Poznanie parametrów napędów o zmiennej częstotliwości (VFD), takich jak prąd termiczny, częstotliwość modulacji PWM oraz innych, może pomóc inżynierom i technikom pracującym w zakładach przemysłowych uzyskać większą sprawność tych napędów w wielu różnych zastosowaniach.
W ciągu ostatniego stulecia silniki elektryczne stały się wszechobecne w napędach wielu urządzeń przemysłowych, w tym pomp, wentylatorów i sprężarek. W ciągu ostatnich kilku dziesięcioleci napędy o zmiennej częstotliwości (falowniki, inwertery; napędy VFD) stały się narzędziem o potężnych możliwościach zmniejszania zużycia energii i optymalizacji sterowania silnikami elektrycznymi, które jest obecnie powszechnie wykorzystywane.
Podczas konfigurowania napędów VFD w automatyce przemysłowej inżynierowie i technicy przeważnie współpracują z wykonawcami instalacji elektrycznej w zakładzie, aby się upewnić, że każdy napęd VFD odpowiednio steruje swoim silnikiem podczas uruchamiania tej instalacji. Jednak wykonawcy prac elektroinstalacyjnych często nie są ekspertami w zakresie optymalizacji napędu pod kątem konkretnego silnika i potrzeb jego aplikacji. Większość nowoczesnych napędów VFD to złożone urządzenia sterujące, posiadające wiele parametrów, które można precyzyjnie dostroić w celu uzyskania jeszcze większych korzyści dla danej aplikacji.
Osiem parametrów napędów o zmiennej częstotliwości do wykorzystania w automatyce przemysłowej
Istnieje osiem parametrów napędów o zmiennej częstotliwości, które często nie są brane pod uwagę podczas ich instalowania, a często można je zoptymalizować, aby wprowadzić szereg ulepszeń w sterowaniu silnikami elektrycznymi.
W przypadku wszystkich ustawień omawianych w tym artykule powinniśmy najpierw sprawdzić, czy dany parametr odpowiada temu, co jest podane w dokumentacji producenta, zwracając szczególną uwagę na jednostki miar.
Parametr 1: Prąd termiczny
Prąd termiczny jest parametrem wskazującym maksymalny dopuszczalny prąd wyjściowy napędu VFD, który różni się od jego znamionowego prądu wyjściowego. Podczas gdy prąd znamionowy odpowiada mocy znamionowej (i napięciu znamionowemu) oraz oznacza maksymalne natężenie prądu dopuszczalne dla silnika w długim okresie, to prąd termiczny oznacza prąd o większym natężeniu, który może płynąć krótkotrwale, umożliwiając napędowi VFD bezpieczne dostarczenie mocy większej niż standardowa moc znamionowa silnika.
Ustawiona wartość prądu termicznego informuje napęd VFD, jak dużą „dodatkową” moc może rozwinąć silnik i nadal pracować bez awarii wywołanej przegrzaniem. Gdy ten limit zostanie przekroczony, VFD może wyzwolić zabezpieczenie jeszcze przed wystąpieniem przeciążenia silnika, chroniąc go przed awarią termiczną. Podczas konfigurowania parametrów napędu dla prądu silnika użytkownicy mogą znaleźć wartość prądu znamionowego i współczynnik przeciążalności SF, podany na tabliczce znamionowej maszyny. Pomnożenie wartości prądu znamionowego przez współczynnik SF daje nam wartość prądu termicznego w amperach.
Parametr 2: Częstotliwość modulacji szerokości impulsów (PWM)
Każdy napęd VFD zasilający silnik prądu przemiennego działa następująco: napięcie przemienne z sieci jest konwertowane na napięcie stałe, które z kolei jest modulowane, tworząc napięcie przemienne. Modulacja ta odbywa się poprzez szybkie włączanie i wyłączanie napięcia stałego w celu utworzenia fali napięcia przemiennego. Napęd VFD reguluje amplitudę i częstotliwość tej fali, tak aby zasilany silnik wirował z wymaganą prędkością. Ustawiana przez użytkownika częstotliwość modulacji szerokości impulsów PWM, czyli częstotliwość kluczowania (przełączania tranzystorów mocy napędu), wpływa na kształt fali napięciowej (mniej lub bardziej łagodny) doprowadzanej do silnika.
Gdy częstotliwość modulacji PWM nie jest zoptymalizowana dla silnika i jego aplikacji, odprowadzanie ciepła wytwarzanego przez silnik oraz jego napęd nie są zrównoważone. Jeśli częstotliwość modulacji PWM jest zbyt niska, silnik będzie się szybciej nagrzewał, co będzie sygnalizowane jego piskiem. Przegrzewanie może w końcu doprowadzić do uszkodzenia izolacji uzwojeń i/lub wżerów w łożyskach. Z kolei wysoka częstotliwość modulacji powoduje większe straty mocy w napędzie, co ostatecznie prowadzi do jego przegrzewania i skrócenia żywotności.
Podwyższona częstotliwość modulacji PWM może również zwiększyć powstawanie fal odbitych pomiędzy silnikiem a napędem, co może spowodować zwiększone indukowanie się napięcia wzdłuż walu silnika i przepływ prądów łożyskowych, a to w konsekwencji powoduje wżery w łożyskach silnika i zwarcia doziemne w napędzie. Poprzez prawidłowe, dokładne dostrojenie częstotliwości modulacji PWM użytkownicy mogą zrównoważyć odprowadzanie ciepła z silnika oraz napędu i w konsekwencji wydłużyć żywotność obydwu tych urządzeń.
Parametr 3: Czas hamowania
Jest to parametr, który określa czas, jakiego VFD będzie potrzebował na zahamowanie silnika. Dłuższy czas hamowania oznacza dłuższą rampę czasową (zmniejszanie przez VFD częstotliwości do zera) dla pełnego zatrzymania silnika. Wielu instalatorów napędów wie, że należy zoptymalizować czas przyspieszania, aby zapobiec problemom z nadmiernym prądem przy rozruchu, natomiast czas hamowania jest często przez nich pomijany.
Ustawianie czasu hamowania jest ważne dla zapobiegania przepięciom, które mogą powstać, gdy od silnika zostanie odłączone zasilanie, a bezwładność obciążenia mechanicznego maszyny będzie powodowała kontynuowanie wirowania. Powoduje ono generowanie przez silnik napięcia, które jest doprowadzane z powrotem do przemiennika, powodując jego uszkodzenie. W tym przypadku odpowiedni czas hamowania zmniejszy wartość napięcia wytwarzanego przez silnik podczas wybiegu i zapobiegnie uszkodzeniu VFD. Na przykład, jeśli mamy silnik sterujący wentylatorem, a hamowanie do zatrzymania wentylatora trwa 10 sekund, to w napędzie powinniśmy ustawić właśnie taki czas hamowania, aby przedłużyć żywotność silnika. Powinniśmy jednak pamiętać, że jeśli ze względu na proces technologiczny lub bezpieczeństwo wymagane jest szybkie zatrzymanie silnika, to może być tu wymagany dodatkowy sprzęt i powinniśmy skonsultować się w tej sprawie z odpowiednimi ekspertami.
Parametr 4: Minimalna prędkość robocza
Minimalna prędkość robocza to wartość zadana prędkości obrotowej, zwykle obliczana jako procent prędkości maksymalnej, poniżej której napęd wyłączy silnik. Ponieważ większość silników jest chłodzona za pomocą wewnętrznego wentylatora, którego prędkość obrotowa jest bezpośrednio powiązana z prędkością silnika, ustawienie minimalnej prędkości roboczej jest ważne, aby zapobiec przegrzaniu silnika, które może wystąpić przy niskich prędkościach. Na przykład, jeśli minimalna prędkość robocza zostanie ustawiona na 10%, a ktoś wprowadzi do VFD wartość referencyjną prędkości równą 5%, to napęd VFD nie będzie pozwalał na pracę silnika. Miejmy na uwadze, że integrator systemów sterowania powinien się upewnić, że zostało to uwzględnione przy wdrażaniu wszelkich konfiguracji współpracujących z VFD sterowników programowalnych (PLC), takich jak algorytmy sterowania proporcjonalno-różniczkująco-całkującego (PID), w których napęd jest sterowany za pomocą zmiennej sterującej (CV).
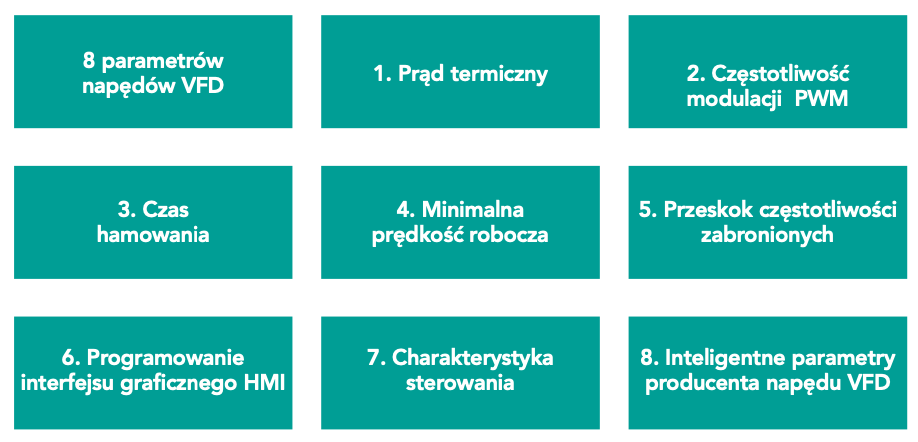
Parametr 5: Przeskok częstotliwości zabronionych
Funkcja przeskoku częstotliwości zabronionych składa się zazwyczaj z kilku parametrów. Parametry przeskoku częstotliwości zabronionych oznaczają przedziały częstotliwości, przy których napęd VFD nie będzie uruchamiać swojego obciążenia. Wiele systemów mechanicznych posiada częstotliwość lub częstotliwości, przy których system taki będzie ulegał nadmiernym wibracjom, co może doprowadzić do uszkodzeń. Na przykład, jeśli częstotliwość rezonansowa systemu wynosi 40 Hz, to silnik pracujący z prędkością obrotową 40 Hz będzie powodował nadmierne wibracje tego systemu, które mogą powodować poluzowanie jego elementów. Przy prawidłowym ustawieniu wartości przeskoku częstotliwości zabronionych napęd VFD pominie przy zmianach częstotliwości napięcia wyjściowego wartość 40 Hz i zapobiegnie tym wibracjom. Chociaż niektórzy producenci urządzeń mogą zidentyfikować ich częstotliwości rezonansowe, to są one częściej znajdowane przez doświadczenie. Mogą istnieć dodatkowe powiązane parametry wskazujące na pasmo częstotliwości, dlatego też istnieje pewien zakres częstotliwości, w którym VFD nie będzie pracował w ogóle.
Parametr 6: Programowanie ustawień interfejsu graficznego
Każdy z głównych producentów napędów VFD dodaje do nich mały, programowalny moduł interfejsu operatorskiego (HMI) z wyświetlaczem graficznym LCD. Chociaż ustawienia domyślne tego modułu mogą być odpowiednie dla niektórych zastosowań, to jest on zazwyczaj programowalny w celu wyświetlania różnych wartości na wyświetlaczu lub dostosowania do preferencji użytkownika. Poniżej omówimy trzy najważniejsze ustawienia interfejsu: wartość wyświetlania, jednostki wyświetlania i hasło, choć nazwy tych parametrów mogą się różnić w zależności od producenta napędu VFD.
1. Wartość wyświetlana
Większość interfejsów operatorskich VFD posiada domyślne ustawienie fabryczne wyświetlania prędkości obrotowej silnika. W niektórych zastosowaniach lepiej sprawdza się jednak wyświetlanie innej wartości. Na przykład w wielu aplikacjach związanych z mieszaniem moc silnika zmienia się wraz ze zmianą lepkości substancji mieszanej. Wyświetlanie aktualnej wartości mocy silnika na interfejsie HMI pozwala operatorowi zorientować się, w jakim stopniu danych produkt jest wymieszany, bez konieczności pójścia do sterowni i wyświetlenia sobie odpowiedniego ekranu systemu sterowania SCADA. Najlepszym sposobem na określenie idealnej wielkości wyświetlanej na interfejsie operatorskim jest znajomość realizowanego procesu, opcji oraz preferencji operatorów fabryki. W zależności od producenta napędu VFD interfejs HMI może także wyświetlać częstotliwość, prąd, komunikaty niestandardowe lub jakąś wartość obliczoną.
2. Jednostki wielkości wyświetlanych
Wartość interfejsu HMI może być zoptymalizowana tylko wtedy, gdy właściwe informacje o realizowanym procesie są wyświetlane we właściwych jednostkach. W niektórych przypadkach jest to po prostu realizowane przez zmianę ustawień interfejsu, aby wyświetlacz pokazywał wartości w jednostkach metrycznych, takich jak litry/min zamiast anglosaskich, takich jak gal/min. W innych przypadkach może to być dokonywane przez dostosowanie wyświetlanych wartości do ekranów systemów SCADA oraz interfejsów HMI, aby uzyskać prędkość obrotową w procentach zamiast w obr./min (RPM).
3. Hasło
Hasło i powiązane z nim ustawienia można wykorzystać do ograniczenia działania VFD z poziomu interfejsu operatorskiego. Chociaż ograniczenie działania VFD może być podyktowane względami bezpieczeństwa, istnieją również powody operacyjne, aby ograniczyć sterowanie silnikiem. Na przykład może nie być pożądane zaskoczenie operatora w sterowni przez włączenie silnika za pomocą interfejsu HMI na obiekcie czy w terenie. Ustawienia haseł w napędach wielu producentów mogą zablokować dostęp nieautoryzowanym użytkownikom, zachowując widoczność parametrów wyświetlanych na ekranie. Wyznaczenie najlepszego wykorzystania tych środków bezpieczeństwa najlepiej jest wykonać we współpracy z personelem zakładu odpowiedzialnym za bezpieczeństwo, ochronę i operacje, w tym inżynierskim.
Parametr 7: Charakterystyka i cztery najczęściej stosowane ustawienia sterowania
Charakterystyka sterowania to grupa parametrów, które pomagają określić, jak napęd VFD będzie zmieniać częstotliwość i moc, aby utrzymać zaprogramowane nastawy w napędach wysokiej klasy. Może to być istotne dla zapewnienia, że odpowiednia wartość momentu obrotowego silnika zostanie zastosowana w odpowiednim czasie dla danej aplikacji. Nie powinniśmy tego mylić z ustawieniami tych wartości regulowanych, które są zawsze konfigurowane podczas uruchamiania napędu. Większość producentów VFD umożliwia kilka różnych ustawień charakterystyki sterowania, aby pomóc użytkownikom w konkretnej aplikacji, przy czym cztery najczęściej spotykane to:
- Sterowanie skalarne U/f (U do f; ang. V/Hz). Utrzymywany jest stały stosunek napięcia do częstotliwości. Dobrze nadaje się do silników napędzających wentylatory i pompy, gdzie przepływ płynu jest ważniejszy niż jego ciśnienie. Utrzymywany jest pełny zakres momentu obrotowego w granicach około ½ poślizgu silnika (różnicy prędkości obrotowych pól magnetycznych stojana i wirnika), ale może nie być w stanie utrzymać momentu obrotowego dla częstotliwości poniżej 2 Hz.
- Sterowanie wektorowe bezczujnikowe (ang. sensor-less vector; SV). Zapewnia wyższy moment rozruchowy i regulację prędkości w granicach ¼ poślizgu silnika. Dobrze nadaje się do silników napędzających pompy głębinowe i zastosowań o wysokim stałym momencie obrotowym (przy tej metodzie sterowania należy stosować autotuning, czyli automatyczne rozpoznawanie parametrów silnika przez napęd).
- Sterowanie wektorowe w pętli otwartej. Ulepsza sterowanie U/f poprzez zapewnienie kontroli zarówno momentu, jak i kąta obrotu. Dzięki pomiarom strumienia magnetycznego silnika oraz położenia jego wału metoda ta zapewnia bardziej precyzyjną kontrolę prędkości i momentu obrotowego silnika.
- Sterowanie wektorowe w pętli zamkniętej. Ta metoda wykorzystuje enkoder zamontowany na silniku, który dostarcza informacje o położeniu wału i prędkości obrotowej silnika z powrotem do napędu. Dzięki temu silnik może uzyskać pełny moment obrotowy przy zerowej prędkości. Metoda idealna dla silników stosowanych w dźwigach i podnośnikach.
Niektóre z powyższych metod sterowania oddziałują na siebie wzajemnie, a inne wykluczają użycie różnych parametrów. Na przykład wprowadzenie nastaw regulacji momentu obrotowego wyklucza możliwość autotuningu.
Parametr 8: „Inteligentne” parametry, specyficzne dla producenta
Obecnie wiele napędów VFD ma szereg „inteligentnych” funkcji, które mogą pomóc w dalszej poprawie sprawności oraz żywotności silnika. Ponieważ jednak funkcje te różnią się w zależności od napędu, w praktyce często wiele z nich nie jest w pełni wykorzystywanych. Na przykład niektóre napędy posiadają czujniki monitorujące to, ile mocy jest potrzebne do uzyskania określonej prędkości obrotowej przez silnik. Podczas pierwszej konfiguracji napędu VFD można ustalić podstawową krzywą mocy i wykorzystać ją do zaprogramowania ostrzeżenia o konieczności przeprowadzenia konserwacji, gdy jakieś łożysko zaczyna się już zużywać, co objawia się większą mocą potrzebną do uzyskania tej samej prędkości.
Niektóre napędy mogą również mieć możliwość wykonywania określonych działań na podstawie czynników wyzwalających. Na przykład napęd podłączony do silnika pompy może na podstawie zwiększonej mocy wymaganej do przemieszczenia płynu przez rurę wykryć, że rurociąg zaczyna się blokować. Taki „inteligentny” napęd może być zaprogramowany tak, aby tymczasowo zwiększył moc silnika pompy w celu oczyszczenia rurociągu.
Jeśli te specyficzne dla producenta napędu VFD inteligentne funkcje są zrozumiałe i prawidłowo wdrożone, możliwa jest poprawa efektywności energetycznej oraz proaktywne wykonywanie niektórych zadań konserwacyjnych. Gdy te funkcje są ustawione w połączeniu z odpowiednią charakterystyką sterowania z omówionych powyżej, użytkownicy mogą nawet uzyskać więcej mocy z napędu, niezależnie od tego, czy pracuje on na niskim, czy wysokim poziomie.
1 oryg. engineering units, angielskie jednostki inżynieryjne
2 ang. full load amps; FLA
3 motor service factor; wg NEMA krotność prądu znamionowego, którą silnik może wytrzymać przez krótki czas podczas normalnej pracy
4 ang. frequency jump
Kurt Niehaus, menedżer sprzedaży, Will Young, inżynier w firmie Applied Control Engineering będącej partnerem CFE Media and Technology ds. treści. Artykuł ten pojawił się na stronie internetowej Applied Control Engineering w dwóch częściach.