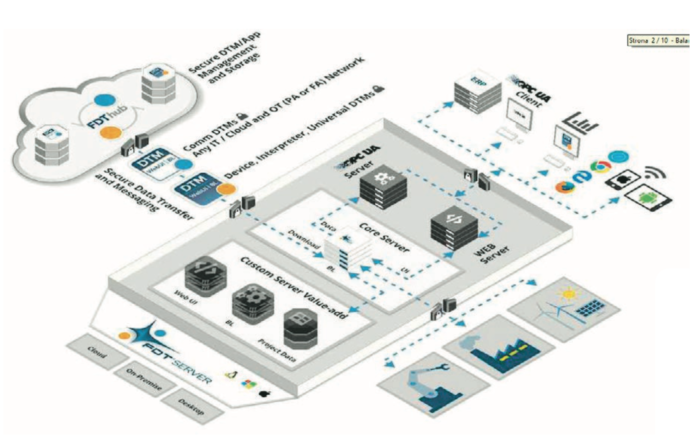
Zmodernizowana technologia Grupy FDT jest czynnikiem napędowym współpracy pomiędzy dostawcami systemów sterowania a dostawcami urządzeń dla przemysłu. Wynikiem tego jest oparty na chmurze monitoring zasobów w zakładach, który zwiększa ich niezawodność.
Dla dzisiejszych organizacji przemysłowych efektywne plany utrzymania ruchu w zakładach są kluczowe dla zapewnienia niezawodności i dyspozycyjności podstawowego sprzętu oraz jednoczesnego utrzymywania kosztów oraz zakłóceń w funkcjonowaniu na minimalnym poziomie.
Grupa FDT przez długi czas skupiała się na wspieraniu integrowania sieci informatycznych oraz urządzeń w zakładach, wprowadzając innowacyjne sposoby usieciowienia systemów automatyki oraz przesyłania w nich danych, będące częścią strategii zarządzania zasobami. Najnowsze postępy technologiczne uzyskane przez tę organizację przekształcają jej standard integracji w platformę wymiany informacji.
Umożliwia to realizację opartego na chmurze obliczeniowej monitoringu zasobów, przeznaczonego do głównych urządzeń realizujących procesy przemysłowe oraz dostarcza elastyczne rozwiązanie do wdrażania predykcyjnego utrzymania ruchu, opartego na technologii Przemysłowego Internetu Rzeczy (IIoT). Konserwacja prognozowana może zmniejszyć koszty serwisowania i zwiększyć niezawodność zasobów oraz dostarczyć użytecznych informacji personelowi utrzymania ruchu, wykonującemu prace na maszynach i urządzeniach w zakładach.
Uzyskiwanie równowagi pomiędzy kosztami eksploatacji a dyspozycyjnością zasobów
Właściciele/personel kierowniczy zakładów przemysłowych borykają się z problemem utrzymania równowagi pomiędzy obniżaniem kosztów eksploatacji a zwiększaniem dyspozycyjności zasobów. Efektywne zarządzanie zasobami odgrywa kluczową rolę w zapewnieniu utrzymywania tej równowagi, umożliwiając firmom zachowanie zgodności z przepisami i regulacjami, unikanie kosztów związanych z niepotrzebnymi pracami konserwacyjnymi oraz nieplanowanych przestojów.
Technologia IIoT wraz z inicjatywą Przemysłu 4.0 jest jednym z najbardziej znaczących trendów w automatyce przemysłowej, umożliwiając firmom produkcyjnym rozszerzanie swoich możliwości zarządzania monitoringiem stanu technicznego urządzeń oraz integralnością zasobów. Predykcyjne utrzymanie ruchu silnie zależy od technologii IIoT, która digitalizuje wskaźniki fizyczne, umożliwiając powstanie połączeń typu człowiek z człowiekiem, człowiek z maszyną oraz maszyna z maszyną, wykorzystywanych do inteligentnej analizy danych.
Zamiast wykonywania rutynowych inspekcji, opartych na zaplanowanych z góry terminach oraz wymianie komponentów/podzespołów, można wykorzystać inteligentne czujniki do monitorowania sprzętu, co pozwala wykrywać zbliżające się awarie i powiadamiać personel techniczny, gdy wymagane są prace serwisowe. Narzędzia konserwacji prognozowanej wykrywają odbiegające od normalnych warunki pracy sprzętu i alarmują personel, gdy zostaną przekroczone bezpieczne wartości graniczne.
Badania przeprowadzone przez firmę doradczą Deloitte wykazały, że dzięki wykorzystaniu rozwiązań predykcyjnego utrzymania ruchu, opartych na technologii IIoT, oczekuje się redukcji kosztów konserwacji sprzętu fabrycznego o 40%. Konserwacja prognozowana może też, według firmy doradczej PwC (PricewaterhouseCoopers), zmniejszyć zagrożenia dla bezpieczeństwa i zdrowia ludzi, środowiska naturalnego oraz jakości produktów o 14%, a także przedłużyć czas eksploatacji starzejących się zasobów o 20%.
Gdy strategia predykcyjnego utrzymania ruchu jest realizowana efektywnie, prace konserwacyjne na maszynach są wykonywane tylko w przypadku, gdy są one rzeczywiście wymagane. Dzięki temu zmniejsza się koszty ponoszone na części zamienne oraz robociznę przy wymianach. Natomiast personel utrzymania ruchu i operacyjny może się skupić na swoich podstawowych obowiązkach, nieplanowane przestoje zostają zminimalizowane i zwiększa się wydajność konserwacji.
Znaczenie rozwiązań mobilnych
Aby program predykcyjnego utrzymania ruchu został skutecznie wdrożony, musi zapewniać mobilność tych pracowników zakładów, którzy są odpowiedzialni za utrzymywanie sprzętu przemysłowego w dobrym stanie technicznym oraz zapobieganie jego awariom, poprzez planowanie i wykonywanie odpowiednich rutynowych prac konserwacyjnych.
Organizacje zmagające się z problemem odchodzących na emeryturę pracowników oraz starzejącego się sprzętu, muszą wyszukiwać i wykorzystywać każdą sposobność optymalizacji wydajności zakładów, zatrudniając i zatrzymując w firmach najbardziej utalentowanych specjalistów.
Aplikacje IIoT na urządzenia mobilne, takie jak smartfony czy tablety, dają użytkownikom błyskawiczne informacje na temat problemów z wydajnością i stanem technicznym sprzętu w zakładach. Umożliwiają one dwukierunkową wymianę danych, wyświetlanie informacji, wprowadzanie danych, zautomatyzowane zbieranie danych oraz dostęp do dokumentacji technicznej, gdy technik z działu utrzymania ruchu znajduje się przy danym sprzęcie i wykonuje na nim prace.
Podczas gdy oprogramowanie do mobilności utrzymania ruchu staje się coraz bardziej funkcjonalne i łatwiejsze w obsłudze, to aplikacje na smartfony i tablety także zwiększyły swoje możliwości i obecnie są narzędziami uzyskiwania wartości dodanej, które pomagają personelowi podczas wykonywania zadań. Urządzenie mobilne pomaga pracownikowi wprowadzać informacje oraz przetwarzać porządek wykonywania prac podczas realizacji wymaganego zadania. Zapewnia to automatyzowane sprawdzanie błędów oraz zwiększa integralność i zgodność danych.
Uzbrojeni w rozwiązania mobilne, technicy utrzymania ruchu mają większy dostęp do historii zasobów, danych o zapasach części zamiennych, instrukcji serwisowych i nie tylko. Mobilność rozszerza procesy zarządzania zasobami oraz strategie predykcyjnego utrzymania ruchu do punktu działania, tworząc nadzwyczajne możliwości optymalizacji wydajności fabryk i zakładów.
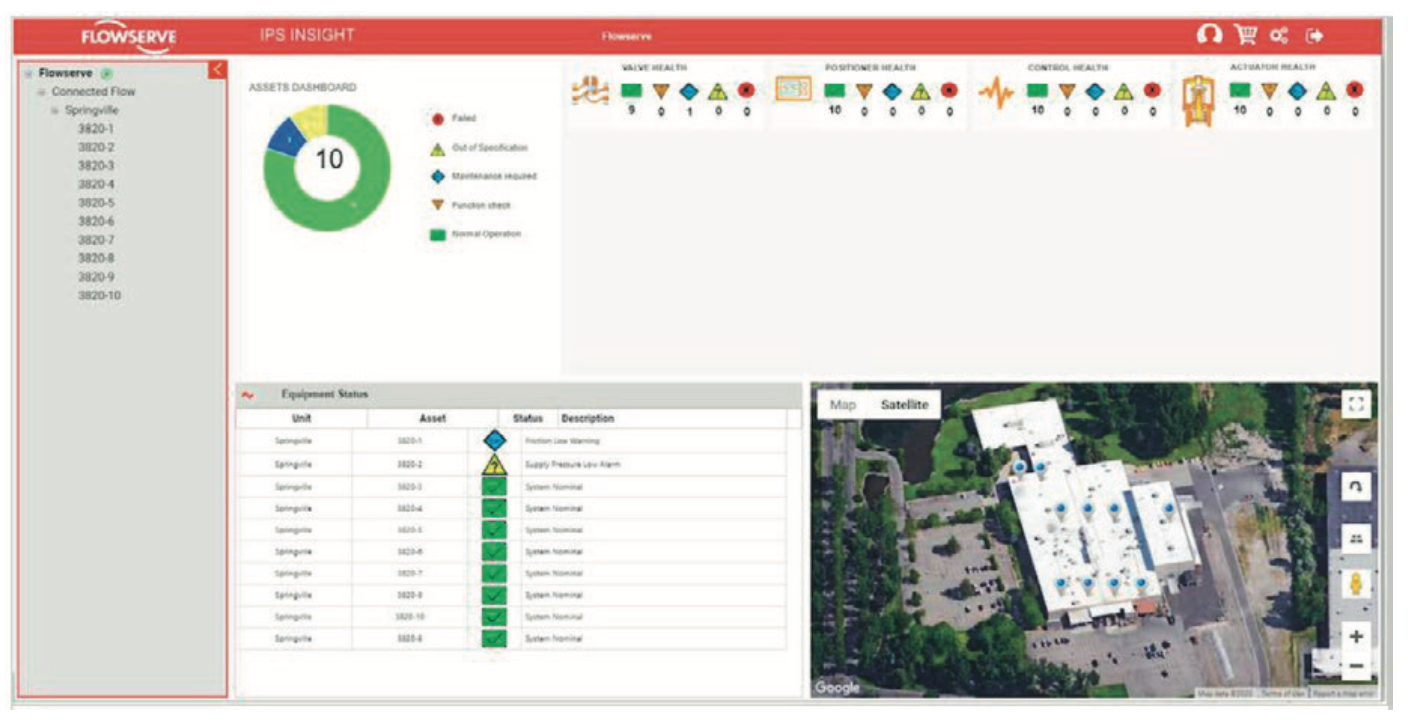
Rola standardu FDT
Standard FDT został wprowadzony po raz pierwszy w 1998 roku przez Grupę FDT, niezależne międzynarodowe stowarzyszenie przemysłowe typu non-profit, skupiające wiodące firmy z branży automatyki procesowej i fabrycznej. Jest to otwarty standard integracji sieci i urządzeń automatyki przemysłowej, wykorzystujący technologię IIoT oraz inicjatywę Przemysł 4.0 do uzyskania usieciowienia całych przedsiębiorstw.
Ostatnio wydana wersja FDT 3.0 przyśpieszy prace w kierunku czwartej rewolucji przemysłowej, poprzez stworzenie ekosystemu rozwiązań opartych na standardzie FDT, spełniającego wymagania aplikacji IIoT oraz Przemysł 4.0. Technologia ekosystemu IIoT wzmacnia skalowalne rozwiązania skid-to-cloud (z hali fabrycznej do chmury) oraz innowacyjne modele biznesowe, umożliwiając uniwersalną integrację urządzeń z mobilnością i zdalnym dostępem, optymalizując procesy zautomatyzowane oraz usieciowienie w takich sektorach przemysłu, jak procesowy, hybrydowy oraz produkcji dyskretnej (rys.1).
Standard FDT 3.0 pozwala inteligentnemu przedsiębiorstwu przemysłowemu na natywne zintegrowanie standardu OPC UA (OPC Unified Architecture), a także interfejsów sterowania i usług webowych dla aplikacji mobilnych. Technologia ta wykorzystuje też solidne cyberzabezpieczenia w celu ochrony kluczowych informacji systemów automatyki oraz danych operacyjnych. FDT 3.0 daje zwiększony poziom ochrony za pomocą wielu warstw zabezpieczeń oraz wykorzystuje sprawdzone standardy przemysłowe, takie jak TLS (transport layer security), WSS (web sockets secure) oraz HTTPS (hypertext transfer protocol secure).
Kluczowym komponentem standardu FDT 3.0 jest Serwer FDT, zbudowany dookoła serwera głównego, co stanowi punkt centralny dla szerokiego zakresu interakcji klienta i serwera. Zawiera serwer OPC UA, dający dostęp do danych DTM (device type manager – sterownik urządzenia obiektowego automatyki) z uwierzytelnionymi klientami OPC UA oraz serwer webowy, umożliwiający wykorzystanie interfejsów użytkownika webowego przez zdalnie połączonych klientów, stosujących przeglądarkę internetową oraz inne urządzenia mobilne, takie jak smartfony, tablety i laptopy. Rozwiązanie to wspiera także wykorzystanie aplikacji, które zwiększają wydajność pracowników oraz dyspozycyjność sprzętu zakładowego.
Interfejs użytkownika sieci (UI) wraz ze standardem FDT 3.0 pozwalają na otwieranie sterowników DTM w dowolnej przeglądarce internetowej, w tym na urządzeniach mobilnych wykorzystywanych przez techników pracujących na obiektach. Producenci mogą wykorzystać standaryzowaną platformę mobilności tej technologii jako część swojej funkcjonalności serwisu sprzętu, co pomaga inżynierom zakładowym rozwiązywać problemy ze zdalną pomocą.
Jednocześnie usługi webowe FDT dają użytkownikom standaryzowany dostęp za pomocą urządzeń mobilnych i zainstalowanych na nich przeglądarek internetowych, samodzielnych aplikacji oraz innego oprogramowania, które wykorzystuje protokół komunikacyjny WebSocket.
Dzięki ostatnim ulepszeniom technologia FDT mobilizuje obecnie monitoring zarówno zakładów oraz procesów przemysłowych, jak i konkretnych sieci i urządzeń, co jest częścią strategii nowoczesnego zarządzania zasobami. Monitoring cyklu życia oraz konserwacja prognozowana mogą być teraz realizowane za pomocą nowego standaryzowanego interfejsu mobilnego FDT lub za pomocą przeglądarek internetowych w taki sposób, który jest w pełni zintegrowany z rozproszonymi systemami sterowania (DCS), programowalnymi sterownikami logicznymi (PLC) oraz innymi układami automatyki przemysłowej.
FDT może komunikować się ze wszystkimi używanymi obecnie przemysłowymi sieciami urządzeń, niezależnie od ich architektury, oraz daje pewien poziom abstrakcji, tak że wszystkie informacje są prezentowane w konsekwentny i standardowy sposób.
Niezależnie od protokołu sieciowego czy producenta urządzeń użytkownicy uzyskają te same informacje, przeznaczone do wykorzystania w pracach związanych z konserwacją prognozowaną. To z kolei zapewnia swobodę wykorzystywania takich sieci i urządzeń, które są najlepiej dopasowane do poszczególnych środowisk operacyjnych.
Wraz z rozwiązaniem FDT 3.0 predykcyjne utrzymanie ruchu zyskuje znacznie więcej możliwości, dzięki dostosowanej do użytkownika widoczności zasobów, lepszej diagnostyce oraz łatwiejszemu dostępowi do sieci i danych dotyczących urządzeń. Pomaga to w skracaniu przestojów i poprawie wskaźnika MTTR (średniego czasu do naprawy).
Użytkownicy mogą osiągać korzyści z bezpiecznego i płynnego przesyłania danych z czujników do chmury obliczeniowej, a następnie uzyskiwania po ich przetworzeniu wartościowych informacji oraz osiągać nowe poziomy integracji technologii informatycznej z operacyjną (IT/OT). Dla producentów urządzeń sterowniki DTM kompatybilne z FDT 3.0 dostarczają rozwiązania dopasowane do aplikacji, przeznaczone do takich zadań, jak diagnostyka wykorzystująca głęboką inspekcję (deep inspection analysis), oparta na technologii sztucznej inteligencji (AI).
Wszystkie sterowniki DTM oparte na specyfikacji FDT 3.0 są zgodne z zaleceniami standardu NAMUR NE-107, który przewiduje, że operatorzy potrzebują widoczności procesu, w tym statusu oprzyrządowania, w prosty i jednolity sposób – niezależnie od urządzenia źródłowego – do wspierania strategii konserwacji prognozowanej. Sterowniki DTM są ważnym aktywatorem dla aplikacji na urządzenia mobilne, przeznaczonych do podglądu stanu technicznego urządzeń w zakładach, co w konsekwencji ulepsza organizację prac konserwacyjnych.
W przeszłości użytkownicy końcowi musieli otwierać i analizować sterownik DTM, aby zidentyfikować sprzęt wymagający serwisu lub naprawy. Technologia FDT 3.0 umożliwia zainicjowanie tej funkcji z perspektywy wielkiej ilości danych. Użytkownik nie musi już wchodzić do DTM, tylko otrzymuje automatycznie alarm o wystąpieniu zmiany stanu technicznego urządzenia.
Mogą być też pisane aplikacje na urządzenia mobilne, powiadamiające odpowiedni personel o wystąpieniu jakiegoś problemu w ich obszarze działań w fabryce. Pozwala to tym pracownikom na wykonanie prac konserwacyjnych na podstawie miarodajnych danych. Technologia FDT 3.0, dzięki wykorzystaniu standardu OPC UA oraz aplikacji na urządzenia mobilne, znacznie ułatwia wykorzystanie informacji dotyczących zasobów do realizacji kluczowych wymagań utrzymania ruchu w zakładzie.
Te same dane o zasobach są bezproblemowo dostępne za pomocą OPC UA w celu integracji z systemami wyższego poziomu, obejmującymi rozwiązania do zarządzania utrzymaniem ruchu takie jak SAP, w celu ustalenia zautomatyzowanych schematów wykonywania prac związanych z konserwacją prognozowaną. Na przykład dane te mogą pomóc personelowi kierowniczemu w wydawaniu poleceń pracownikom na podstawie odczytu dokładnego stanu technicznego sprzętu. Umożliwia to działom utrzymania ruchu uniknięcie potencjalnych awarii i pozwala na przeprowadzanie prac serwisowych w optymalnych terminach.
Obecnie, dzięki łatwo dostępnemu bogactwu danych dotyczących zasobów, specjaliści od automatyki mogą tworzyć aplikacje wykorzystujące sztuczną inteligencję oraz uczenie maszynowe do badania pełnego zakresu funkcjonalności maszyn. Mogą oni także wykorzystywać zaawansowaną prognostykę do identyfikacji i naprawy błędów związanych z wydajnością sieci i urządzeń. Bez standaryzacji wprowadzonej przez FDT oraz jej bogatego źródła danych z całego przedsiębiorstwa, te rozwiązania predykcyjnego utrzymania ruchu stają się bardziej złożone i trudne we wdrażaniu.
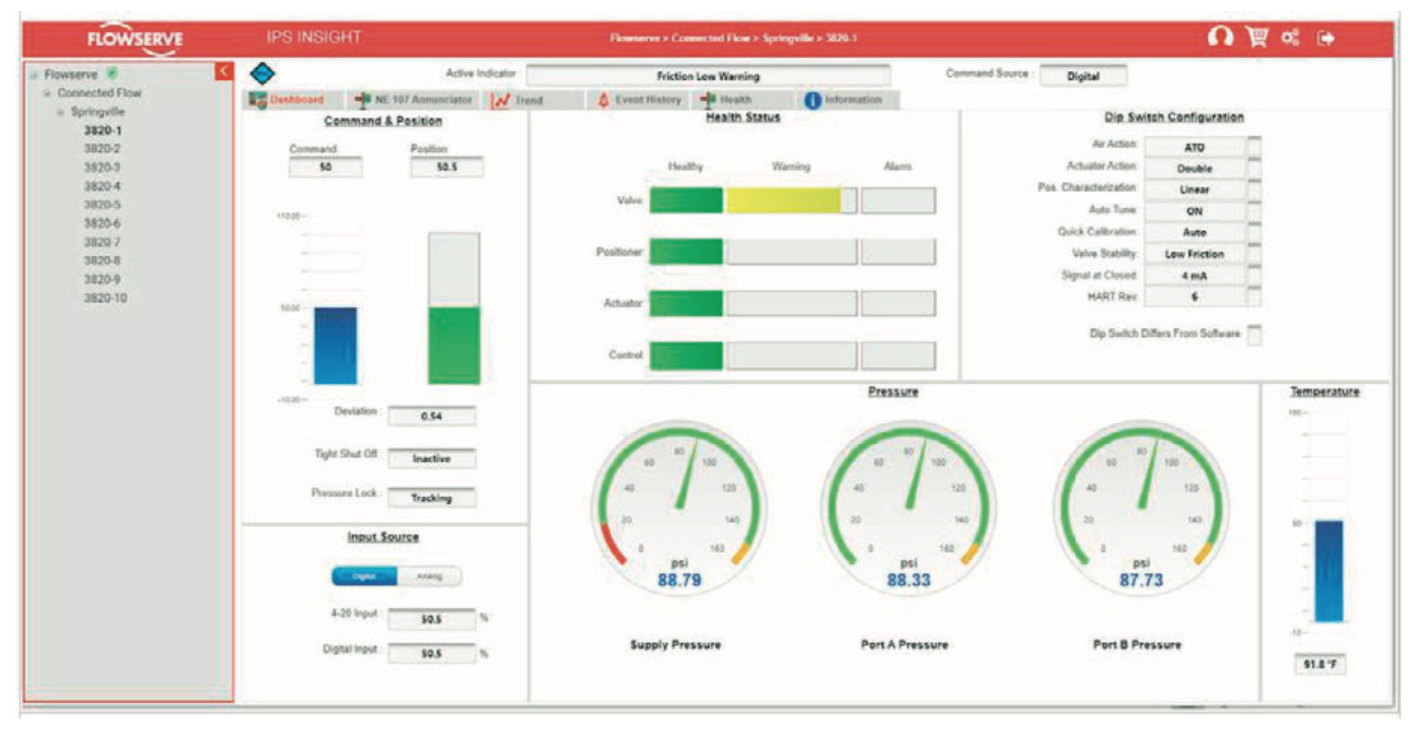
Perspektywy dla głównych dostawców automatyki
Producenci i dostawcy przemysłowych urządzeń i systemów sterowania pragną wykorzystać pojawiające się okazje dla rozwiązań technologii IIoT oraz inicjatywy Przemysł 4.0. Adaptując standard FDT 3.0, mogą oni rozszerzyć swoje oferty produktowe o modele biznesowe oparte na standardach, niezależne od platformy i sterowane informacjami. W ten sposób wkraczają w nową erę automatyki oraz zarządzania zasobami w przemyśle.
Jak uważa Suriya Selvaraj, starszy menedżer w firmie Yokogawa, będącej głównym światowym dostawcą rozwiązań dla automatyki procesowej, standard FDT daje swobodę dostawcom systemów sterowania i producentom urządzeń. Mogą oni współpracować w celu stworzenia w pełni zintegrowanego rozwiązania.
– Obecnie dostępnych jest wiele narzędzi do zarządzania zasobami i konserwacji prognozowanej, jednak w większości przypadków nie są one dostatecznie zintegrowane wśród całej społeczności dostawców. Uważam, że FDT 3.0 wprowadza pewną równowagę, dzięki której dostawcy systemów sterowania i producenci urządzeń mogą zaoferować swoim klientom ściśle zintegrowane rozwiązanie, wykorzystując interfejsy OPC UA oraz inne otwarte platformy – twierdzi Suriya Selvaraj.
Za pomocą solidnego modelu informacyjnego FDT 3.0 producenci automatyki przemysłowej mogą dostarczać zintegrowane rozwiązanie, wspierające konwergencję IT/OT. Ten model informacyjny umożliwia producentom urządzeń wychodzenie poza schematy i daje swobodę uwolnienia się od pewnych zdefiniowanych interfejsów, wzorów matematycznych oraz parametrów urządzeń. W przypadku innych technologii producent taki musi czekać na aktualizację specyfikacji, zanim wprowadzi jakąś zmianę w swoim urządzeniu. Natomiast FDT w prosty sposób definiuje mechanizm interoperacyjności, zamiast dawnej sytuacji, w której każdy indywidualny etap wymagał zaimplementowania pewnej funkcji. Oferuje on wszystko, co najlepsze z obydwu światów, pozwalając producentom urządzeń podawać parametry w elektronicznych opisach urządzeń (electronic device description – EDD) oraz jednocześnie odczyt lub zapis w innych wymaganych parametrach. Producenci mogą podawać wybrane przez siebie parametry za pomocą uniwersalnego interfejsu DTM standardu FDT.
– Technologia FDT jest dla dostawców urządzeń i systemów sterowania bodźcem do współpracy na takich samych zasadach w celu rozwiązywania problemów użytkownika końcowego. To podejście chroni wiedzę specjalistyczną poszczególnych producentów, jednocześnie zaś dostarcza najlepszą wartość z biznesowego punktu widzenia – mówi Suriya Selveraj.
Ed Silva, globalny menedżer ds. technologii cyfrowej w firmie Flowserve, będącej wiodącym dostawcą maszyn przemysłowych oraz urządzeń chroniących środowisko uważa, że technologia FDT 3.0 jest przełomowa dla sektora automatyki (rys. 2 i 3).
Obszar zainteresowania organizacji przemysłowych ewoluuje. Sprawą naglącą dla nich jest wydłużanie czasu bezawaryjnej pracy sprzętu oraz zapewnianie stabilności realizowanych operacji. Jedynym sposobem na osiągnięcie tego jest uzyskiwanie informacji na temat pracy urządzeń oraz przewidywanie ich awarii, zanim spowodują nieplanowany przestój. Jednak wskutek odchodzenia na emeryturę doświadczonych pracowników firmy przemysłowe muszą znajdywać sposoby na wykorzystanie technologii do szybkiego wdrażania nowych generacji do pracy w działach operacyjnych i utrzymania ruchu.
W obecnym środowisku przemysłowym zakłady produkcyjne poszukują sposobów na zdalny monitoring swoich zasobów, przewidywanie awarii sprzętu przed ich rzeczywistym wystąpieniem oraz podejmowanie działań zapobiegającym zakłóceniom w produkcji. Firmy chcą w pełni wykorzystać możliwości technologii IIoT oraz analizy predykcyjnej bez dokonywania poważnych zmian w infrastrukturze (rys. 4).
Najnowsze trendy w przemyśle skupiają się na zaawansowanej analizie danych, technologii cyfrowych bliźniaków oraz chmurze obliczeniowej. Standard FDT 3.0 wspiera te rozwiązania poprzez dostarczanie informacji sieciowych i o urządzeniach, co umożliwia ulepszenie diagnostyki i stosowanie analizy predykcyjnej. Technologia ta dostarcza narzędzie służące nie tylko do monitorowania i przewidywania stanu technicznego urządzeń, ale także zdalnego konfigurowania i zarządzania zasobami, co pozwala na uzyskanie najwyższych poziomów niezawodności.
– Z mojej perspektywy rozwiązanie FDT IIoT ma dwie strony: predykcyjno-diagnostyczną, która wykorzystuje dane obiektowe za pomocą serwera OPC UA w sposób niezależny od producenta urządzeń, oraz konfiguracyjno-kalibracyjną, która wykorzystuje DTM/serwer webowy/ przeglądarkę internetową do wykonywania zdalnej diagnostyki i konfiguracji zaworów oraz innego sprzętu, bez potrzeby dokonywania tego przez technika na miejscu. Dzięki serwerowi FDT dane dotyczące zasobów są teraz dostępne w chmurze w celu wykorzystania ich do uzyskania trendów oraz analizy predykcyjnej, co pozwala na unikanie awarii sprzętu – mówi Ed Silva.
Ed Silva poinformował też, że firma Flowserve zamierza wkrótce wypuścić pakiet oprogramowania wykorzystującego technologię IIoT, które ma pomagać firmom produkcyjnym w zdalnym monitorowaniu swoich zasobów, przewidywaniu awarii sprzętu przed ich wystąpieniem oraz podejmowaniu działań zapobiegawczych w celu uniknięcia zakłóceń w działalności firmy. Ta nowa platforma wspiera każdy sprzęt do kontroli przepływu, niezależnie od jego producenta. Otwiera to firmom możliwości szybkiego realizowania pełnych korzyści z technologii IIoT oraz analizy predykcyjnej bez wprowadzania poważnych zmian w infrastrukturze zakładów.
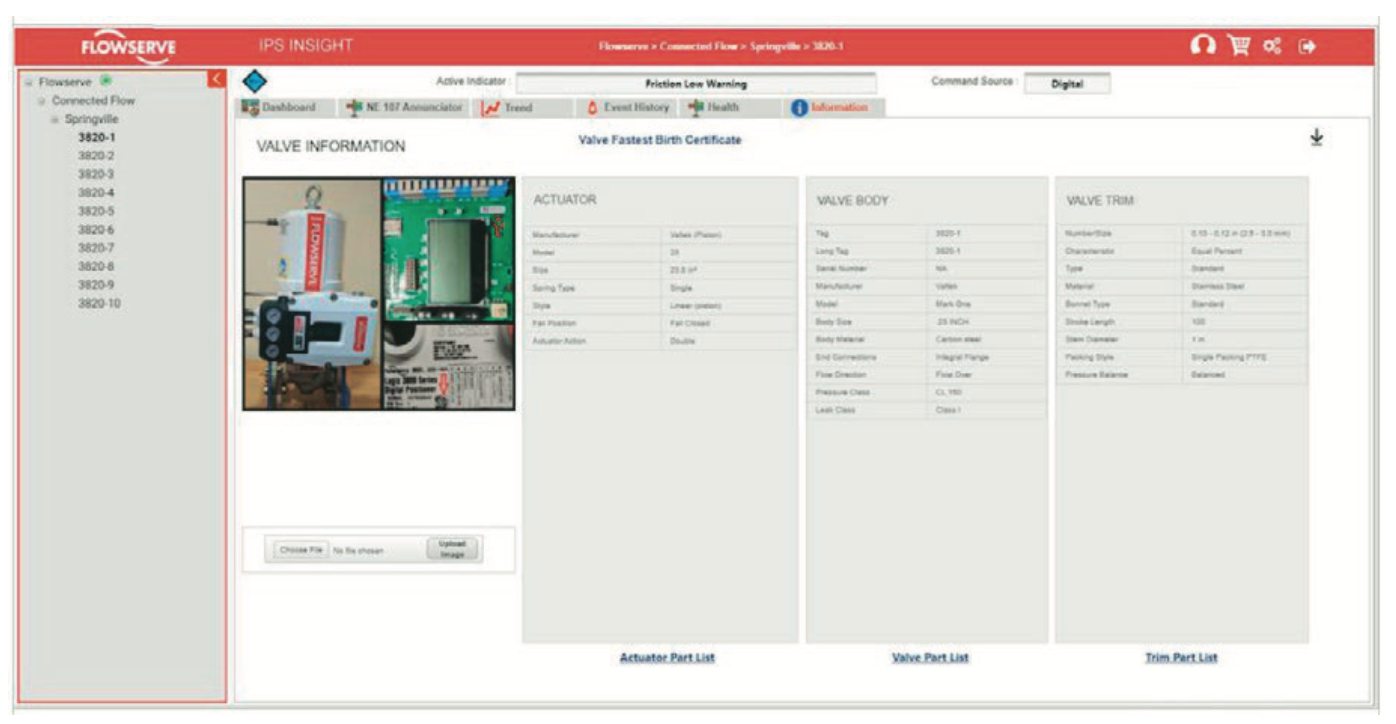
Korzyści z technologii FDT 3.0
Jako otwarty, niezależny od platformy standard, FDT 3.0 przyniesie korzyści firmom posiadającym zakłady przemysłowe, w których znajdują się urządzenia i systemy automatyki pochodzące od różnych producentów. Wspiera on monitoring w czasie rzeczywistym i aplikacje predykcyjnego utrzymania ruchu, wymagające jednolitego dostępu do urządzeń obiektowych za pomocą platform.
Technologia ta wspiera też kontrolę nad przedsiębiorstwem, tak że pojedynczy serwer w chmurze obsługujący daną aplikację (cloud instance) może przynosić korzyści dla wielu zakładów firmy w postaci zmniejszenia kosztów ogólnych oraz centralizacji zadań administracyjnych.
Dzięki ostatnim postępom w technologii FDT dane oraz informacje obiektowe mogą być automatycznie przesyłane do aplikacji w chmurze. Toruje to drogę do realizacji monitoringu stanu technicznego urządzeń za pomocą aplikacji w chmurze – niezależnie od rodzaju systemu automatyki. Zebrane dane mogą być także przesłane przy użyciu funkcji eksportu w celu dalszego przetworzenia w systemach zarządzania zasobami przedsiębiorstwa lub systemów monitoringu stanu technicznego sprzętu w chmurze.
Rozwiązanie FDT 3.0 umożliwi fabrykom uzyskanie ważnych korzyści, takich jak:
- mniejszy całkowity koszt posiadania (TCO) dzięki prawdziwie otwartej technologii,
- niezawodna konfiguracja, uruchamianie i diagnostyka urządzeń,
- uproszczenie prac inżynierskich oraz zwiększenie produktywności,
- redukcja przestojów (eliminacja niepotrzebnych prac konserwacyjnych),
- predykcyjne utrzymanie ruchu, pomagające w identyfikowaniu problemów zanim staną się poważne.
Idąc dalej, adaptacja uniwersalnej platformy FDT 3.0 stworzy okazję do zarządzania zasobami jako usługi. Dostawcy takiej usługi będą całkowicie zarządzali środowiskiem w chmurze oraz wdrażaniem modelu kosztów zmiennych na podstawie liczby użytkowników oraz zasobów. Ta możliwość będzie wspierana przez skonsolidowane panele raportów typu dashboard, wyświetlające dane z monitoringu zasobów we wszystkich zakładach danego przedsiębiorstwa oraz ich analizy, dostarczanej z lokalizacji centralnej firmy.
Perspektywy na przyszłość
Technologia Grupy FDT w wersji zaawansowanej FDT 3.0 jest kluczem do monitoringu kluczowych operacji dokonywanych w zakładach przemysłowych. Umożliwia to redukcję kosztów związanych z utrzymaniem ruchu w fabrykach oraz zainstalowanymi urządzeniami inteligentnymi. Technologia ta czyni dane sieciowe i dotyczące urządzeń dostępnymi we właściwym miejscu i we właściwym czasie. Dostarcza ważne informacje na temat pracy urządzeń w zakładach, co wspiera strategie predykcyjnego utrzymania ruchu i doskonałości operacyjnej.
Glenn Schulz, dyrektor zarządzający w Grupie FDT, będącej partnerem CFE Media ds. treści.