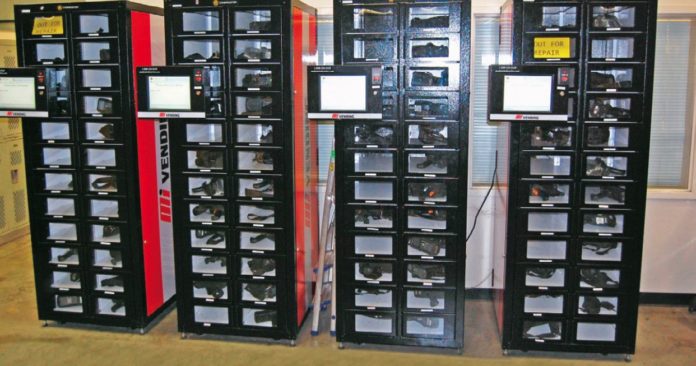
Programy zautomatyzowanego zaopatrzenia pracowników w materiały mogą poprawić zarządzanie materiałami, oraz dać pracownikom lepszy dostęp do nich.
Efektywność definiowana jest jako zdolność do działania bez marnowania materiałów, czasu lub energii. Poświęcenie czasu na zidentyfikowanie miejsc występowania marnotrawstwa w zakładzie przemysłowym może być problemem podczas dnia pracy, gdy jesteśmy zajęci sprawami związanymi z produkcją. Pracownicy wielu zmian roboczych muszą realizować swoje zadania, których wymaga regularna produkcja, oraz zajmować się przypadkowymi przestojami, które się czasami zdarzają.
Gdy pracownik fabryki musi wykonać naprawę maszyny czy urządzenia i potrzebuje do tego celu pobrać z magazynu materiały lub środki ochrony indywidualnej (ang. personnel protective equipment, PPE), może on udać się do odpowiedniego pomieszczenia aby otrzymać te pozycje. Wdrożenie programu zautomatyzowanego zaopatrzenia pracowników jest jednym ze sposobów jednoczesnego szybkiego dostarczania pracownikom potrzebnych im materiałów, narzędzi i środków ochrony, oraz badania obszarów potencjalnego marnotrawstwa.
Odpowiedzialność pracodawców polega na zaufaniu: czy pracownicy mogą ufać że pozycje, których potrzebują do wykonania swoich zadań, będą łatwo dostępne i funkcjonalne?
Czy pracownicy mogą ufać, że ich pracodawcy są odpowiedzialni za produkty, które pracownicy ci używają do wykonywania swoich zadań?
Czas jest ważnym i ograniczonym zasobem. Prawidłowy program zautomatyzowanego zaopatrzenia pracowników może przekształcić czas w pieniądze poprzez umożliwienie pracownikom skupienia się na realizacji swoich zadań zamiast na poszukiwaniach, czasem bezskutecznych, pozycji z magazynu których potrzebują do wykonania pracy.
Dobrze zaprojektowany i wdrożony program zautomatyzowanego zaopatrzenia pracowników w materiały, środki ochrony indywidualnej i narzędzia może pomóc firmie w zidentyfikowaniu i osiągnięciu niektórych z jej celów. Zaopatrzenie to działa poza kulisami, a jego celem jest prawidłowo funkcjonujący zakład i pracownicy będący skupionymi na wykonywaniu swoich zadań oraz byciu produktywnymi. Aby osiągnąć najlepszy wynik wdrożenia takiego programu, każdy zakład wymaga rozwiązania opracowanego specjalnie pod kątem jego potrzeb. Poniżej podano dwa przykłady osiągnięcia sukcesu przez firmy, oraz zwiększenia produktywności personelu.
- Zmiany w branży stalowej.
Pewien zaawansowany technologicznie producent wyrobów stalowych posiadał po jednej stronie swojego zakładu duży magazyn, z którego wydawano materiały pracownikom. Firma zadecydowała, aby zreorganizować ten proces w celu ulepszenia przepływu roboczego i skonsultowała się ze swoim dostawcą materiałów aby był on zorientowany, które pozycje pracownicy fabryki zużywają regularnie. Z kolei określiło to także pozycje będące kandydatami do dystrybucji za pomocą automatów.
Prace te umożliwiły kierownictwu firmy bliższe przyjrzenie się swoim istniejącym systemom, oraz identyfikację obszarów marnotrawstwa. Dostawca współpracował z każdym działem fabryki, aby zebrać odpowiednie dane i otrzymać bardziej wszechstronny wgląd w potrzeby każdego działu, realizowane przez przyszły program zaopatrzenia. Na przykład niektóre działy uświadomiły sobie, że nie zużywają aż tak wiele produktów, jak oczekiwano w pewnych obszarach fabryki.
W tym przypadku okazało się, że wielki magazyn nie jest wydajny. Kierownicy działów musieli opracowywać „listy zakupów” potrzebnych produktów, aby składać zamówienia z góry. Nabywcy próbowali zmierzyć zapotrzebowanie i zamawiać to, czego według swoich oczekiwań potrzebowali, na podstawie poziomu maksymalnego i minimalnego. To zgadywanie spowodowało, że magazyn posiadał konsekwentnie nadmiar lub niedobór materiałów.
Czas potrzebny pracownikom na przejście ze stanowiska pracy do magazynu, pobranie potrzebnych pozycji i powrót powodował straty produktywności tych pracowników, wynoszące wiele godzin tygodniowo. Rozwiązaniem problemu okazało się zainstalowanie magazynu karuzelowego i wag do materiałów w specyficznych punktach zużycia materiałów w całej fabryce.
Poza oszczędnościami czasu dla tych pracowników kierownictwo fabryki uwolniło się od innego problemu – papierkowej roboty. Rozwiązania zautomatyzowanego zaopatrzenia pracowników w materiały dostarczyły także zautomatyzowany system składania zamówień, który usprawnił proces rozliczeń i zmniejszył ilość faktur od kilku dziennie do dziewięciu tygodniowo.

2. Piękno efektywności pracy
W przypadku pewnej firmy z branży kosmetycznej zautomatyzowany program zaopatrzenia pracowników działał dobrze, gdy został wdrożony w centrum dystrybucji. Podstawową potrzebą było tam zarządzanie pracą radiowych czytników kodów, oraz posiadanie jakiejś metody kontrolowania wydawania środków ochrony indywidualnej.
Pracownicy mieli możliwość używania jednego z czterech typów radiowych czytników kodów. Narzędzia te były przechowywane na półkach i nie istniała formalna metoda ich sprawdzania przy pobieraniu i zdawaniu. Pracownicy często preferowali jeden model czytnika, niechętnie zaś używali pozostałych. Pracownicy ci nie mogli liczyć na otrzymanie dostępnego czytnika na początku swojej zmiany roboczej, szczególnie gdy istniało nakładanie się zmian w czasie, lub gdy wybierany przez nich czytnik nie miał w pełni naładowanych baterii, albo był uszkodzony.
Istniejący system zaopatrzenia polegał na zgłaszaniu przez pracowników nieprawidłowo funkcjonujących urządzeń, lub konieczności dostarczenia nowych baterii, ale brak wygodnego systemu zgłaszania problemów powodował, że zbyt często zgłaszano je za późno, dopiero po zakończeniu długiej zmiany roboczej. W wyniku tego utworzyła się następna grupa pracowników, którzy przed rozpoczęciem pracy musieli tracić cenny czas na poszukiwanie sprawnego czytnika.
Po wykonaniu pełnej analizy potrzeb tego klienta okazało się, że najlepszym rozwiązaniem problemu jest automat do wydawania sprzętu (automat vendingowy), skanujący identyfikatory pracowników, lub wymagający od nich podania numeru identyfikacyjnego, oraz zgłoszenia stanu technicznego sprzętu przy jego zdawaniu. Było to szybkie i proste rozwiązanie, które automatycznie alarmowało personel kierowniczy gdy czytniki wymagały konserwacji, oraz zapewniało że każdy pracownik miał zagwarantowany dostęp do działającego czytnika. Ta mała zmiana rozwiązała główny problem z marnotrawieniem czasu w pracy. Inna korzyścią z wprowadzenia automatu było to, że można było rozliczać się z każdego urządzenia, tak więc kierownictwo mogło utrzymywać nadwyżkę dostępnych narzędzi w przypadku nakładania się zmian roboczych w czasie.
Kierownictwo firmy zastosowało rozwiązanie zautomatyzowanego zaopatrzenia pracowników w potrzebne narzędzia i samo pozostało odpowiedzialne za liczną załogę, poprzez zainstalowanie dwóch magazynów karuzelowych do wydawania pracownikom środków ochrony indywidualnej. W tym przypadku personel nadzoru wykorzystał wbudowaną w maszynę funkcję śledzenia, oraz proces automatycznego składania zamówień do zapewnienia, że pracownicy zawsze posiadają swoje wymagane przepisami BHP środki ochrony indywidualnej.
Odpowiedzialność personelu kierowniczego za podległych pracowników podąża dwiema drogami. Kierownicy, którzy muszą pracować ze swoimi podwładnymi jako jeden zespół, często widzą doskonałe wyniki, które wpływają na ich zyski. Wdrażanie z konieczności programu zautomatyzowanego zaopatrzenia pracowników zmienia sposób działania całego zespołu, a ta zmiana oferuje możliwość dokonania ulepszeń, które są trudne do zmierzenia, ale są bezdyskusyjne.
Na przykład rozwiązanie w postaci automatu do wydawania narzędzi zdemokratyzowało system. Pracownicy nie mieli w nim zagwarantowanej dostępności do swojego ulubionego czytnika, co początkowo uważali za mankament. Jednak dało to kierownictwu okazję do skupienia się na szkoleniu pracowników, po przejściu którego każdy z nich czuł się komfortowo używając dowolnego czytnika z dostępnych. To usunęło potencjalną słabość z ich siły roboczej, jednocześnie pomagając każdej zmianie w rozpoczęciu pracy w wyznaczonym czasie i zgodnie z wyznaczonymi zadaniami.
Badania termowizyjne stanowią wartościowe narzędzie dla utrzymania ruchu w zakładach
Autor: David Manney, firma L&S Electric
Maksymalizacja czasu pracy bez przestojów musi być głównym celem przy prowadzeniu firmy w obecnych, trudnych dla gospodarki światowej czasach. Wykonywanie corocznych badań termowizyjnych (skanowania w podczerwieni, IR) powinno być główną częścią firmowego programu konserwacji predykcyjnej. Badania termowizyjne pomagają w zabezpieczaniu zasobów, oraz zapobiegają przestojom i katastrofalnym uszkodzeniom sprzętu.
Zaawansowane funkcje kamer termowizyjnych dają użytkownikom szczegółowe obrazy, pokazujące miejsca nadmiernego wydzielania się ciepła w sprzęcie. Nadmierne temperatury w podzespołach wskazują na możliwe problemy, takie jak korozja, zachwianie równowagi czy przeciążenie. Po zinterpretowaniu profilu cieplnego łatwo jest dokładnie zdiagnozować kondycję sprzętu. Następnie po przeanalizowaniu przyczyny znalezionego problemu można dostarczyć zalecenia dotyczące jego rozwiązania.
Badania termowizyjne instalacji i urządzeń elektrycznych lokalizują miejsca przegrzewania się w komponentach i połączeniach. Możliwe jest odnalezienie odcinków instalacji narażonych na nadmierne wydzielanie się ciepła z powodu zwiększonej rezystancji. W ten sposób łatwiej jest stwierdzić istnienie potencjalnego problemu przed wystąpieniem awarii całego urządzenia czy systemu. Badania termowizyjne zapobiegają ponadto zagrożeniem dla BHP, oraz stratom wydajności produkcji. Wszystkie te czynniki mają wpływ na firmę.
Na podstawie wykonywanych przez towarzystwa ubezpieczeniowe statystyk i analiz można stwierdzić, że ponad 30% strat spowodowanych przez pożary jest spowodowanych problemami z instalacjami i urządzeniami elektrycznymi. Nawet jeśli awarie tych instalacji i urządzeń nie powodują dużych pożarów, to mogą jednak spowodować uszkodzenia sprzętu. Wszystkie takie wypadki przyczyniają się do zmniejszenia wydajności produkcji, co powoduje długotrwałą utratę klientów przez firmę.
Tak więc wiele towarzystw ubezpieczeniowych wymaga od firm przeprowadzania co roku badań termowizyjnych. Jeśli przeanalizujemy sposób, w jaki ten proces zmniejsza ryzyko uszkodzenia zakładu czy sprzętu oraz zranienia personelu, to możemy w rezultacie płacić niższe składki ubezpieczeniowe.
Amerykański Narodowy Związek Ochrony Przeciwpożarowej (ang. National Fire Protection Association, NFPA) zauważa, że badania termowizyjne pomagają w zapobieganiu stratom powodowanym przez nadmierne wydzielanie się ciepła w zakładach, które prowadzi do powstawania pożarów. NFPA zaleca, aby właściciele firm co roku przeprowadzali badania termowizyjne instalacji elektrycznych w swoich zakładach. Badania termowizyjne obejmują obszerne testy, które wyznaczają kondycję sprzętu bez przerywania jego normalnej pracy. Badania te mają miejsce w czasie pracy fabryki, gdy sprzęt znajduje się pod pełnym obciążeniem. Kamera termowizyjna nie styka się w żaden sposób z badanym obiektem. Jeśli sprzęt znajduje się w niebezpiecznej lokalizacji, to badanie odbywa się z bezpiecznej odległości.
Coroczne wykonywanie badań termowizyjnych zwiększa wydajność sprzętu poprzez precyzyjne wskazanie problemów z instalacją elektryczną na wczesnym etapie. Ponieważ wykonywanie tego testu nie wpływa na działanie sprzętu, firma może realizować bez przerw swoje normalne operacje, jednocześnie zapobiegając kosztownym i nieoczekiwanym wyłączeniom systemów.
David Manney jest administratorem marketingu w firmie L&S Electric. Niniejszy artykuł oryginalnie został opublikowany na blogu L&S Electric Watts New Blog.
Ulepszenie komunikacji pomiędzy pracownikami a kierownictwem
Otwarta komunikacja pomiędzy pracownikami a kierownictwem w temacie potrzeby wprowadzenia i wartości programu zautomatyzowanego zaopatrzenia w materiały, narzędzia i sprzęt jest cechą charakterystyczną skutecznego działania. Na przykład gdy centrum dystrybucji tej firmy podjęło decyzję o przeniesieniu swoich czytników kodów do automatów, zarząd firmy aktywnie promował tę zmianę w okresie kilku miesięcy. Zarząd i pracownicy spotykali się ze sobą na różnych zebraniach, aby wspólnie przedyskutować plan działań i powstałe wątpliwości.
Po zainstalowaniu systemu automatów okazało się, że była to zmiana typu nagłe zerwanie z nałogiem (ang. „cold turkey”). Rankiem pierwszego dnia działania nowego systemu zaopatrzenia kierownicy przybyli wcześniej do zakładu i byli dostępni dla pojawiających się pracowników w celu pomagania im w pracy w nowych realiach. Ten wspólny wysiłek zwrócił się – do końca pierwszego tygodnia funkcjonowania nowego systemu 80% pracowników skutecznie przestawiło się na jego wykorzystywanie, natomiast na koniec pierwszego miesiąca tylko pięciu pracowników nadal wymagało pewnej ilości dodatkowego szkolenia.
Według dyrektora generalnego centrum dystrybucyjnego tej firmy, wdrożenie zautomatyzowanego rozwiązania zaopatrzenia pracowników w narzędzia poprawiło dostępność czytników kodów o 300%, zaś wskaźnik uszkodzeń został zredukowany o 50%. Te ulepszenia były wynikiem zmiany w percepcji pracujących razem ludzi, dotyczącej produktów, których używali w swojej pracy. Dyrektor ten stwierdził, że zautomatyzowane rozwiązania zaopatrzenia „stworzyły poczucie wartości wśród pracujących razem ludzi. Przedtem traktowali oni materiały eksploatacyjne typu rękawice i okulary ochronne, jak artykuły jednorazowego użytku. Automaty dystrybucyjne stworzyły poczucie wartości produktu i doprowadziły do zmiany podejścia pracowników, oraz kontrolowania używanych przez nich materiałów i narzędzi”.
Ta firma z branży kosmetycznej stwierdziła ponadto, że wykorzystanie nowych rozwiązań zaopatrzenia zaoszczędziło jej personelowi nadzoru znaczną ilość czasu. Nowe magazyny karuzelowe przejęły rolę dystrybutorów środków ochrony indywidualnej, pracownicy mają dzięki automatom łatwy dostęp do swoich czytników kodów, zaś personel nadzoru może spędzić więcej czasu na hali fabrycznej i skupić się na realizacji swoich zadań. Tak więc w ciągu dnia pracy „i wilk jest syty i owca cała”.

Optymalizowanie operacji realizowanych w zakładzie
Proces wdrażania zautomatyzowanego rozwiązania zaopatrzenia pracowników w potrzebne im materiały może dostarczyć „widok z lotu ptaka” operacji realizowanych w zakładzie, co pomaga w lepszym zrozumieniu sposobu, w jaki pracownicy zużywają te materiały, oraz może uwydatnić okazje do ulepszeń realizacji procesów lub szkoleń. Zaś zautomatyzowane rozwiązania zaopatrzenia mogą być opracowane dla konkretnych użytkowników w różnych gałęziach przemysłu, oraz dla konkretnych aplikacji.
Umożliwienie firmie pełnego skupiania uwagi na produkcji wyrobów, lub świadczeniu usług jest celem skutecznego programu zautomatyzowanego zaopatrzenia. Redukcja kosztów i jednoczesne zwiększanie wydajności produkcji, oraz utrzymywanie wysokich dochodów jest sprawą nadrzędną dla firmy. Może to pomóc firmom w kontynuacji adoptowania praktyk zarządzania i środowisk produkcyjnych Lean management, oraz pozostawaniu konkurencyjnymi na rynku, szczególnie w USA.
Zautomatyzowane zaopatrzenie pracowników w materiały, narzędzia i środki ochrony indywidualnej jest integralną częścią tej przyszłości, ponieważ pomaga ona zakładom w maksymalnym wykorzystywaniu swojego potencjału.
Megan Mullins, John Morton i Eric King, są pracownikami zespołu d/s Rozwiązań Zarządzania Inwentarzem (Inventory Management Solutions, IMS) firmy Motion Industries z Birmingham (Alabama, USA).