Uzyskanie statusu neutralności klimatycznej stało się powszechnie znaną mantrą dla wielu działów ds. zrównoważonego rozwoju w przedsiębiorstwach przemysłowych. W dążeniu do tego celu mogą pomóc odpowiednie instalacje sprężonego powietrza w fabrykach.
Spostrzeżenia na temat zrównoważonego rozwoju
- Osiągnięcie celów zrównoważonego rozwoju może być realne poprzez podjęcie różnych działań mających na celu redukcję lub eliminację emisji dwutlenku węgla. Instalacje sprężonego powietrza są odpowiedzialne za zużycie niemal jednej trzeciej energii elektrycznej przez typowy zakład przemysłowy i dlatego są one kluczem do uzyskania neutralności węglowej.
- Dokonywanie przeglądów kompresorów powietrza, stosowanie narzędzi do oszczędzania energii, wykorzystywanie automatyki sterującej oraz ulepszanie istniejącego sprzętu to przykłady strategii działań, które mogą wdrożyć firmy przemysłowe w celu osiągnięcia neutralności klimatycznej
Firma uzyskuje status neutralności klimatycznej, gdy ilość emitowanego przez jej zakłady dwutlenku węgla (CO2) jest kompensowana przez zmniejszanie emisji tego gazu wszędzie w produkcji, używaniu lub utylizacji wyrobu. Obecnie uzyskanie neutralności klimatycznej czy też wszelkie działania na rzecz klimatu na wyższym poziomie nie są już dłużej jakimś drugorzędnym problemem firmy. Są one niezbędne, aby zapewnić ochronę naszej planety i egzystencji.
Dla firm przemysłowych znajdowanie sposobów na rozpoczęcie lub kontynuowanie ograniczania albo kompensowania emisji dwutlenku węgla jest czymś więcej niż tylko uzyskaniem przewagi nad konkurencją. Instalacje sprężonego powietrza odpowiadają za 30% lub więcej całkowitej energii elektrycznej zużywanej przez typowy zakład produkcyjny. Są one jednymi z największych pojedynczych odbiorników energii, a sprężone powietrzne jest przez wielu traktowane jako czwarte medium przemysłowe.
Z tego powodu instalacja pneumatyczna jest w zakładzie przemysłowym ważnym obszarem pod względem neutralności klimatycznej. Firma powinna zapewnić, że instalacja ta pracuje tak efektywnie, jak to tylko jest możliwe. Dalej prezentujemy 10 sposobów na poprawę efektywności instalacji sprężonego powietrza, co pomoże firmie przybliżyć się do celu, jakim jest uzyskanie certyfikatu neutralności klimatycznej.
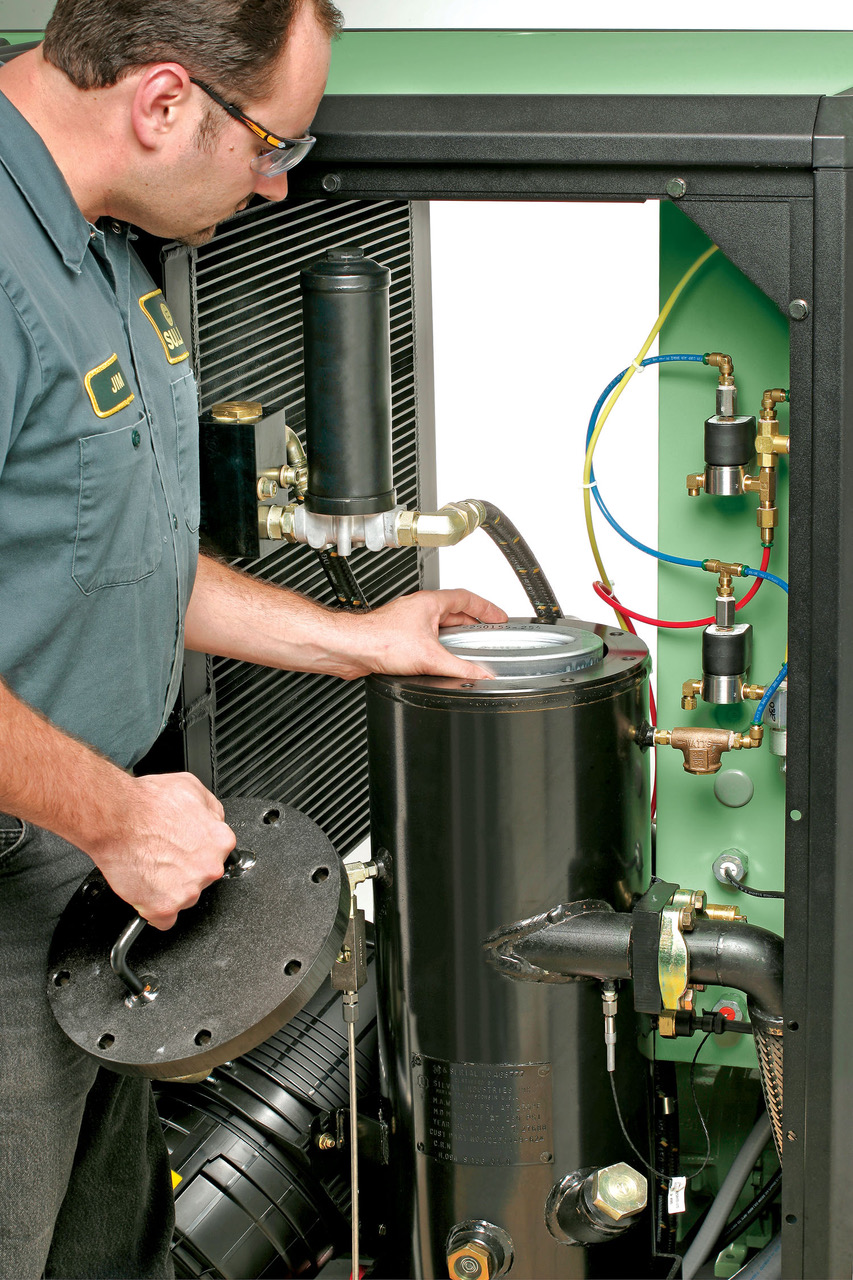
1. Przegląd instalacji sprężonego powietrza w zakładzie
Działania rozpoczynamy od wykonania przeglądu technicznego instalacji sprężonego powietrza, aby upewnić się, że jest ona wykorzystywana efektywnie. Każdy kompresor powietrza pracuje z największą sprawnością energetyczną, gdy jest w pełni obciążony. Doświadczony specjalista od przeglądów instalacji pneumatycznych potrafi stwierdzić, czy dany zakład przemysłowy posiada kompresor o mocy właściwie dobranej do potrzeb oraz udzielić porady na temat tego, czy kompresor ten jest najbardziej wydajny. Właściwy dobór kompresora do instalacji, takiego jak wyposażony w napęd o zmiennej prędkości (falownik) czy technologię elektronicznego zaworu spiralnego, może oznaczać znaczne oszczędności zużywanej energii (więcej na ten temat w dalszej części artykułu). Specjalista od przeglądów może też wykonać kontrolę instalacji pod względem nieszczelności. Jest ona ważna, ponieważ na przykład szczelina o długości 0,25 cala (6,35 mm) w rurze transportującej powietrze pod ciśnieniem 125 psi (8,62 bar) może kosztować firmę od 2500 do nawet 8000 USD rocznie za niepotrzebnie zużytą energię elektryczną. Dobór kompresora o właściwej mocy i właściwego typu oraz usunięcie wszelkich wycieków powietrza z instalacji może często oznaczać, że inwestycja w nową instalację lub modernizację istniejącej zwróci się w czasie zaledwie sześciu miesięcy.
2. Odzyskiwanie ciepła ubocznego powstającego w kompresorach
W kompresorach wykorzystuje się dodatkowo takie narzędzia jak rozwiązanie (dla) efektywności energetycznej. Polega ono na wykorzystaniu ciepła ubocznego, powstającego podczas sprężania powietrza, do ogrzewania fabryki w okresie zimowym. Dodanie do zakładu systemu kanałów wentylacyjnych, w których płynie powietrze podgrzane przez pracujący kompresor, jest doskonałym sposobem zaoszczędzenia na rachunkach za energię elektryczną. W okresie letnim lub w przypadku zakładów zlokalizowanych w cieplejszym klimacie to ciepło uboczne z kompresora może być odprowadzone na zewnątrz fabryki, co wspomaga utrzymanie chłodu wewnątrz. Inne narzędzia wspomagające redukcję emisji CO2 to np. system odzysku energii. Jego działanie polega na zastosowaniu wymienników ciepła, pobierających ciepło pochodzące z cyklu sprężania powietrza i wykorzystywania go do ogrzewania kotłów lub wody technologicznej. Ta technologia pozwala wykorzystać w przybliżeniu 85% ciepła powstającego w kompresorze, dzięki czemu zakład może szybko uzyskać oszczędności energii.
3. Modernizacja technologii wykorzystywanej w zakładzie
Wytwarzanie sprężonego powietrza tylko w takiej ilości, jakiej potrzebuje dana fabryka oraz wyeliminowanie niepotrzebnej pracy kompresorów jest czułym miejscem w każdej instalacji pneumatycznej. Aby uzyskać tę równowagę, instalacja wymaga kompresora z elektronicznym zaworem spiralnym lub napędem o zmiennej prędkości obrotowej (VSD). Obie te technologie wykazują doskonałą efektywność w systemach o zmiennym zapotrzebowaniu na sprężone powietrze, jednak przed ich wykorzystaniem powinniśmy skonsultować się z ekspertem od instalacji pneumatycznych. Może on doradzić, która z tych technologii będzie lepsza w danym zakładzie. W przypadku napędów VSD zakres regulacji prędkości obrotowej jest większy, dzięki czemu kompresor może obsługiwać instalację o większych wahaniach zapotrzebowania na sprężone powietrze. Natomiast elektroniczny zawór spiralny jest lepszym wyborem dla środowisk zanieczyszczonych, w których napęd VSD uległby uszkodzeniu, lub dla zakładów, w których zapotrzebowanie na sprężone powietrze waha się od 45 do 100%. Ponadto wiele stanów USA oferuje rabaty na energię dla firm wykorzystujących napędy VSD, co może być czynnikiem decydującym o ich wyborze.
4. Wykorzystanie sterowników logicznych oraz rozdziału obciążeń kompresorów
W przypadku zakładów wykorzystujących więcej niż 1 kompresor powietrza (od 2 do 16) odpowiedni rozdział ich obciążeń jest doskonałym sposobem zwiększenia efektywności energetycznej. Dzięki logice sterującej taki system automatycznie wyłącza i wyłącza kompresory – w zależności od zapotrzebowania na sprężone powietrze. Oprogramowanie sterownika odnajduje najbardziej efektywny sposób dostarczania sprężonego powietrza do instalacji i „wie”, które z kompresorów ma wyłączyć, a które pozostawić włączone tak, aby utrzymywać maksymalną efektywność.
5. Zautomatyzowanie monitorowania procesów
Zautomatyzowany monitoring procesów realizowanych w zakładzie może dostarczyć bardzo wiele użytecznych informacji na temat efektywności oraz stanu technicznego systemu sprężonego powietrza. Na przykład monitoring temperatury powietrza wylotowego z kompresora może wykrywać powstałe problemy. Taki system wysyła sygnał alarmowy, gdy separatory zaczynają się zapychać lub gdy powstaje potrzeba dokonania czynności serwisowych przez techników, co pozwala na utrzymanie pracy kompresora z maksymalną wydajnością.
6. Kontrolowanie osuszaczy, filtrów i zapychania się kompresorów
Jeśli dany zakład przemysłowy nie posiada zautomatyzowanego systemu monitorującego instalację sprężonego powietrza, to powinien opracować sekwencyjną listę kontrolną w celu zapewnienia, że kompresor codziennie pracuje na swoim optymalnym poziomie. Powinniśmy sprawdzać filtry i manometry ciśnienia różnicowego, aby się zorientować, czy nie powstały żadne zapchania wpływające negatywnie na funkcjonowanie maszyny. Praca kompresora z wysoką efektywnością oznacza oszczędności energii.
7. Dobór prawidłowego orurowania dla instalacji sprężonego powietrza
Rury instalacji sprężonego powietrza wykonane z aluminium mają kilka zalet w porównaniu do rur wykonanych z żeliwa, stali czy innych materiałów żelaznych. Jedną z nich, wcale nie najmniej znaczącą, jest lepszy przepływ powietrza. Gdy na powierzchni rur powstaje lub gromadzi się nalot – szczególne w przypadku żeliwa, które może rdzewieć i oddziaływać na przepływające powietrze – istnieje ryzyko zwiększenia oporów przepływu powietrza (współczynnika tarcia) oraz zmniejszania się światła rury, co oznacza straty energii. Poza tymi stratami zanieczyszczenia sprężonego powietrza w systemie dystrybucji produktami korozji mogą stworzyć konieczność częstszej wymiany filtrów lub, co gorsza, ryzyko dostania się zanieczyszczeń do sprzętu czy wytwarzanego produktu. Pewne rury lub ich osprzęt mogą także nie być kompatybilne z pewnymi środkami smarnymi stosowanymi w kompresorach. Zmiana natężenia przepływu powietrza w takim nieprawidłowym orurowaniu systemu może być niewielka, jednak w miarę upływu czasu straty energii mogą rosnąć.
8. Eliminacja strat ciśnienia powietrza za pomocą odpowiednich osuszaczy
Firmy przemysłowe mogą dosłownie wyrzucać w błoto nakłady na zwiększenie efektywności instalacji pneumatycznych, jeśli instalacje te nie są wyposażone w odpowiednie osuszacze sprężonego powietrza. Osuszacze bezstratne nie pozwalają na spadek ciśnienia powietrza w cyklu zbierania i spuszczania kondensatu. Podczas gdy jest to zadziwiająco znaczący obszar strat efektywności, osuszacz jest tanim i łatwym w eksploatacji środkiem uzyskania oszczędności energii w instalacji pneumatycznej.
9. Przedłużanie okresu pomiędzy serwisowaniem kompresora dzięki odpowiednim środkom smarnym
Co prawda niektórzy uważają, że wszystkie środki smarne do kompresorów powietrza są takie same, ale nie jest to do końca prawdą. Cena gra tu rolę. Zakup właściwego środka smarnego wyższej jakości – przeznaczonego do kompresora danego typu – może mieć podstawowe znaczenie. Prawidłowy smar może wydłużyć okres pomiędzy kolejnymi konserwacjami kompresora, jednocześnie zmniejszając ślad węglowy, ponieważ nie jest konieczna częsta wymiana oleju.
10. Nabywanie sprzętu wysokiej jakości
Jednym z najlepszych sposobów działania na rzecz środowiska jest nabywanie maszyn, które będą mogły być eksploatowane przez długi czas. Co prawda firmy mogą zaoszczędzić niewielkie kwoty na początku, kupując kompresor niższej jakości, jednak będą musiały potem ponosić dodatkowe koszty na naprawy oraz koszty wynikające z mniejszej efektywności energetycznej i żywotności takiego sprzętu.
Ponadto w przypadku konieczności wykonania napraw kompresorów podstawą jest wybór komponentów pochodzących od producenta wyposażenia oryginalnego (OEM). Nowoczesne kompresory powietrza są projektowane drobiazgowo, z nastawieniem na wysoką efektywność energetyczną, jednak odpowiednie parametry maszyn są zachowane tylko wtedy, gdy są w nich użyte części zaprojektowane dla konkretnych typów tych maszyn. Nie możemy dawać się omamić pokusami nabycia tańszych podzespołów – nie będą one trwałe i maszyna nie uzyska przy nich odpowiedniego poziomu efektywności.
Uzyskanie statusu neutralności klimatycznej to długa, ale ważna droga. Odnajdowanie oszczędności w każdym aspekcie działalności firmy przemysłowej jest niezbędne. Na szczęście istnieją pewnie działania, jakie firmy mogą obecnie podjąć, aby zapewnić, że instalacja sprężonego powietrza w ich zakładzie działa tak efektywnie jak to możliwe oraz utrzymywać to czwarte medium w ryzach.
1 węglowej; ang. carbon neutrality
2 ang. energy efficient solution, EES
3 ang. energy recovery system, ERS
4 ang. turndown
5 ang. electronic spiral valve; np. opracowany przez firmę Sullair zawór sterujący obciążeniem bloku śrubowego – w zależności od zapotrzebowania na sprężone powietrze
Peter Modrow pracuje jako starszy menedżer produktu w firmie Sullair, LLC. Zajmuje się stacjonarnymi kompresorami powietrza. Peter Modrow rozpoczął pracę w Sullair w 2020 r. jako menedżer produktów z branży uzdatniania sprężonego powietrza, przynosząc ze sobą ponad 10-letnie doświadczenie w opracowywaniu produktu i wprowadzaniu na rynek. Obecne stanowisko związane z kompresorami stacjonarnymi zajmuje od sierpnia 2022 roku. Peter Modrow posiada tytuł magistra inżyniera mechanika, uzyskany na politechnice Texas Tech University w Lubbock (stan Texas).