Systemy Energy Monitoring System, w skrócie EMS, stają się nieodłącznym elementem w nowoczesnych przedsiębiorstwach w niemalże każdej branży. Nie tylko usprawniają procesy produkcyjne i pozwalają je utrzymywać, ale też realnie wpływają na oszczędności, które mogą sięgać nawet 15% w skali roku. O ich zastosowaniu opowiada w naszym wywiadzie Janusz Zajączkowski, Industry Manager Power & Energy w Endress+Hauser, światowym liderze automatyki pomiarowej.
Polski rynek bardzo dynamicznie się rozwija, a wraz z nim wszystkie sektory przemysłu. Kluczowy jest tutaj też rozwój systemów do monitorowania zużycia mediów i energii, czyli EMS. Jak to wygląda na naszym rynku?
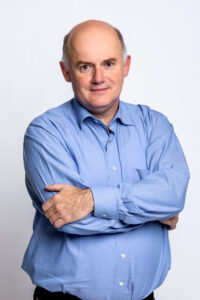
Janusz Zajączkowski: Rozwój ten jest coraz bardziej wymuszany czynnikami ekonomicznymi. Zużycie nośników ciepła, wiąże się szybko rosnącymi kosztami. Patrząc na systemy EMS od strony sprzętowej – rośnie ich funkcjonalność i komunikatywność, co też rzutuje na kształt systemów automatyki, wizualizacji i raportowania.
Zdecydowanie szybsze zmiany odbywają się w sferze integracji systemów i transmisji danych. Ze względu na coraz częstsze rozproszenie terytorialne przedsiębiorstw, dużym wyzwaniem staje się elastyczność w zakresie zdalnego dostępu do danych.
I tutaj naprzeciw wymaganiom operatorów instalacji i menedżerów firm wychodzą rozwiązania chmurowe, dotychczas traktowane z pewną rezerwą, wynikającą z obawy o bezpieczeństwo danych. Widzimy jednak, że te opory są przełamywane, zarówno dzięki rosnącej wiedzy użytkowników o ich bezpieczeństwie, jak również ze świadomości, że jest to rozwiązanie niezawodne i ekonomiczne.
Drugim, podobnym wyzwaniem, jest elastyczność w zakresie skalowania systemów. Kiedyś systemy EMS były luksusem dostępnym dla firm dużych, w szczególności dysponujących rozbudowanymi systemami automatyki. Dziś po te rozwiązania sięgają firmy średniej wielkości, szczególnie z rozproszonymi centrami produkcyjnymi.
Dobrze, wiemy już, że wiele zależy od wielkości zakładów, ich mocy produkcyjnych i lokalizacji. To jak bardzo więc automatyka przemysłowa wpływa na wydajność przedsiębiorstw?
Na wydajność rozumianą jako zdolności produkcyjne automatyka wpływa w sposób zasadniczy i dość oczywisty. Nikt dziś nie wyobraża sobie ręcznego sterowania procesami przemysłowymi, co więcej, szeroko dyskutowana obecnie idea Przemysłu 4.0 dotyczy również gospodarki cieplnej i energetycznej. Odnosi się to w również do tzw. predykcyjnego utrzymania ruchu, przy którym personel ma skupić się nie na usuwaniu zaistniałych awarii, lecz na działaniach zapobiegawczych.
W kontekście systemów EMS należy zauważyć, że układy pomiarowe pomagają znacząco obniżyć koszty generowane przez nośniki energii. Dla przykładu: w wyniku dobrze działającego, szybkiego układu pomiaru i regulacji temperatury pary w układach pasteryzacji produktu spożywczego, np. soku, producent może zmniejszyć wielkości przeregulowania i obniżyć naddatki temperaturowe, bez szkody dla bezpieczeństwa sanitarnego. Tym samym producent nie tylko obniży energochłonność procesu, ale również najprawdopodobniej poprawi jakość swojego wyrobu.
To proszę powiedzieć, jakiego rzędu są to realne oszczędności przy stosowaniu rozwiązań Endress+Hauser?
Odniosę się do wspomnianego przed chwilą przykładu. Jeden z producentów produktów mlecznych zdecydował się na wykorzystanie w procesie sterylizacji UHT naszego termometru ze specjalnym szybkim czujnikiem QuickSens, co pozwoliło to na obniżenie w układzie regulacji temperatury pary o około 2°C. To z kolej przełożyło się na obniżenie zużycia pary o około 150 ton na rok, czyli około 25.000 zł rocznie dla każdego takiego modułu.
Na bazie doświadczeń Endress+Hauser, systemy monitorowania energii pozwalają na zidentyfikowanie oszczędności w wysokości około 5% w dla układów chłodniczych, po 10% dla układów sprężonego powietrza i dla wytwarzania pary oraz 15% dla cieplnych systemów przesyłowych i dystrybucyjnych. To się odnosi oczywiście odnosi do systemów sprawnych i prawidłowo zaprojektowanych.
Jeśli chodzi o wykorzystanie specyficznych technologii Endress+Hauser, to należałoby wspomnieć o unikatowych rozwiązaniach zastosowanych w naszych przepływomierzach wirowych, takich jak pomiar stopnia suchości pary, pełnowymiarowy licznik ciepła z procedurą obliczeniową zgodną z IAPWS-IF97. Tego rodzaju funkcje pozwalają np. dokładnie kontrolować stopień przegrzania pary na wlocie do wymienników ciepła.
Jakie są też potencjalne straty?
Mówiąc o oszczędnościach, na podstawie danych zebranych przez systemy EMS, odnosimy się zazwyczaj do stanów prawidłowych. A straty z kolei najczęściej wynikają ze stanów awaryjnych lub błędów w doborze urządzeń. Wobec tego największą oszczędnością, znacznie większą od wymienionych wcześniej korzyści, jest unikanie nieplanowanych przestojów, czyli przerw w produkcji. Wyobraźmy sobie, że nieprawidłowo działający system odwodnień zatrzyma dostawę pary do procesu sterylizacji instalacji biotechnologicznej lub nagrzewania pasteryzatora produktu spożywczego. Pomijam tu okoliczności drastyczne, gdy np. w wyniku uderzenia hydraulicznego spowodowanego korkiem wodnym zostanie fizycznie uszkodzony fragment instalacji cieplnej.
Jednak najgorszy rodzaj strat to takie, których istnienia nawet nie podejrzewamy. Mogą to być na przykład nieszczelności instalacji sprężonego powietrza, ale może to być również źle dobrana aparatura pomiarowa. Tu znowu posłużę się przykładem. Dla obliczeń cieplnych pary nasyconej, można posługiwać się jednym wybranym parametrem stanu – wartością temperatury lub ciśnienia. Dla pary przegrzanej, musimy uwzględniać obydwa. Jednak są procesy, w których przy obniżeniu ciśnienia, na przykład na zaworach redukcyjnych, para się „osusza” i może przejść w przegrzaną, mimo spadku jej temperatury. Wówczas, traktowanie jej jako pary nasyconej może prowadzić do błędów w obliczeniach cieplnych sięgających 30-40%.
To przejdźmy do zagadnień związanych z jednym z najważniejszych trendów ostatnich lat, czyli cyfryzacji przemysłu. Jak wyglądają rozwiązania chmurowe i co dają przedsiębiorcom?
Obecnie systemy te rozwijają się bardzo szybko. Przede wszystkim dzięki temu, że stoi za nimi potężną infrastruktura oferująca niespotykaną wcześniej elastyczność dostępu do danych z praktycznie każdego miejsca.
Już od lat, Endress+Hauser rozwija własne środowisko chmurowe Netilion. Opracowane ono zostało w celu umożliwienia użytkownikom zarządzanie swoimi zasobami AKP. Jest to usługa obejmująca zdalny wgląd zarówno w dane pomiarowe, a także stan techniczny podłączonych urządzeń.
Dla kogo i dla jakiej wielkości zakładów rozwiązania chmurowe są najlepsze?
Rozwój rozwiązań chmurowych jest szczególnie atrakcyjny dla mniejszych i średnich przedsiębiorstw. Tym bardziej, że coraz szerzej dostępne są gotowe rozwiązania o ogromnej zdolności skalowania. Jednym z takich rozwiązań jest oferowany przez Endress+Hauser Polska system zdalnej wizualizacji i raportowania oparty o usługę Data Portal. Jest to platforma internetowa pracująca w środowisku bezpiecznej chmury obliczeniowej AWS. Minimalnym nakładem inwestycyjnym użytkownik uzyskuje zdalny i bezpieczny dostęp do danych pomiarowych, do tworzenia interaktywnych wykresów, map procesowych, grafik oraz indywidualnie skonfigurowanych raportów i bilansów.
Czy w kolejnym etapie rozwoju systemów EMS będą one współdziałały ze sztuczną inteligencją?
Jeśli chodzi o sztuczną inteligencję w systemach automatyki i wizualizacji, to na obecnym etapie jest to domena integratorów pracujących na dużych zbiorach danych, tzw. Big Data. Ich celem jest stworzenie środowiska, które w niedalekiej przyszłości będzie można wykorzystać do wdrożenia modeli uczenia maszynowego (Machine Learning). Obecnie jest to pole naszej współpracy z firmami takimi jak Magma pod kątem Przemysłu 4.0, ale w oczywisty sposób dotknie to również systemów EMS.
My w Endress+Hauser specjalizujemy się w rozwiązaniach i urządzenia będących bliżej poziomu obiektowego i w tym obszarze zauważam trzy trendy, które będą w najbliższych latach silnie wpływać na rozwój systemów takich jak EMS. Pierwszy z nich to dalszy intensywny rozwój rozwiązań chmurowych, coraz bardziej atrakcyjnych dzięki takim usługom, jak wspomniany wcześniej DataPortal i Netilion.
Drugim kierunkiem rozwojowym, który właśnie rodzi się na naszych oczach, związany jest z możliwościami jakie stwarza nowy 2-przewodowy przemysłowy Ethernet oparty na warstwie fizycznej Advanced Physical Layer (APL). Dzięki komunikacji za pomocą Ethernetu APL 2-przewodowe przetworniki pomiarowe, stanowiące zdecydowaną większość urządzeń stosowanych w pomiarach cieplnych, uzyskają zdolność transmisji danych z szybkością 10MB/s, czyli około 30 razy większą od najszybszych dotychczasowych 2-przewodowych sieci obiektowych. W ten sposób wszystkie dane mierzone, jak również wyliczane wielkości cieplne, będą mogły błyskawicznie być przesyłane do odpowiednich stacji systemu automatyki. Warto dodać, że przyrządy z komunikacją APL mają też wbudowany serwer WWW, dzięki czemu do ich obsługi i diagnostyki nie są wymagane programy narzędziowe udostępniane przez dostawców urządzeń, a jedynie zwykła przeglądarka internetowa.
Trzeci trend wiąże się rosnącym znaczeniem Przemysłu 4.0, a w szczególności wspomnianą wcześniej koncepcją predykcyjnego utrzymania ruchu, tzw predictive maintenance. Z naszej strony naprzeciw tym oczekiwaniom wychodzi Heartbeat Technology, software’owa i hardware’owa platforma diagnostyki i weryfikacji urządzeń.
Urządzenia wyposażone w Heartbeat wykonują pełną diagnostykę i weryfikację swojego stanu technicznego bez przerywania pomiaru, a w przypadku pogarszania się parametrów wybranych punktów kontrolnych, przesyłane są ostrzeżenia lub alarmy. Na żądanie operatora, przyrząd taki generuje protokół weryfikacji będący jego pełnowartościową dokumentacją jakościową. Jest to kolejny krok na drodze nie tylko do automatyzacji opartej o przewidywanie zagrożeń.