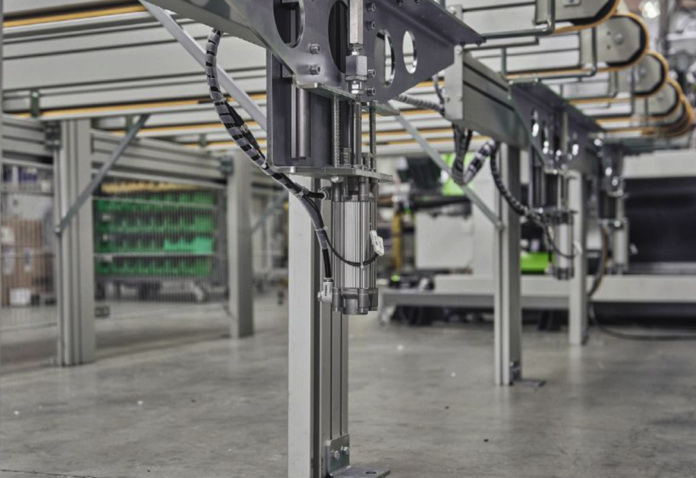
Ewolucja automatyki maszynowej dowodzi, że jedynym ograniczeniem jest tu tylko wyobraźnia człowieka.
W przeszłości ideą „powietrze jest do oddychania, woda do picia, a benzyna do samochodu”, kierowało się wielu projektantów podczas specyfikowania komponentów, projektowania systemów oraz konstruowania maszyn. Wynikiem takiego podejścia były wielkie maszyny o niewielkiej sprawności energetycznej, które zużywały znaczne ilości surowców i mediów.
Ponieważ obecnie przemysł produkcyjny ewoluuje w kierunku adaptacji bardziej wymagających, bezpiecznych i precyzyjnych procesów, obejmujących zużycie sprężonego powietrza oraz oszczędną energetycznie automatykę, przemysł pneumatyczny dostosowuje się do tego jako kluczowy partner strategiczny przemysłu produkcyjnego.
Producenci systemów pneumatycznych mają wysoką motywację do pozostawania na czele najnowszych trendów. Pojawiające się nowe technologie jednoznacznie rozwiązują problemy związane zarówno z gabarytami i masą, zużyciem energii, połączeniami w sieci, jak i monitoringiem automatyki przemysłowej, ponieważ jest to związane z efektywnością operacyjną i planowaniem utrzymania ruchu.
W dawniejszych zakładach produkcyjnych instalacje pneumatyczne były zdominowane przez całą masę zaworów, siłowników oraz innych dużych, zajmujących dużo miejsca i nieefektywnych energetycznie elementów systemu. Sprężarki powietrza były wyjątkowo przewymiarowane, zaś zawory umieszczone na podstawach o wielkości i masie cegieł. Siłowniki pneumatyczne zajmowały dużo miejsca w maszynach (chociaż syczały, co było dla obsługi sygnałem obecności sprężonego powietrza i gotowości do pracy). Co prawda te tradycyjne konstrukcje z przeszłości były użyteczne i skuteczne, jednak czasy wykorzystywania przez pracowników pneumatycznych zaworów sterujących jako stołków ze schodkiem do sięgania po coś wyżej na maszynę, odeszły już do historii.
Siłowniki te zostały zastąpione przez bardziej eleganckie i estetyczne oraz efektywniejsze energetycznie środki dostarczania sprężonego powietrza dla procesów zautomatyzowanych.
Zapotrzebowanie na sprzęt efektywny energetycznie oraz zautomatyzowane maszyny wpłynęło też na zawory pneumatyczne. Stały się one mniejsze, lżejsze i sprawniejsze energetycznie. Przygotowanie sprężonego powietrza obejmuje w pełni funkcjonalne zespoły, które zapewniają efektywność oraz odtwarzalną funkcjonalność i bezpieczeństwo. Siłowniki są lekkie, mają funkcje sprzężenia zwrotnego położenia oraz szerszy zakres zastosowań. Konieczność smarowania komponentów została wyeliminowana.
Te innowacje pozwalają projektantom skupić się na maszynach o kompaktowych wymiarach i możliwościach ich pracy w sieci, jednocześnie nie zapominając o oszczędnościach kosztów dla fabryk. Uzyskuje się dużą trwałość zespołów, które są w stanie zrealizować miliony cykli pracy zaworów oraz siłowników. Są one jednocześnie połączone z technologiami monitoringu, które wspierają programy usprawnionej konserwacji zapobiegawczej w wielu zakładach przemysłowych.
Poprawa efektywności energetycznej systemów pneumatycznych
Aby poprawić ogólną efektywność energetyczną systemu pneumatycznego w zakładzie, należy zawsze rozpocząć działania od kompresorowni. Jest to miejsce, w którym znajdują się silniki elektryczne dużej mocy, zużywające najwięcej energii. Gdy zmniejszy się obciążenie silników napędzających sprężarki, to firma uzyska korzyści finansowe.
Producenci kompresorów „czują” zapotrzebowanie zarówno na większą sprawność energetyczną, mniejszy poziom hałasu oraz instalacje bardziej przyjazne dla środowiska, jak i na integrowanie systemów pneumatycznych z podstawowymi systemami monitoringu i sterowania w fabrykach.
Dostarczyli już na rynek rozwiązania kompresorów o mniejszych gabarytach, mniej hałaśliwych w pracy oraz posiadających efektywniejsze obudowy. Kompresory mogą być wykonywane w wersji bezolejowej, silniki wyposażone w napędy o zmiennej częstotliwości (VFD) oraz innowacyjne układy sterujące, które mogą być podłączone do platformy monitoringu w fabryce (fot. 1). Takie konstrukcje umożliwiają sterowanie pracą kompresora, tj. przyśpieszaniem, hamowaniem lub nawet pracą na biegu jałowym czy wyłączeniem, zgodnie z zapotrzebowaniem fabryki. Te opcje monitoringu i sterowania oznaczają, że system pneumatyczny może być zarządzany z dowolnego miejsca w fabryce, zaś w niektórych przypadkach nawet poza zakładem.
Sprężone powietrze było kiedyś traktowane jako zwykłe medium robocze, teraz jest ono pozycją bilansową. Jego parametry i zużycie są sterowane i monitorowane przy wykorzystaniu nowych technologii, które umożliwiają uzyskanie realnych ulepszeń operacyjnych.
Uzyskanie kontroli nad zużyciem sprężonego powietrza i zmniejszenie tego zużycia można postrzegać jako etap początkowy ogólnego programu poprawy efektywności energetycznej fabryki.
Na hali produkcyjnej użytkownicy maszyn mają do dyspozycji różne opcje wyboru rozwiązań. Prawidłowy dobór mocy był odwiecznym tematem na przestrzeni lat. Gdy wpiszemy w wyszukiwarkę Google termin „projektowanie systemu pneumatycznego” („pneumatic system design”), otrzymamy ponad 84 miliony wyników. Wśród nich znajduje się wielu dostawców rozwiązań pneumatyki oferujących takie rozwiązania oprogramowania, które pozwalają na optymalny pod względem efektywności dobór komponentów maszyn. Eliminuje to możliwość dobrania przypadkowej wartości na podstawie wykorzystywanej kiedyś reguły praktycznej – według średnicy rur.
Takie narzędzia w postaci odpowiedniego oprogramowania eliminują potrzebę przewymiarowania komponentów systemu, co było kiedyś normą, i zapewniają, że maszyny będą pracować tak, jak zostały zaprojektowane, bez marnowania mediów.
Efektywność energetyczna komponentów systemów pneumatycznych
Co prawda kompresorownia z silnikami o dużej mocy jest pierwszym miejscem, któremu należy się przyjrzeć, jednak są też obszary, które można uczynić bardziej efektywnymi. Technologia zaworów została dopasowana do tej samej potrzeby oszczędzania energii, które wpłynęła na inne komponenty pneumatyczne, i to w sposób kompleksowy.
Zawory, które kiedyś wymagały mocy ponad 6 W, obecnie zużywają zaledwie 0,8 W, niedługo zaś zostaną wprowadzone konstrukcje zużywające jeszcze mniej. Łączenie wielu zaworów w bloki jest obecnie standardem. Przynosi oszczędność przestrzeni w maszynach, zmniejszenie poboru mocy oraz pozwala na wykorzystanie technologii magistrali obiektowej (fieldbus). To z kolei zredukuje ilość oprzewodowania, jednocześnie przenosząc komponenty do świata danych oraz informacji czasu rzeczywistego.
Poza dostępnymi narzędziami do doboru komponentów i ustalania parametrów projektowych technologia systemów pneumatycznych wspiera prace mające na celu wykluczenie możliwości wyczerpania się źródła sprężonego powietrza, co może być bardzo kosztowne dla zakładu.
Producenci obecnie analizują i poszukują lepszego zrozumienia takich parametrów, jak siła, ciśnienie, przepływ i prędkość. Ma to na celu odkrycie innowacyjnych sposobów zmniejszenia zużycia sprężonego powietrza. Wykorzystywane są technologie wykrywania położenia siłownika, komunikacji bezprzewodowej, regulacji ciśnienia proporcjonalnego oraz przepływu, a także nowe technologie, takie jak inteligentna pneumatyka oraz Przemysłowy Internet Rzeczy (IIoT).
Te inteligentne systemy pneumatyczne budują mosty do technologii IIoT, zapewniają widoczność systemu oraz zmniejszają koszty operacyjne – wspierane przez analizę centralną i elektronikę sterującą, wyposażoną w możliwość alarmowania fabryki o potencjalnych nieprawidłowościach lub awariach systemu.

Systemy pneumatyczne a elektryczne układy sterowania
Poza ulepszeniami rozwiązań układy sterowania maszynami zmieniły się na inne sposoby, w tym pod względem sposobu zarządzania projektami. Projekty konstrukcji maszyn oraz ich układów sterowania miały dwie strony: mechaniczną, obejmującą pneumatykę, oraz elektryczną, skoncentrowaną na sygnałach sterujących zaworami i pracą maszyn. Projektanci z obydwu dziedzin konsultowali swoje schematy, nakładali swoje plany i decydowali na miejscu, jak przekazywać sygnały sterujące.
Obecnie kontynuowany jest postęp technologiczny na drodze ku poprawie efektywności energetycznej, jednak zapotrzebowanie na najlepsze praktyki wsparcia zarządzania projektami powoduje powstanie nowego profilu dla lidera projektu „sterowania”. Taki nowy lider projektu automatyki tworzy drogę sterowania ruchem maszyn, wykorzystania elektroniki, regulacji przepływu powietrza, wykorzystania sprzężenia zwrotnego oraz monitoringu stanu technicznego maszyn. Odpowiedzialność lidera stale ewoluuje pod wpływem oczekiwań użytkownika dotyczących wydajnej technologii i wywierania nacisku na dostawców, aby obserwowali rynek i uwzględniali wszystkie trendy innowacyjne. Włączenie ciągłych ulepszeń do automatyki w fabryce spowoduje zmniejszenie kosztów produkcji oraz zwiększenie widoczności sprzętu w ramach konserwacji prognozowanej, dzięki której będzie możliwe ciągłe i efektywne utrzymanie ruchu w zakładzie.
Postępy w projektowaniu systemów pneumatycznych od strony elektrycznej obejmują: przesyłanie danych za pomocą magistrali obiektowych fieldbus, technologię IIoT oraz monitoring stanu technicznego maszyn. Są to fundamentalne ulepszenia instalacji sprężonego powietrza oraz elektrycznych w przemyśle, w porównaniu do rozwiązań z przeszłości.
Technologia fieldbus umożliwia komunikację pomiędzy komponentami związanymi z maszyną i w całej fabryce za pomocą pojedynczego kabla oraz jednoczesny wgląd w czasie rzeczywistym w pracę każdego komponentu za pomocą sieci fabrycznej lub koncentratora IIoT.
Liderzy projektów automatyki mogą analizować operacje wykonywane w fabryce z dowolnej lokalizacji – nawet z innych fabryk danej firmy, znajdujących się na całym świecie. Dane dotyczące utrzymania ruchu wspierają strategiczne zarządzanie fabryką oraz pomagają w dokonywaniu niezbędnych zmian czy rozważaniu żądań ulepszeń w maszynach lub ich wymiany. Operacje realizowane w fabryce są monitorowane i programowane tak, aby możliwa była wymiana danych ze smartfonami oraz innymi urządzeniami inteligentnymi. Pozwala to na rozwiązywanie znacznie większej ilości problemów, niż tylko zmniejszenie zużycia energii przez instalację sprężonego powietrza.
Bezpieczeństwo maszyn a oszczędzanie energii
Niezależnie od wprowadzania IIoT, inteligentnej pneumatyki oraz innych modnych nowych technologii, bezpieczeństwo zawsze będzie traktowane jako priorytet w konstruowaniu maszyn przemysłowych. W wielu przypadkach technologia skupia się na kwestiach BHP – wykorzystuje się np. strefowe zawory bezpieczeństwa czy bezkontaktowe czujniki położenia. Przy możliwości wykrywania położenia zaworów sterujących oraz potwierdzania ich położenia za pomocą monitoringu redundantnego, prawdopodobieństwo zranienia ludzi zostaje znacznie zmniejszone.
Możliwości zintegrowania tych inteligentnych komponentów ze strategiami konstruowania maszyn są coraz większe. Komponenty te są obecnie wprowadzane do systemów bezpieczeństwa w formie samodzielnych obwodów, odizolowanych i niezależnych od pracy maszyn.
W miarę ciągłego ewoluowania ulepszeń produktów projektanci systemów mogą liczyć na takie siłowniki pneumatyczne, które są lekkie, efektywne energetycznie, dokładne i wykorzystują najnowsze technologie. W zastosowaniach siłowników priorytetem jest bezpieczeństwo. Dają one całą gamę konfiguracji, takich jak: liniowe, obrotowe i beztłoczyskowe. Dzięki temu można uzyskać kompaktową konstrukcję maszyn oraz odizolowanie od operatora części wykonujących zautomatyzowane ruchy (fot. 2). Jedną z popularnych funkcji związanych ze zwiększonym poziomem bezpieczeństwa jest wykrywanie położenia siłownika na całej jego długości roboczej. W połączeniu z obwodem czujników bezpieczeństwa umożliwia to dodatkowy monitoring oraz proaktywne wezwania do działań, usuwając wiele potencjalnych zagrożeń.
Dzięki współpracy specjalistów, mającej na celu oszczędzanie energii oraz uzyskanie ogólnej efektywności energetycznej, uzyskuje się znaczne zwiększenie poziomu bezpieczeństwa maszyn za pomocą komponentów pneumatycznych oraz układów sterujących. Standardy opracowane przez organy zarządzające wymagają wdrażania funkcji bezpieczeństwa maszyn, takich jak nadzorowanie parametrów z blokadami bezpieczeństwa zatrzymującymi pracę maszyn, systemy wizyjne oraz środki do uwalniania zmagazynowanej energii. Obecnie wdrażane są dodatkowe standardy działań w kierunku bezpiecznej przestrzeni roboczej. Wszystko to ma na celu zachowanie bezpieczeństwa naszych znajomych, rodziny i współpracowników. Eksperci od automatyki maszyn cały czas traktują kwestie BHP jako najwyższy priorytet dla produktów, rozwiązań i technologii, które integrują pneumatykę z innymi produktami automatyki przemysłowej. Ich celem jest uczynienie dzisiejszych maszyn bezpieczniejszymi w użytkowaniu.
Perspektywy na przyszłość
Obecnie produkty z branży technologii automatyki przemysłowej są projektowane, wprowadzane na rynek oraz włączane w nowe projekty w odpowiedzi na oczekiwania większej efektywności energetycznej. Tendencja ta jest silna i rosnąca. Coraz więcej projektantów i dostawców systemów pneumatycznych spełnia te oczekiwania poprzez kreatywne i innowacyjne podejście do nowych i pełnych wyzwań zastosowań. Można by się spierać w kwestii tego, czy wcześniejsze systemy pneumatyczne były przewymiarowane i zużywały zbyt dużo sprężonego powietrza. Jednak technologia zmieniła krajobraz całej fabryki. Producenci systemów pneumatycznych reagują na oczekiwania konstrukcyjne oraz aplikacyjne, uwzględniając wszystkie aspekty danej fabryki. Rozumieją, że sprężone powietrze nie jest już tylko zwykłym medium roboczym, jak to było w przeszłości.
Dzisiejsza fabryka pracuje bardziej efektywnie, panuje pełna świadomość oczekiwania bardziej efektywnych procesów. Fabryka jutra będzie podlegać nawet większym fundamentalnych zmianom technologicznym. Producenci systemów pneumatycznych wykraczają obecnie poza granice technologii, z którymi byli i są najlepiej zaznajomieni. Włączają do swoich produktów aplikacje na smartfony, komunikację bezprzewodową, monitoring maszyn oraz produkcji w czasie rzeczywistym i – co najważniejsze – zwiększone bezpieczeństwo operatorów i zapobieganie wypadkom przy pracy. W miarę jak te innowacje cały czas zwiększają efektywność oraz wprowadzają nowe możliwości, fabryka jutra będzie dysponowała opcjami ograniczonymi jedynie wyobraźnią człowieka.
Bob Bradley jest certyfikowanym specjalistą od hydrauliki siłowej w firmie Motion Industries. Mieszka w Loves Park (stan Illinois). Pracuje w przemyśle hydrauliki siłowej od 1988 r., zaś w firmie Motion Industries od 17 lat. Obecnie zajmuje się wsparciem sprzedaży w wielu lokalizacjach firmy w północnym Illinois.
Robert (Robby) Haun jest dyrektorem ds. sprzedaży krajowej produktów mechanicznych w firmie Emerson. Pracuje tam od 2012 r. Mieszka w Knoxville (stan Tennesee). Ukończył uniwersytet w Ashford ze stopniem magistra oraz podyplomowe studia menedżerskie (MBA) na uczelni South College. Rozpoczął swoją karierę w branży automatyki maszyn w 2000 r. Obecnie specjalizuje się w hydraulice siłowej większej mocy, projektując i sprzedając systemy pneumatyczne i hydrauliczne oraz zarządzając działami sterowania elektrycznego i automatyki firmy Emerson.