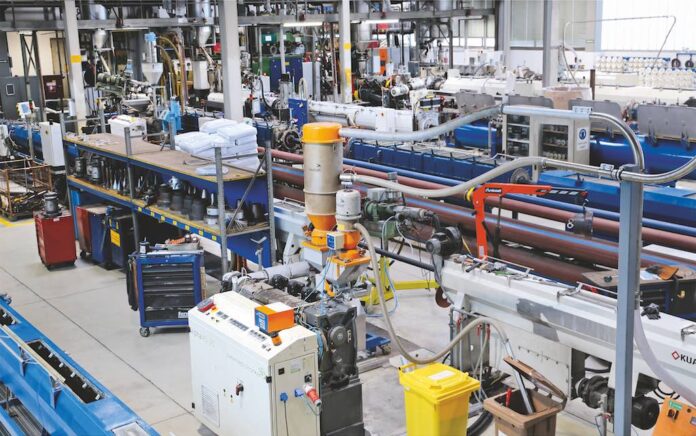
W globalnie konkurencyjnej branży produkcyjnej liczy się każda minuta dnia, każdy gram surowca i każda kilowatogodzina energii. Grupa Wienerberger mierzy się z tym wyzwaniem od dziesięcioleci. Ale ostatnio ten wiodący międzynarodowy dostawca innowacyjnych materiałów budowlanych i rozwiązań infrastrukturalnych wykorzystał TwinCAT i „wsparcie agenta danych”, aby osiągnąć te cele. W ramach kompleksowej inicjatywy cyfryzacji Grupa, która określa się jako czołowy producent cegieł na świecie, zaczęła codziennie przesyłać kilka milionów zmierzonych wartości do chmury w celu analizy, aby uzyskać przydatne informacje we wszystkich obszarach firmy jako podstawę do ukierunkowanych działań optymalizacyjnych.
Energooszczędne budynki, bezpieczne systemy kanalizacyjne, atrakcyjne przestrzenie publiczne: Dowody specjalistycznej wiedzy Grupy Wienerberger można znaleźć we wszystkich dziedzinach życia. Wiedeński producent cegieł, systemów rurowych i kostki brukowej, którego korzenie sięgają 1819 roku, od 200 lat z powodzeniem napędza przyszłość budownictwa, posiadając dzisiaj 197 zakładów produkcyjnych w 29 krajach.
Aby obronić tę wiodącą pozycję nawet w czasach coraz ostrzejszej globalnej konkurencji, Grupa uruchomiła kompleksową inicjatywę digitalizacji. Z jednej strony promuje ona tworzenie inteligentnych produktów – na przykład plastikowych rur, które mogą zbierać dane o poziomie wody lub opadach – oraz rozwój nowych cyfrowych modeli biznesowych. Z drugiej strony firma robi wszystko, co w jej mocy, aby zwiększyć przejrzystość we własnych zakładach produkcyjnych.
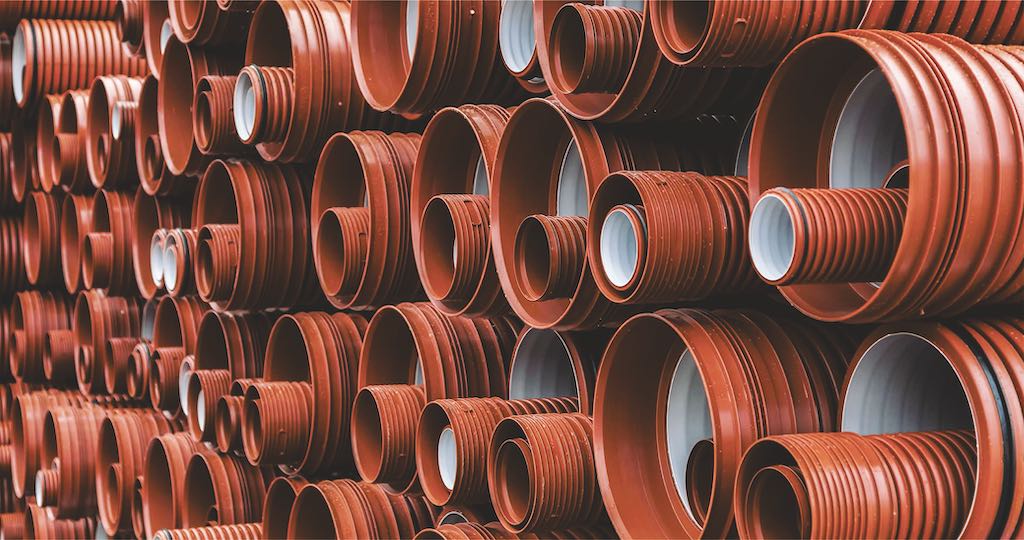
Cyfrowe bliźniaki do doskonałości operacyjnej
„Naszą wizją jest stworzenie cyfrowego bliźniaka każdej linii produkcyjnej, w którym przechowywane są nie tylko dane dotyczące procesów, planowania i jakości, ale także szczegółowe informacje o kursach szkoleniowych dla operatorów systemu” – wyjaśnia Roy Sibbald, specjalista ds. doskonałości produkcyjnej w Pipelife, spółce zależnej Wienerberger.
Ostatecznie Sibbald chce wiedzieć o każdej minucie produkcji i o tym, czy czas ten został wykorzystany produktywnie, czy nie. „Jeśli nie, to nie była to dobra minuta. To samo dotyczy każdego grama użytego przez nas surowca. Czy został on przekształcony w coś, co możemy sprzedać, czy też co się z nim stało? Wartość wiarygodnych odpowiedzi na wszystkie te pytania jest ogromna” – wyjaśnia.
Firma Wienerberger wybrała linie do wytłaczania 21 i 26 w zakładzie Pipelife w Wiener Neudorf w Austrii na potrzeby weryfikacji koncepcji opracowanej wspólnie z dostawcami rozwiązań TietoEVRY i HEAP Engineering GmbH, a także z firmą Beckhoff. Na tych liniach produkowane są rury z tworzyw sztucznych o specjalnych wymaganiach jakościowych.
„W tym przypadku należy przechwytywać dane dotyczące grubości ścianki, owalności, mimośrodowości, kilogramów na metr, impulsów piłowania i wiele innych” – mówi Andreas Roither-Voigt, starszy konsultant biznesowy w TietoEVRY. W procesie produkcyjnym konieczne jest między innymi ustalenie, które rury zostały przycięte w celu pomiaru i w jakim czasie oraz czy rzeczywiście zostało to wykonane z dokładnością do jednego milimetra. Zadania pomiarowe są obsługiwane przez terminale EtherCAT EL1512 i EL5151 firmy Beckhoff. „Jeden terminal I/O umożliwia bezpośrednie podłączenie enkoderów, podczas gdy drugi przesyła bieżące odczyty licznika w czasie rzeczywistym w celu obliczenia długości rur w oprogramowaniu TwinCAT – wszystko na bramce brzegowej” – wyjaśnia Roither-Voigt.
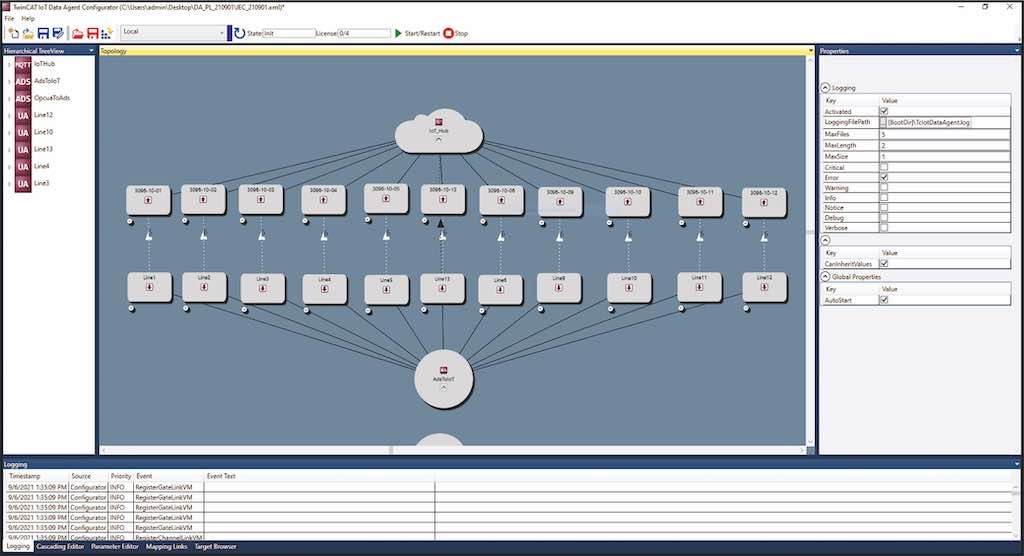
Komputery przemysłowe służą jako optymalne urządzenia brzegowe
W międzyczasie miliony rekordów danych z różnych zakładów Grupy Wienerberger są codziennie przechowywane w chmurze do celów analitycznych. W celu jednoznacznego przypisania przesyłanych sygnałów, są one opatrzone niepowtarzalnymi kodami fabryki, linii i typu maszyny. „Połączyliśmy siły, aby stworzyć 'Pojedyncze Źródło Prawdy’, dzięki któremu wizja firmy 'wszystkie istotne dane online – przez cały czas’ stanie się rzeczywistością. Chodziło między innymi o to, by ostatecznie każdy użytkownik otrzymywał istotne dla niego informacje” – mówi Manuel Hausjell, konsultant ds. IoT i danych w TietoEVRY. „Niezależnie od tego, czy analityk danych planuje wykorzystać surowe dane jako dane wejściowe dla modeli uczenia maszynowego, czy też są one już skonsolidowane i/lub skoncentrowane w celu włączenia do różnych narzędzi raportowania, w każdym przypadku muszą być kompletne i poprawne”.
W związku z tym kierownicy projektu ustandaryzowali i określili sposób integracji poszczególnych maszyn z siecią Internetu rzeczy (IoT). Ultrakompaktowy komputer przemysłowy C6030 firmy Beckhoff odgrywa centralną rolę jako strażnik węzła Azure IoT w chmurze. Jego kompaktowa konstrukcja i wydajność wielordzeniowego procesora do 3,6 GHz na rdzeń sprawiają, że jest to idealne urządzenie brzegowe, według Lukasa Pechhackera, dyrektora zarządzającego HEAP Engineering.
„Jest to zaleta technologii sterowania opartej na komputerach PC – urządzenia sterujące mogą być skalowane zgodnie z wymaganiami i oferują wystarczające rezerwy wydajności do wstępnego przetwarzania danych na miejscu” – wyjaśnia Pechhacker. „Na przykład w przypadku nawijarek interwały próbkowania są rzędu milisekund. Dlatego też edge computing jest tutaj wykorzystywany do przeliczania na obroty na minutę w celu utrzymania w ryzach przepływu informacji do chmury”.
C6030 z TwinCAT 3 IoT Data Agent generalnie musi przejąć wiele funkcji „tłumacza”. Z jednej strony wykorzystuje TwinCAT ADS i OPC UA do budowania mostów komunikacyjnych między maszynami w różnym wieku i różnego pochodzenia. Z drugiej strony działa również jako brama do chmury.
„Mając łącznie 197 zakładów produkcyjnych w 29 krajach, mamy do czynienia z niezwykle zróżnicowanym środowiskiem maszyn i licznymi protokołami, które muszą być sprowadzone do wspólnego mianownika. W niektórych przypadkach terminale EtherCAT EL6001 są wymagane jako interfejsy szeregowe RS232 do ustanowienia wymaganych połączeń; w innych działa to za pośrednictwem OPC UA” – mówi Pechhacker.
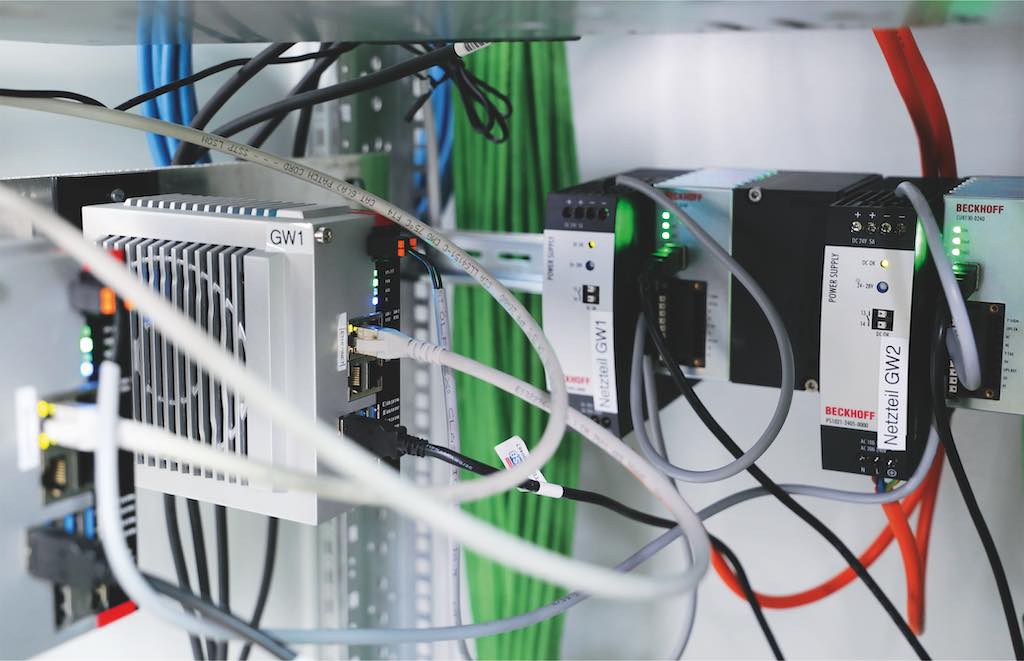
Doskonała praca zespołowa
Jako dostawcy rozwiązań Beckhoff, zarówno HEAP Engineering, jak i TietoEVRY rozumieją, jak w pełni wykorzystać możliwości technologii sterowania opartej na PC i EtherCAT, według Manfreda Hegera, szefa strategii IT, innowacji i projektów w Wienerberger. „Każdy w naszym zespole projektowym może po prostu zaufać, że druga osoba dokładnie wie, co robi i że zawsze widzi szerszy obraz we wszystkim, co robi” – mówi Heger.
Ze względu na ograniczenia w podróżowaniu związane z COVID-19, dwa zakłady produkcyjne zostały nawet zdalnie podłączone do sieci LoT – jeden w Szwecji, a drugi w Holandii. „Lokalni elektrycy dostarczyli kluczowe szczegóły dotyczące istniejącej infrastruktury. Następnie wymagane komponenty zostały zamówione w firmie Beckhoff i wstępnie skonfigurowane przez HEAP Engineering, aby umożliwić proste podłączenie typu plug-and-play na miejscu. Następnie HEAP Engineering wkroczył do akcji, aby przeprowadzić ostateczną konfigurację za pośrednictwem bezpiecznego połączenia zdalnego, a my ustaliliśmy odpowiedni kurs w chmurze lub zajęliśmy się kontrolą jakości danych” – mówi Manuel Hausjell z TietoEVRY, opisując idealną współpracę.
„Zawsze pojawiają się nowe pomysły dotyczące tego, co jeszcze możemy zrobić, aby usprawnić codzienne operacje w naszych zakładach, takie jak przeprowadzanie analiz porównawczych między poszczególnymi zakładami, osiąganie poprawy jakości, wspieranie konserwacji predykcyjnej, wykorzystywanie mniejszej ilości zasobów i wiele innych” – mówi Sibbald, dodając, że cyfryzacja jest procesem ciągłym. „Możesz stać się lean tylko wtedy, gdy dostępne są prawidłowe dane porównawcze. A piękno naszego systemu polega na tym, że można go łatwo rozbudowywać i skalować”.
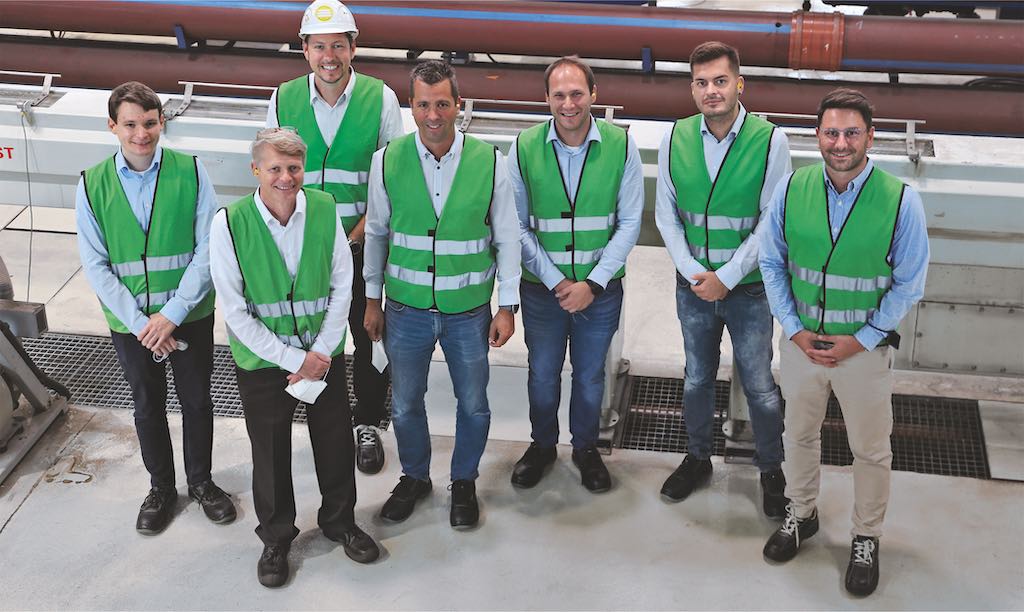
Ponadto przekładniki prądowe są obecnie coraz częściej umieszczane w zakładach produkcyjnych, ponieważ liczy się nie tylko każda minuta i każdy gram, ale także każda kilowatogodzina energii. W ten sposób projekt wnosi również znaczący wkład w realizację celów zrównoważonego rozwoju w zakresie redukcji emisji CO2, a także zużycia energii i surowców. Wraz z późniejszym wdrożeniem rozpoznawania kodów QR, możliwości adaptacyjne zainstalowanego rozwiązania zostały już udowodnione.
„Wszystko, co musieliśmy zrobić, to aktywować licencje na oprogramowanie wizyjne na IPC i podłączyć kamerę przez Ethernet, aby rozszerzyć bramę brzegową o TwinCAT Vision i włączyć przetwarzanie obrazu w czasie rzeczywistym” – mówi Balazs Bezeczky, szef biura sprzedaży Beckhoff w Wiedniu. „Oczywiście odczytane kody QR są przesyłane do chmury za pomocą TwinCAT IoT Data Agent. Dane są również dostępne do wykorzystania w systemach MES i ERP”.