W wielu branżach obróbka strumieniowo ścierna jest nieodzowną technologią
obróbki powierzchni. Oprócz celu, jakim jest osiągnięcie najlepszych
możliwych wyników, klienci zawsze wymagają krótkich czasów cyklu,
najniższych możliwych kosztów i minimalnego wkładu materiałowego. Rösler
spełnia te wymagania, między innymi dzięki wykorzystaniu ultranowoczesnego
oprogramowania do symulacji. Ponadto wirtualne modele znacznie skracają
czas projektowania – zwłaszcza w przypadku dużych, złożonych maszyn – i
zapewniają dostępność urządzeń w krótszych terminach realizacji.
Obróbka strumieniowo ścierna jest doskonałym narzędziem do czyszczenia
powierzchni, usuwania zadziorów, przygotowania powierzchni do malowania lub
powlekania i śrutowania. Technologia obróbki strumieniowo-ściernej jest
wykorzystywana do tworzenia optymalnych wykończeń powierzchni, czy to w
celu zapewnienia bezproblemowych operacji produkcyjnych na wyjściu, czy też
w celu optymalizacji cech funkcjonalnych produktu. Dzięki obróbce
strumieniowo ściernej i innym procesom przemysłowym klienci stają przed
wyzwaniem poprawy produktywności i efektywności kosztowej, a także
minimalizacji zużycia cennych zasobów. Rösler wspiera swoich klientów
najnowocześniejszym oprogramowaniem do symulacji na etapie planowania nowej
obróbki strumieniowo ściernej, szczególnie w odniesieniu do opracowywania i
optymalizacji procesów.
Osiąganie optymalnych wyników przy wysokiej efektywności kosztowej
Dzięki oprogramowaniu do symulacji Rösler każdy fizyczny etap procesu
obróbki strumieniowo ściernej, w tym odpowiednie obrabiane detale, można
wyświetlić jako model 3D. Obejmuje to typ ścierniwa, ilość wyrzucanego
ścierniwa i przepływ ścierniwa. Dane wygenerowane przez tak zwaną symulację
cząstek pozwalają na precyzyjną ocenę, jaka ilość ścierniwa jest wymagana i
z jaką energią uderzenia musi trafić w różne obszary powierzchni
obrabianego przedmiotu, aby osiągnąć 100% pokrycie. Jednocześnie dane te
pomagają określić wymaganą moc turbin, idealną pozycję turbin i
zaprojektować odpowiednie urządzenia badawcze. Symulacje ułatwiają rozwój
urządzeń do obróbki strumieniowo ściernej i procesów w celu osiągnięcia
optymalnych wyników obróbki strumieniowo ściernej przy najniższej możliwej
liczbie turbin, niskim zużyciu energii i minimalnym zużyciu maszyny.
Pomagają również zmniejszyć nakłady inwestycyjne, koszty operacyjne i
zużycie cennych zasobów.
Kolejną zaletą symulacji jest to, że maszyny do obróbki strumieniowo-
ściernej nowych detali mogą być planowane na podstawie danych CAD, na długo
zanim rzeczywiste detale będą dostępne w formie prototypu. Oszczędza to
cenny czas, ponieważ urządzenie do obróbki strumieniowo ściernej może
rozpocząć pracę produkcyjną w tym samym dniu, w którym zostało uruchomione.
Czasochłonne i kosztowne próby obróbki z rzeczywistymi detalami są mniej
lub bardziej całkowicie wyeliminowane.
Co więcej, symulacje dostarczają również cennych informacji na temat tego,
czy określone wyniki obróbki strumieniowo-ściernej można osiągnąć na
detalach o danej geometrii. Jeśli nie jest to możliwe, wyniki symulacji
dostarczają cennych wskazówek dotyczących optymalizacji kształtu
obrabianego detalu.
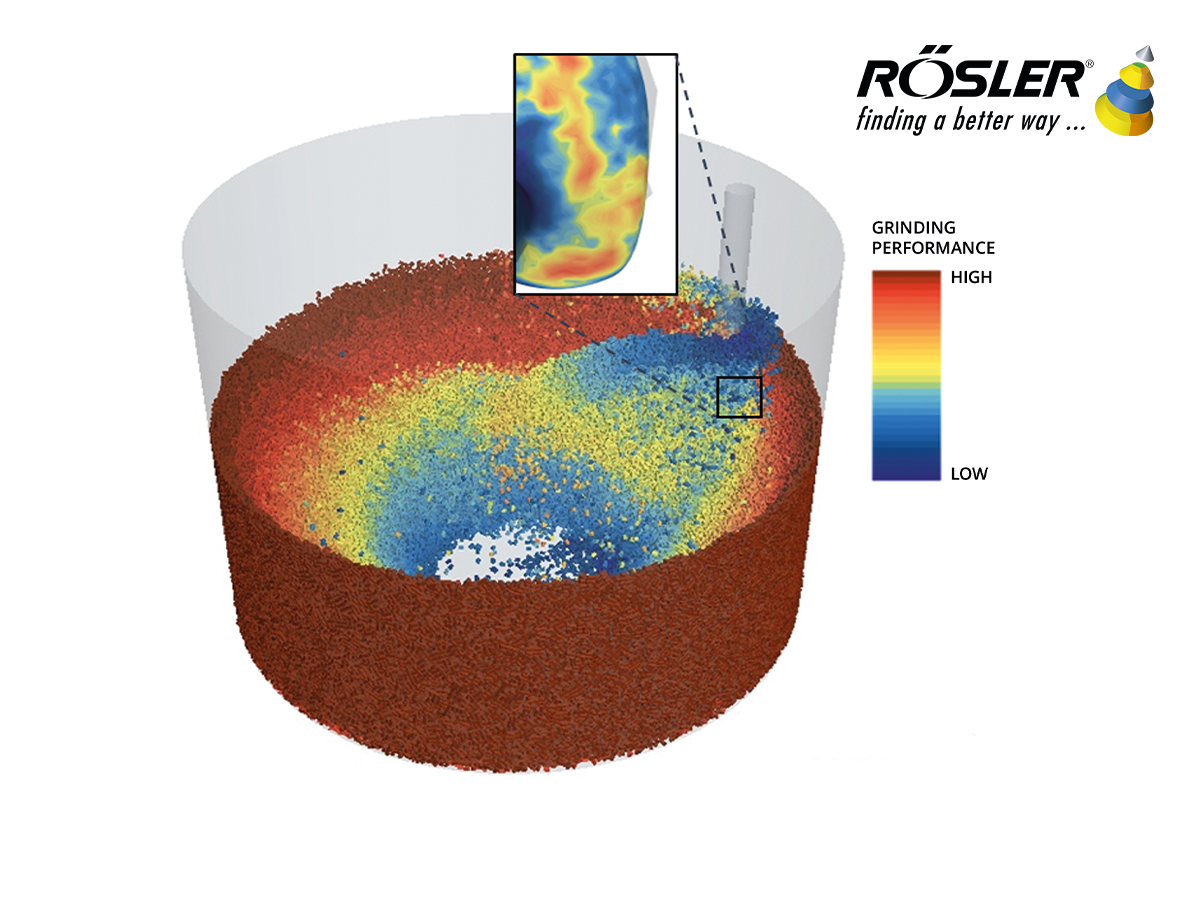
do ruchu materiałów szlifierskich lub polerskich i ich wpływu na powierzchnię detalu.
Krótsza faza planowania i optymalne wyniki obróbki strumieniowo ściernej w
przypadku projektów złożonego wyposażenia
Planowanie i uruchamianie złożonych, dużych urządzeń do obróbki
strumieniowo ściernej podzespołów o dużych wymiarach, na przykład 20 x 5 x 4
metry (dł. x szer. x wys.) jest szczególnie trudne. Zazwyczaj dla tak
dużych detali praktycznie nie są dostępne maszyny do przeprowadzenia prób
obróbki. W takich przypadkach symulacja i wirtualne planowanie procesów
obróbki strumieniowo-ściernej może być jedynym dostępnym narzędziem do
osiągnięcia doskonałych wyników obróbki strumieniowo-ściernej i wysokiej
wydajności wyposażenia. Dokładnie w tym celu firma Rösler opracowała
kolejny moduł oprogramowania, który modeluje duże, złożone wyposażenie i
odpowiednie procesy obróbki strumieniowo ściernej. Z jednej strony
realistyczne i prawidłowe odwzorowanie wzorów strumieniowania i przepływu
mediów znacznie zmniejsza ogólne ryzyko inwestycyjne. Z drugiej strony,
wymagania czasowe dotyczące planowania i uruchomienia urządzenia do obróbki
strumieniowo ściernej mogą zostać znacznie skrócone.
Szybsza obróbka całych partii detali
Jeśli chodzi o obróbkę strumieniowo ścierną całych partii stosunkowo małych
detali, na przykład w urządzeniach do obróbki strumieniowo ściernej z
wieloma bębnami (RMT), optymalne połączenie detali i ścierniwa może
znacząco wpłynąć na wyniki obróbki i czas cyklu. W przypadku takich
zastosowań oprogramowanie umożliwia symulację i optymalizację procesu
obracania detali w bębnowej komorze śrutowniczej. Skutkuje to najkrótszymi
możliwymi czasami procesu. W niektórych przypadkach można osiągnąć
skrócenie czasu cyklu o około 25 % na partię, co skutkuje znacznym wzrostem
wydajności.
Energooszczędne i wydajne odpylacze
W urządzeniach do obróbki strumieniowo ściernej turbiny i odpylacze
wymagają zdecydowanie największego nakładu energii. Dotyczy to zarówno
standardowych, jak i dużych urządzeń do obróbki strumieniowo ściernej.
Dlatego pakiet oprogramowania zawiera również specjalny moduł symulacji
przepływu powietrza, który określa objętość powietrza wymaganą do
bezpiecznego odprowadzenia pyłu powstającego podczas operacji śrutowania z
komory śrutowniczej. Jeśli pył może być skuteczniej usuwany dzięki lepszemu
przepływowi powietrza, możliwe jest zastosowanie mniejszego odpylacza, co
skutkuje niższym zużyciem energii. W każdym przypadku zoptymalizowany
system odprowadzania powietrza pomaga skrócić czas cyklu, a tym samym
zwiększa produktywność. Co więcej, obrabiane elementy opuszczają urządzenie
do obróbki strumieniowo ściernej czystsze, co ułatwia dalsze operacje
produkcyjne.
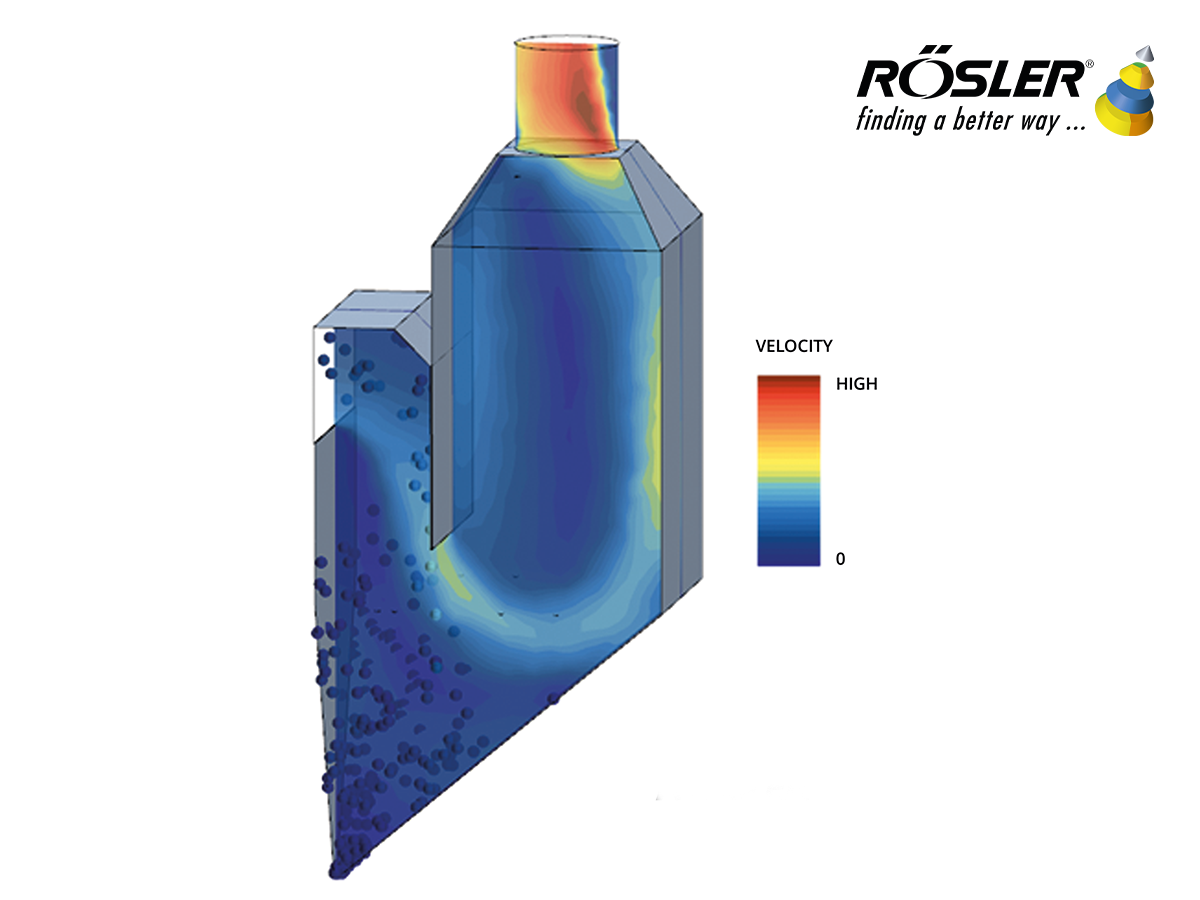
wyciągu powietrza.
Cyfrowe kopie turbin śrutowniczych zwiększają wydajność operacyjną
Aby zmniejszyć zużycie energii i stopień zużycia, a jednocześnie zwiększyć
wydajność operacyjną, Rösler pracuje z cyfrowymi kopiami turbin
śrutowniczych. Odwzorowanie przepływu cząstek zapewnia wirtualną analizę
obszarów zużycia w turbinie. To z kolei pozwala na wprowadzenie modyfikacji
geometrii turbiny w celu zminimalizowania stopnia zużycia. Inne symulacje
mogą być przeprowadzane w celu zwiększenia wydajności turbiny, co z kolei
spowoduje dodatkowe oszczędności energii.
Dzięki szerokiemu zastosowaniu oprogramowania do symulacji do projektowania
urządzeń do obróbki strumieniowo ściernej i odpowiednich procesów, a także
do optymalizacji przepływu powietrza i technologii turbin, czas realizacji
zamówień na urządzenia do obróbki strumieniowo ściernej firmy Rösler ulega
znacznemu skróceniu. Co więcej, zapewniają one znaczne oszczędności energii
i niższy wskaźnik zużycia. Wszystko to przekłada się na znaczące korzyści
dla klientów.
Systemy symulacji dla procesów masowej obróbki wykańczającej złożonych
detali
Do tej pory rozwój procesów masowej obróbki wykańczającej dla obróbki
pojedynczych detali o złożonej geometrii i trudnych do obróbki, takich jak
implanty kolanowe, wymagał licznych prób obróbki. W przypadku tak
skomplikowanych zastosowań, zwykle obsługiwanych w tak zwanych maszynach do
szlifowania zanurzeniowo-wleczącego, Rösler wykorzystuje również
technologie symulacyjne.