W artykule opisujemy, jak stosowanie podejścia warstwowego do bezpieczeństwa w automatyce przemysłowej przynosi optymalne wyniki.
Rozważania na temat projektowania i wdrażania systemów bezpieczeństwa w automatyce procesowej są obszerne. Aby w pełni rozwiązać każdy z możliwych problemów w tej dziedzinie, potrzebne jest specjalistyczne szkolenie. W rzeczywistości przed zaplanowaniem każdego systemu związanego z bezpieczeństwem ważne jest, aby posiadający odpowiednie certyfikaty specjaliści przeprowadzili w danym zakładzie przemysłowym audyt bezpieczeństwa. Jego celem jest ocena warunków panujących w tym obiekcie i określenie prawidłowej ścieżki zaprojektowania systemu zabezpieczeń. Częściowo jest to spowodowane faktem, że normy, standardy i przepisy bezpieczeństwa zmieniają się wraz z upływem czasu, dlatego też koncepcja „zawsze tak to robiliśmy” nie ma w tym przypadku zastosowania.
Z drugiej strony dobry projekt systemu bezpieczeństwa w automatyce przemysłowej niemal zawsze obejmuje podejście wielowarstwowe, łączące właściwe produkty, praktyki projektowe oraz szkolenia operacyjne. Pierwszym krokiem na drodze do uzyskania bezpiecznego miejsca pracy jest wykonanie oceny ryzyka w celu identyfikacji potencjalnych problemów, następnie zaś celem staje się obniżanie poziomu zagrożeń poprzez ich ograniczanie. Aby opracować najbardziej efektywne metody ochrony pracowników w zakładzie, stosuje się podejście hierarchiczne do metod technicznych oraz administracyjno-organizacyjnych BHP.
Zrozumienie koncepcji odnoszących się do bezpieczeństwa przynosi korzyści wszystkim, zarówno projektantom, jak i pracownikom działów operacyjnych zakładu, nawet jeśli ich podstawowe obowiązki w pracy nie obejmują tworzenia aktualnych, szczegółowych projektów systemów bezpieczeństwa. Ważne jest, aby rozumieć najczęstsze tematy związane z projektowaniem systemu zabezpieczeń oraz opracować informacje ogólne na temat tego systemu do przekazania pracownikom zakładu.
Hierarchia działań i metod ograniczania ryzyka zawodowego w przemyśle
W przypadku każdego urządzenia wykorzystującego automatykę przemysłową projekt tych systemów z pewnością odgrywa pewną rolę, jeśli chodzi o bezpieczeństwo. Jednak projekt zabezpieczeń, które będą skutecznie chroniły pracowników, jest koncepcją znacznie szerszą, rozciągającą się na właściwości fizyczne oraz użytkowanie rozważanego sprzętu.
Tradycyjne podejście projektantów zabezpieczeń polega na przeanalizowaniu kilku warstw w hierarchii środków kontroli zagrożeń w celu stworzenia kompletnego rozwiązania bezpieczeństwa.
Termin „hierarchia kontroli zagrożeń” nie odnosi się do sterowania w czasie rzeczywistym, tylko definiuje kroki, jakie powinni wykonać użytkownicy w celu kontrolowania i ograniczania zagrożeń stwarzanych przez każde urządzenie czy instalację. Często projektant może zastosować wiele możliwych kroków, które mogą się ze sobą wzajemnie łączyć do pewnego stopnia. Opisywany proces obejmuje pięć warstw.
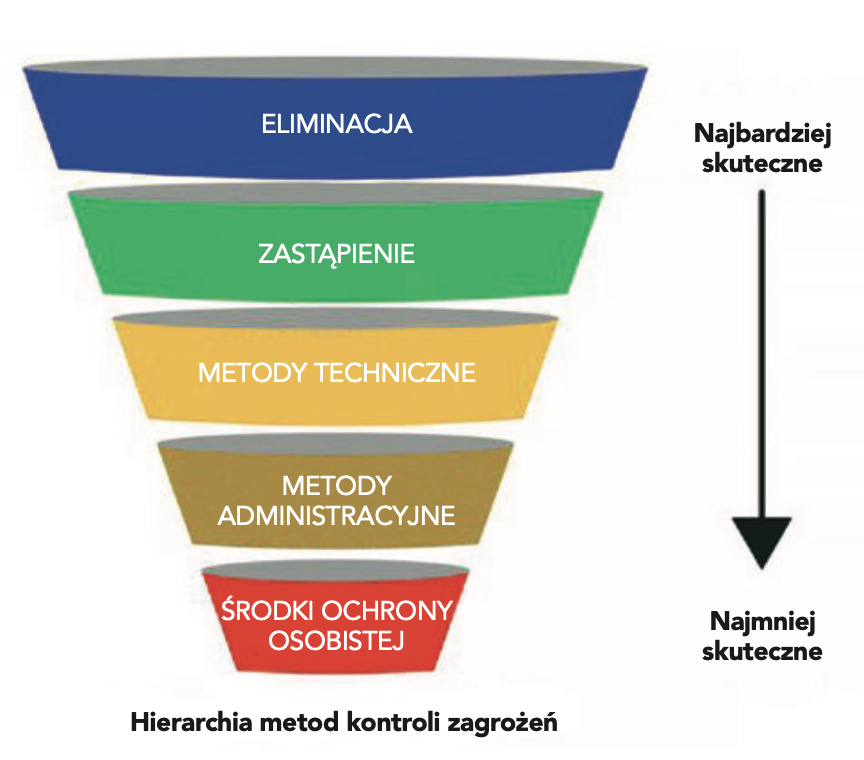
- Eliminacja zagrożeń w celu zmniejszenia ryzyka
Najlepszą i najskuteczniejszą metodą ograniczania ryzyka jest jego eliminacja, która oznacza usunięcie źródła potencjalnego zagrożenia. Niestety opcja ta przeważnie nie jest realna, ponieważ większość maszyn i procesów technologicznych nie może być zaprojektowana tak, aby usunąć wszelkie możliwe zagrożenia. Jednak projektanci powinni zawsze rozważyć eliminację ryzyka jako opcję.
Na przykład maszyna może posiadać łatwo otwierany właz inspekcyjny, co naraża jej użytkowników na potencjalne niebezpieczeństwo. Właz ten można by zastąpić zamontowaną na stałe pokrywą metalową, jednak będzie to stanowiło problem dla pracowników utrzymania ruchu. Być może zainstalowanie wyłącznika bezpieczeństwa z blokadą oraz przerobienie włazu tak, aby można go było otworzyć tylko przy użyciu narzędzi, byłoby w tej sytuacji lepszym podejściem.
- Zastępowanie zagrożeń w celu zmniejszenia ryzyka
Nawet jeśli jakiegoś zagrożenia nie można wyeliminować, to może okazać się wykonalnym jego zastąpienie, czyli zamiana źródła zagrożenia na inne, które stwarza mniejsze zagrożenie albo wymaga rzadszego dostępu, choć czasami nie jest to możliwe. Rozważmy na przykład sprzęt, w którym stosowane są chemikalia. Można by spróbować zastąpić dotychczas stosowaną substancję inną – bezpieczniejszą z punktu widzenia palności lub toksyczności. Nawet jeśli ta bezpieczniejsza substancja jest droższa, to często może okazać się warta zakupu, gdyż zakład uzyska dzięki temu korzyści w postaci wydajniejszej pracy oraz mniejszej liczby potencjalnych wypadków.
Kontynuując nasz przykład z włazem inspekcyjnym maszyny – być może okienko inspekcyjne ze szkła odpornego na uderzenia mogłoby zastąpić właz. Pracownicy mogliby wtedy dokonywać inspekcji urządzenia bez narażania się na niebezpieczeństwo ze strony jej mechanizmu.

- Metody techniczne zmniejszania ryzyka
Co prawda zawsze jest ważne, aby przeanalizować pierwsze dwa szczeble hierarchii, jednak realia są takie, że dla nowoczesnego, zautomatyzowanego sprzętu następnym krokiem jest często zastosowanie technicznych środków tam, gdzie będzie realizowane największe ograniczenie ryzyka. Środki techniczne zmniejszania ryzyka mogą być proste lub złożone oraz przyjmować wiele różnych form, jak podajemy poniżej:
- Fizyczne: dodanie bramek, osłon, ścian, klatek i słupków. Są to proste, ale bardzo ważne sposoby zabezpieczania użytkowników (Fot. 2).
- Czujniki i wyłączniki bezpieczeństwa. Wiele czujników może wykrywać niebezpieczne warunki lub być wyzwalanych ręcznie przez użytkowników w celu sygnalizacji i zmniejszenia zagrożenia. Urządzenia te to: przyciski awaryjne (e-stop), linki awaryjne e-stop, kurtyny świetlne, wyłączniki krańcowe oraz inne. Do zainicjowania wyłączenia awaryjnego można wykorzystać każdy z dostępnej gamy czujników i wyłączników, przewodowych i ewentualnie połączonych szeregowo (Fot. 3).
- Blokady: niektóre urządzenia bezpieczeństwa blokują mechanicznie dostęp użytkownikom do niebezpiecznego sprzętu aż do chwili, gdy sprzęt ten przestanie stwarzać zagrożenie.
- Odłączenie od źródła energii. Czujniki, wyłączniki oraz blokady bezpieczeństwa mogą być połączone przewodowo z przekaźnikami lub sterownikami bezpieczeństwa, które odłączają energię od silników, siłowników oraz innych urządzeń, które w innym przypadku mogłyby stanowić zagrożenie dla użytkowników. Energia może być dostarczana do urządzeń w kilku formach: z sieci elektroenergetycznej, innych źródeł napięcia oraz (co jest często pomijane) z instalacji sprężonego powietrza, a nawet w postaci energii hydraulicznej. Czujniki lub wyłączniki bezpieczeństwa mogą być połączone przewodowo z zabezpieczanymi urządzeniami, aby odłączać ich zasilanie, bądź też mogą stanowić część bardziej złożonego obwodu z połączeniami przewodowymi, obejmującego posiadający większe możliwości przekaźnik czy cyfrowy sterownik bezpieczeństwa. Sterowniki bezpieczeństwa to zaawansowane urządzenie cyfrowe, mające duże możliwości konfiguracji za pomocą oprogramowania oraz komunikacji z systemami wyższego poziomu.
- Usunięcie zagrożenia ze strony energii kinetycznej: niektóre systemy fizyczne wymagają dodatkowej uwagi w celu zapobieżenia zagrożeniom przez elementy będące w ruchu nawet po wyłączeniu zasilania za pomocą przycisku e-stop. Obwody pneumatyczne mogą wymagać szybkiego zaworu upustowego do zmniejszania ciśnienia w siłownikach, aby zapobiec wykonywaniu przez nie ruchu. Sprzęt taki jak prasy pionowe lub nożyce może wymagać zastosowania stoperów mechanicznych, które zapobiegają grawitacyjnie ruchowi po wciśnięciu przycisku e-stop. Układy mechaniczne z napędem silnikowym mogą wymagać hamulców do zatrzymania ruchu obrotowego po zatrzymaniu awaryjnym
- Specjalne wykonanie zabezpieczeń: wspomniane wyżej zabezpieczenia w postaci czujników, wyłączników, blokad, przekaźników i sterowników posiadają specjalne konstrukcje z podwójnymi stykami elektrycznymi oraz innymi środkami wdrażania zasady uszkodzenia w kierunku bezpiecznym (ang. failsafe). Standardowe wersje tych urządzeń nie są akceptowalne w układach bezpieczeństwa.
W naszym przykładzie z włazem inspekcyjnym maszyny można by zastosować techniczny środek kontroli zagrożeń w postaci wyłącznika bezpieczeństwa z blokadą. Zabezpieczenie to pozwala na otwarcie drzwi jedynie wtedy, gdy maszyna znajduje się w stanie bezpiecznym. Gdy drzwi są otwarte, wyłącznik uniemożliwia włączenie maszyny.
- Środki administracyjne zmniejszania ryzyka
Po wdrożeniu pierwszych trzech środków ważne jest, aby zająć się elementem ludzkim. Obejmuje to wszystkich projektantów, inżynierów i techników, pracowników utrzymania ruchu, wykonawców prac z firmy zewnętrznej, osoby wizytujące zakład oraz inne, które pracują ze sprzętem lub mają możliwość wejścia do obszaru niebezpiecznego.
Ważne jest tu, aby wdrożyć program szkoleń, które zaznajomią użytkowników z zagrożeniami dla bezpieczeństwa, praktykami pracy oraz prawidłowymi procedurami postępowania. Rygorystyczne procedury blokowania zasilania serwisowanych urządzeń oraz oznakowania ich przywieszkami ostrzegawczymi (LOTO) są niezbędne dla ochrony pracowników, którzy potrzebują bezpośredniego dostępu do tych urządzeń. Ponadto można stosować dodatkową warstwę ochrony w postaci wyraźnych etykiet, znaków oraz świateł ostrzegawczych i sygnalizacyjnych.
- Sprzęt ochrony osobistej (PPE) jako środek zmniejszania ryzyka
W większości obiektów przemysłowych sprzęt ochrony osobistej, taki jak okulary ochronne, douszne wkładki przeciwhałasowe, półmaski filtrujące, buty robocze BHP, rękawice robocze itd., jest standardowym wyposażeniem pracowników. W niektórych sytuacjach wymagane są dodatkowe środki w postaci ochrony przed upadkiem oraz odpowiednich szkoleń dla pracowników. Chociaż środki PPE są nieodzowne dla ochrony pracowników, to znajdują się na samym dole hierarchii środków kontroli zagrożeń i nie powinny być postrzegane jako ograniczające zidentyfikowane ryzyka, ponieważ są przysłowiową ostatnią deską ratunku. Ponadto stosowanie środków ochrony osobistej wymaga ciągłego wysiłku ze strony pracowników.
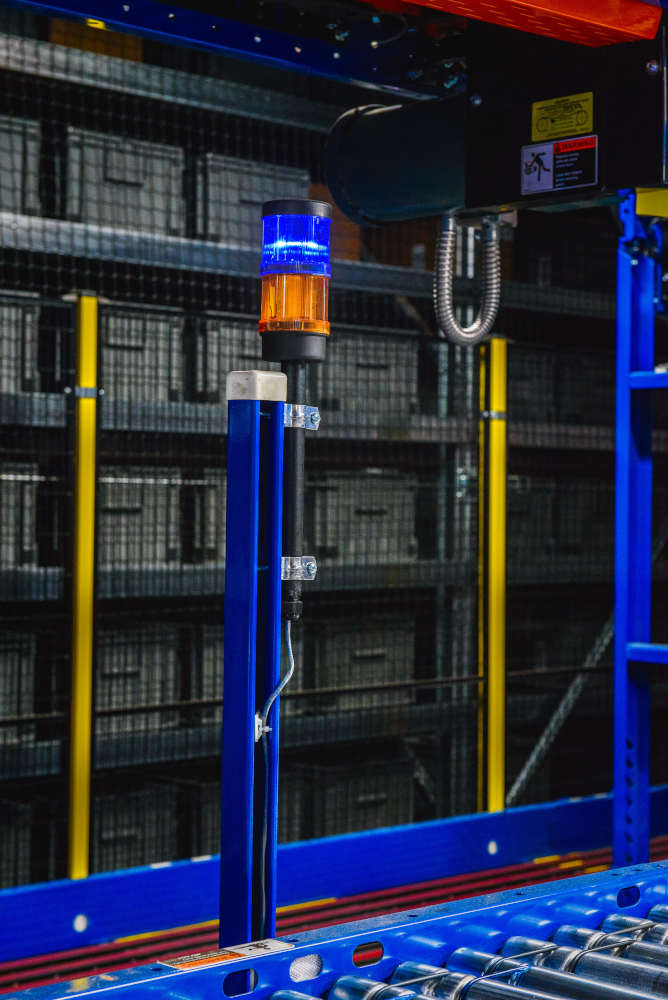
Ograniczanie ryzyka i zatwierdzanie projektów systemów zabezpieczeń
Po opracowaniu projektu systemu bezpieczeństwa wyniki muszą być zatwierdzone pod kątem zgodności ze standardem IOS 13849-2, aby zapewnić, że system ten rzeczywiście zmniejsza zagrożenia zidentyfikowane w ocenie ryzyka. Czasami proces ten może być nieco złożony, wymagający powtórzenia kilku etapów.
Przykładem może być tu praca nad zmniejszaniem zagrożeń w etapach eliminacji i zastąpienia. Przeważnie tworzone są tu nowe czynniki ryzyka. Dlatego po zakończeniu procesu zatwierdzania musi być wykonana nowa ocena ryzyka. Wykorzystanie oceny ryzyka jako listy kontrolnej nie wystarczy.
Ponadto niektóre standardy w USA mówią, że ocena ryzyka musi być wykonywana okresowo (ANSI/RIA R15.06). Nakłania to użytkownika końcowego do wykonania ponownej analizy jego sprzętu przemysłowego w celu stwierdzenia, czy wszelkie zmiany w danym obszarze nie stworzyły nowych zagrożeń. Ponadto każdego roku pojawiają się nowe produkty oraz idee, które mogą poprawić bezpieczeństwo w zakładzie.
Gama rozwiązań w zakresie bezpieczeństwa w przemyśle
Tworzenie bezpiecznego sprzętu, systemów i automatyki przemysłowej nigdy nie jest zadaniem jednorazowym. Jest to ciągły cykl życia. Ponadto odpowiedzialność za bezpieczeństwo nie spoczywa na barkach tylko jednej osoby – inspektora BHP. Wszyscy pracownicy zakładu mają swój udział w projektach zabezpieczeń oraz bezpiecznej obsłudze sprzętu. Każde zadanie, od oceny ryzyka do zmniejszania zagrożeń i zatwierdzania projektu, powinno być wykonywane przez zespół. Innym zaleceniem jest tu wprowadzenie jakiegoś systemu kontroli i równowagi, na przykład jedne osoby zajmują się technicznymi środkami ochrony, a inne zatwierdzaniem projektu. Daje to więcej świadomości zespołowi i umożliwia patrzenie na temat z różnych perspektyw.
Do tworzenia projektów zabezpieczeń w przemyśle potrzeba wielu analiz i produktów technicznych. Pracownicy zespołu projektowego, pełniący wszystkie funkcje w danej firmie, mogą znaleźć pomocne informacje na stronach internetowych producentów i dostawców z branży automatyki przemysłowej. Na stronach tych znajduje się szeroka gama produktów, które można wdrożyć w danym zakładzie, aby powstały warstwy bezpieczeństwa.
Joshua Draa jest inżynierem produktu w firmie AutomationDirect. W ciągu swojej 14-letniej kariery pracował jako inżynier specjalista ds. automatyki i bezpieczeństwa w firmach zajmujących się integracją systemów w zakładach produkujących wyroby konsumenckie. Joshua Draa ma tytuł magistra inżyniera elektryka, uzyskany na Politechnice w Atlancie (Georgia Institute of Technology) oraz tytuł associate engineer, uzyskany na Uniwersytecie UNG (University of North Georgia).