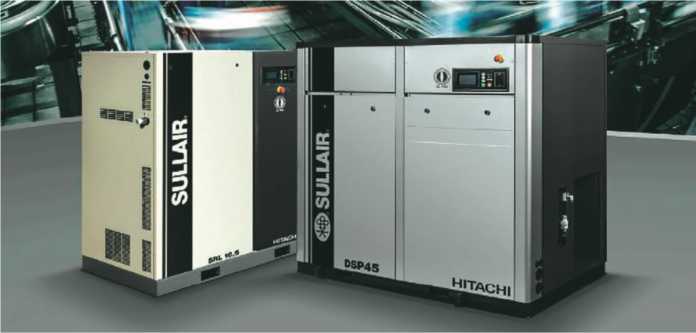
W przemyśle stawki są zbyt wysokie, aby oszczędzać na instalacjach pneumatycznych. W artykule opisujemy klasy czystości sprężonego powietrza i ich znaczenie dla firm produkcyjnych.
W świecie bezolejowych sprężarek śrubowych używa się wielu terminów: bezolejowa, klasa 1, „technicznie bezolejowa”, klasa 0, certyfikowana klasa 0 i tak dalej. Podczas gdy te terminy mogą brzmieć podobnie, istnieje pomiędzy nimi wiele różnic, które powinny być dobrze zrozumiane. Konsekwencje wybrania złego rozwiązania czy technologii mogą być bowiem poważne.
W tym artykule skupiamy się na porównaniu sprężarek bezolejowych o klasie 0 jakości sprężonego powietrza ze sprężarkami klasy 1, wytwarzającymi powietrze nazywane także „technicznie bezolejowym”. Opisujemy zawiłości klasy 0 w porównaniu z klasą powietrza „technicznie bezolejowego” oraz definiujemy kluczowe różnice pomiędzy tymi obydwoma klasami. Jednak najpierw musimy ustalić, dlaczego sprężone powietrze niezawierające oleju ma tak duże znaczenie w przemyśle.
Przyczyny zapotrzebowania na bezolejowe sprężone powietrze w wielu gałęziach przemysłu
Istnieją pewne gałęzie przemysłu oraz aplikacje, w których czystość sprężonego powietrza ma kluczowe znaczenie. Wymagana jest w nich maksymalna jakość sprężonego powietrza, aby zmniejszyć ryzyko wpływu zanieczyszczeń na instalację pneumatyczną, produkt końcowy oraz inne elementy związane z procesem produkcji. Wśród tych gałęzi przemysłu znajdują się między innymi: spożywczy, farmaceutyczny, motoryzacyjny, medyczny, elektroniczny, lotniczy, produktów laboratoryjnych, półprzewodnikowy, chemiczny oraz rafineryjny (patrz fot.1).
Bezolejowe sprężone powietrze ma kluczowe znaczenie w tych gałęziach przemysłu, ponieważ nawet najmniejsza ilość oleju jako zanieczyszczenia obecnego w tym powietrzu może mieć fatalne skutki w postaci zanieczyszczenia produktu końcowego, uszkodzenia sprzętu produkcyjnego, spowodowania nieplanowanych przestojów lub naruszenia reputacji firmy na skutek wypuszczenia produktu końcowego złej jakości i/lub reklamacji klientów.
Klasy jakości sprężonego powietrza
Wydana przez Międzynarodową Organizację Normalizacyjną norma ISO 8573-1 Sprężone powietrze ogólnego stosowania – Zanieczyszczenia i klasy czystości podaje wymagania dotyczące czystości oraz określa klasy czystości sprężonego powietrza stosowanego w przemyśle do celów ogólnych. W aplikacjach bezolejowych wymagane jest sprężone powietrze o jakości minimum klasy 1, ale preferowana jest tu klasa 0. Spowodowane jest to tym, że klasa 0 jest stabilna, a klasa 1 – niestabilna. Klasa 1 wymaga filtracji powietrza wychodzącego ze sprężarki w celu eliminacji oleju pochodzącego z procesu sprężania, natomiast rodzaj filtracji zależy głównie od dwóch zmiennych czynników, które mają wpływ na wydajność procesu filtracji: ciśnienia sprężonego powietrza oraz temperatury sprężonego powietrza / temperatury otoczenia.
Kryteria czystości sprężonego powietrza dla klasy 0 są ostrzejsze w porównaniu z klasą 1 (zawartość 0,01 mg/m3 oleju w postaci zanieczyszczenia), jak uzgodniono pomiędzy producentem a użytkownikiem sprężarki. Im niższa klasa czystości, tym niższe jest stężenie zanieczyszczeń olejowych w sprężonym powietrzu oraz mniejsze prawdopodobieństwo obecności w nim innych zanieczyszczeń.
Norma ISO 8573-1 podaje klasy czystości sprężonego powietrza ze względu na obecność zanieczyszczeń takich jak cząstki stałe, woda i olej. Klasy czystości wg tej normy mogą być użyte do opisania jakości instalacji sprężonego powietrza lub do podania specyfikacji wymaganej jakości powietrza dla celów jakiejś precyzyjnej aplikacji.
Dla celów naszego artykułu skupimy się tylko na zanieczyszczeniu sprężonego powietrza olejem.

Klasa 1 czystości sprężonego powietrza wg ISO 8573-1
Sprężone powietrze o klasie czystości 1 uzyskuje się z kompresorów olejowych z filtrami wylotowymi, które wychwytują część oleju z powietrza dostarczanego przez te urządzenia do instalacji. Z tego powodu sprężone powietrze o klasie czystości 1 może być traktowane jako „technicznie bezolejowe”.
Dla przykładu rozważmy sprężarkę olejową o wydajności 1000 cfm (1699,01 m3/h). Maszyna ta uwalnia w ciągu roku do instalacji pneumatycznej około 14 galonów (53 dm3) oleju (w temperaturze 86°F/30°C oraz przepuszczaniu oleju w separatorze 3 mg/m3). W tej sytuacji wymagane jest zainstalowanie trzech filtrów do usunięcia tego oleju ze sprężonego powietrza, w tym filtru z węglem aktywnym do pochłaniania oparów oleju. Jednak może to być ryzykowna i niebezpieczną metoda, ponieważ wydajność filtrów sprężonego powietrza pogarsza się wraz ze wzrostem temperatury powietrza dolotowego.
Parametry filtrów wylotowych są podane dla temperatur powietrza dolotowego sprężarki w zakresie 68–70°F (20–21°C). Jest to bardzo wąski przedział. Wydajność filtracji spada wykładniczo w wyższych temperaturach (patrz wykres na rys. 3). Wyobraźmy sobie, co się stanie, jeśli temperatura sprężonego powietrza osiągnie 80°F (26,7°C), 100°F (37,8°C) lub jeszcze większą wartość. Takie temperatury mogą być łatwo osiągnięte, ponieważ temperatura sprężonego powietrza na wyjściu kompresora jest o około 27°F (15°C) wyższa od temperatury otoczenia. Dlatego też, gdy temperatura sprężonego powietrza wzrasta, to znacznie wzrasta prawdopodobieństwo przepuszczenia zanieczyszczeń olejowych przez filtr do instalacji pneumatycznej. Oznacza to, że olej może dostać się do sprzętu produkcyjnego, zanieczyścić ten sprzęt i produkt końcowy oraz środowisko.
Ponadto, jeśli wykorzystuje się kompresor olejowy z filtracją w celu uzyskania sprężonego powietrza o klasie czystości 1, czyli „technicznie bezolejowego”, to należy uwzględnić kwestie związane z konserwacją sprzętu. Poza dużym ryzykiem zanieczyszczenia sprzętu produkcyjnego i produktu końcowego olejem użytkownicy takich kompresorów powinni przeanalizować pracochłonność i koszty konserwacji separatorów oleju, filtrów w liniach pneumatycznych, filtrów pochłaniających opary oleju oraz sprzętu uzdatniającego kondensat. Powstają tu bowiem takie problemy, jak:
- częstsze serwisowanie oraz często wyższe koszty konserwacji;
- wyższe koszty energii elektrycznej, spowodowane spadkiem ciśnienia sprężonego powietrza w filtrach;
- zwiększone ryzyko przepuszczania oleju przez filtry ze względu na możliwość uszkodzenia lub awarii tych elementów. Konsekwencją tego może być zanieczyszczenie olejem oraz uszkodzenia sprzętu produkcyjnego i oprzyrządowania
Czas eksploatacji filtrów sprężonego powietrza jest krótki. Jeżeli użytkownik konsekwentnie utrzymuje temperaturę w granicach 68–70°F (20–21°C), to filtry z węglem aktywowanym – które pochłaniają opary oleju w ilości do 0,01 mg/m3 powietrza – wytrzymują nieco poniżej sześciu tygodni pracy (41 dni). Natomiast przy wszelkich wzrostach temperatury do około 100°F (37,8°C) żywotność filtra z węglem aktywowanym może spaść poniżej czterech dni (90 godzin).
Wrażliwość na zmiany temperatury sprawia, że filtry klasy czystości 1 są niestabilne. Oznacza to, że jakość przefiltrowanego sprężonego powietrza może łatwo przeskoczyć z klasy 1, czyli „technicznie bezolejowego” do klasy 2, która nawet nie kwalifikuje sprężonego powietrza jako bezolejowe.
Filtry o klasie czystości 1 nie zawsze dają na wyjściu technicznie bezolejowe sprężone powietrze, ponieważ jakość/wydajność filtracji zależy od temperatury tego powietrza. Im wyższa temperatura, tym bardziej spada jakość sprężonego powietrza. Jakość ta może przeskakiwać pomiędzy klasami 1 i 2 w zależności od temperatury.
Nawet w optymalnych warunkach i przy zastosowaniu kilku warstw usuwania oleju (filtrów w linii pneumatycznej) rozwiązania „technicznie bezolejowe” nie są już uważane za najlepszą praktykę. Jest to spowodowane ryzykiem niestabilności jakości sprężonego powietrza (przeskoki z klasy 1 do 2 i odwrotnie) ze względu na fluktuacje wydajności filtrów wraz ze zmianami temperatury.

Klasa 0 czystości sprężonego powietrza
Wymagania klasy 0 są ostrzejsze niż dla klasy 1 (0,01 mg/m3 oleju jako zanieczyszczenia). Sprężone powietrze klasy 0 jest bezpieczniejszym rozwiązaniem dla użytkownika niż klasy 1, ponieważ parametry czystości są stabilne, nie zmieniają się wraz z temperaturą oraz nie jest wymagana filtracja powietrza wylotowego, w celu usuwania zanieczyszczeń olejowych, pochodzących ze sprężarki.
Użycie w zakładzie sprężarki o klasie czystości 0, czyli najwyższej z klas czystości sprężonego powietrza, zapewnia, że do instalacji pneumatycznej będzie dostarczane powietrze wolne od aerozoli olejowych, oparów oleju lub ciekłego oleju, pochodzącego ze sprężarki. Kompresory bezolejowe o klasie czystości 0 pomagają w eliminacji potencjalnego zanieczyszczenia sprzętu produkcyjnego, produktu końcowego i środowiska, ponieważ żaden olej czy środek smarny nie jest wykorzystywany w procesie sprężania powietrza.
Chociaż sprężarki bezolejowe klasy 0 są droższe od olejowych, to jednak ich zakup jest opłacalny, ponieważ wyższe koszty początkowe są rekompensowane niższym ryzykiem. Kompresory klasy 0 są znacznie bezpieczniejsze w aplikacjach wrażliwych na zanieczyszczenia – w branży spożywczej, farmaceutycznej, elektronicznej i medycznej. Wykorzystywanie sprężarek z certyfikatem klasy czystości 0 zmniejsza ryzyko zanieczyszczenia sprężonego powietrza, co może spowodować wyprodukowanie wyrobów o złej jakości i znaczne zmniejszenie zysków firmy oraz utratę zaufania klientów i nadszarpnięcie reputacji całej branży.
Urządzenia klasy 0 spełniają wymagania normy ISO 8573-1. Certyfikaty na klasę 0, potwierdzające zgodność danego urządzenia ze wszystkimi wymaganiami tej klasy, wydają laboratoria zewnętrzne. Zasadniczo certyfikat na klasę 0 jest czymś w rodzaju dodatkowego potwierdzenia jakości sprężonego powietrza przez stronę trzecią.
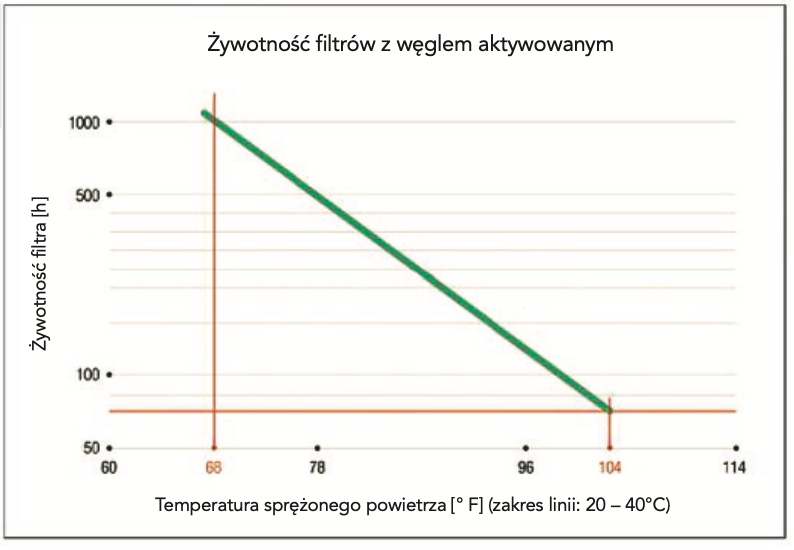
SPRĘŻONE POWIETRZE
INSTALACJE SPRĘŻONEGO POWIETRZA są epicentrum sukcesu lub porażki dla wielu fabryk. Gdy elementy instalacji pneumatycznej są w jak najlepszym stanie technicznym, narzędzia zasilane sprężonym powietrzem także funkcjonują tak jak powinny. Jednak gdy elementy instalacji są uszkodzone, to skutki mogą być poważne. Na przykład spadek ciśnienia jest zjawiskiem doświadczanym głównie w obwodzie odbioru systemu sprężonego powietrza. Jeśli kompresor nie dostarcza sprężonego powietrza z wymaganą wydajnością, mierzoną w stopach sześciennych na minutę (SFCM; 1,699 m3/h), to ciśnienie powietrza w rurach i wężach instalacji, mierzone w funtach na cal kwadratowy (PSI; 0,069 bar), nie może być utrzymane na wymaganym poziomie.
W dużej fabryce instalacja sprężonego powietrza może rozciągać się na dystansie dziesiątek metrów oraz pojawiać się i znikać wśród różnych innych systemów. Problemy w instalacji pneumatycznej mogą wystąpić w każdym jej elemencie – w tym w kompresorze, osuszaczu powietrza, linii głównej lub zasilanych z niej narzędziach pneumatycznych, takich jak klucze, wiertarki i szlifierki powietrzne. Nieszczelności powodują zmniejszanie przepływu powietrza w instalacji, czego konsekwencją jest zbyt małe ciśnienie powietrza, aby zasilany sprzęt działał prawidłowo.
Fragment artykułu „Małe wycieki powodują duże szkody” („Tiny leaks cause big damages”) – autor Justin Sheard, Fluke Corp.
Podsumowanie
W świecie bezolejowych sprężarek śrubowych używa się wielu terminów. Podczas gdy te terminy mogą brzmieć podobnie, istnieją pomiędzy nimi ogromne różnice, które powinny być zrozumiane. Konsekwencje wybrania złego rozwiązania czy technologii mogą być bowiem poważne. W tym artykule wyjaśniliśmy zarówno znaczenie zainwestowania w sprężarki bezolejowe, jak i różnice pomiędzy klasami czystości sprężonego powietrza: 1 – „technicznie bezolejowego” – oraz 0.
Każdego dnia w zakładzie produkcyjnym istnieje wiele zagrożeń i ryzyk. Oszczędzanie na instalacji sprężonego powietrza może doprowadzić do wielu utrzymujących się długo problemów. Jednak wykorzystywanie kompresorów bezolejowych, posiadających certyfikat klasy 0 czystości sprężonego powietrza wg ISO 8573-1, pomaga firmie przemysłowej w ulepszaniu jej operacji biznesowych oraz zwiększaniu zysków poprzez obniżenie ogólnego ryzyka.
1 ang. technically oil free
2 ang. Compressed air — Part 1: Contaminants and purity classes
Camilo Villalobos jest dyrektorem rozwiązań OEM oraz inżynierskich w firmie Sullair LLC. Jest menedżerem rozwiązań OEM i produktów firm Sullair i Hitachi, wykorzystywanych w górnictwie, medycynie, przemyśle, transporcie i pojazdach elektrycznych.
Stephanie Roberts jest dyrektorem ds. komunikacji w Sullair LLC. Pracuje ona w tej firmie od niemal sześciu lat i odpowiada za komunikację wykonawczą, zewnętrzną i wewnętrzną, public relations oraz media społecznościowe na obszar obu Ameryk, a także dla Hitachi Industrial Equipment Systems.