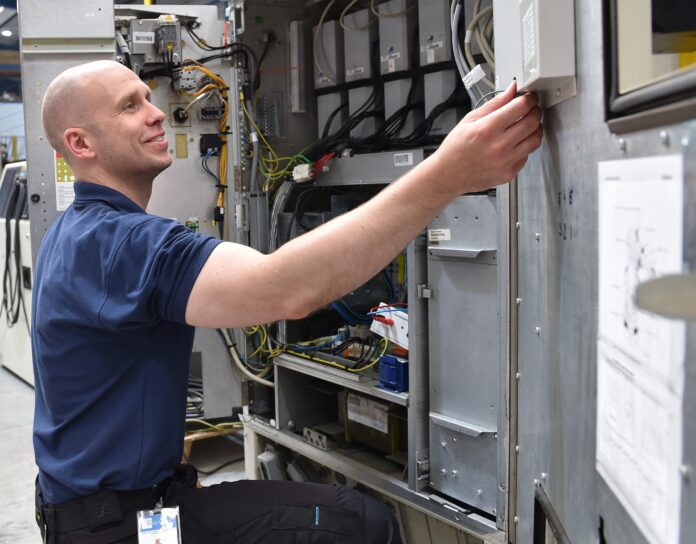
Badania pokazują, że konserwacja zapobiegawcza stała się obecnie kluczową strategią dla firm dążących do uniknięcia rosnących kosztów przestojów. Jednakże, w przypadku większości producentów, którzy wciąż korzystają z urządzeń fabrycznych starszych niż dziesięć lat, pojawia się potrzeba znalezienia równowagi między zarządzaniem przestarzałością, unikaniem przestojów a realizowaniem celów zarządu, zarówno w zakresie produktywności, jak i ESG (Środowiskowego, Społecznego i Ładu Korporacyjnego). Wyjaśnia Paweł Berlicki, Dyrektor Operacyjny Radwell Polska.
Raport firmy Siemens The True Cost of Downtime 2024 wykazał, że koszty przestojów wzrosły znacząco, średnio we wszystkich branżach, w ciągu ostatnich pięciu lat. Według raportu Siemens, nieplanowane przestoje kosztują obecnie 11% przychodów 500 największych firm na świecie. To daje łącznie 1,4 biliona dolarów, co odpowiada rocznemu PKB dużego państwa przemysłowego, takiego jak Hiszpania.
W przypadku wielu firm rosnące koszty przestojów można również odnieść do niedawnego raportu white paper by ERIKS UK & Ireland and IET, który wykazał, że ponad 50% urządzeń wykorzystywanych w 65% fabryk ma ponad 10 lat, a ponad 70% firm dysponuje sprzętem, do którego nie są dostępne części zamienne od producenta (OEM).
Zatem, podczas gdy producenci sprzętu przez ostatnie kilka lat skupiali się na temacie Przemysłu 4.0 i IIoT (Przemysłowy Internet Rzeczy) jako rozwiązaniu minimalizującym przestoje w przyszłości, nasuwa się pytanie, co to oznacza dla ogromnej większości firm, które nadal korzystają z przestarzałego sprzętu? A jak to wpisuje się w agendę zrównoważonego rozwoju, motywując firmy do maksymalizacji długoterminowej wydajności sprzętu inwestycyjnego?
W kontekście agendy ESG (Environmental, Social & Governance), wybór części zamiennych zamiast całych systemów zamiennych pozwala znacząco ograniczyć zużycie zasobów, produkcję odpadów oraz zużycie energii. Jest to podejście, które wspiera utrzymanie i wydłużenie żywotności produktów oraz systemów w bardziej zrównoważony i odpowiedzialny sposób, przynosząc następujące korzyści:
Korzyści środowiskowe
- Efektywne wykorzystanie zasobów: Zastosowanie części zamiennych pozwala zachować funkcjonalne elementy systemów w dobrym stanie, ograniczając zapotrzebowanie na nowe surowce.
- Redukcja odpadów Wymiana części generuje mniej odpadów niż wymiana całych systemów i przyczynia się do rozwoju gospodarki o obiegu zamkniętym.
- Obniżenie śladu węglowego: Produkcja części zamiennych zwykle wymaga mniej energii i powoduje niższą emisję gazów cieplarnianych niż produkcja nowego systemu.
- Oszczędzanie wody i energii: Produkcja części zamiennych zazwyczaj cechuje się niższym zużyciem wody i energii w porównaniu z produkcją nowych systemów.
Korzyści społeczne
- Wsparcie lokalnej gospodarki: Wymiana części często wiąże się ze współpracą z lokalnymi dostawcami i usługami naprawczymi, co wspiera lokalne gospodarki oraz przyczynia się do tworzenia miejsc pracy.
- Zaufanie konsumentów: Stosowanie części zamiennych świadczy o trosce o satysfakcję klientów poprzez wydłużenie żywotności produktów i systemów.
Korzyści związane z ładem korporacyjnym
- Odpowiedzialne zarządzanie zasobami: Wybór części zamiennych świadczy o odpowiedzialnym zarządzaniu zasobami i dobrej praktyce zarządzania, uwzględniającej długoterminowy wpływ działalności.
- Ograniczenie ryzyka: Korzystanie z części zamiennych może złagodzić niektóre ryzyka związane z wymianą systemu, takie jak zakłócenia w funkcjonowaniu, wyzwania związane z przestrzeganiem przepisów oraz kwestie reputacyjne
- Przejrzystość i raportowanie: Uwzględnienie części zamiennych w strategiach zrównoważonego rozwoju świadczy o zaangażowaniu w przejrzystość i odpowiedzialne raportowanie, podkreślając dążenie do minimalizowania wpływu na środowisko.
Te korzyści ESG można osiągnąć poprzez strategiczne podejście, które łączy planowanie konserwacji zapobiegawczej z zarządzania sprzętem przestarzałym, realizowane w następujących etapach:
Ocena ryzyka
Planowanie ryzyka najlepiej przeprowadzać w oparciu o bieżący harmonogram, korzystając z inkluzywnego podejścia, które uwzględnia wszystkie czynniki mogące wpływać na prawdopodobieństwo oraz potencjalne skutki przestarzałego sprzętu.
Zazwyczaj punktem wyjścia jest po prostu identyfikacja kluczowych aktywów, a następnie ocena ryzyka ich przestarzałości pod względem jakościowym i ilościowym. Po zidentyfikowaniu ryzyka związanego z każdym aktywem kolejnym krokiem jest ocena prawdopodobieństwa jego przestarzałości. Dane te można zebrać z różnych źródeł, począwszy od rejestrów konserwacji i systemów wewnętrznych, po informacje o niezawodności dostawcy w zakresie umów SLA, serwisu i wsparcia. Analiza planów dostawców dotyczących zakończenia cyklu życia produktów (EOL) może pomóc w zminimalizowaniu ryzyka związanego z zaprzestaniem wsparcia lub modernizacji technologii.
Naprawy
Co można naprawić w razie awarii? Czy możesz poczekać na naprawę? Dla komponentów, dla których przestoje są całkowicie niedopuszczalne, naprawa może nie być możliwym rozwiązaniem. W przypadku takich komponentów jak panele HMI, gdzie do naprawy wymagana jest często wymiana płyty głównej zawierającej oprogramowanie, czas realizacji może wydłużyć się z dni do tygodni.
Dobrze jest ustalić na początku, kto będzie przeprowadzać naprawy i jakimi zasobami dysponuje. Czy mają one dobrą historię użytkowania? Czy Firma realizuje prace samodzielnie, czy zleca je innym podmiotom? Szybka weryfikacja firmy pomoże zawęzić listę dostawców.
Części zamienne
Jakie części zamienne będą potrzebne, aby zapewnić ich szybką wymienność? Czy posiadają je Państwo w swoim magazynie?
W przypadku części, których naprawa lub modernizacja nie wchodzi w grę, a mają one kluczowe znaczenie dla produkcji, warto mieć w magazynie część zapasową, aby w razie awarii można było wymienić wadliwy element w ciągu kilku minut. Umożliwia to minimalizację przestojów, a jednocześnie pozwala naprawić uszkodzone urządzenie i ponownie wprowadzić je do magazynu, co przyczynia się do redukcji przyszłych kosztów związanych z zarządzaniem częściami zamiennymi.
Zakup części zamiennych w odpowiednim czasie może pozwolić na zaoszczędzenie znacznej kwoty w porównaniu do zakupu w momencie awarii, kiedy należy uwzględnić koszty ekspresowej wysyłki z dowolnego miejsca na świecie, a także fakt, że część może być znacznie droższa z powodu swojej rzadkości, ponieważ stała się przestarzała.
Firma Radwell niedawno uruchomiła SparesVault – usługę zarządzania zapasami opartą na subskrypcji, która oferuje kompleksowe zarządzanie zapasami zewnętrznymi, mające na celu rozwiązanie tego rodzaju problemów.
Strategia
Po ustaleniu wszystkich powyższych kwestii kluczowe jest opracowanie strategii umożliwiającej regularny przegląd i aktualizację polityk oraz procedur związanych z tymi działaniami.
Modernizacja
Wreszcie, należy wziąć pod uwagę modernizacje. Modernizacja w trakcie nieplanowanego przestoju zawsze jest niewskazana, dlatego warto rozważyć, czy sprzęt można zmodernizować przed wystąpieniem problemów.
Jakie urządzenia można zmodernizować? Jakie urządzenia należy zmodernizować i kiedy? Samo posiadanie planu odpowiadającego na te pytania pomoże wyprzedzić konkurencję.
Ze względu na ich rzadką dostępność, koszt niektórych przestarzałych części może przekraczać nawet dwukrotność ceny ich nowoczesnego odpowiednika. Nowy sprzęt objęty jest gwarancją i cechuje się lepszą dostępnością, co gwarantuje wsparcie na wiele lat.
Modernizacje mogą również zwiększyć produktywność, przepustowość i niezawodność maszyn, a także pomóc w obniżeniu kosztów energii.
Napędy AC często są pierwszym wyborem do modernizacji, ponieważ większość zastosowań jest stosunkowo prosta i wymaga jedynie niewielkich zmian w okablowaniu. W przypadku bardziej złożonych zastosowań może występować niechęć do przeprowadzania modernizacji w sytuacji awaryjnej. Często łatwiej jest trzymać się sprawdzonych rozwiązań, ale nie zawsze jest to najlepsza opcja. Dobry dostawca powinien dysponować odpowiednimi umiejętnościami, aby pomóc w instalacji lub nawet zrealizować wymianę przed wysyłką. Planowanie modernizacji z wyprzedzeniem jest zawsze najlepszym rozwiązaniem.
O Autorze:
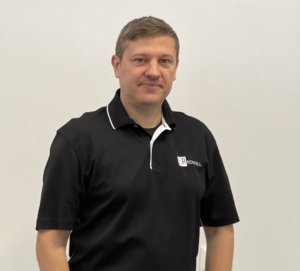
Paweł Berlicki jest Dyrektorem Operacyjnym w Radwell Polska. Firma Radwell International jest wiodącym globalnym dostawcą nadwyżkowych i odnowionych systemów sterowania przemysłowego. Firma Radwell, posiadająca 17 biur na całym świecie, jest autoryzowanym dystrybutorem ponad 350 marek nowych komponentów i części. Firma specjalizuje się również w dostarczaniu trudno dostępnych części oraz regenerowanych komponentów automatyki przemysłowej.