Droga do cyfrowego zakładu produkcyjnego może być stopniowa, przynosząc korzyści po drodze dzięki proponowanemu podejściu polegającemu na powiązaniu praktyk lean z gromadzeniem danych, tak aby użytkownicy w całym zakładzie mieli dostęp do wizualizacji i analiz.
Wgląd w cyfryzację
Firmy wprowadzające cyfryzację i transformację cyfrową do swoich obiektów mogą uzyskać więcej informacji i poprawić wydajność w swoich zakładach produkcyjnych.
Zastosowanie szczupłego podejścia do tego procesu i krótkich sprintów może pomóc firmom w osiągnięciu niewielkich, ale przyrostowych korzyści tam, gdzie są one potrzebne i wykorzystać je jako dowód koncepcji przy rozszerzaniu jej zakresu.
Zakład Phoenix Contact w Bad Pyrmont w Niemczech to zakład produkcji elektroniki, który wdrożył cyfryzację fabryki. Lokalizacja ta działa jako inteligentny zakład produkcyjny od kilku lat. Podczas cyfryzacji operatorzy zakładu zidentyfikowali i wdrożyli projekty, które poprawiły wydajność o ponad 10% rocznie. Odkryli również, że mogą przejść od pomysłu do realizacji nawet pięć razy szybciej. Owijanie cyfrowych informacji produkcyjnych wokół istniejących procesów lean i agile pomaga uczynić te dane łatwo dostępnymi dla pracowników. Tworzy to pętlę sprzężenia zwrotnego, która może zwiększyć produkcję.
Amerykański zakład produkcyjny Phoenix Contact, zlokalizowany w pobliżu Harrisburga w Pensylwanii, ma 70 000 stóp kwadratowych powierzchni produkcyjnej podzielonej na produkcję elektroniczną i elektromechaniczną. Działalność produkcyjna w Stanach Zjednoczonych formalnie rozpoczęła się w 2003 roku, od niestandardowych produktów na rynek amerykański. Możliwości rozwoju były stopniowo dodawane, a produkcja rosła, obejmując standardowe produkty katalogowe do globalnej dystrybucji.
W 2021 roku Phoenix Contact rozpoczął pięcioletni program inwestycyjny o wartości 19 milionów dolarów, aby lepiej obsługiwać organiczny wzrost na rynku północnoamerykańskim, zmniejszyć ryzyko związane z łańcuchem dostaw i lepiej wykorzystać ogólne aktywa zakładu.
Program składa się z dziewięciu projektów podzielonych na 39 podprojektów. Sześć podprojektów koncentruje się na stworzeniu w pełni cyfrowej fabryki. Wysiłek został zaplanowany jako część codziennej pracy, a istniejący personel produkcyjny wdraża działania. Ten sam zespół jest również odpowiedzialny za wdrażanie nowych maszyn w ramach projektów rozbudowy. To sprawia, że priorytetyzacja działań na hali produkcyjnej ma kluczowe znaczenie. Chociaż spowalnia to tempo podróży, jest to praktyczne podejście. Krótkie “sprinty” pilotażowe lub wydarzenia pozwalają na eksperymentowanie, sprawdzanie koncepcji i szybkie uzyskiwanie informacji zwrotnych na temat nowych działań.
Zakład produkcji elektroniki Bad Pyrmont stał się szablonem potencjalnego sukcesu. Amerykański zakład jest inny, co oznaczało, że podejście Bad Pyrmont nie mogło zostać skopiowane. Oprócz produkcji elektronicznej i elektromechanicznej, Harrisburg posiada starszy system realizacji produkcji (MES) na wielu stacjach roboczych i większości zautomatyzowanych maszyn. Różne obszary produkcyjne działają prawie niezależnie, a wszystkie systemy informacyjne i raportowanie kluczowych wskaźników wydajności (KPI) zostały ustanowione w ten sam sposób. Chociaż można było zastosować podejście Bad Pyrmont, zespół projektowy musiał dostosować się do już istniejącego sprzętu i narzędzi raportowania.
Podejście do cyfryzacji składało się z trzech filarów: Zarządzanie halą produkcyjną, gromadzenie i analiza danych oraz wizualizacja.
1. Zarządzanie halą produkcyjną
Zarządzanie halą produkcyjną to instytucjonalizacja procesu lean. Zespół praktykuje techniki lean od ponad dekady. Phoenix Contact zazwyczaj organizował wydarzenia Kaizen podczas identyfikowania problemów lub instalowania nowych linii produktów. Program zarządzania halą produkcyjną sprawił, że działania te stały się codziennymi nawykami.
Ten podprojekt rozpoczął się w połowie 2021 r., kiedy zespół projektowy rozszerzył codzienne spacery Gemba na wszystkie obszary produkcyjne i spotkania kierownictwa hali produkcyjnej, wykorzystując dane z procesu w czasie zbliżonym do rzeczywistego (rysunek 1). Spacery i spotkania koncentrowały się na natychmiastowym rozwiązywaniu problemów z personelem tak blisko zdarzeń, jak to możliwe. Regularnie odbywają się wydarzenia 5S (sortowanie, prostowanie, zamiatanie, standaryzacja i utrzymanie), a wyniki są śledzone. Działania związane z doskonaleniem procesów są prowadzone w sposób ciągły.
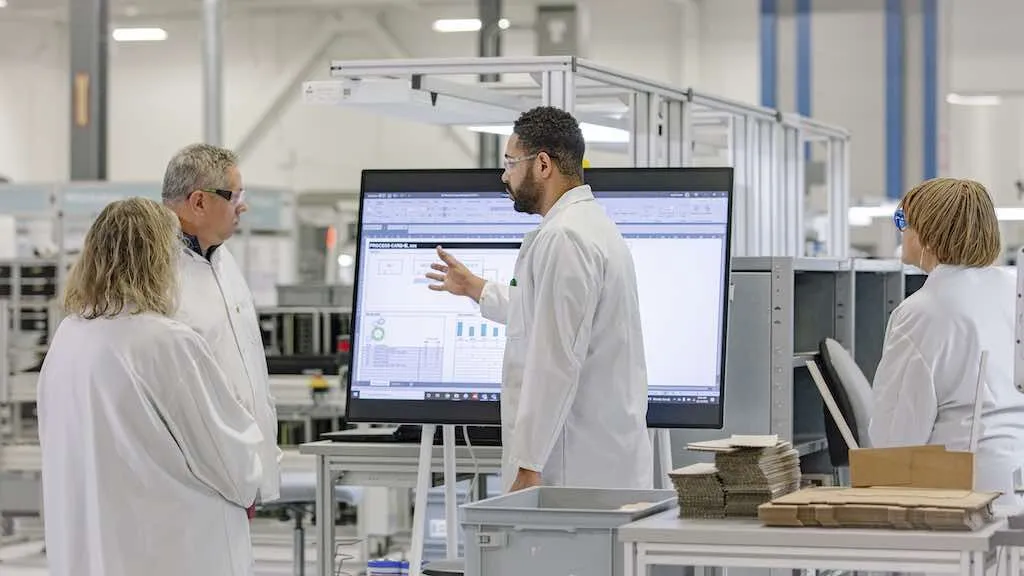
2. Gromadzenie danych
Gromadzenie danych rozpoczęło się w czerwcu 2022 roku. Wymagane są dane z trzech unikalnych kategorii sprzętu: MES, sprzętu, który jest połączony głównie za pośrednictwem otwartej platformy komunikacyjnej (OPC) lub interfejsu programowania aplikacji (API) oraz samodzielnych starszych maszyn i stacji roboczych.
System MES został początkowo wdrożony do planowania hali produkcyjnej w jednym z elektromechanicznych obszarów produkcyjnych. Wszystkie zautomatyzowane maszyny zbudowane wewnętrznie również posiadają łączność z MES. Mierzy on efektywność operacyjną sprzętu (OEE) i porównuje operacje z podobnymi maszynami na całym świecie. Te dwie aplikacje zostaną połączone w celu rozszerzenia planowania hali produkcyjnej na zautomatyzowane maszyny i pomiar całego przepływu wartości procesu. Wszystkie dane są dostępne wyłącznie za pośrednictwem scentralizowanych aplikacji korporacyjnych.
Możliwe jest również udostępnienie tych danych narzędziom wizualizacyjnym do raportowania KPI i narzędzi analitycznych wybranych przez użytkownika końcowego. Standardowe interfejsy API zapewniają dostęp do aplikacji i wizualizacji specyficznych dla użytkownika.
Urządzenia z obsługą połączeń zapewniają dostęp za pośrednictwem standardowego interfejsu, głównie OPC UA. Większość tego sprzętu jest kupowana od producentów maszyn, którzy zapewniają łączność w standardzie. Przykłady tego sprzętu obejmują moduły liniowe do montażu powierzchniowego, automatyczny sprzęt testujący i półautomatyczne pakowanie. Nowe, niestandardowe lub częściowo niestandardowe, lokalnie pozyskiwane maszyny mają kontroler open-source, który działa również jako serwer kolejkowania komunikatów telemetrycznych (MQTT). Zapewnia to taką samą łączność jak samodzielne maszyny i stacje robocze (rysunek 2).
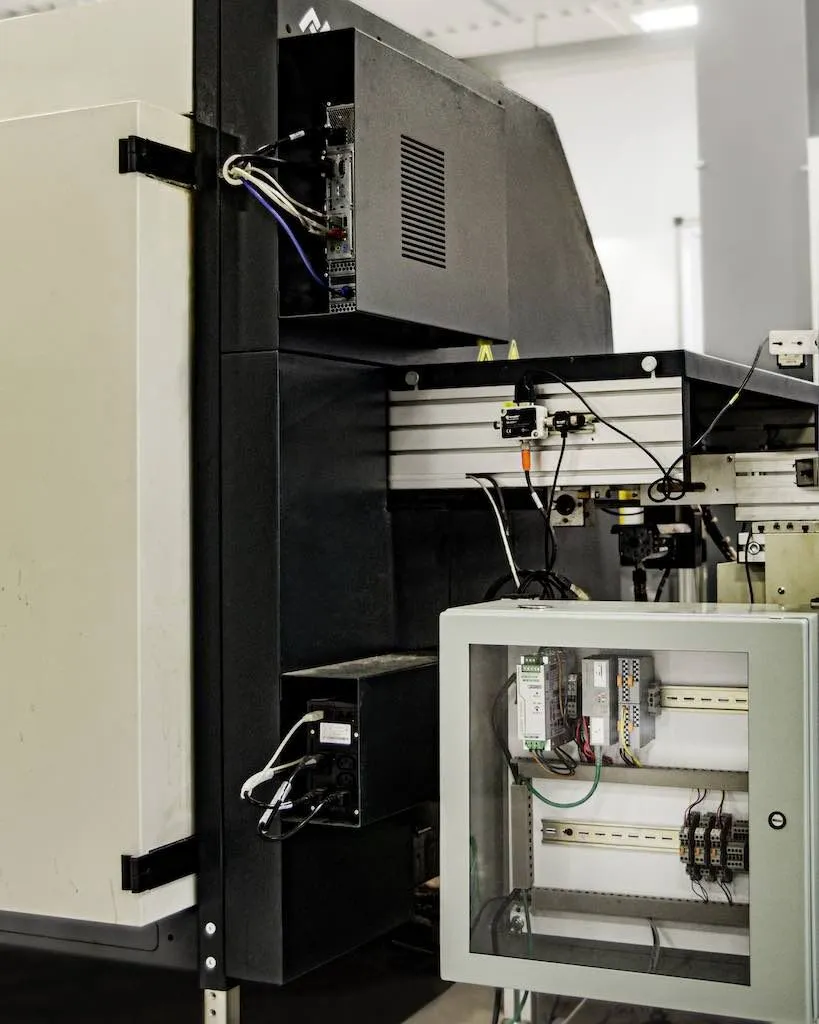
Samodzielne maszyny i stacje robocze stanowią dużą część istniejących aktywów w produkcji i obejmują ręczne, półautomatyczne i w pełni zautomatyzowane maszyny lub obszary robocze. Są one sterowane przez komputery przemysłowe lub programowalne sterowniki logiczne (PLC) wcześniejszej generacji. Maszyny te są częścią codziennej produkcji, więc zespół projektowy potrzebował niskiego ryzyka i nieinwazyjnego podejścia do podłączenia sprzętu. Wejścia są często okablowane równolegle w szafie sterowniczej, do czujników z pożądanymi danymi. Są one podłączone z powrotem do kontrolera open-source, który działa jako brama MQTT do sieci produkcyjnej.
Metodą wybraną do połączenia tego wszystkiego jest architektura mikrousług. Każde źródło danych lub program analityczny zbierający dane znajduje się w kontenerach dostępnych za pośrednictwem interfejsów API. Aplikacje lub osoby z prawami dostępu za pośrednictwem interfejsu API mają dostęp do danych w czasie zbliżonym do rzeczywistego bez konieczności ich wstępnego przetwarzania lub przechowywania. Narzędzia open-source wspierają ten wysiłek.
Zaletami tej architektury są elastyczność, szybkość i rozszerzone wykorzystanie istniejącej siły roboczej. Nie wiąże ona również nikogo z jednym dostawcą. Aplikacje mogą być tworzone zgodnie z potrzebami i pilotowane. Jeśli zakończą się sukcesem, wewnętrzni specjaliści utwardzają je i udostępniają szerszej społeczności.
Programiści tworzą aplikacje przy użyciu znanych im środowisk programistycznych. Struktura nie jest specyficzna dla dostawcy, więc narzędzia od różnych dostawców mogą być używane i mieszane w ramach architektury.
MES jest aplikacją obejmującą całe przedsiębiorstwo, jednak za pośrednictwem interfejsu API można uzyskać dostęp do danych, aby umożliwić korzystanie z innych aplikacji zdefiniowanych przez użytkownika. Na przykład cyfrowy bliźniak uzyskuje status maszyny z MES, aby wyświetlić go w osobnym narzędziu do wizualizacji (rysunek 3). Architektura ta pasuje do infrastruktury bezpieczeństwa IT, jednocześnie umożliwiając personelowi pracę zgodnie z wytycznymi sieci produkcyjnej.
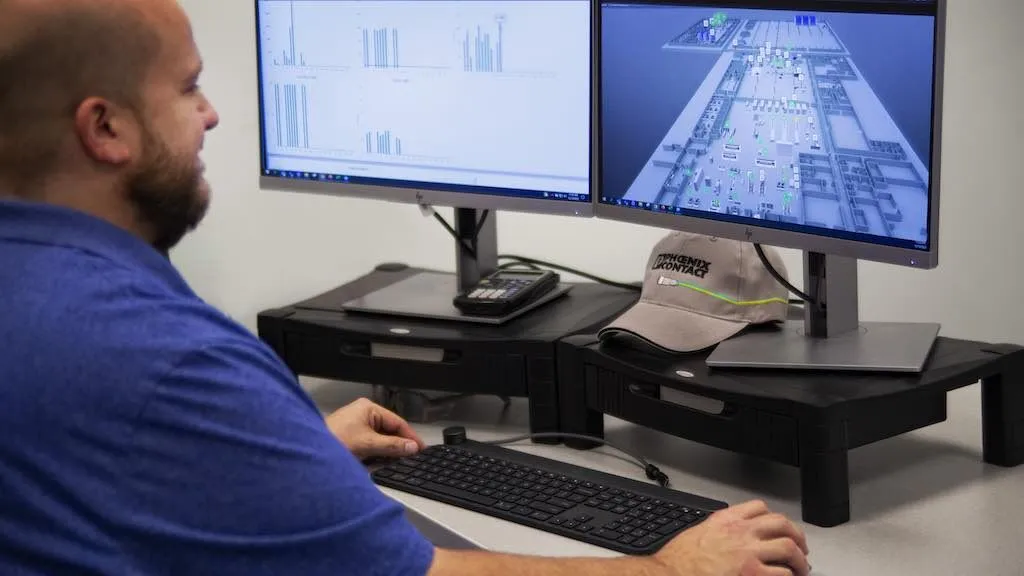
3. Analityka i wizualizacja
Analityka i wizualizacja zostały wdrożone na stanowiskach pracy ze zautomatyzowanymi maszynami lub MES. Operatorzy używają tych narzędzi do wywoływania, otwierania, śledzenia i zamykania zleceń pracy. Dostępne są również narzędzia OEE maszyn i statystycznej kontroli procesów. Dodatkowy dostęp do planowania zasobów przedsiębiorstwa, MES i zarządzania cyklem życia produktu zapewnia dane KPI produkcji na poziomie bezpośredniej produkcji, nadzoru i inżyniera produkcji lub na poziomie maszyny lub stacji roboczej. Celem jest rozszerzenie dostępu do informacji w przedsiębiorstwie.
Cyfrowy bliźniak był pierwszym krokiem w tym kierunku, zapewniając świadomość sytuacyjną. Oto jeden ze sposobów, aby to wyjaśnić: Użytkownik znajduje coś na interfejsie operatora w tym samym miejscu na hali produkcyjnej. Jeśli konkretna maszyna znajduje się poza wejściem produkcyjnym i po prawej stronie, użytkownik znajdzie ją tam na grafice cyfrowego bliźniaka. Grafika maszyny umożliwia dostęp do podstawowych informacji: włączona lub wyłączona, liczba wyprodukowanych lub odrzuconych jednostek i inne. Obejmuje również wszelkie bieżące projekty usprawniania procesów, ze statusem w procesie lub obszarze produkcyjnym. Lokalizacje tablic KPI w produkcji są również dostępne elektronicznie za pośrednictwem cyfrowego bliźniaka.
Zaangażowanie pracowników generuje nowe pomysły
Bezpośrednia i ciągła komunikacja umożliwiła pracownikom dzielenie się pomysłami na usprawnienie procesów. Wszyscy pracownicy w amerykańskiej organizacji Phoenix Contact są informowani o działaniach na wysokim szczeblu co najmniej raz na kwartał. Zespół kierowniczy jest informowany co miesiąc, a cały personel produkcyjny i projektowy otrzymuje cotygodniowe aktualizacje.
Taka komunikacja i zaangażowanie pozwalają na większe uczestnictwo. Na przykład, praktykant mechatroniki zaangażowany w jedną z tych aktualizacji wyraził zainteresowanie programowaniem niektórych aplikacji poza sterownikami PLC. Został sparowany z inżynierem produkcji z doświadczeniem w programowaniu, aby wdrożyć pierwszą bramę MQTT na miejscu.
W innym przykładzie, technik mechatronik z drugiej zmiany wykonał hack przy użyciu kodu QR przyklejonego do maszyny, aby pomóc mu zapamiętać często używane numery części zamiennych. Podzielił się tym ze swoim przełożonym, który dostrzegł korzyści i zagrożenia. Współpracowali z działem IT, aby stworzyć niestandardowe rozwiązanie rzeczywistości rozszerzonej (AR).
Zbudowali aplikację do skanowania maszyny za pomocą autoryzowanego telefonu komórkowego lub tabletu, dzięki czemu mogli zidentyfikować i natychmiast uzyskać dostęp do całej dokumentacji maszyny, w tym list części (rysunek 4). Ten pilotaż zakończył się sukcesem i jest obecnie skalowany w całym dziale. Posiadanie serwera danych w całym przedsiębiorstwie pozwala na większy dostęp użytkowników do osób, które nie są zależne od innych w celu tworzenia raportów lub uzyskiwania dostępu do danych. To niewielki zysk, ale przyniósł realne rezultaty.
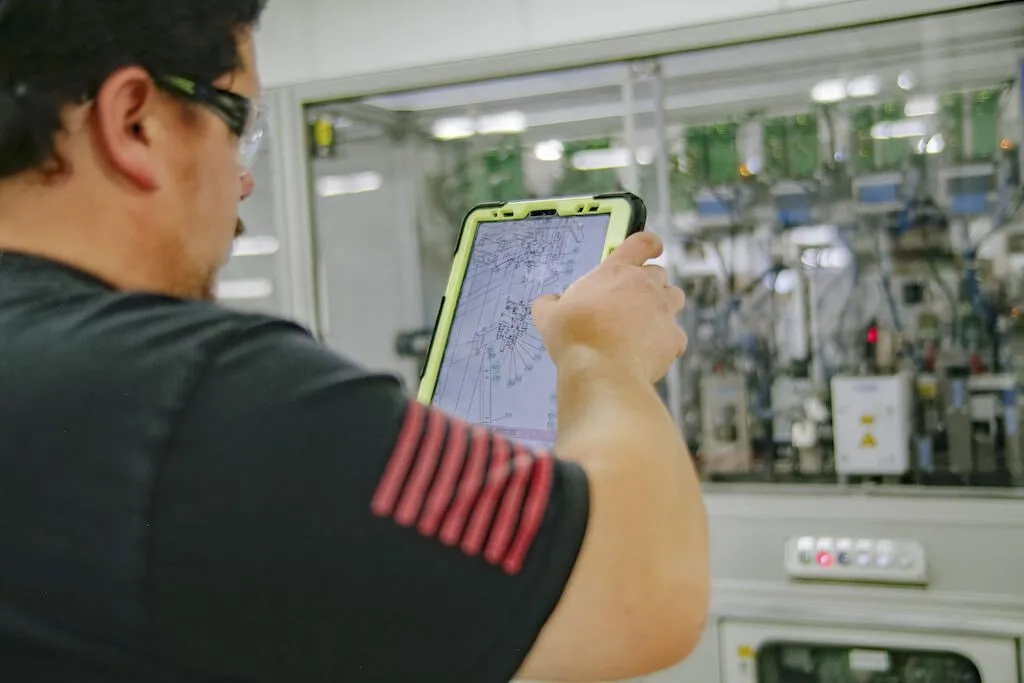
Wstępne wyniki i wyciągnięte wnioski
Program zarządzania halą produkcyjną przyniósł znaczące korzyści. Pomimo problemów z łańcuchem dostaw, produkcja wzrosła o 23% w 2022 roku. Wydarzenia Kaizen poprawiły wydajność od 7% do 33%. Nowy układ hali produkcyjnej zoptymalizował przestrzeń, tworząc miejsce na dodanie dwóch nowych linii produktów. Wysiłek zaowocował również zaktualizowanymi mapami strumienia wartości, które pomogą ustalić priorytety działań związanych z gromadzeniem danych.
Gromadzenie danych posuwa się naprzód. Do tej pory podłączono 30% wszystkich maszyn i stacji roboczych. Integracja API MES umożliwiła pilotażowy projekt gromadzenia i wyświetlania statusu maszyny za pośrednictwem cyfrowego bliźniaka. Sukces ten potwierdził słuszność koncepcji i zapoczątkował projekt automatycznego wyświetlania wskaźników KPI w czasie rzeczywistym. Stamtąd zespół projektowy może przejść do poszczególnych maszyn w celu codziennego zarządzania produkcją. Firma przeprowadziła pilotaż nowej maszyny typu pick-and-place ze standardowym interfejsem i opracowała harmonogram dla pozostałego sprzętu. Dwie samodzielne maszyny pilotowały koncepcję gromadzenia danych MQTT i zaplanowały pozostałe stacje robocze.
Cyfrowy bliźniak jest aktywny i jest na bieżąco aktualizowany o nowe instalacje sprzętu i działania związane z przekazaniem zakładu. Dostępny jest aktualny status maszyny cyfrowej. Dane kilku maszyn mogą być wyświetlane za pomocą oprogramowania open-source. Utworzono komitet sterujący ds. cyfryzacji składający się z personelu operacyjnego i informatycznego, który kieruje kwalifikacją, wdrażaniem i standaryzacją aplikacji obejmujących analitykę i wizualizację. Pierwsze programy obejmowały rozbudowę istniejących aplikacji MES we wszystkich obszarach produkcji. Proces ten jest już prawie zakończony.
Wdrożono dwie kolejne aplikacje pilotażowe. Pierwsza dotyczy zarządzania pracą, a druga jakości procesu. Każda z nich dotyczy innego obszaru produkcji, ale wiele projektów może być prowadzonych jednocześnie, aby pomóc w poszerzeniu wiedzy w całym zakładzie. Jeśli oba projekty pilotażowe zakończą się sukcesem, zostaną wdrożone w całym zakładzie.
Dwa projekty pilotażowe dotyczące AR zostały zakończone i rozpoczyna się ich skalowanie na inne obszary. Jednym z nich jest rozwiązanie specyficzne dla dostawcy, które pomaga wdrażać nowych pracowników. Drugim jest aplikacja do rozwiązywania problemów z maszynami.
Najlepsze praktyki dla przyszłych projektów
Wszystkie zakłady produkcyjne i ich specyficzne działania są wyjątkowe, ale inne organizacje mogą stosować to podejście, jeśli będą przestrzegać kilku najlepszych praktyk.
Po pierwsze, zakład musi określić jasny kierunek lub ogólny cel cyfryzacji produkcji i regularnie komunikować go organizacji.
Ważne jest powiązanie lean z działaniami cyfrowymi. Rzeczywiste dane z maszyn umożliwiają lepsze i szybsze podejmowanie decyzji. Zbieranie danych wzdłuż strumienia wartości procesu zapewnia punkt wyjścia i natychmiastową informację zwrotną po zmianie. Chociaż istnieją różne sposoby gromadzenia danych, ważne jest, aby były one dostępne dla wszystkich użytkowników.
Najpierw przeprowadzaj testy pilotażowe i nie staraj się być doskonały. Jeśli pilot osiągnie 80% początkowego zakresu, jest wystarczająco dobry, co pomoże zapobiec utknięciu firm w martwym punkcie. Opieraj się na tych sukcesach i informuj o nich całą organizację.