Spośród zgłoszonych w tym roku do udziału w konkursie zakładów produkcyjnych jury doceniło należący do koncernu Bunge Zakład Produkcyjny ZT „Kruszwica” zlokalizowany w Brzegu. Dzięki wdrożeniu programu niezawodności polegającego na przejściu z reaktywnego UR na proaktywny obniżono w nim koszty utrzymania ruchu oraz zwiększono produktywność.
W zarządzaniu zakładem produkcyjnym liczy się dziś przede wszystkim efekt ekonomiczny. Na obniżenie kosztów produkcji składa się wykorzystanie nowych technologii oraz ograniczenie kosztów utrzymania ruchu. Inwestycje w nowe linie produkcyjne i modernizacje są, oczywiście, ważne, nie zawsze natomiast docenia się rolę, jaką odgrywa efektywność działu UR w efektywności całego przedsiębiorstwa. Przykład Zakładu ZT „Kruszwica” w Brzegu pokazuje, jakie możliwości dają nowoczesne metody diagnostyczne oraz zmiana strategii UR na proaktywną.

Od lewej stoją: Leszek Skibiński, kierownik działu utrzymania ruchu, Tomasz Lewicki, kierownik ds. predykcyjnego utrzymania ruchu i niezawodności oraz Krzysztof Urbanek, dyrektor zakładu. (Źródło: M. Kokot, IMAGING TECHNICS)
Nowoczesne utrzymanie ruchu
W 2010 r. Grupa Bunge wprowadziła w korporacji ARROP – Program Niezawodności Środków Trwałych i Optymalizacji Raportowania. Zakład w Brzegu rozpoczął wdrożenie w 2011 r.
W lutym tego roku dokonano analizy postępu ARROP w zakładach, które wprowadziły program. Efekty w fabryce w Brzegu były bliskie 100% oczekiwanego rezultatu (wynik średni – 80% – został osiągnięty przez 50% zakładów Bunge).
– Nasza fabryka okazała się najlepsza w Grupie pod względem wydajności i kosztów produkcji i jako jedyna została nagrodzona przez korporację za efekty wdrożenia programu – mówi Krzysztof Urbanek, dyrektor zakładu w Brzegu.
– W obszarze rozwoju niezawodności mamy wyjątkowe rezultaty. Do naszego zakładu przyjeżdża na szkolenia wiele osób z obrębu Grupy, nie tylko z Polski, ale i z całej Europy. Niezawodności w naszym zakładzie uczą się menedżerowie m.in. z Węgier czy Ukrainy – dodaje Tomasz Lewicki, kierownik ds. predykcyjnego utrzymania ruchu i niezawodności.
Policzalne efekty
Celem wdrożenia programu niezawodności było obniżenie kosztów operacyjnych utrzymania ruchu. W 2011 r. koszty UR w odniesieniu do wartości odtworzeniowej zakładu (Total Maintenance Cost/Replacement Asset Value – RAV) wynosiły 3,15%. W ciągu 5 lat wskaźnik ten został obniżony do poziomu 1,5%. Ponadto znacznie zmniejszona została liczba nieplanowanych awarii – obecnie prace reaktywne stanowią mniej niż 3% wszystkich prac działu utrzymania ruchu. – Dzięki diagnostyce potrafimy przewidzieć zbliżającą się usterkę, a dzięki sprawnemu systemowi planowania ustalić dogodny termin współgrający z produkcją w celu przeprowadzenia działań korektywnych – mówi Tomasz Lewicki.
Efektem przeprowadzonego wdrożenia jest również zwiększona wydajność maszyn i urządzeń. Na przykład ekstraktor, od którego wydajności zależy poziom produkcji, początkowo miał wydajność ok. 1000 ton nasion na dobę, obecnie zaś przerabia 1680 ton.
Produkcja, historia, zatrudnienie
W fabryce w Brzegu produkuje się Olej Kujawski, w tym poszukiwane przez klientów jego odmiany smakowe, a także margaryny konsumenckie (kostkowe i kubkowe). Wytwarzana jest tu również lecytyna spożywcza oraz olej do produkcji biokomponentów. Zakład może pochwalić się długą tradycją w branży spożywczej. W 1936 r. uruchomiono tu cukrownię, ale już w 1950 r. wybudowano w tym miejscu nowe zakłady produkujące oleje spożywcze i margarynę. W 2007 r. zakład znalazł się strukturach ZT „Kruszwica” i koncernu Bunge – jednego z największych na świecie przetwórców nasion oleistych i producenta konfekcjonowanych olejów roślinnych. W fabryce w Brzegu zatrudnionych jest obecnie 258 osób. Dział utrzymania ruchu liczy 21 pracowników (łącznie z kierownikiem, planistami i diagnostami). |
Składniki przepisu na sukces
Najważniejszym działaniem, które zaowocowało opisanymi rezultatami, jest według Tomasza Lewickiego wprowadzenie metod diagnostycznych – badań ultradźwiękowych, wibracji, termografii – gospodarki smarowniczej opartej na diagnostyce i analizach olejowych, a także proaktywnego utrzymania ruchu bazującego na takich działaniach, jak laserowe osiowanie urządzeń czy dynamiczne wyważanie. Drugim elementem, który jego zdaniem zadecydował o sukcesie wdrożenia programu, jest planowanie i harmonogramowanie prac, mające na celu maksymalizację wydajności materiałów i minimalizację przestojów produkcyjnych. Trzecim czynnikiem, mającym wpływ na uzyskane wyniki, są wiedza i doświadczenie pracowników oraz odpowiednia komunikacja i współpraca zespołu UR z osobami zatrudnionymi w działach produkcyjnych.
Predykcja, gospodarka smarownicza i proaktywne UR
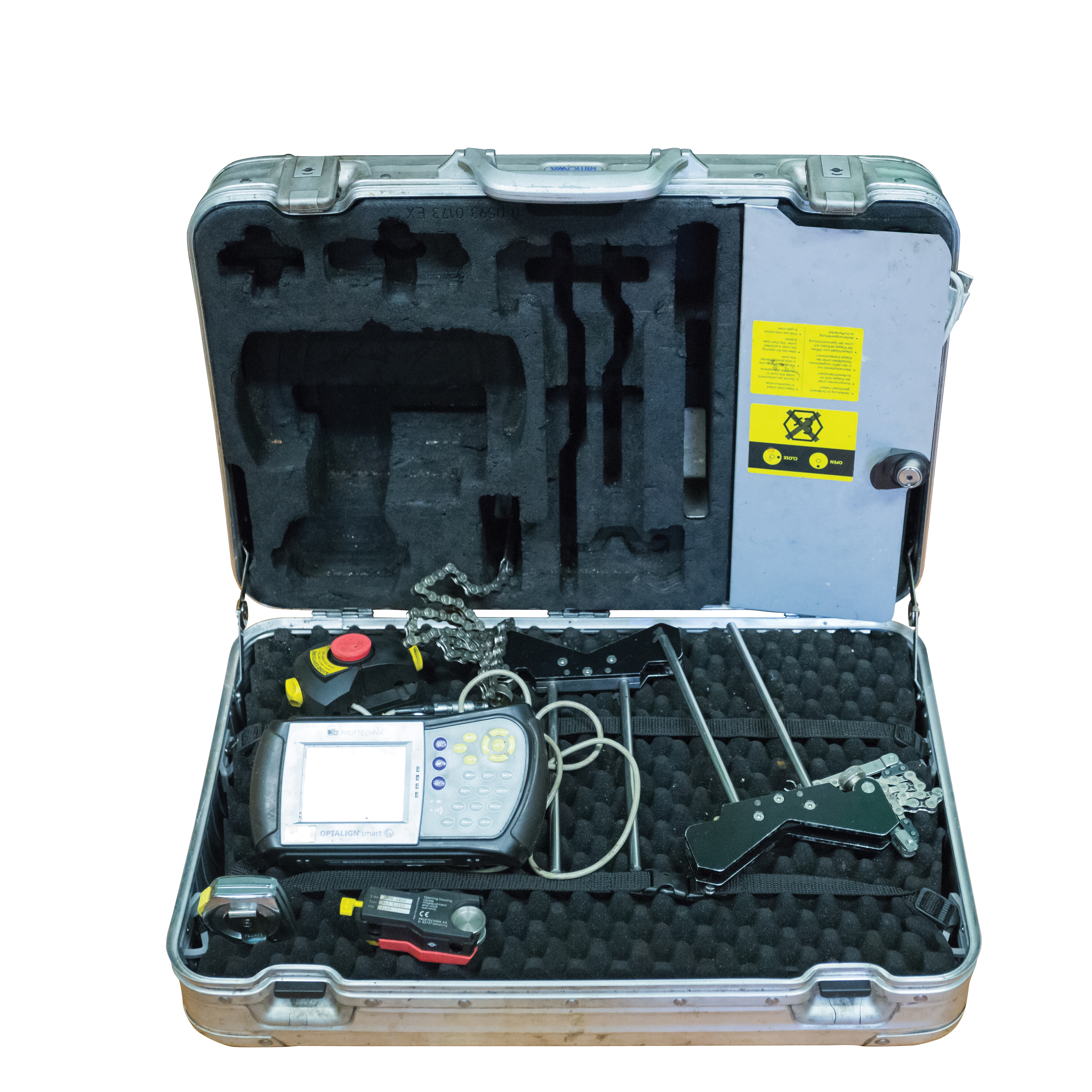
Badania ultradźwiękowe to technologia, która wykrywa objawy zużycia łożysk, sygnalizując problem już we wczesnej fazie powstawania awarii. – Wykorzystanie ultradźwięków umożliwia nam rozpoznanie problemu i zaplanowanie naprawy od kilku tygodni do kilku miesięcy przed faktycznym wystąpieniem awarii. Pozwala również na wykrywanie wszelkich nieszczelności, np. układów sprężonego powietrza – mówi Tomasz Lewicki.
Wibroakustyka to, jak mówią przedstawiciele zakładu, po ultradźwiękach druga najskuteczniejsza metoda detekcji potencjalnych uszkodzeń. – Zaletą wibroakustyki jest to, że daje nam nie tylko sygnał o pogarszającym się stanie maszyny, ale również obraz tego, czym może być on spowodowany. Dzięki wibroakustyce możemy z dużą dozą prawdopodobieństwa przewidzieć niewyważenie, niewyosiowanie, problemy z konstrukcją wsporczą i inne – stwierdza Tomasz Lewicki.
Badania termowizyjne natomiast wykorzystywane są do mierzenia osprzętu elektrycznego i mechanicznego. Wykorzystanie tej metody diagnostycznej umożliwia ograniczenie strat energii i wykrywanie obszarów o podwyższonej temperaturze, sygnalizujących miejsca potencjalnych awarii.
– Diagnostyka pozwala planować prace z dużym wyprzedzeniem. Nie trzeba gasić pożarów – dzięki diagnostyce można im zapobiegać – podsumowuje Leszek Skibiński, kierownik działu utrzymania ruchu.
W diagnostyce najważniejsza jest powtarzalność, dlatego w Zakładzie ZT „Kruszwica” w Brzegu zawsze ci sami pracownicy (dwie osoby) zajmują się diagnostyką ultradźwiękową i smarowaniem, diagnostyką wykorzystującą pomiary wibracji oraz badaniami termowizyjnymi.

W fabryce wdrożony jest program diagnostyczny i analiza olejowa prowadzona we współpracy z laboratorium firmy Ecol – próbki wysyłane są do badania, analizowane, a na podstawie wyników podejmuje się dalsze decyzje związane z eksploatacją. Sprawdzane parametry oleju to: zanieczyszczenia, zawartość wody, konsystencja oleju i zawartość pierwiastków (spektrometryczne badanie oleju ICP). Nie ma stałych interwałów czasowych wymiany oleju, co przynosi oszczędności przy zapewnieniu optymalnego smarowania. Tam, gdzie prowadzone jest smarowanie ręczne, w celu zapewnienia jego prawidłowego wykonania stosuje się smarownice ultradźwiękowe (od 2016 r. wykorzystuje się system UP401 Digital
Grease Caddy Pro firmy UE Systems). Badania oleju przed remontem rocznym pozwalają na podjęcie decyzji o wymianie oleju w przekładni lub, ewentualnie, o remoncie zgodnie z wynikami uzyskanymi w przeprowadzonych badaniach.

Pracownicy działu UR korzystają m.in. z techniki laserowego osiowania wałów (system Aligment firmy Pruftechnik – wynalazcy laserowego osiowania wałów) oraz dwuosiowego wyważania wentylatorów. Korzyści z ich zastosowania są np. widoczne w dziale ekstrakcji, gdzie pracuje 30 pomp. – Przed zastosowaniem technologii laserowego osiowania wałów, po remoncie rocznym, kiedy były one ponownie składane i uruchamiane, 45 pomp ulegało w krótkim czasie awariom. Obecnie nie ma takiego problemu – zauważa Tomasz Lewicki.
W celu zwiększenia niezawodności maszyn i urządzeń produkcyjnych oraz wydłużenia żywotności łożysk na wszystkich połączeniach wałów zakład wprowadza sprzęgła elastyczne firmy OMEGA.
Do montowania łożysk używana jest nagrzewnica indukcyjna, co eliminuje ryzyko ich uszkodzenia na etapie montażu przez np. użycie sił mechanicznych lub nierównomierne podgrzewanie jego części.
Elementy programu niezawodności ARROP
-> Lista minimalnego wyposażenia – MEL (ang. Minimum Equipment List)
-> Analiza krytyczności urządzeń
-> Gospodarka smarownicza
-> Analizy przyczynowo-skutkowe: RCA (ang. Root Cause Analysis) i FMEA (ang. Failure Mode and Effects Analysis)
-> Zdefiniowanie strategii niezawodności i uaktualnianie programu RCM (ang. Reliability Centered Maintenance)
-> Uruchomienie programu prewencyjnego i predykcyjnego utrzymania ruchu
-> Zestawienie materiałów, części zamiennych, podzespołów oraz informacji na ich temat – BOM (Bill of Materials)
Planowanie to podstawa
Jak mówią przedstawiciele zakładu, program ARROP to nie tylko najlepsze praktyki wykorzystujące diagnostykę. W jego ramach została utworzona baza danych urządzeń produkcyjnych i zaimplementowana do używanego systemu CMMS – API Pro. Zgodnie z ustaloną wcześniej krytycznością i wynikami prowadzonej diagnostyki w API Pro planowane są prace dla warsztatu działu UR. Planowanie i harmonogramowanie pozwala nie tylko na tworzenie historii prac, ale również planowanie zasobów, narzędzi oraz ustalanie, kiedy pracownicy mogą rozpocząć czynności remontowe w części produkcyjnej.

Pracownicy działu Olejarnia analizujący dane w systemie sterowania Delta V firmy Emerson. (Źródło: M. Kokot, IMAGING TECHNICS)
Inwestycje w sprzęt i wiedzę
Wdrożenie takiego programu jak ARROP wymaga inwestycji. Największy jej koszt w zakładzie w Brzegu stanowił zakup nowoczesnego sprzętu pomiarowego. Drugim w kolejności kosztem były szkolenia związane z diagnostyką.
Diagności zatrudnieni w zakładzie w Brzegu mają uprawnienia w zakresie badań termowizyjnych, ultradźwiękowych oraz wibroakustycznych, a także analiz olejowych (termografia: 2 osoby, ultradźwięki – Level 1: 6 osób, Level 2: 2 osoby, wibroakustyka – Level 1: 3 osoby, analizy olejowe: 20 osób). Jak dodaje Krzysztof Urbanek, jeśli chodzi o diagnostykę ultradźwiękową, dwóch diagnostów ukończyło drugi poziom szkoleń firmy UE Systems (tylko trzy osoby w Polsce mają takie uprawnienia).
Stałe doskonalenie i podnoszenie kompetencji pracowników jest, zdaniem przedstawicieli fabryki w Brzegu, podstawą funkcjonowania działu utrzymania ruchu. Zakład ściśle współpracuje z Urzędem Dozoru Technicznego oraz Naczelną Organizacją Techniczną. Prowadzone są szkolenia, np. spawaczy (rozszerzanie kompetencji spawalniczych, napawanie na zimno), automatyków (programowanie sterowników przemysłowych, systemy SCADA), wspomniane szkolenia diagnostów czy specjalistów w planowaniu, harmonogramowaniu i doskonaleniu utrzymania ruchu.
Pomysły na usprawnienia

Zakład w Brzegu jest dowodem na to, że to ludzie są jednym z najcenniejszych zasobów przedsiębiorstwa. Odpowiednio zmotywowani i zaangażowani, wykorzystują swoje talenty i umiejętności, by w kreatywny sposób rozwiązywać problemy.
Pracownicy warsztatu UR w zakładzie w Brzegu nie tylko modernizują maszyny produkcyjne, ale również projektują i wykonują własne. – W naszym warsztacie mimo nie najnowszego już parku maszynowego potrafimy wykonać wiele „patentów”. Pracownicy sami zgłaszają propozycje usprawnień – mówi Leszek Skibiński. Przykładami realizacji własnych pomysłów są: dozownik ziaren słonecznika prażonego dla rozlewni oleju, dwustopniowy układ filtracji olejów przekładniowych (75 μm/10 μm) oraz przenośnik łopatkowy dwuwałowy do transportu śruty.
Plany
Jak mówią przedstawiciele zakładu, w zakresie gospodarki smarowniczej pozostała do zrealizowania jeszcze jedna faza – centralizacja systemu smarowania. W 2017 r. ma być wybudowany centralny magazyn smarów i olejów, zgodnie ze standardami Noria Corporation. Pozwoli to zgromadzić środki smarne w jednym miejscu i przejąć całkowitą kontrolę nad smarowaniem w zakładzie.
Po zrealizowaniu tej fazy menedżerowie fabryki w Brzegu nie zamierzają jednak spocząć na laurach. – Inicjatywa została podjęta w 2011 r. i trwa do dzisiaj – jest to rodzaj działania typu „continous improvement”, czyli ciągłego doskonalenia – mówi Tomasz Lewicki. – Nasi pracownicy cały czas chcą się również szkolić i być na bieżąco z najnowszymi trendami w zakresie diagnostyki oraz proaktywnego utrzymania ruchu – podsumowuje Krzysztof Urbanek.
Autor: Bohdan Szafrański
Tekst pochodzi z nr 6/2016 magazynu „Inżynieria i Utrzymanie Ruchu”. Jeśli Cię zainteresował, ZAREJESTRUJ SIĘ w naszym serwisie, a uzyskasz dostęp do darmowej prenumeraty w formie drukowanej i/lub elektronicznej.