Nowoczesny proces produkcyjny składa się z wielu powiązanych ze sobą elementów. Poruszenie jednego z nich powoduje efekt domina. Jedną z przyczyn niosących takie skutki jest awaria maszyny bądź urządzenia wykorzystywanego w produkcji. Aby zapobiec tego typu sytuacjom należy przeprowadzać systematyczne kontrole stanu technicznego sprzętu, jak też przestrzegać zaleceń eksploatacyjnych i serwisowych producenta.
Oczekuje się, że do 2025 roku światowy przemysł produkcji tworzyw sztucznych metodą wtryskową osiągnie wartość 496 miliardów dolarów. W Europie, która jest jednym z najszybciej rozwijających się regionów, całkowita wartość branży ma w tym samym okresie dojść do 122 miliardów dolarów. Dynamicznie rozwijający się rynek i szybki postęp technologiczny oznaczają duże możliwości wzrostu dla przedsiębiorstw i wiążą się z rozwojem inteligentnych fabryk w ramach Przemysłu 4.0.
Ze względu na wysokie koszty początkowe inwestycji w maszyny oraz bardzo silną konkurencję, firmy muszą przyjąć podejście oparte na całkowitym koszcie użytkowania (TCO), w którym bierze się pod uwagę długoterminowy koszt całkowity. Istotnym elementem takiego podejścia jest wdrożenie skutecznego systemu konserwacji, który pomaga w radzeniu sobie z problemami związanymi z maszynami. Każdy z tych problemów może przyczynić się do awarii lub nieplanowanych przestojów, co w konsekwencji doprowadzi do strat finansowych.
Znaczenie gospodarki smarowniczej
Odpowiednio zorganizowana gospodarka smarownicza i usługi w zakresie konserwacji mogą przyczynić się do ograniczania ryzyka awarii oraz do podniesienia efektywności funkcjonujących maszyn, co jest szczególnie istotne i pomaga w rozwoju firm z branży produkcji tworzyw sztucznych metodą formowania wtryskowego.
Jak wynika z danych Shell, niedostateczna konserwacja może zmniejszyć wydajność fabryki o od 5 do nawet 20%. Odsunięcie jej na dalszy plan może mieć istotne konsekwencje dla wydajności produkcyjnej, a więc i wyniku finansowego. Na przykład wysokowydajny olej hydrauliczny nie tylko mechanicznie rozprowadza energię w obrębie całego układu, lecz zapewnia również ochronę ruchomych części znajdujących się w sercu wtryskarki do tworzyw sztucznych. Z kolei od 50 do 70% awarii urządzeń związanych jest z nieodpowiednim stanem oleju hydraulicznego. Od układów hydraulicznych oczekuje się maksymalnej wydajności podczas pracy pod wysokim ciśnieniem, w zmiennych temperaturach i często w trudnych warunkach. Prawidłowa ochrona tych układów za pomocą skutecznych olejów hydraulicznych może ograniczyć ryzyko awarii i kosztownych napraw, wydłużając tym samym okres użytkowania oraz wpływając pozytywnie na wynik finansowy.
Sięgając po niezbędne środki smarne warto korzystać z rozwiązań przygotowanych przez ekspertów w swojej dziedzinie. Shell oferuje szereg profesjonalnych produktów smarnych przeznaczonych do zastosowań przemysłowych. Wyróżniają się one wysokimi parametrami użytkowymi, w tym pracy pod obciążeniem i odpornością na zużycie. To między innymi olej sprężarkowy Shell Corena czy olej hydrauliczny Shell Tellus S4 VE.
Stosowanie środków smarnych, których jakość jest potwierdzona przez producentów maszyn i urządzeń, przekłada się na niższe koszty eksploatacji uzyskiwane głównie dzięki dłuższej i bezawaryjnej pracy podzespołów oraz niższym kosztom zużycia oleju. Najbardziej znanym produktem tego typu w ofercie Shell jest olej hydrauliczny Shell Tellus S2 MX w lepkościach 32-68. Oferujemy również oleje hydrauliczne które zapewniają 2-3 razy dłuższy czas pracy w porównaniu do obecnie stosowanych olejów mineralnych oraz oszczędności energii nawet do 5%. Są one wytwarzanych z olejów bazowych powstających w procesie GTL, a sprzedawane pod nazwą Shell Tellus S4 VE. Dzięki swoim właściwościom Shell Tellus S4 VE powoduje, że maszyna staje się niemal bezobsługowa a brak jednej wymiany kompensuje często jego koszt
– mówi Cezary Wyszecki, Doradca Techniczny w dziale Sprzedaży Dystrybucyjnej środków smarnych w Shell Polska.
Oleje hydrauliczne o dłuższej żywotności
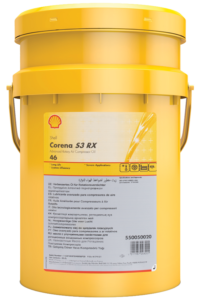
Oleje Shell Tellus S4 VE i ME zostały opracowane w celu zwiększenia efektywności energetycznej układu, w którym są stosowane. Na podstawie kontrolowanych badań stanowiskowych układu hydraulicznego, w którym zastosowano Shell Tellus S4 ME obliczono, że oszczędność energii w jednej wtryskarce może wynieść do 6,4%[1]. Ponadto olej ten ma wydłużoną żywotność, nawet czterokrotnie w porównaniu z konwencjonalnymi olejami z gamy Shell oraz konkurencji, a także może pomóc wydłużyć żywotność urządzeń dzięki doskonałej ochronie pompy hydraulicznej przed zużyciem.
Potwierdzeniem wysokiej skuteczności działania oleju Shell Tellus S2 MX jest przypadek firmy FARPLAS – tureckiego producenta tworzyw sztucznych i wiodącego dostawcy dla największych producentów samochodów na świecie. W swojej fabryce FARPLAS posiada 53 wtryskarki, większość produkcji ENGEL. W maszynach stosowano olej hydrauliczny ISO VG 46. Podczas ich pracy pojawiały się problemy techniczne związane ze stosowaniem środków smarnych. Specjaliści Shell przeanalizowali te problemy i zasugerowali zmianę dotychczasowego oleju hydraulicznego na olej Shell Tellus S2 M/MX 46, zapewniający wysoką odporność na utlenianie i degradację termiczną oraz dobrą ochronę przeciwzużyciową, jak też kompatybilność z uszczelnieniami. Zespół Shell polecił także korzystanie z usługi Shell LubeAnalyst, która pomogłaby w monitorowaniu stanu oleju i sprzętu podczas pracy.
Rzeczywiste korzyści dzięki rozwiązaniom Shell

Dzięki zastosowaniu oleju Shell Tellus S2 M/MX oraz korzystaniu z usługi Shell LubeAnalyst przedsiębiorstwu FARPLAS udało się ograniczyć liczbę problemów technicznych związanych ze środkami smarnymi oraz wydłużyć okresy między wymianami oleju bez obniżenia poziomu zabezpieczenia maszyn. Przedsiębiorstwo odnosi korzyści dzięki zmniejszeniu kosztów utrzymania oraz wzrostowi mocy produkcyjnej, ponieważ wydłużył się okres pracy maszyn pomiędzy wymianami oleju i są one mniej narażone na nieplanowane przestoje. W związku z tym w skali roku przedsiębiorstwo FARPLAS odnotowało łączne oszczędności w kwocie 69 100 dolarów[2].
Oleje sprężarkowe do stosowania w przemyśle
Kolejnym ważnym środkiem smarnym w procesie utrzymania ruchu są oleje sprężarkowe. Shell jest znanym na całym świecie producentem wysokiej jakości olejów Shell Corena, które również pozwalają na obniżanie kosztów i maksymalizacji wydajności. Gama tych produktów powstała przy ścisłej współpracy z klientami i producentami urządzeń. Należy do nich Shell Corena S3 RX – pierwszy na rynku syntetyczny olej sprężarkowy wytwarzany w technologii GTL.
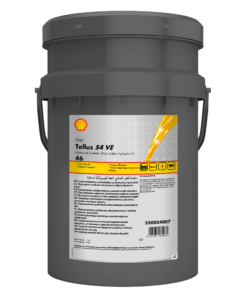
Shell Corena S3 RX zalecany jest do różnorodnych sprężarek wykorzystywanych między innymi w przemyśle przetwórczym, papierniczym, tekstylnym czy chemicznym. Potwierdzone testami i badaniami właściwości ponad dwukrotnie wydłużają interwały wymiany[3] oraz generują trzy razy mniej zanieczyszczeń[4], gwarantując nawet osiem tysięcy godzin bezpiecznej pracy[5]. W efekcie, w porównaniu do oleju mineralnego, ograniczona zostaje konieczność dolewek. Co więcej, Shell Corena S3 RX jest kompatybilny z innymi olejami, a jego stosowanie nie wymaga wcześniejszego płukania układu. Środek ten spełnia wymagania wielu producentów sprężarek.
Szeroka gama naszych środków smarnych pozwala dostosować właściwości użytkowe do konkretnych zastosowań. Wszystkie, zgodnie ze swoim przeznaczeniem, spełniają wymagania producentów maszyn z układami hydraulicznymi oraz wykorzystującymi stacjonarne i mobilne sprężarki powietrza. Kluczowe pozostaje jedno – właściwie dobrane oleje hydrauliczne Tellus i sprężarkowe Corena gwarantują ograniczenie całkowitych kosztów użytkowania (TCO), co przekłada się na efektywność prowadzonej działalności – podkreśla Cezary Wyszecki, Doradca Techniczny w dziale Sprzedaży Dystrybucyjnej środków smarnych w Shell Polska.
[1] Rzeczywiste oszczędności zależą od zastosowania, aktualnie stosowanego oleju, procedur konserwacji, stanu urządzenia, warunków eksploatacji i intensywności zużycia mocy hydraulicznej.
[2] Wskazane oszczędności są charakterystyczne dla dnia obliczeniowego i wymienionego zakładu. Powyższe obliczenia mogą się różnić w zależności od lokalizacji i czasu oraz zależą, np. od zastosowania, warunków pracy, aktualnie stosowanych produktów, stanu sprzętu oraz praktyk konserwacyjnych.
[3] W porównaniu z olejami mineralnymi w testach w temperaturze 120° C przy użyciu sprężarek Hydrovane 22, które przyspieszają starzenie się oleju.
[4] Przemysłowe testy stabilności termicznej z metalami katalitycznymi w temperaturze 135° C przez 168 godzin (ASTM D2070).
[5] W oparciu o wewnętrzne, rygorystyczne testy Shell