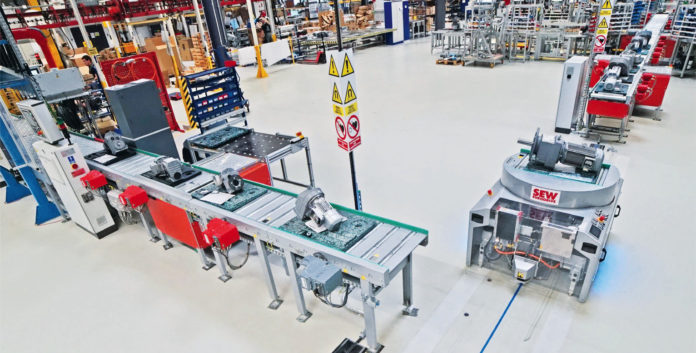
Dzisiejsza fabryka to środowisko pełne wyzwań dla działów utrzymania ruchu. Jednym z nich jest zwiększanie tempa pracy wraz z doskonaleniem przebiegu procesów produkcyjnych. Cele te w dobie Przemysłu 4.0 pomagają realizować roboty. Wśród nich ważne miejsce zajmują rozwiązania AGV i AIV, służące do transportu wewnętrznego w halach produkcyjnych, magazynach i centrach logistycznych.
Bezzałogowe, automatycznie sterowane pojazdy, które przemieszczają się po hali fabrycznej, przewożąc ładunki o różnych gabarytach i wadze – brzmi to jak zdobycz techniki ostatnich lat, a tymczasem pierwsze tego typu urządzenia pojawiły się już w 1954 r. Były to rozwiązania o prostej konstrukcji, z nawigacją wykorzystującą system kabli, których obecność, nieraz w nadmiarze, w praktyce często utrudniała realizację innych prac na terenie zakładu. Przez tych kilkadziesiąt lat zmieniła się zarówno konstrukcja wózków, jak i metody ich nawigacji oraz sterowania. Współczesne rozwiązania AGV (Automated Guided Vehicles) i AIV (Automated Intelligent Vehicle) to roboty mobilne, których ruch odbywa się po wyznaczonym torze, jest sterowany automatycznie, a ich ingerencja w przestrzeń fabryki jest minimalna.
Zalety i korzyści z zastosowania
Współczesne wózki bezzałogowe mają mniejszą wagę, gdyż zrezygnowano w nich z dużych akumulatorów. Ponadto zapewniają większe bezpieczeństwo ludziom, ich obecność pociąga bowiem za sobą konieczność wydzielenia tras przeznaczonych do ruchu pieszego i bezwzględnego przestrzegania zasad BHP. Automatyczne wózki samojezdne sprawdzają się jednak nie tylko wtedy, gdy chodzi o zagwarantowanie bezpieczeństwa ludziom znajdującym się na trasach ich przejazdu – w wielu sytuacjach bezobsługowe AGV mogą wyręczyć ludzi w miejscach, gdzie niebezpieczeństwem jest duży ruch np. wózków widłowych.
Pojazdy bezzałogowe odgrywają coraz większą rolę w środowisku produkcyjnym, a ich zastosowanie może znacznie ułatwić operacje obejmujące produkcję just-in-time i just-in-sequence, optymalizować przepływy logistyczne w zakładzie, a także poprawić zarządzanie magazynem. Ich wykorzystanie zwiększa efektywność i przepustowość transportu. Roboty mobilne znacznie redukują liczbę błędów związanych z transportem wewnątrzzakładowym i umożliwiają śledzenie przepływu materiałów w przedsiębiorstwie. Odciążają też pracowników, dzięki czemu mogą oni skupić się na zadaniach bardziej wymagających i skomplikowanych niż transport materiałów w obrębie fabryki.
Jak mówi Paulina Bubek, Sales Assistant w firmie Omron, zaletą większości rozwiązań AGV i AIV jest również stosowanie systemu nawigacji opartego na istniejącym układzie przestrzeni w zakładzie, dzięki czemu przy ich wdrażaniu nie są potrzebne kosztowna i czasochłonna przebudowa czy dostosowanie infrastruktury, w przeciwieństwie do kosztów ponoszonych przy wdrażaniu tradycyjnych systemów transportu. – Roboty mobilne wykorzystują proces samoczynnego mapowania przestrzeni i szukania na bieżąco optymalnej drogi transportu. Ta cecha zapewnia dużą elastyczność systemu i umożliwia bezproblemową zmianę organizacji przestrzeni w zakładzie, jeśli jest taka potrzeba – dodaje Paulina Bubek.

Różne rozwiązania – wiele możliwości
Przy wyborze rozwiązań AGV i AIV należy zwrócić uwagę przede wszystkim na ich zastosowanie. Ze względu na sposób transportu urządzenia tego typu dzieli się na kilka grup: pojazdy holownicze – umożliwiające przewóz kilku ładunków jednocześnie, pojazdy pojedynczego załadunku – w postaci platformy mobilnej, przystosowane do transportu ładunku o różnych rozmiarach i kształtach, a także wózki widłowe – obsługujące np. palety, rolki, specjalne stojaki na poziomie podłogi lub na podwyższeniu oraz używane do magazynowania ładunków na regałach.
Na wybór rodzaju pojazdu często ma również wpływ sposób wyznaczenia trasy, po której będzie się on poruszał. Najprostsze, najmniej zawodne i jednocześnie najtańsze wersje AGV są najczęściej sterowane przy użyciu taśmy magnetycznej. Poruszające się po niej pojazdy są wyposażone w czujniki magnetyczne lub optyczne. Taką taśmę można łatwo i tanio zainstalować, a wyznaczona w ten sposób trasa może być modyfikowana sprawnie i tak często, jak to konieczne. Możliwy jest również wariant, w którym trasa jest wytyczona taśmą magnetyczną, a poszczególne stacje, zakręty, punkty hamowania odczytywane są za pomocą kodów DataMatrix. Specjalistyczną, odporną na mechaniczne uszkodzenia taśmę naklejaną na trasie przejazdu mogą też śledzić kamery. Z kolei w przypadku metody indukcyjnej w podłodze w kanale zostaje umieszczony pojedynczy przewód, w którym przepływ prądu generuje pole magnetyczne wychwytywane przez antenę wózka poruszającego się zgodnie ze ścieżką sygnału. W tym przypadku problematyczna jest jednak zmiana trasy przejazdu.

Kolejną metodą jest wykorzystanie do nawigacji fal radiowych, proponowane m.in. przez RB Poland. Firma oferuje system AgWay, w którym nie jest potrzebna taśma. – Stosowanie tras znaczonych taśmą jest często kłopotliwe ze względu na intensywność ruchu np. wózków widłowych. Taśmy są zrywane i wymaga to dodatkowych nakładów, a przede wszystkim czasu. W przypadku zastosowania systemu radiowego wiele trudności w utrzymaniu ruchu zostaje łatwo rozwiązanych – mówi Elżbieta Mocna, Sales Director w RB Poland.
Na popularności zyskuje też laserowe mapowanie terenu, czyli LMS. Nowoczesne wózki AGV, wykorzystując skaner laserowy, odpowiednie oprogramowanie oraz naturalne otoczenie zakładu, tworzą wirtualną mapę otoczenia, pozwalającą na automatyczne i w pełni bezpieczne dla człowieka przemieszczanie się pojazdów w zmiennej przestrzeni fabryki. Jak wyjaśnia Joanna Sławińska, koordynator działu marketingu w firmie WObit, wyznaczając trasę wózków sterowanych za pomocą systemu LMS, należy najpierw przeanalizować procesy realizowane w produkcji lub w magazynie oraz określić miejsca, w których pojazd będzie się musiał zatrzymywać. Następnie tworzona jest wirtualna mapa. – Robot wyposażony jest w skaner laserowy o kącie skanowania 270° i częstotliwości 120 skanów na sekundę – wyjaśnia Joanna Sławińska na przykładzie pojazdów oferowanych przez WObit. – Przejeżdżający powoli przez całą trasę robot AGV skanuje przestrzeń, wysyłając wiązki laserowe w różnych kierunkach, a następnie mierzy czas, w którym powrócą one do detektorów. Na tej podstawie robot tworzy w swojej pamięci chmurę punktów układających się w ściany, stoły itp., czyli wirtualną mapę przestrzeni, w której będzie się poruszał. Zebrane dane przesyłane są do komputera umieszczonego w urządzeniu, wyposażonego w oprogramowanie do analizy pozycji na podstawie skanów otoczenia. Za jego pośrednictwem generowana jest wstępna mapa otoczenia. W celu uzyskania określonej precyzji pozycjonowania proces skanowania wykonywany jest kilkukrotnie. Następnie nanoszone są poprawki na mapę i usuwane błędy powstałe w wyniku poślizgów czy błędnej odometrii (pomiaru odległości – przyp. red.). Na koniec weryfikowana jest poprawność nawigacji i robot jest gotowy do pracy.
Wybierając system AGV czy AIV, trzeba przede wszystkim zwrócić uwagę na elementy, które są najważniejsze z punktu widzenia potrzeb danej firmy i pozwolą na ich optymalne zaspokojenie. Takimi przykładowymi parametrami – oprócz rodzaju wózka czy sposobu nawigacji – mogą być udźwig pojazdów, maksymalny czas pracy między kolejnym ładowaniem baterii, algorytm wyboru optymalnej trasy czy typowe aspekty techniczne, np. gabaryty towaru, sposób załadunku, prędkość przejazdu.
Jak mówi Krzysztof Szafraniec, dyrektor techniczny i członek zarządu w firmie Lean-Tech, bardzo istotną kwestią jest doświadczenie w implementacji takich systemów: – Często klienci nie zdają sobie sprawy ze stopnia zaawansowania takiego systemu. Wtedy starają się własnym sumptem opracować takie rozwiązanie lub zlecają je firmom, które nie mają odpowiedniej wiedzy. Konsekwencje są takie, że systemy te nie działają poprawnie. – Oprócz wyboru odpowiedniego typu pojazdu i metody jego nawigowania warto więc dobrze przeanalizować doświadczenie i oferty poszczególnych firm.

Co wybrać?
Na polskim rynku dostępne są rozwiązania o różnych zastosowaniach i odpowiadające na różne potrzeby zakładów produkcyjnych, magazynów i centrów logistycznych.
Firma Keyence posiada skanery bezpieczeństwa serii SZ-V do montażu na wózkach samojezdnych (AGV), sygnalizujące obecność obiektów lub osób na drodze wózka. Skanery pozwalają uniknąć szkód i wypadków powodowanych kolizją wózka z obiektem na jego drodze. Tym samym przyczyniają się do redukcji przestojów na hali produkcyjnej lub w magazynie. Skanery mają wbudowane dwie kamery, które rejestrują historię zdarzeń w postaci zdjęć lub filmów. Przemiatanie przestrzeni wiązką lasera pozwala rozpoznać przestrzeń przed skanerem bezpieczeństwa. Użyteczna jest również możliwość
rozdzielenia jednostki skanującej od sterującej skanera bezpieczeństwa.
Jedną z firm oferujących pojazdy AGV jest Lean Tech – przedsiębiorstwo, które proponuje własną koncepcję iCart – system pojazdów sterowanych automatycznie. Jak zapewniają przedstawiciele firmy, jest on prosty do wdrożenia i zainstalowania oraz działa bez programowania przez użytkownika. Wykorzystuje inteligentną kombinację wielu technologii komunikacji radiowej i oprogramowanie adaptacyjne do dostarczania części i produktów w miejscu pracy. System rozpoznaje trasę, odczytując zamontowane w podłodze znaczniki RFID, kierujące iCart do stanowisk i wskazujące funkcje do wykonania.
Rozwiązanie iCart powstało z myślą o pracy w większości środowisk produkcyjnych i przy liniach produkcyjnych. Znajduje zastosowanie przy dostarczaniu i pobieraniu w wielu punktach. Mały rozmiar pojazdu umożliwia jego jazdę po wąskich przejściach i mijanie innych wózków. Inteligentny zaczep u góry systemu iCart pozwala na automatyczne zaczepienie i odczepienie wózków o ładowności do 0,5 tony. Oznacza to, że iCart może odczepić pełny wózek i pobrać pusty w tym samym cyklu pracy.
W ofercie firmy dostępne są także wózki z napędzanymi przenośnikami rolkowymi, do transportu standardowych pojemników przemysłowych z plastiku, bezpośrednio do i ze stanowisk roboczych. Drugim wariantem systemu iCart jest iCart Cube. Wózek-sześcian jest lepiej dostosowany do typowego holowania, wykorzystującego istniejące wózki. Model ten jest w stanie przewozić ładunki o wadze do 1,5 tony.

RB Poland oferuje AGV jako standardowe rozwiązania do transportu wózków, palet (w formie pociągów – typ T, regały samoprzeładunkowe – typ Z czy też typ S, który podjeżdża pod wózek z ładunkiem, automatycznie o niego zahacza, transportuje do miejsca przeznaczenia i pozostawia w nim towar). Produkowane przez RB Poland pojazdy AGV mogą transportować ładunek o wadze do 3,5 ton. Obecnie firma wprowadza na rynek nowość – AGV-Liner do automatycznego, bezobsługowego załadunku i rozładunku palet o maksymalnym ciężarze 2,5 tony, a ponadto wdraża nowatorski system nawigacji radiowej. Rozwiązania wprowadzane przez RB Poland są systemami kompleksowej automatyzacji, tzn. opierają się na komunikacji pomiędzy stanowiskiem nadzorcy a linią produkcyjną (przyzywanie AGV po odbiór wyrobów lub dostarczenie pustych opakowań), ustalają pierwszeństwo ruchu dla innych pojazdów, określają ruch na skrzyżowaniach, automatycznie otwierają bramy itd. – Wychodzimy naprzeciw potrzebom klienta, który dąży do zminimalizowania interwencji człowieka. Wszystkie proponowane przez nas rozwiązania funkcjonują na bazie naszego własnego software’u i w oparciu o ponaddziesięcioletnie doświadczenie w tej branży – przekonuje Elżbieta Mocna.
Z kolei w ofercie firmy Omron dostępne są roboty mobilne AIV serii LD, które można konfigurować na różne sposoby. Konstrukcja ich podstawy jezdnej jest ujednolicona, natomiast w zależności od zastosowania modyfikuje się górną sekcję. Trzy warianty bazowe: platforma, przenośnik lub transporter wózków pozwalają na różnorodne zastosowanie pojazdów Omron. Roboty mobilne AIV z platformą są półautonomicznymi pojazdami, wymagającymi ręcznego załadowania i rozładowania. Platforma mobilna OEM jest dostępna dla projektantów niestandardowych rozwiązań urządzeń transportu ładunków. Przygotowana jest w dwóch wersjach, z czasem działania do 19 godzin dziennie: LD60 z możliwością transportu do 60 kg oraz LD90 z możliwością transportu do 90 kg. Roboty AIV, które wykorzystywane są w postaci przenośników oraz transporterów wózków, są w pełni autonomicznymi pojazdami.
Transportery wózkowe Omron są zaprojektowane do podłączania do ruchomych wózków i transportowania ich z punktu odbioru do punktu dostawy. Pojazdy te wykorzystywane są głównie w celu uzupełniania stanu linii produkcyjnej, transportu półproduktów pomiędzy etapami procesu produkcji oraz do przewożenia produktów gotowych do magazynu. Transportery wózkowe dostępne są w dwóch konfiguracjach: LD-105CT o nośności 105 kg oraz LD-130CT o nośności 130 kg. – Wszystkie roboty mobilne naszej firmy wyposażone są w nawigację, która wykorzystuje naturalne elementy przestrzeni zakładu, aby autonomicznie znajdować drogę przez zakład bez konieczności jego przebudowy – wyjaśnia Paulina Bubek. – Dzięki wbudowanym laserom i czujnikom bezpieczeństwa transporter wózkowy potrafi wykryć i ominąć ludzi, wózki widłowe i inne przeszkody, znajdując przy tym alternatywną drogę. Wózki są też wyposażone w urządzenia sygnalizacyjne i głosowe, aby bezpiecznie poruszać się między ludźmi, a w razie potrzeby poprosić ich o udostępnienie przejazdu.
Firma SEW-EURODRIVE ma w swojej ofercie wózki AGV w kilku wariantach. W wersji ze stołem obrotowym i przenośnikiem rolkowym wózek ma możliwość pobrania ładunku (np. palety) w linii prostej oraz wyładowania go po obróceniu o 90° poprzecznie do toru jazdy (możliwa jest także odwrotna kolejność). Wersja z poprzecznym przenośnikiem rolkowym umożliwia pobieranie i wyładowywanie ładunku na obydwie strony w stosunku do toru jazdy. Z kolei w wersji z przenośnikiem łańcuchowym i poprzecznym przenośnikiem rolkowym wózek może pobierać lub wyładowywać ładunek w kierunku toru jazdy oraz pobierać i wyładowywać go bez obracania, poprzecznie do toru jazdy. Pojazdy nawigowane są dzięki antenom śledzącym zasilanie bezprzewodowe Movitrans lub głowicom optycznym śledzącym taśmę naklejoną na posadzce. Wózki dojeżdżają do zadanych pozycji w trybie automatycznym. Funkcje transportowe pojazdów uzgadniane są każdorazowo z klientem i mogą być dostosowywane do potrzeb, z uwzględnieniem zasilania, nawigowania oraz sterowania. Podstawowe rozwiązania to pojazdy umożliwiające transport palet lub skrzyń o wagach 1 oraz 2 ton i kilku możliwościach pobierania i wyładowywania ładunku.

Firma WObit oferuje serię robotów MOBOT AGV własnej produkcji, na którą składa się sześć typów robotów. Różnią się one między sobą transportowaną masą – od 100 kg do 1,5 tony, wymiarami oraz układem napędowym. Zadaniem robotów jest automatyczne ciągnięcie wózka transportowego między wyznaczonymi punktami. Wózek podczepiany jest nad robotem przez system dwóch wysuwanych trzpieni. – Kompaktowa konstrukcja oraz system dokowania wózków wyróżnia roboty MOBOT AGV, gdyż pozwala na ich łatwe przezbrojenie do transportu zupełnie innego rodzaju produktów poprzez zwykłą zmianę wózka, np. z paletowego na wyposażony w rolki grawitacyjne lub z napędem elektrycznym – zapewnia Joanna Sławińska. Najnowsze modele MOBOT AGV FlatRunner MW oraz MOBOT AGV eRunner mogą transportować detale również na sobie. W ofercie firmy jest także robot MOBOT AGV FlatRunner MW, o nieograniczonej mobilności, który dzięki wyposażeniu w koła typu Mecanum Wheels może się poruszać w dowolnym kierunku. Do nawigacji wózków MOBOT AGV, w zależności od potrzeb klienta, wykorzystywane są: linia kolorowa z kodami QR/tagami RFID, linia magnetyczna + tagi RFID lub system LMS. Urządzenia pracują do 12 godzin na jednym ładowaniu (w zależności od modelu), co zapewniają dwa akumulatory, które są umieszczone w specjalnych kasetach umożliwiających szybką wymianę (<3 min). Roboty MOBOT AGV mogą być ładowane również za pomocą stacji ładującej, podłączanej ręcznie bądź automatycznie. Wszystkie urządzenia mogą bezpiecznie pracować bezpośrednio pomiędzy ludźmi dzięki wyposażeniu ich w skaner laserowy z funkcją bezpieczeństwa. Odpowiada on za detekcję wszelkich przeszkód pojawiających się przed robotem i odpowiednią reakcję gwarantującą uniknięcie kolizji.

Podsumowanie
W dobie postępującej czwartej rewolucji w przemyśle bezzałogowe pojazdy wewnątrzzakładowe przestają być udogodnieniem, a stają się koniecznym elementem wyposażenia. Inżynierowie poszukujący usprawnień w swoich fabrykach, magazynach i centrach logistycznych mają z czego wybierać. Warto więc przeanalizować ofertę rynkową i wybrać odpowiedni pojazd AGV lub AIV, który znacząco zwiększy efektywność pracy zakładu i odciąży pracowników, przekierowując ich do wykonywania innych zadań.
Anna Strożek – dziennikarka i redaktorka od wielu lat współpracująca z prasą branżową. Interesuje się nowymi technologiami i praktyczną realizacją koncepcji Przemysłu 4.0.