Systemy automatyki i ludzie mogą współpracować dzięki kulturze bezpieczeństwa przemysłowego, która kładzie nacisk na brak tolerancji wobec ryzyka i właściwe zrozumienie zasad inżynierii, takich jak stosowanie odpowiednich strategii i systemów zarządzania alarmami, procedur regulacyjnych i najlepszych praktyk branżowych.
W środowiskach przemysłowych zagrożenie bezpieczeństwa może wystąpić w każdej chwili i w każdym miejscu z powodu kombinacji wielu czynników. Awarie procesów mogą być wywołane niespodziewanie przez awarie sprzętu lub inne problemy. Jeśli sprzęt ulegnie awarii, a alarmy i znaki ostrzegawcze pozostaną niezauważone, potencjalne ryzyko może być ogromne. Zakład niezdolny do automatycznego utrzymania kontroli stanu ustalonego podczas normalnej pracy to wysokie prawdopodobieństwo wypadku. Zapobieganie zagrożeniom bezpieczeństwa zależy od skutecznej kontroli procesu i ludzi zarządzających operacjami. Oba te elementy muszą ze sobą płynnie współpracować, aby zakłady mogły bezpiecznie funkcjonować. W przypadku personelu przemysłowego zaczyna się to od zakorzenionego w kulturze korporacyjnej sposobu myślenia o bezpieczeństwie.
Budowanie kultury bezpieczeństwa
Kultura bezpieczeństwa wymaga wykorzystywania każdej okazji do podkreślania i wzmacniania postawy bezpieczeństwa – postawy cechującej się brakiem tolerancji wobec ryzyka, w której samozadowolenie nie jest naszym przyjacielem. Nikt nie chce być świadkiem tego, jak ktoś zostaje ranny, nikt nie chce doświadczyć negatywnego wpływu tego zdarzenia na produkcję, środowisko pracowników, stan zasobów i reputację zakładu. Najwyższym priorytetem jest zapewnienie bezpieczeństwa ludziom i otaczającym ich społecznościom. Bezpieczeństwo przemysłowe zaczyna się na poziomie korporacyjnym i obejmuje wszystkich pracowników. Oto elementy, które powinny być częścią polityki bezpieczeństwa w każdej firmie:
– Przekazywanie sobie wewnętrznych polityk i wdrażanie zabezpieczeń kontroli procesów oraz planów działania.
– Inwestowanie w szkolenia, naprawy i wymianę sprzętu.
– Postępowanie zgodnie z obowiązującym prawem i przepisami.
– Wykorzystanie standardów i wytycznych branżowych (np. IEC 61508 i IEC/ISA 61511).
Sięgając dalej w głąb kultury bezpieczeństwa, firmy powinny uwzględniać wstępną ocenę bezpieczeństwa i analizę ryzyka istniejących systemów automatyki i procesów w celu określenia tolerowanego i nietolerowanego ryzyka. „Tolerowane ryzyko” jest punktem odniesienia, który zakłady wykorzystują do określenia swojej względnej strategii bezpieczeństwa. Jest to ważne pojęcie, pozwalające zmniejszyć ryzyko odpowiedzialności. Jest to również doskonała okazja do przeglądu kluczowych obszarów w celu sprawdzenia, czy automatyka obiektu, systemy bezpieczeństwa i personel współpracują ze sobą w celu zapewnienia bezpiecznych i pewnych operacji.

Zautomatyzowane warstwy bezpieczeństwa
Efektywny, podstawowy system kontroli procesu (BPCS) jest najważniejszą z warstw ochrony (rys. 1). Posiada on zautomatyzowane warstwy bezpieczeństwa zaprojektowane w celu zapobiegania wypadkom. System BPCS prowadzi proces, identyfikuje sytuacje nietypowe i uruchamia alarm lub podejmuje inne działania. Powinien on być w stanie skompensować większość sytuacji nietypowych. Innym powszechnie stosowanym zabezpieczeniem jest przyrządowy system bezpieczeństwa (SIS), który musi interweniować, jeżeli proces wykracza poza bezpieczne granice kontrolne. Jeżeli BPCS starzeje się lub nie jest regularnie serwisowany, incydenty zaczynają się często nasilać, a znaczenie SIS staje się jeszcze większe. Gdy personel często polega na SIS w przypadku rutynowych zdarzeń i częste akcje systemu SIS stają się coraz bardziej zauważalne, nadszedł czas, aby przyjrzeć się dokładnie systemowi BPCS. W przypadku przeglądu systemu bezpieczeństwa przeprowadza się analizę zagrożeń procesowych (PHA)/badanie zagrożeń i operacyjności (HAZOP) lub inny audyt w celu określenia wszelkich pozostałych elementów bezpieczeństwa.
„Kultura świadomego bezpieczeństwa wymaga wykorzystania każdej okazji do podkreślenia i wzmocnienia postawy bezpieczeństwa – postawy cechującej się brakiem tolerancji dla ryzyka, w której samozadowolenie nie jest naszym przyjacielem.”
W tym celu należy zidentyfikować sytuacje lub inne potencjalne awarie systemu, które mogą spowodować wypadek lub problem. Warstwa SIS ma za zadanie zminimalizować ryzyko zidentyfikowane jako nieakceptowalne w ramach analizy HAZOP. Składa się ona z niezależnie działających przyrządowych funkcji bezpieczeństwa (SIF). Ponieważ BPCS jest uważany za pierwszą warstwę ochrony w dobrze zaprojektowanym i utrzymywanym obiekcie, większość SIF jest specjalnie zaprojektowana tak, aby nie wymagała dużego nakładu pracy (tzn. była uruchamiana nie częściej niż raz w roku), a częstego korzystania z niej należy unikać. Na przykład jeżeli SIF obsługuje sytuacje codziennie, a nie zdarzające się raz w roku, jak było pierwotnie zaprojektowane, należy zwrócić uwagę na system BPCS. Poleganie na SIS jako ostatniej linii obrony nie jest rozsądną strategią, ponieważ maszyny i alarmy mogą przejąć jedynie określoną ilość ryzyka. W pewnym momencie operator może być zmuszony do przejęcia kontroli i powinno być jasne, co i kiedy powinien zrobić. Oprócz systemu BPCS i SIS istnieje dodatkowa linia obrony: operator. Jeżeli operator jest powiadomiony przez alarm, posiada spójne instrukcje, co ma robić, i wystarczająco dużo czasu na wykonanie tej czynności, reakcja operatora na alarm (OPR) może być uznana jako ochrona. Aby zminimalizować ryzyko w takich przypadkach, operatorzy muszą w pełni rozumieć ogólnofirmowe polityki, strategie i inicjatywy w zakresie bezpieczeństwa, a także przejść odpowiednie szkolenie w zakresie alarmów i systemów. Przeszkoleni operatorzy są kluczem do utrzymania integralności zautomatyzowanych funkcji bezpieczeństwa systemów BPCS i SIS. Jeżeli system BPCS lub SIS wysyła sygnał ostrzegawczy, a jest on ignorowany lub operator nie jest odpowiednio przeszkolony w zakresie rozpoznawania sygnałów ostrzegawczych, to cel posiadania zabezpieczeń systemowych zostaje zniweczony.
Operatorzy, alarmy i panele operatorów
Właściwy system zarządzania alarmami i szkolenia mają kluczowe znaczenie dla zapewnienia prawidłowej reakcji operatorów na zdarzenia. Niewłaściwe zarządzanie alarmami prowadzi do nieplanowanych przestojów, przyczyniając się do utraty miliardów dolarów produkcji każdego roku oraz możliwości wystąpienia poważnego incydentu przemysłowego.
„Poleganie na SIS jako ostatniej linii obrony nie jest rozsądną strategią, ponieważ maszyny i alarmy mogą przejąć jedynie określoną ilość ryzyka.”
System alarmowy informuje operatorów o zakłóceniach, z którymi system BPCS nie może sobie poradzić w sposób automatyczny (rysunek 2). Wymagana jest wtedy reakcja operatora, aby naprawić lub złagodzić problem. Każdy alarm jest z góry zdefiniowany i ma przypisaną reakcję operatora, a operator musi znać odpowiednie działanie. Częstym problemem dla operatorów jest zbyt duża liczba alarmów sygnalizowanych podczas awarii obiektu, co określa się mianem „powodzi alarmów”. Takie przypadki zmniejszają szansę, że alarm OPR zostanie potraktowany z należytą uwagą. Procedury reagowania na alarmy powinny być jasne i łatwo dostępne – najlepiej w interfejsie człowiek-maszyna (HMI) – aby operatorzy mogli reagować szybko i skutecznie. Dzisiejsze wysokowydajne interfejsy HMI (HP-HMI) ułatwiają operatorom identyfikację alarmów dzięki grafikom w skali szarości o spójnych kolorach lub kształtach. Operatorzy powinni jednak nadal być szkoleni w zakresie krytycznych elementów alarmowych i symboli P&ID oraz być w stanie rozpoznawać i reagować na sytuacje nietypowe. Powinni oni również mieć jasną wiedzę na temat tego, co dzieje się z systemami i procesami w zakładzie. Dla celów zgodności z przepisami norma ISA-18.2 wymaga, aby obiekty przeprowadziły audyt i stworzyły kompleksową ocenę, która definiuje kryteria oceny powagi i pilności alarmu. W ramach oceny sprawdza się działanie systemu alarmowego oraz praktyki robocze wykorzystywane do administrowania systemem alarmowym. Okresowe przeglądy częstotliwości wywoływania alarmów OPR oraz czasu i dokładności reakcji operatora ujawniają luki, które nie są widoczne w rutynowym monitoringu i pozwalają personelowi zidentyfikować niezbędne usprawnienia. Mając opracowaną filozofię alarmową (czyli w zasadzie zestaw wytycznych), obiekty mogą stosować się do zestawu kryteriów przy projektowaniu, opracowywaniu, wdrażaniu, modyfikowaniu, zarządzaniu oraz ciągłym doskonaleniu i konserwacji alarmów. Można również opracować procedury reagowania na alarmy, a konkretne informacje o każdym alarmie mogą być osadzone w panelu HMI, aby pomóc operatorom szybko reagować i bezpiecznie łagodzić nietypowe sytuacje.
Wykorzystanie alarmów jako zabezpieczeń przed zagrożeniami bezpieczeństwa sterowania procesem zwiększa ich znaczenie i dodaje kolejny wymiar do prawidłowego zarządzania alarmami. Zarządzanie alarmami powinno stanowić część programu ciągłego doskonalenia zakładu i być włączone do wszelkich aktualizacji sprzętu lub projektów migracji starszych systemów. Właściwe zarządzanie alarmami staje się dzisiaj koniecznością bardziej niż kiedykolwiek.
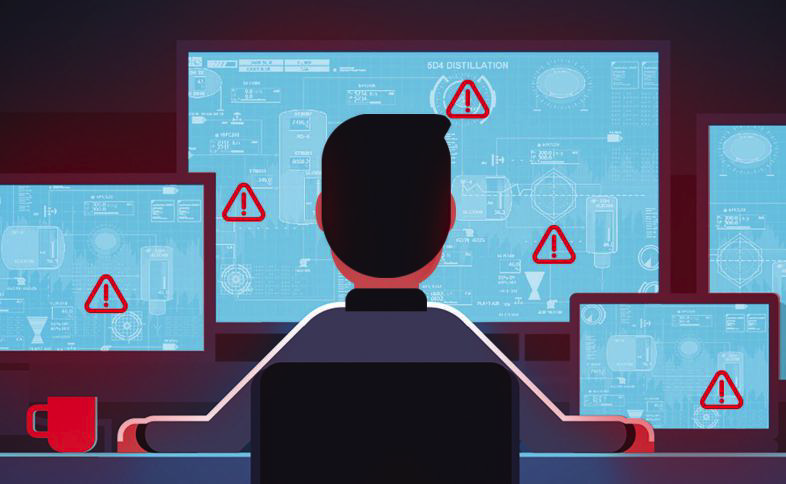
Bezproblemowa automatyzacja
Aby zapewnić bezpieczeństwo wszystkim osobom przebywającym w obiekcie i jego otoczeniu, najlepiej spojrzeć na automatykę holistycznie i przeprowadzić analizę istniejących systemów i procesów. Proces ten jest ogromnym przedsięwzięciem i może wymagać pomocy zewnętrznego dostawcy rozwiązań automatyki, który może połączyć wiedzę o procesach i automatyce z wstępną analizą i udoskonaleniami SIS oraz wiedzą na temat zarządzania alarmami. Pomoc z zewnątrz jest przydatna również wtedy, gdy operatorzy muszą zostać przeszkoleni w zakresie szerszego postrzegania tematu bezpieczeństwa i tolerowanych poziomów ryzyka. Systemy automatyki i ludzie mogą współpracować z korporacyjną kulturą bezpieczeństwa, która kładzie nacisk na brak tolerancji wobec ryzyka i właściwe zrozumienie zasad inżynierii, takich jak stosowanie odpowiednich strategii i systemów zarządzania alarmami, procedur regulacyjnych i najlepszych praktyk branżowych. Gdy wszystkie te elementy są stosowane jednocześnie, firmy mogą kontrolować zagrożenia i ryzyko oraz osiągać skuteczną kontrolę procesu.
Scott Hayes (scott.hayes@mavtechglobal.com) jest kierownikiem programu w MAVERICK Technologies. Ma ponad 20 lat doświadczenia w sterowaniu procesami. Jest licencjonowanym inżynierem systemów sterowania i certyfikowanym przez TÜV inżynierem bezpieczeństwa funkcyjnego.