Pomiary w systemach sprężonego powietrza dzielimy na dwie grupy. Pierwsza z nich to pomiary parametrów jakości, druga to pomiary „energetyczne”: przepływu (wytworzenia, zużycia), ciśnienia, strat (nieszczelności w instalacji) oraz efektywności urządzeń wytwarzających i uzdatniających sprężone powietrze.
Jakość sprężonego powietrza definiuje norma ISO 8573-1:2010, która określa: zawartość cząstek stałych, ciśnieniowy punkt rosy oraz resztkową zawartość oleju (węglowodorów). Każdy z tych parametrów jest zmienny w czasie dlatego stosując odpowiednie urządzenia /czujniki pomiarowe oraz rejestrator danych, możemy na bieżąco monitorować i kontrolować jakość sprężonego powietrza.
Daje to możliwość szybkiej reakcji w przypadku zaobserwowania niewłaściwych parametrów i pozwala zapobiec wystąpieniu różnorakich problemów.
Niezależnie od rodzaju instalacji oraz wymaganej jakości sprężonego powietrza, począwszy od tzw.: „powietrza technicznego” w klasie 2:4:2, skończywszy na powietrzu w klasie 1:1:1, wykorzystywanym w zakładach farmaceutycznych, spożywczych oraz innych wymagających najwyższej jakości , parametry jakościowe można sprawdzać w dwojaki sposób.
Pierwszym, który każdy wykonuje lub powinien wykonywać okresowo, w celu minimalnego zabezpieczenia swoich „procesów produkcyjnych” jest audyt wykonywany przez wyszkolonych techników BEKO TECHOLOGIES wyposażonych w mobilne systemy pomiarowe METPOINT, zakończony raportem i wsparciem technicznym w przypadku wystąpienia parametrów przekraczających wymagane normy.
Drugi sposób, znacznie bezpieczniejszy z punktu widzenia jakości i ciągłości procesów produkcyjnych jest wykorzystanie systemów pomiarowych METPOINT® do prowadzenia ciągłej kontroli i analizy parametrów jakościowych sprężonego powietrza. Taki monitoring jest możliwy dzięki stacjonarnym rozwiązaniom pomiarowym, które na stałe instalujemy na terenie zakładów naszych klientów.
W połączeniu ze specjalnym oprogramowaniem, web serwerem lub integracją z istniejącym systemem zakładowym, pozwala na uzyskanie bieżących informacji o jakości sprężonego powietrza, parametrach pracy i stanie technicznym urządzeń uzdatniania (osuszaczy, filtrów, kolumn z węglem aktywnym oraz katalizatorów – BEKOKAT®).
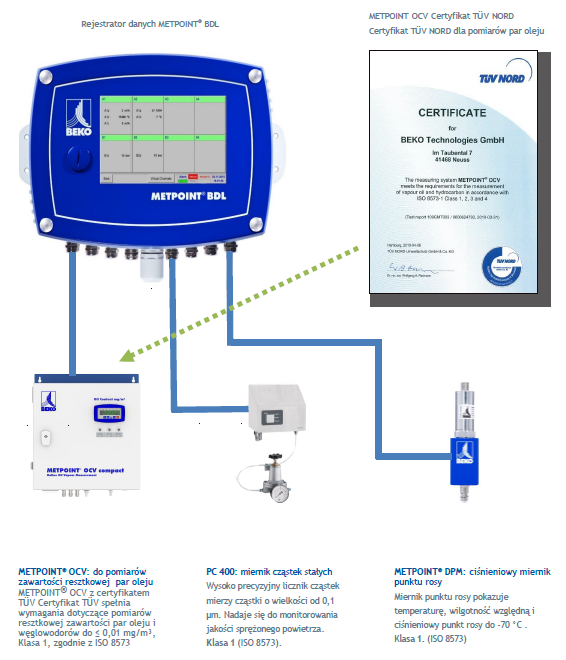
Efektywność energetyczna i optymalizacja zużycia sprężonego powietrza jest bardzo ważnym aspektem w wielu firmach szczególnie w dobie drożejących źródeł energii.
Podstawowym parametrem wpływającym na koszty sprężonego powietrza jest jego ciśnienie, na które w bardzo dużym stopniu wpływają nieszczelności, stanowiące często wysoki koszt stały.
Pomagamy naszym klientom w detekcji i analizie kosztowej nieszczelności tak aby ten aspekt kosztowy zminimalizować.
Po zoptymalizowaniu zużycia sprężonego powietrza kolejnym krokiem jest poprawa sprawności energetycznej systemów wytwarzania oraz uzdatniania (osuszania i filtracji). W celu prawidłowej optymalizacji należ znać podstawowe parametry systemu: wielkość przepływu (wytworzenie), zużycia sprężonego powietrza oraz wielkość poboru/zużycia energii elektrycznej. Dodatkowym parametrem, bez którego nie ma mowy o optymalizacji energetycznej jest ciśnienie, a konkretnie łączny spadek ciśnienia na wszystkich elementach uzdatniania. Im spadek ciśnienia niższy tym niższe koszty wytworzenia. Należy również pamiętać, że parametr ciśnieniowego punktu rosy również może generować znaczne koszty.
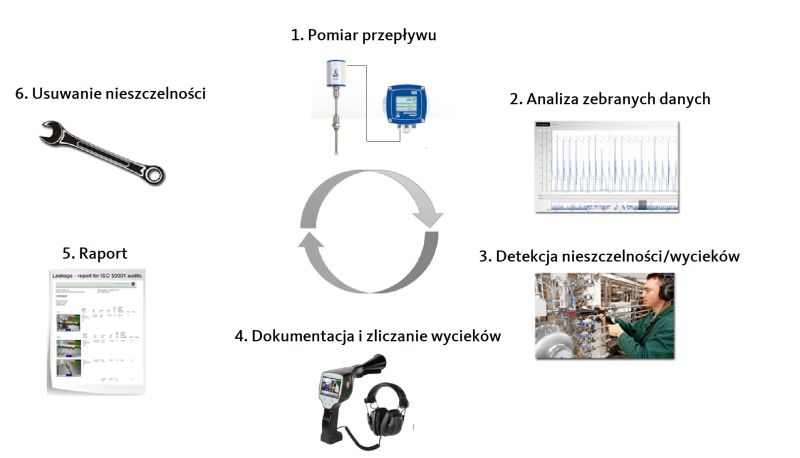
Im niższy, wymagany ciśnieniowy punkt rosy – tym koszty energii wyższe. Szczególnie widoczne jest to w przypadku stosowania zimno-regenerowanych osuszaczy adsorpcyjnych gdzie straty w procesie osuszania mogą wynosić nawet 20% sprężonego powietrza. Ten element można wyeliminować stosując osuszacze gorąco-regenerowane – bezstratne BEKO TECHNOLOGIES – EVERDRY®.
Aby jednak prawidłowo wnioskować i móc przeprowadzić analizę energetyczną w sprężarkowni, trzeba wszystkie wyżej wymienione parametry mierzyć. Stosowanie systemów pomiarowych BEKO TECHNOLOGIES – METPONIT®, pozwala zarówno na pomiar wszystkich parametrów jakościowych jak również parametrów energetycznych. Rejestratory danych BDL® – pozwalają na zapis wartości, przepływów, ciśnienia, energii elektrycznej oraz na obliczenie współczynnika sprawności sytemu – stosunku zużytej energii elektrycznej do ilości wytworzonego sprężonego powietrza kWh/m3/h. Pozwala to naszym klientom na uzyskanie informacji o ilości energii elektrycznej zużywanej do wytworzenia 1 m3 sprężonego powietrza.
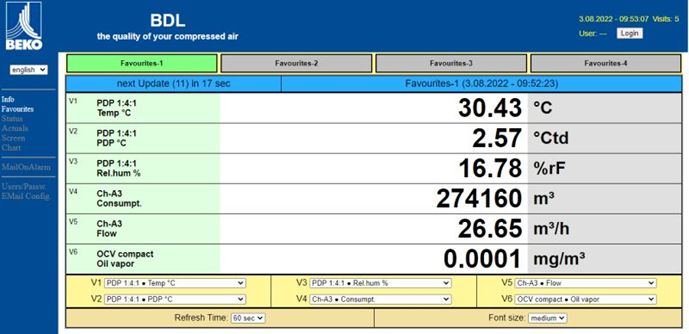
Wszystkie elementy systemu wytwarzania i uzdatniania odgrywają istotną rolę. Jakość i sprawność energetyczną pozwalają zobrazować odpowiednio dobrane czujniki, rejestratory oraz detektory. Pomimo, że same w sobie pomiary parametrów energetycznych, jakościowych czy detekcja nieszczelności nie wpływają na poprawę jakości, efektywności energetycznej oraz nie usuwają nieszczelności, to przy właściwej implementacji oraz diagnostyce i wnioskowaniu użytkownik może szybko podjąć niezbędne działania aby zoptymalizować koszty wytworzenia, a w przypadku parametrów jakościowych zapobiec wielu poważnym problemom w funkcjonowaniu zakładu.