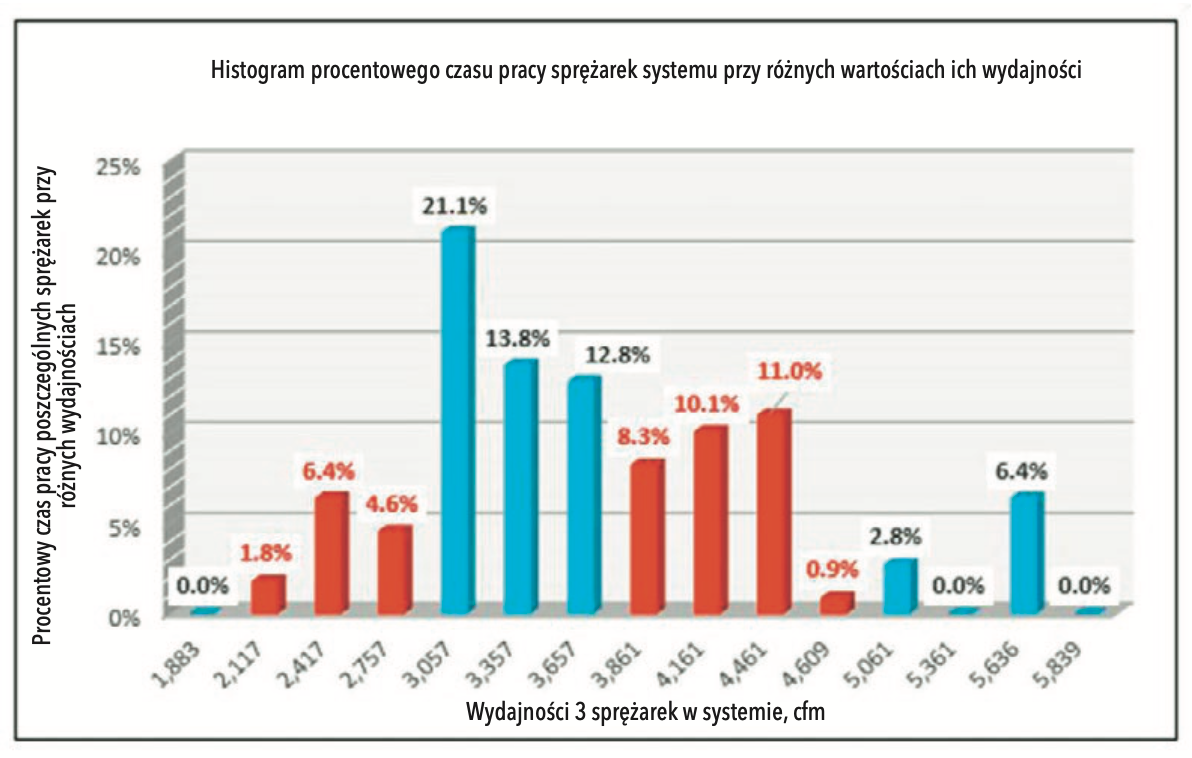
Rys. 6 pokazuje zakres regulacji w tym samym systemie z dwoma sprężarkami odśrodkowymi oraz jedną śrubową z regulacją typu włącz/wyłącz. Wykres ten pokazuje brak dziur regulacyjnych, jednak może to być czasem mylące. Sprężarka śrubowa może mieć większy interwał cyklu lub pracować bez obciążenia. Histogram na Rys. 5 pomoże w określeniu, czy sprężarka śrubowa o stałej prędkości obrotowej jest właściwym wyborem dla tego systemu.
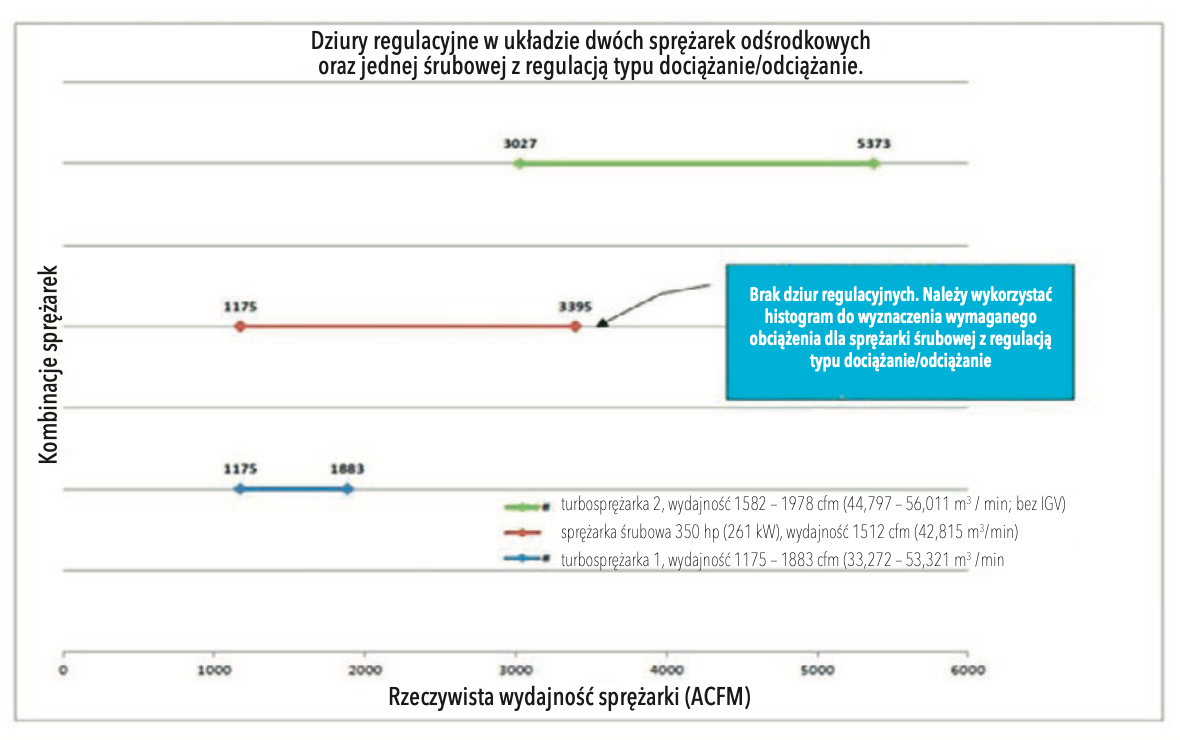
Rys. 7 pokazuje zakres regulacji w tym samym systemie z dwoma sprężarkami odśrodkowymi oraz jedną śrubową zmiennoobrotową (VSD). Wykres ten pokazuje brak dziur regulacyjnych, jednak może to być również mylące. Sprężarka śrubowa zmiennoobrotowa może pracować w trybie włącz/wyłącz, jeśli zapotrzebowanie sprężarki dopasowującej obciążenie jest poniżej minimalnej wydajności (prędkości obrotowej sprężarki). Układ sterowania sprężarki może wpływać na jej pracę w pobliżu minimalnej wydajności. Niektóre sprężarki śrubowe zmiennoobrotowe pracują w trybie dociążanie/odciążanie poniżej minimalnej wydajności, a zatem mają szerszy zakres wydajności, co powoduje zwiększenie sprawności. I znów użycie histogramu pokazującego czas pracy przy danej wydajność pomoże w określeniu, jaki typ sprężarki śrubowej zmiennoobrotowej będzie właściwym wyborem dla tego systemu.
Profil wydajności systemu pneumatycznego ma zasadniczy wpływ na dobór właściwego sprzętu, aby zredukować lub nawet wyeliminować dziury regulacyjne.
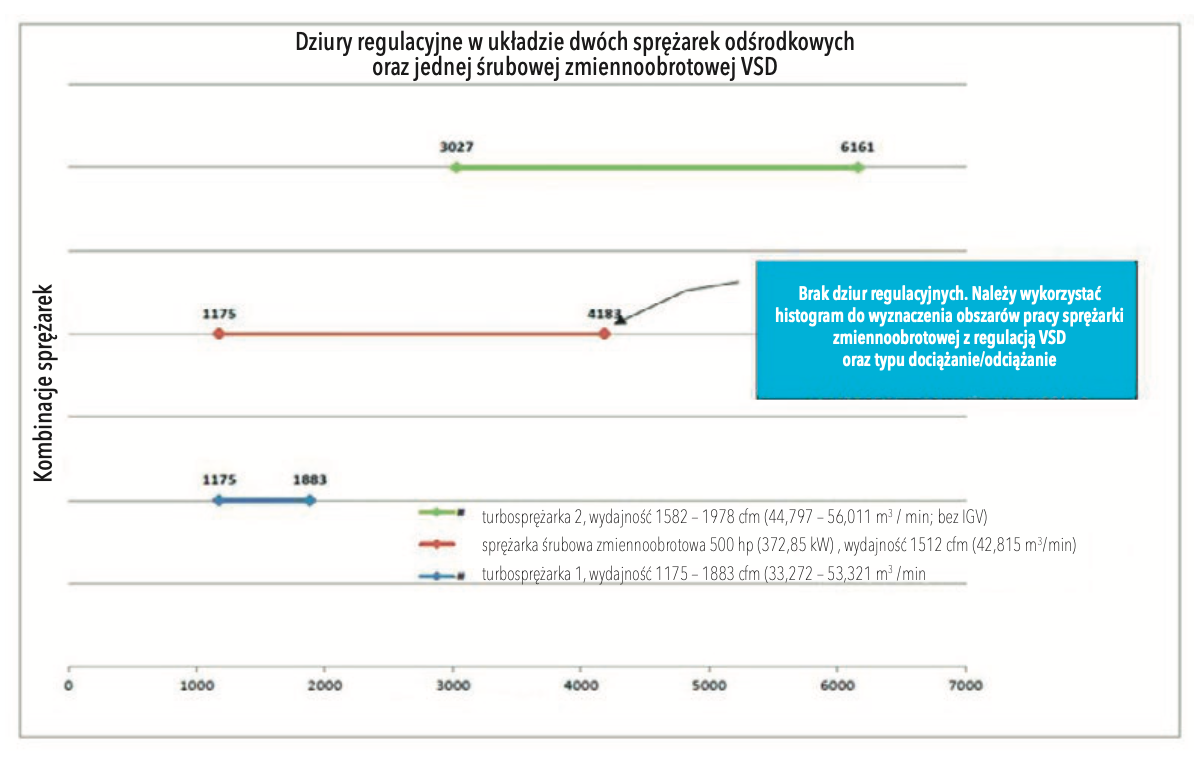
Zbiorniki ciśnieniowe do sprężonego powietrza
Zbiorniki ciśnieniowe do magazynowania sprężonego powietrza są często najbardziej ekonomiczną inwestycją dla systemu pneumatycznego. Co prawda na przykład instalacyjna rura 8-calowa (czyli o średnicy 203,2 mm) o długości 500 stóp (152,4 m) może sprawiać wrażenie, że ma dużą pojemność, jednak w rzeczywistości wynosi ona jedynie 1305 galonów (4,939 m3). Każdy system sprężonego powietrza jest unikalny, tak więc nie ma tu uniwersalnych zasad praktycznych. Na Rys. 8 pokazano objętości zbiorników w galonach odpowiadające różnym wymiarom rur o długości 1000 stóp (304,8 m). Z punktu widzenia wartości zbiorniki ciśnieniowe zapewniają znacznie lepszą wydajność systemu w porównaniu do takiego, który w kwestii magazynowania sprężonego powietrza opiera się tylko na pojemności rur i rozdzielaczy.
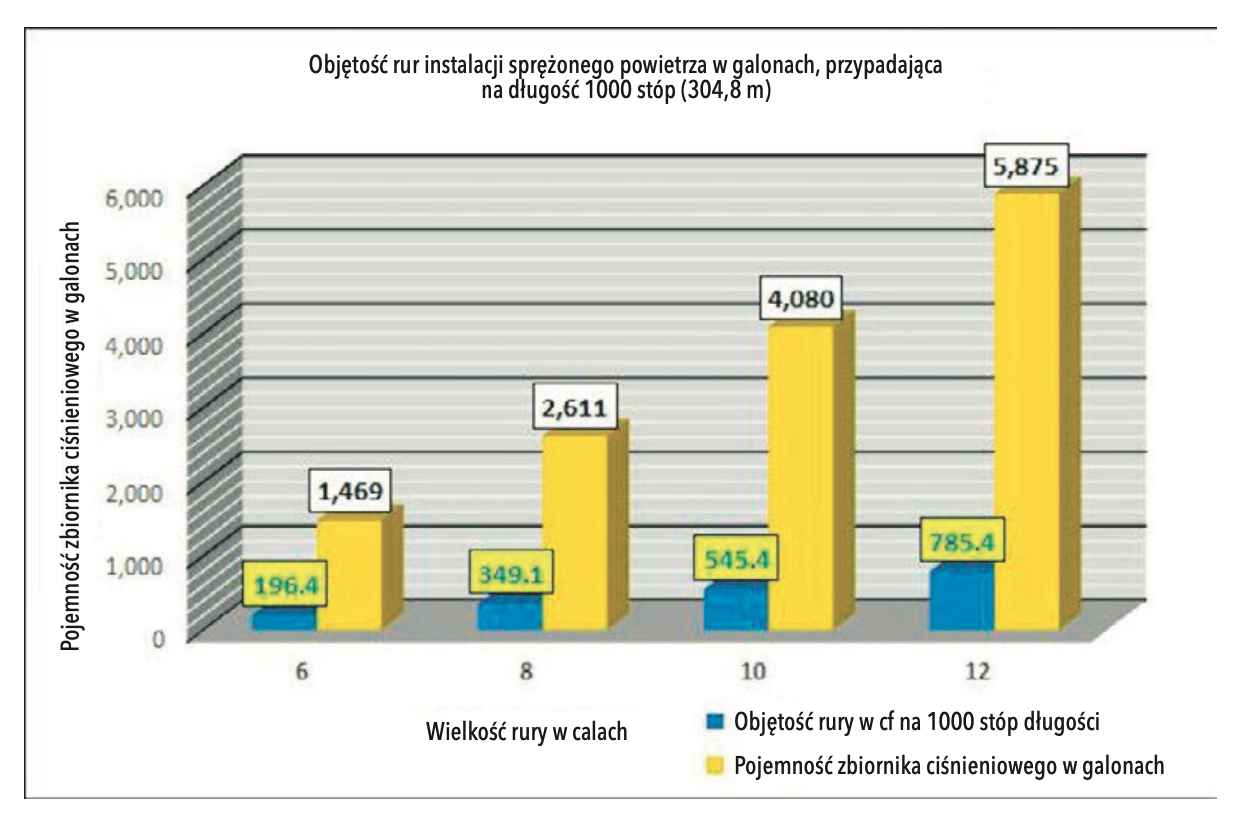
Podsumowanie
Wdrożenie systemu sterowania rozdziałem obciążeń sprężarek może drastycznie zwiększyć wydajność oraz niezawodność instalacji pneumatycznej posiadającej więcej niż jedną sprężarkę. Zainstalowanie sprzętu pomiarowego do ciągłego monitorowania i rejestrowania danych dotyczących pracy systemu pomoże w ocenie wydajności systemu, gdy warunki w zakładzie ulegają zmianie. Ustalenie wskaźników efektywności pozwoli na śledzenie negatywnych zmian w efektywności. Dysponując doświadczeniem, operatorzy będą mogli wykrywać nieefektywności po stronie zasilania i odbioru w instalacji sprężonego powietrza.
Uzyskanie zwrotu z inwestycji znajduje się w rękach kierownika projektu lub zespołu projektowego. Opracowanie listy działań oraz listy wymagań dla wdrożenia pozwoli na ustalenie realistycznych celów projektu. Dobrze przemyślany plan wyeliminuje zgadywanie oraz da kierownikowi projektu dane potrzebne do dokonania najlepszej inwestycji dla zakładu.
Christopher Nacrelli jest menedżerem ds. rozwoju biznesu w firmie Atlas Copco Compressors.